Les fonderies sont magnifiques. Ces énormes fours dégagent de la chaleur et ont le pouvoir de transformer d'énormes blocs de métal en liquides ardents, facilitant chaque jour des merveilles scientifiques extraordinaires.
Cet article explore le processus de fusion des métaux et met en lumière différents types de fours de fonderie.
Table des matières
Le processus de fusion des métaux
Types de fours de fusion de fonderie
Comment choisir un four de fusion ?
La ligne de fond
Le processus de fusion des métaux
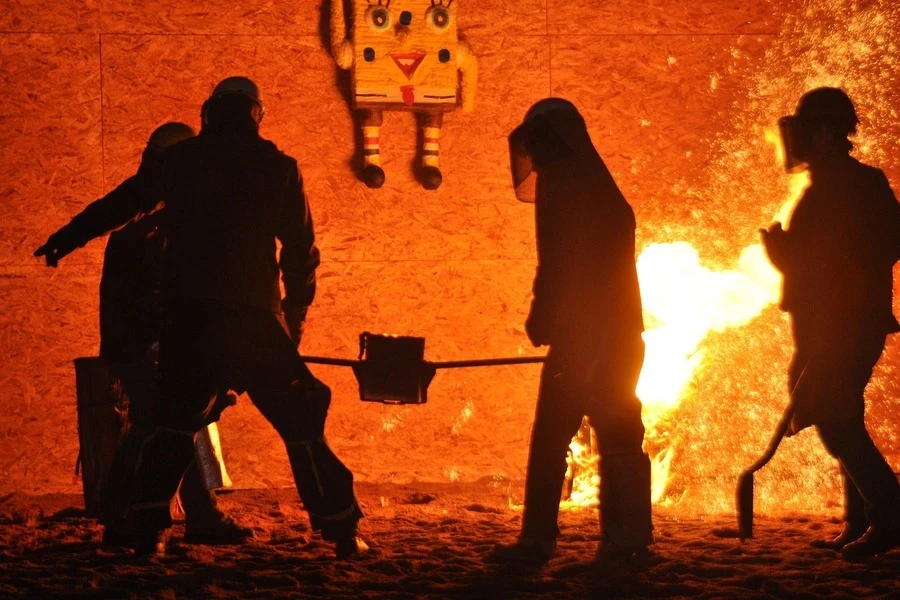
Pendant des milliers d'années, la fonte des métaux, du verre et d'autres matériaux a été un moyen important pour les civilisations de fabriquer des choses. Le processus de transformation des solides en liquides permet de les verser dans moules avant de durcir en formes utiles. L'ensemble du processus de fusion du métal repose sur les étapes suivantes :
Finalisation du rapport de mélange des métaux
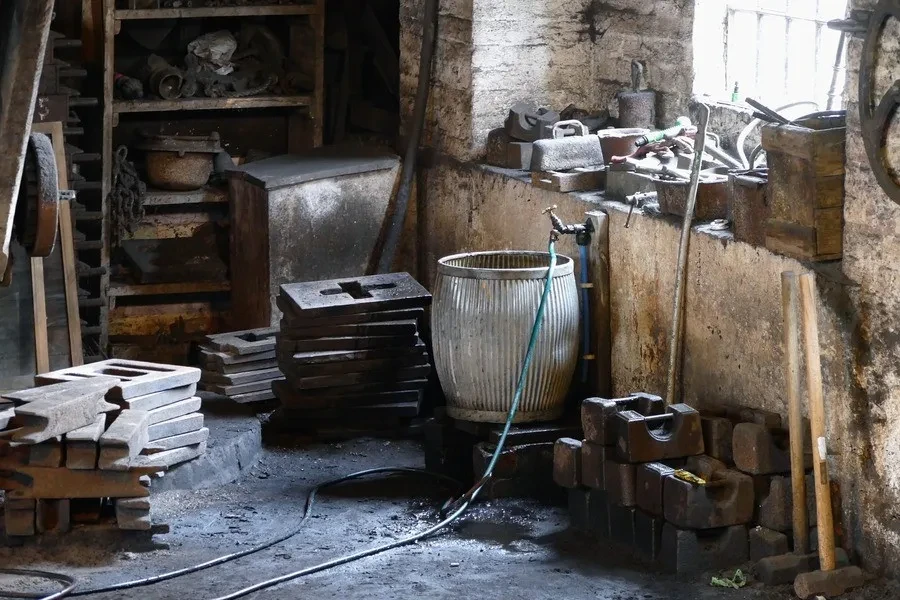
Chaque coulage l'application a des exigences différentes pour leurs propriétés mécaniques du métal. Les fabricants établissent leur formule de mélange des métaux en fonction de la classe de matériaux qu'ils utilisent et de leurs exigences spécifiques.
