Welding isn’t something consumers can just jump into without the right tools. And when it comes to fusion welding, choosing the right machine is critical. Whether they are working on DIY home projects, fixing up a car, or tackling major industrial tasks, the right fusion welder makes all the difference.
But how do businesses build a collection of fusion welders to sell? There are many options, and they can quickly become overwhelming. This article will break down everything about choosing fusion welders without the headache.
Table of Contents
What exactly is fusion welding?
Types of fusion welders
6 key factors to consider when choosing fusion welders
4 advanced features consumers might want
Rounding up
What exactly is fusion welding?
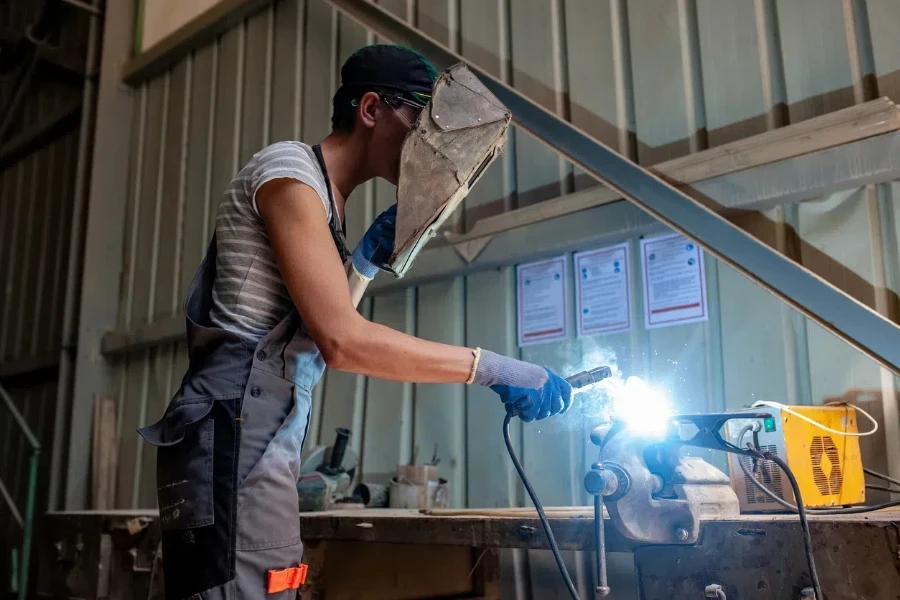
Fusion welding is a process that uses heat to melt and fuse materials (usually metal). The result? A strong bond once everything cools and solidifies. Simple, right? Well, yes and no. While the concept is straightforward, the technique and the equipment operators use can vary widely depending on their project.
Businesses will see fusion welding in various forms, including MIG, TIG, and stick welding. Each has its place, depending on the material consumers work with and how precise or heavy-duty the job is.
Types of fusion welders
Here’s where things start to get interesting. Different jobs call for different welders, so here are three major types in the market businesses can offer.
1. MIG welders
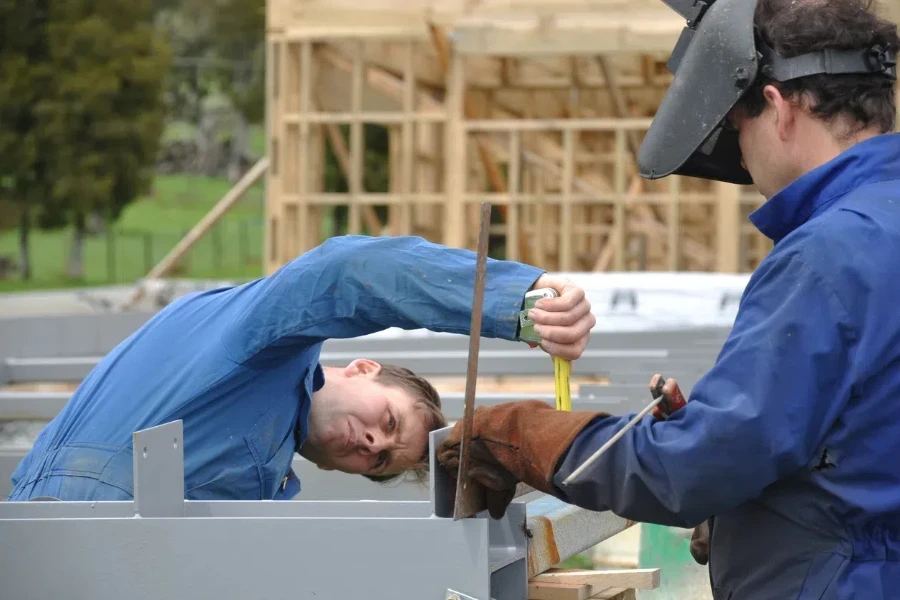
If consumers are beginners, metal insert gas (MIG) welding is probably where they’ll start. It’s user-friendly and fairly forgiving, making it great for those smaller projects around the house or in the garage. The machine feeds a wire through the gun while shielding the weld pool from contaminants with gas.
