Lean Manufacturing, a methodology that has transformed industries worldwide, emphasizes waste reduction and efficiency. Originating from the Japanese manufacturing industry, this approach has become a global standard for operational excellence. In this article, we’ll explore the core principles of Lean Manufacturing, its benefits, implementation strategies, and common challenges, providing you with a well-rounded understanding of this pivotal methodology.
Table of Contents:
– What is lean manufacturing?
– The five core principles of lean manufacturing
– Key benefits of implementing lean manufacturing
– Strategies for successful lean manufacturing implementation
– Common challenges in lean manufacturing
What is lean manufacturing?
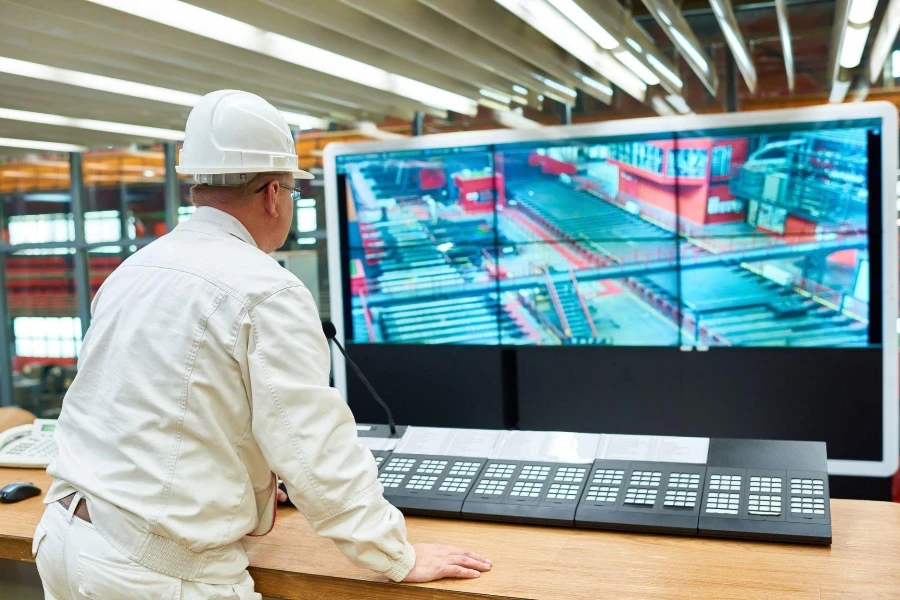
Lean Manufacturing, at its core, is a systematic method for waste minimization within a manufacturing system without sacrificing productivity. It focuses on the value from the customer’s perspective, eliminating all processes that do not add value. This concept is not about doing more with less; it’s about doing more of what matters with less. It’s a philosophy that encourages a culture of continuous improvement, where small, incremental changes regularly lead to significant improvements.
The origins of Lean Manufacturing can be traced back to the Toyota Production System, which emphasized the importance of optimizing the flow of products and services through the value stream. This approach has since been adopted and adapted across various industries, proving its versatility and effectiveness.
Understanding Lean Manufacturing requires a shift in mindset from traditional manufacturing practices. It’s not merely a set of tools or techniques; it’s a way of thinking that prioritizes efficiency, adaptability, and respect for people.
The five core principles of lean manufacturing
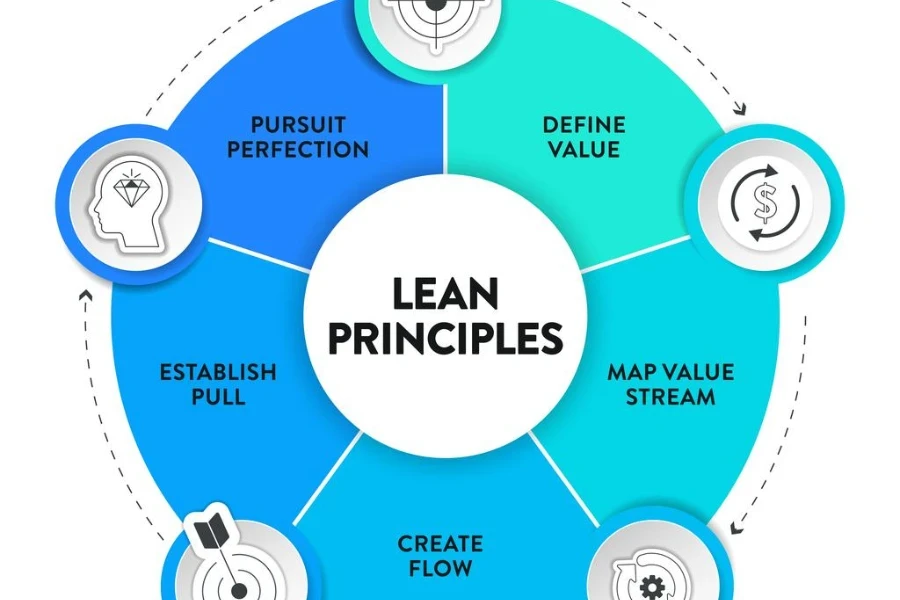
Lean Manufacturing is built on five core principles that guide organizations in their journey towards operational excellence. These principles are:
- Define Value: The first step in Lean Manufacturing is to define value from the customer’s perspective. What exactly does the customer value in your product or service? Understanding this allows businesses to focus their efforts on what truly matters.