Par exemple, le rapport de mélange de l'aluminium dans la plupart des fonderies est de 40 % lingots d'aluminium + 50% ferraille d'aluminium + 10% autres. Les 10% des autres incluent des matériaux additifs comme le cuivre, le silicium et le zinc, etc.
Chargement du métal
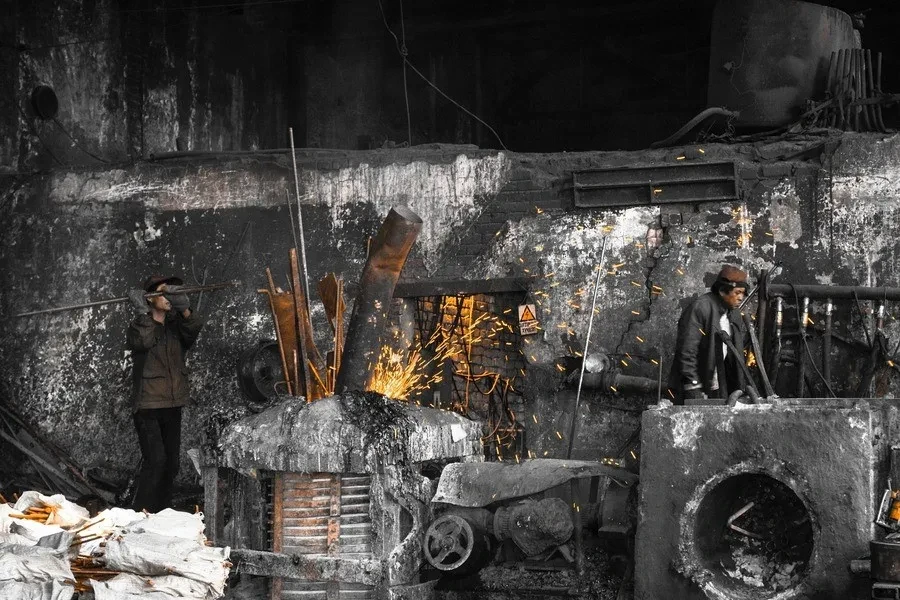
Avant de mettre les lingots et les chutes de métal dans le four, ils doivent être nettoyés, chauffés et séchés. Il s'agit d'une étape importante, éliminant toute humidité et saleté du métal pour s'assurer que le four ne soit pas endommagé ou sale.
Une certaine énergie peut être perdue lorsque les matériaux sont chargés dans le four. Si le four est chargé alors qu'il n'est pas assez chaud, le processus sera rendu moins efficace car il faudra plus de temps pour tout faire fondre. Cependant, si un four fonctionne constamment, cela améliore l'efficacité car il n'a pas besoin d'être chauffé à chaque fois que quelque chose est fondu.
Cependant, une grande quantité de chaleur peut s'échapper lorsqu'un four chaud est ouvert afin d'y mettre plus de matériaux. Il existe plusieurs façons de résoudre ce problème, y compris l'utilisation d'un four à puits latéral, où le métal chaud est remis dans le four pour être réchauffé pendant le processus de chargement.