2. TIG welders
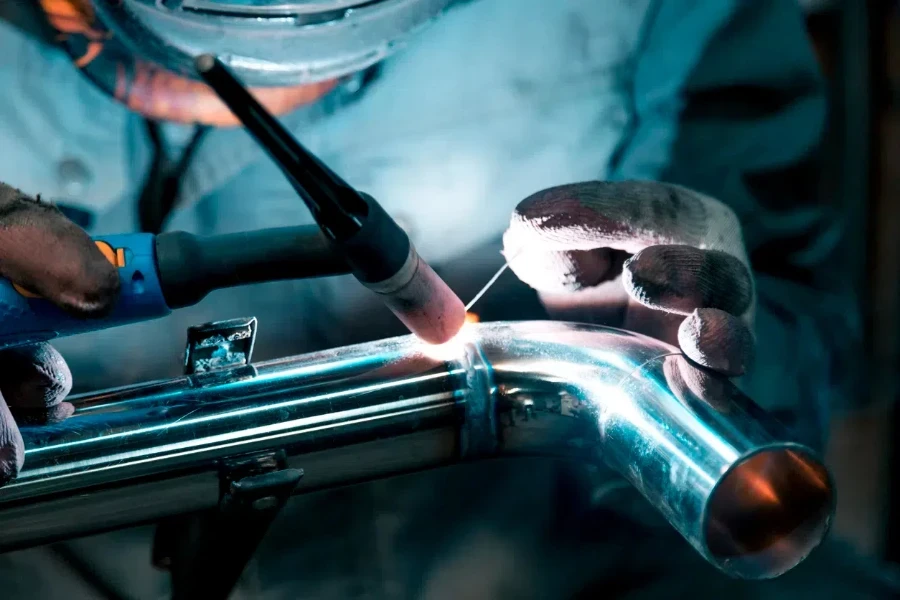
Are consumers looking for more control and precision? That’s where tungsten inert gas (TIG) welding shines. TIG is a little more advanced than MIG and requires a steady hand. However, consumers must control the filler material separately, which takes some practice.
3. Stick welders

Stick welding, or shielded metal arc welding (SMAW), is a bit more old-school but still incredibly reliable. It’s rugged, can handle dirty or rusty materials, and works outdoors in windy conditions. Since these welders use rods (usually ⅛ inches), they can handle weld beads surprisingly well.
6 key factors to consider when choosing fusion welders
Now that businesses have a sense of the types of welders, here is a look at what they need to consider when choosing one. After all, it’s not just about picking the “best” welder—it’s about picking the right one for consumers’ needs.
1. Type of material
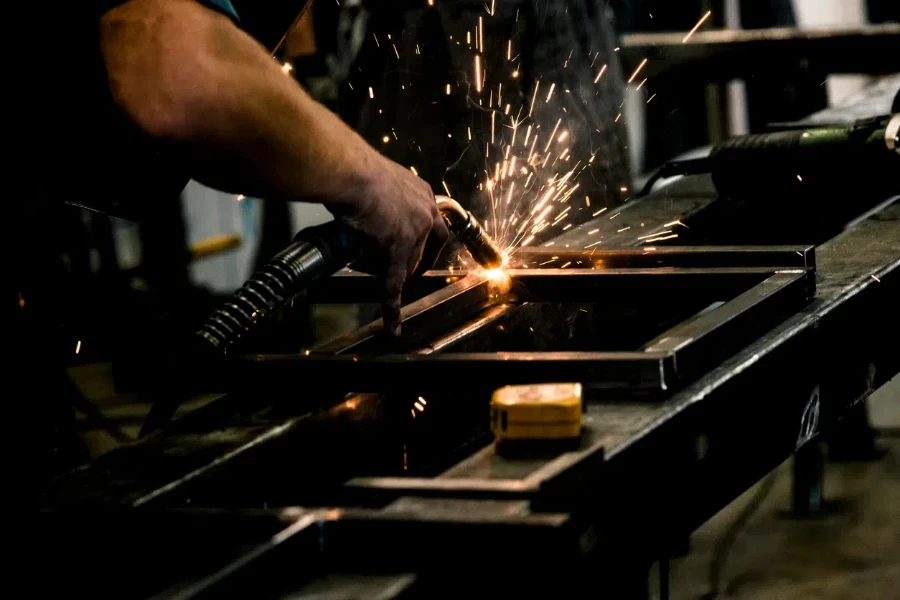
Different materials need different types of welders. For example, aluminum works best with TIG welding, while a MIG welder can handle mild steel. Make sure to match the welder to the materials the target consumers often work with. Here’s a table showing the welder type and the materials they can handle.