- Map the Value Stream: Once value is defined, the next step is to map out all the steps that contribute to this value, identifying and eliminating any process that does not add value.
- Create Flow: After removing waste, the focus shifts to ensuring that the remaining steps flow smoothly without interruptions, delays, or bottlenecks.
- Establish Pull: This principle revolves around producing only what is needed, when it is needed, reducing excess production and inventory.
- Pursue Perfection: The final principle is the ongoing effort to perfect processes, products, and services, fostering a culture of continuous improvement.
Key benefits of implementing lean manufacturing
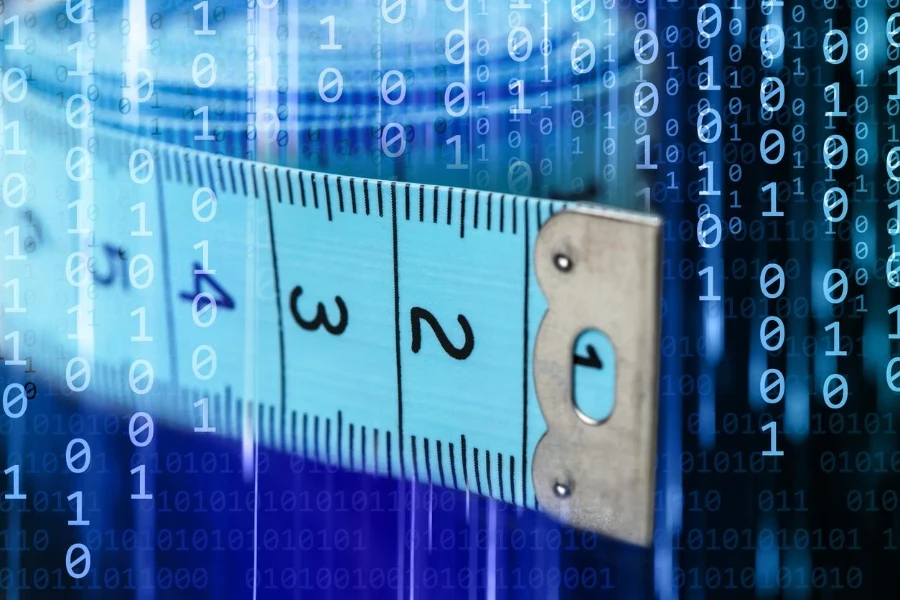
Implementing Lean Manufacturing can bring about a multitude of benefits, including:
- Reduced Costs: By eliminating waste, companies can significantly lower their production costs, leading to increased profitability.
- Improved Quality: Lean Manufacturing emphasizes defect prevention over defect detection, leading to higher quality products and fewer returns or repairs.
- Increased Efficiency: Streamlining processes and removing non-value-adding steps increase efficiency and productivity.
- Enhanced Customer Satisfaction: By focusing on value from the customer’s perspective, companies can better meet customer needs, leading to higher satisfaction and loyalty.
- Fosters a Culture of Continuous Improvement: Lean Manufacturing encourages employees at all levels to contribute ideas for improvement, leading to a dynamic and adaptable organization.