Fusion du métal
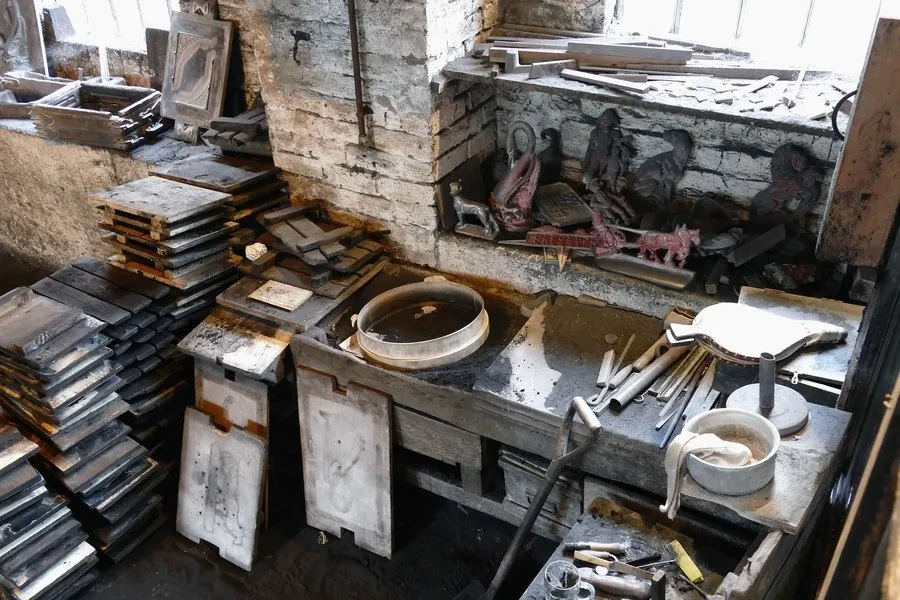
Parce qu'ils fonctionnent à des températures très élevées et qu'ils entrent en contact direct avec les métaux en fusion, les revêtements de four, les gaz et le combustible brûlé, les fours doivent être particulièrement résistants. De plus, ils doivent être capables de résister à la chaleur produite par des sources de combustible telles que le coke, le gaz naturel ou l'électricité qui sont utilisées pour faire fondre les matériaux.
En général, les fours doivent être capables de produire entre 350°C et 2000°C de chaleur afin de faire fondre le métal, ou d'atteindre le point de fusion d'un métal - le point auquel il passe d'un solide à un liquide.
Affinage et traitement du métal
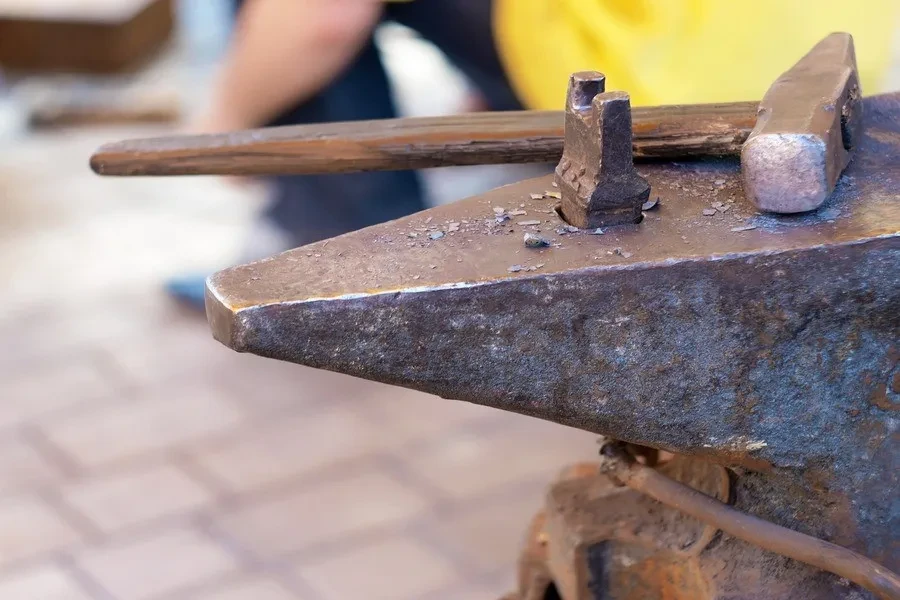
L'affinage consiste à nettoyer et à améliorer la qualité du métal fondu en supprimant toutes les irrégularités indésirables telles que les morceaux solides restants ou les bulles de gaz. L'idée est de s'assurer que le métal a le bon mélange de matériaux.