Welder type | Best compatible materials |
MIG welders | Mild steel, aluminum, carbon steel, and stainless steel. |
TIG welders | Stainless steel, aluminum, carbon steel, and non-ferrous metals. |
Stick welders | Heavy-duty jobs like steel and ironwork. |
Butt fusion machines/electrofusion welders | Plastic pipes and fittings. |
Hot air welders | Plastic sheets and other high-temperature materials. |
2. Material thickness
Are consumers welding thin metal sheets? MIG and TIG are their go-to options. But if they’re dealing with thicker materials, like heavy steel plates, consumers will need the power of a stick welder or a high-powered TIG machine. Plastic pipes and sheets require different welders, like butt fusion, electrofusion, and socket fusion machines.
3. Power requirements
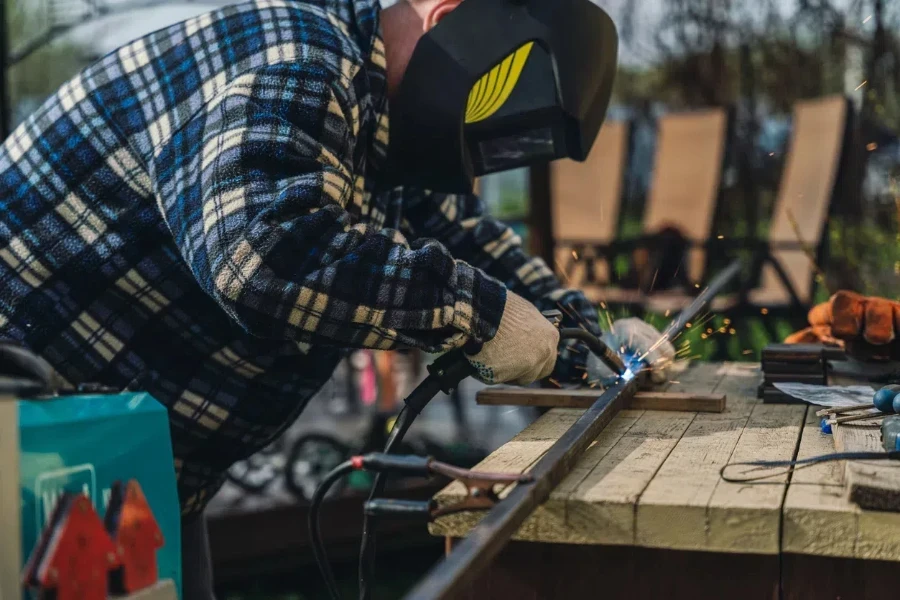
Not all welders are created equal when it comes to power. Smaller residential welders often work on 110V or 220V, while industrial machines might need three-phase power. So, ensure product listens have the proper power requirements so buyers know if their power supply (or socket) can handle the welder you’re eyeing.
4. Portability
Will consumers be welding in their garage or moving between job sites? If they’re constantly on the go, a lightweight, portable welder might be better than a big, stationary one. However, the opposite is the case for those working in more fixed environments.