Strategies for successful lean manufacturing implementation
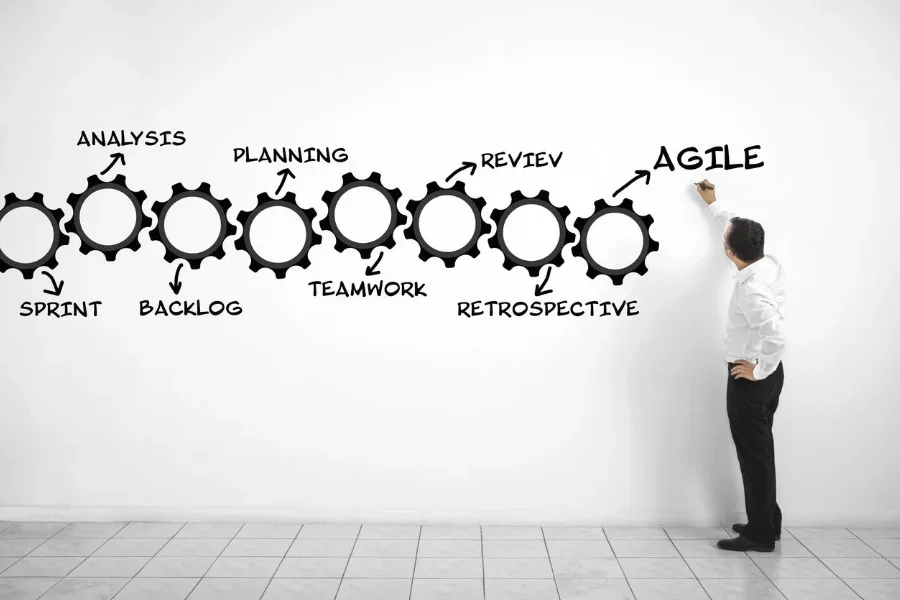
Implementing Lean Manufacturing requires a strategic approach, including:
- Comprehensive Training: Educating all employees on Lean principles and tools is crucial for fostering a culture of continuous improvement.
- Value Stream Mapping: Analyzing and visualizing processes to identify waste and opportunities for improvement is a foundational step in Lean implementation.
- Empowering Employees: Encouraging employees to identify inefficiencies and suggest improvements ensures that Lean principles are applied effectively.
Implementing Lean Manufacturing is not a one-time event but an ongoing journey. Success requires commitment from all levels of the organization and a willingness to adapt and change.
Common challenges in lean manufacturing
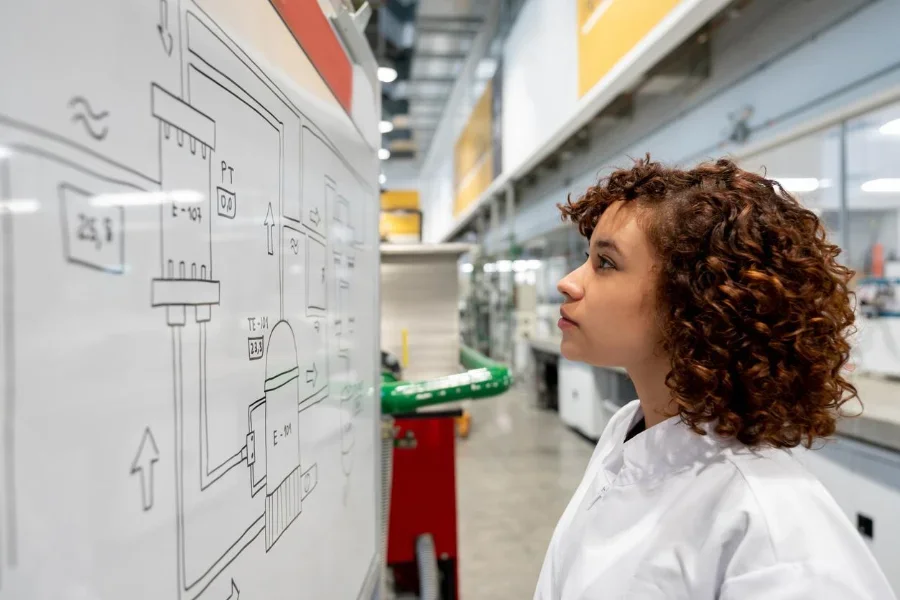
Despite its benefits, implementing Lean Manufacturing can present challenges, including:
- Resistance to Change: Changing long-standing practices and mindsets can be difficult. Overcoming resistance requires strong leadership and clear communication.
- Lack of Understanding: Without a deep understanding of Lean principles, efforts can be misdirected, leading to frustration and limited results.
- Sustaining Improvements: Maintaining momentum and continuing to improve requires dedication and a structured approach to continuous improvement.
Overcoming these challenges is possible with a clear strategy, strong leadership, and a commitment to education and empowerment.
Conclusion:
Lean Manufacturing is more than a set of tools; it’s a transformative philosophy that can lead to significant improvements in efficiency, quality, and customer satisfaction. By understanding and applying its core principles, businesses can navigate the challenges and reap the benefits of this powerful approach. As industries continue to evolve, Lean Manufacturing remains a critical strategy for staying competitive and meeting the ever-changing demands of customers.