Avant que le métal ne soit moulé en une forme solide, l'ajout d'autres matériaux ou un nettoyage supplémentaire peut aider à le rendre plus solide, plus flexible ou plus robuste. Cette étape est importante car elle peut affecter la qualité du produit final.
Transport de métal fondu
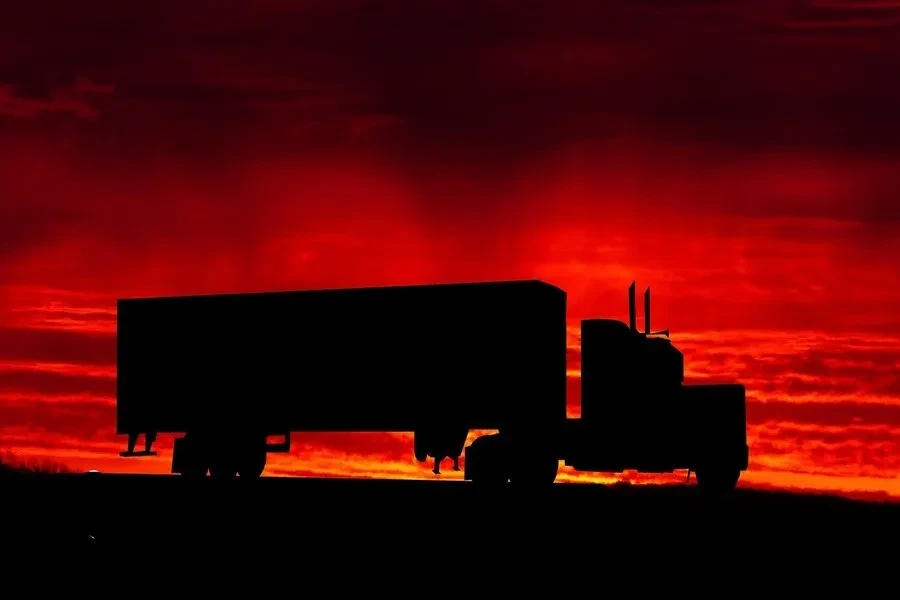
Une fois le métal fondu, il est transféré du four à la ligne de moulage à l'aide d'un système de coulée.
Types de fours de fusion de fonderie
Fours de fusion sont utilisés pour chauffer des matériaux solides à un degré tel qu'ils se transforment en liquide. Cette transformation physique dépend à la fois de la pression et de la température ; le four de fusion doit être capable de créer et de maintenir une température spécifique afin que le matériau à l'intérieur fonde uniformément.
Plusieurs types de fours sont utilisés pour réaliser des variantes de ce procédé. Les plus notables d'entre eux comprennent:
Fours à creuset
Fours à creuset sont un type simple de four utilisé pour la fusion du métal. Un creuset est un récipient qui peut supporter des températures extrêmement élevées et qui est généralement fait de céramique ou d'un autre matériau résistant à la chaleur.
De nos jours, les bijoutiers, les amateurs et certaines petites usines utilisent des fours à creuset pour faire fondre le métal en petites quantités. Les creusets sont de différentes tailles, des plus petits pour faire fondre le métal avec un chalumeau aux plus grandes variétés pouvant contenir jusqu'à 50 livres de métal.
Cubilots
Les cubilots ont longtemps été utilisés pour faire fondre le fer afin d'en faire de la fonte, de meilleure qualité que la fonte brute. Le sommet d'un cubilot est souvent équipé d'un bouchon pour empêcher les mauvais gaz de s'échapper et pour empêcher l'eau de pluie de pénétrer.
La fusion du fer dans un cubilot et l'ajout de coke, de carbone et d'autres matériaux créent différents types de fer et d'acier. De nos jours, les cubilots ne sont généralement pas utilisés car les méthodes à arc électrique et à induction sont plus efficaces pour produire la chaleur nécessaire.
Fours à arc électrique
Les fours à arc électrique sont utilisés pour fabriquer du fer à partir de minerai de fer. Le four produit de la chaleur à partir d'un arc électrique déchargé dans le cadre d'une réaction entre deux électrodes. De l'oxygène est insufflé dans le four ainsi que de la chaux et des éléments afin d'éliminer les éléments indésirables et de faire du laitier. Le fer fondu est ensuite versé à partir d'un bec verseur.