5. Ease of use
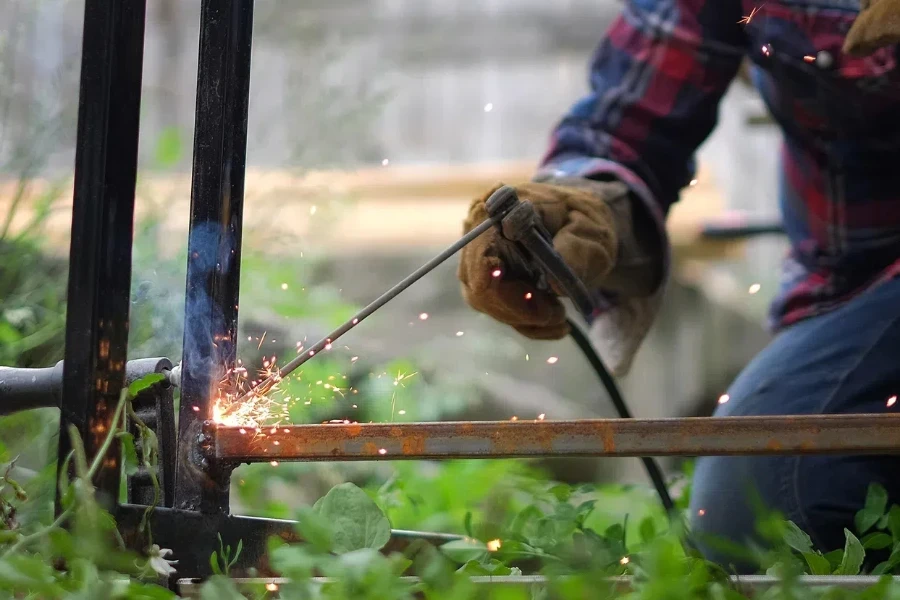
If consumers are just starting, they probably don’t want something that takes years to master. MIG welders are generally the easiest to use, while TIG and stick welders offer more control but take time to master.
6. Budget
Welders can get expensive. But consumers don’t need to spend a fortune if they’re just working on small projects. So, businesses can offer them more affordable machines. However, if they plan on using it for professional or frequent use, be sure to provide them with a better investment; a more durable, feature-rich machine is worth the extra cost.
4 advanced features consumers might want
If consumers are looking for welders with all the bells and whistles, here are some features that can make a big difference in performance.
1. Adjustable heat settings

Having the ability to adjust the heat gives consumers more control over the weld, which is particularly helpful when switching between different materials or thicknesses.
2. Pulse functionality
Pulse welding also helps control the heat, which is great for minimizing warping. Consumers who work with thinner metals will love this feature.
3. Digital controls
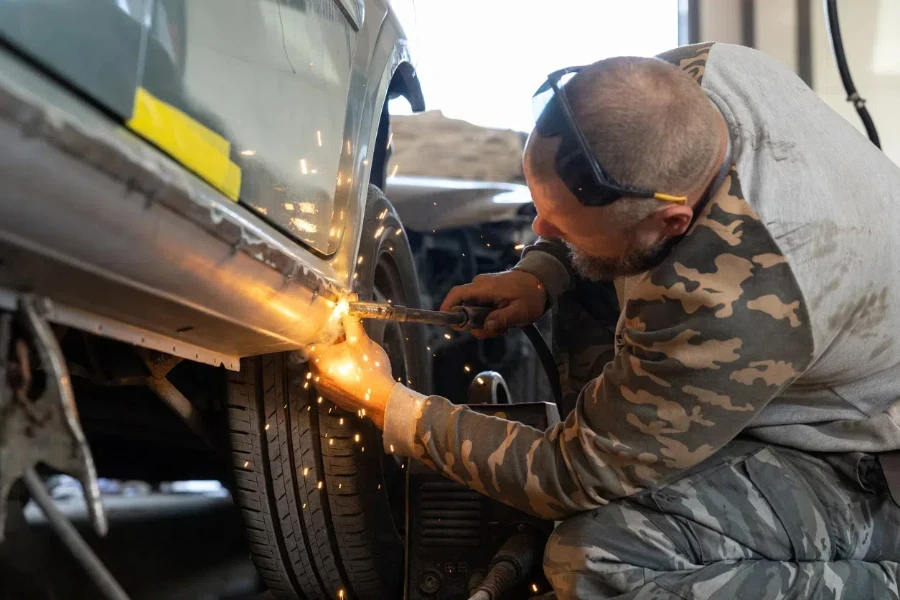
More and more welders are coming with digital interfaces, which makes setting things up a breeze. So, follow the trends and focus on models with user-friendly controls, especially if the targets are new welders. However, remember to balance the store with fewer digital models, too—not all consumers love digital functionality.
4. Safety features
Welding isn’t without risks, so businesses must prioritize machines with safety features like thermal overload protection and auto-shutoff to prevent accidents.
Rounding up
Choosing the right fusion welder isn’t just about selling the fanciest machine on the market. It’s about offering the one that fits what the target consumer wants. They could be welding in their garage or taking their heavy equipment to the job site, so businesses must take the time to consider various factors before creating a fusion welder inventory. Remember to factor in material type, thickness, power needs, and consumer budget to ensure the smoothest experience possible.