Les fours à arc électrique font fondre le matériau par contact direct avec l'électricité d'arc, qui traverse le matériau. Cela rend le processus de fusion plus efficace que d'autres méthodes qui reposent sur la chaleur externe.
Fours à induction
Fours à induction avoir un récipient ou une chambre en métal entouré d'une bobine parcourue par un courant électrique. Cela crée des courants de Foucault dans le métal, ce qui produit les hautes températures nécessaires pour le faire fondre et pour fabriquer des alliages avec des compositions précises.
La chaleur est générée par des molécules excitantes dans le fer lui-même sans ajout d'oxygène ou d'autres gaz. Bien que cela facilite la fusion des matériaux car il y a moins de variables à prendre en compte, cela signifie également que le four ne peut pas être utilisé pour fabriquer de l'acier moulé de haute qualité, car tout ce qui est mis dans le four sort le même.
Comment choisir un four de fusion ?
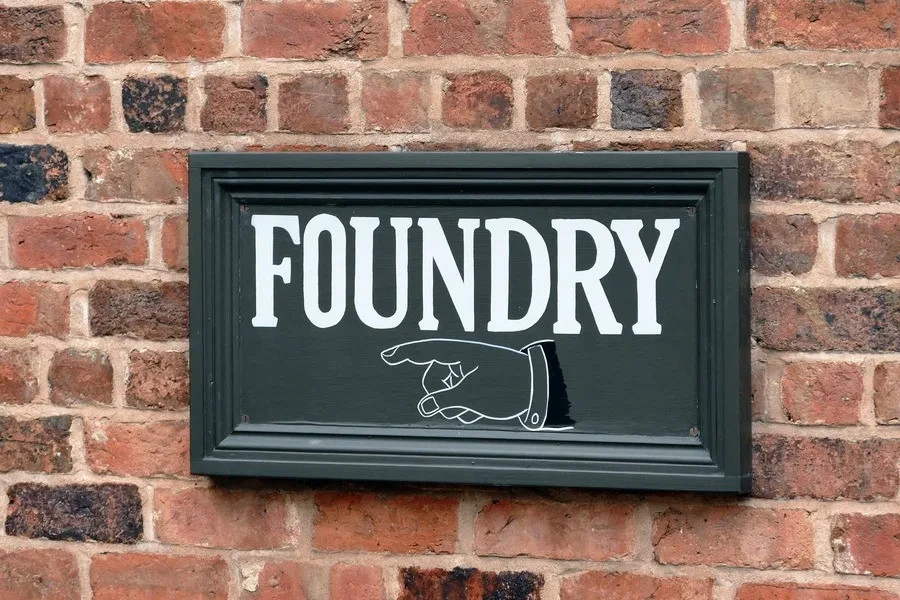
Laquelle four de fusion est utilisé aura un impact sur l'efficacité de la fonderie et des pièces moulées finales. Par conséquent, il est essentiel de déterminer quels résultats sont requis, car cela influencera les technologies de four nécessaires.
Les facteurs suivants aideront à décider quel four de fusion conviendra aux opérations de fonderie spécifiques :
- Espace disponible
- Alliages cibles et leur point de fusion
- Investissement financier
- L'efficacité énergétique
- Exigences de maintenance
- Quantité de métal nécessaire
- Problèmes environnementaux
Notez qu'il n'y a pas de solution unique pour toutes les opérations de moulage. Chaque fonderie peut avoir des critères différents pour son échelle de production et les demandes du marché. Il est essentiel de cocher toutes les cases avant de prendre la décision finale quant à la technologie de four et au processus de fusion global requis.
La ligne de fond
Les dernières décennies ont vu plusieurs avancées dans les technologies de fusion des métaux. Pourtant, il existe de nombreuses étapes et processus de base qui peuvent aider les fondeurs de métaux à améliorer l'efficacité de la fusion des métaux et à réduire les pertes de métal pendant la production. À ce titre, il est essentiel pour les fonderies de garder un œil sur l'évolution des technologies et de s'adapter en fonction des tendances du marché.