TIG welders, also called tungsten inert gas welders, use non-consumable tungsten electrodes to produce the weld on metal. These welders are versatile as they suit welding a wide variety of metals, including aluminum, brass, bronze, magnesium, stainless steel, and gold, among other metals. Since TIG welders are becoming common, these machines are readily available.
Knowing which among the options is suitable for different welding applications can become a challenge. Therefore, this article will examine the crucial features to consider while choosing a TIG welder. It will also look at the different types of TIG welders available to assist buyers in getting what fits their needs best.
Table of Contents
Global market overview of TIG welders
Selection tips for TIG welders
Types of TIG welders
Conclusion
Global market overview of TIG welders
The global TIG welding market is worth US$ 13 billion and is projected to reach US$ 25 billion by 2032, growing at a compound annual growth rate (CAGR) of 6.7%. The market growth is fueled by the demand for welding machines from various industrial sectors, including the automotive, aerospace, shipping, and oil and gas industries.
The consumer’s need for welding more exotic metals with different thicknesses have also led to the growth of the TIG welders market size. Since they produce more precise and quality welds, many prefer tungsten inert gas welding over traditional stick welding machines.
Selection tips for TIG welders
Amperage level
When buying a TIG welder, consider the amperage level. It is the strength of the electric current from the welding machine measured in amperes. Machines with low amperage levels provide good arc stability for starting and finishing welds.
Low-amperage TIG welders are suitable for thin metals because they can produce sturdy welds without burning them. On the other hand, high amperage level welders are suitable for professionals working with thick metals.
AC and DC welding
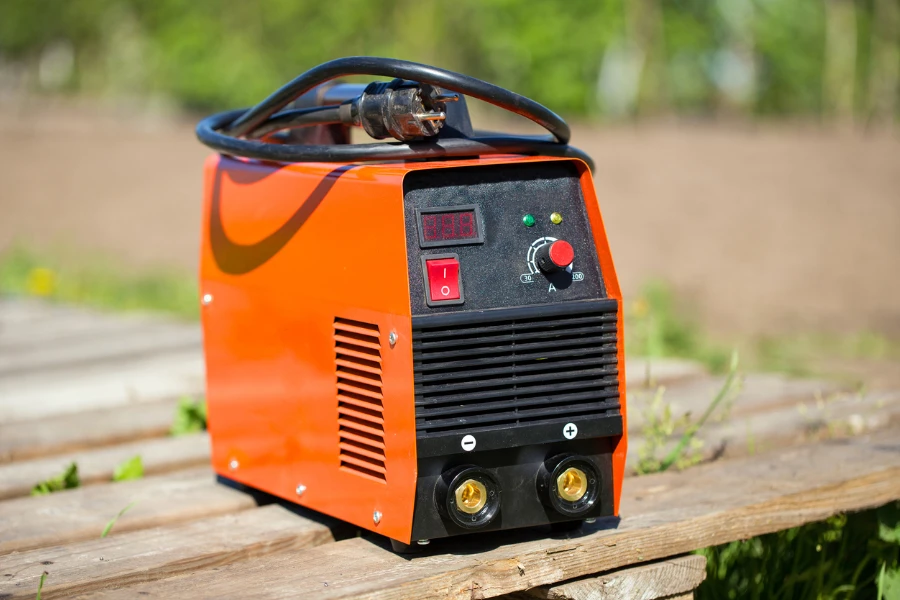
Before investing in a TIG welder, it is important to consider its current options. The welders available provide the DC option or the DC/AC alternative. These choices are dependent on the type of metal they can weld efficiently.
For instance, DC TIG welding is appropriate when welding common metals such as steel. When working on light and hard metals like aluminum, a DC/AC machine suits the purpose appropriately.
Right controls
Checking the controls of the welder is also crucial while shopping for a reliable TIG welder. These machines are designed with a foot pedal which helps adjust the amperage level. It becomes easy to control the welding accuracy and final quality by controlling the amperage level.
Therefore, buyers should inspect the controls and ensure that they are firm and secure with the machine. Correctly inspecting the welder avoids ruining a weld upon tapping on the wrong control. Checking crucial details such as sturdy and correct controls ensures a smooth welding process without compromising on the quality of the final result.
Low-amperage welding performance
Checking the welder’s performance on low amperage is important before making a purchase. Machines with low amperage can give the most stable arcs. Also, they offer an easy weld start, better weld quality control, and an excellent crater-filling capacity.
Low-amperage welders are reliable when working on thin metals. In contrast, high-amperage welders perform poorly on thin metals. They produce intense weld arcs which can ignite and damage the metal.
Arc stability at low amperage is also needed for finishing the weld. For instance, a large concave may form when welding aluminum, which may crack after the weld cools. Low amperage welding forms a smaller concave to reduce the chances of cracking when the welding cools.
Plasma cutter and stick welding options
Buyers should also consider looking for a tungsten inert gas welder with additional features. Having additional features in a welder allows the accomplishment of more tasks in one machine. For instance, a welding machine that offers plasma cutting and stick welding features makes metal working a seamless job.
The TIG welder can use the tungsten electrode to offer both plasma cutting benefits and welding the cut metal pieces together. The stick welder becomes the alternative to TIG welding if a backup option is needed. Additionally, having a versatile welder saves on the costs of buying separate machines and the overall power they would consume altogether.
Power
It is important to consider the amount of power the welder needs to operate. It depends on the type of metal being welded. For example, aluminum, magnesium, and most metal alloys use high-power welders. Mild steel and stainless steel require using lower-power welding machines.
The amount of power to choose also depends on the shop size. Small shops doing small-scale welding may want to use a welder that consumes low power. Large-scale welding shops can pick a machine with high power consumption.
The metal thickness also determines which welding machine to acquire. For thick metals, a high-power TIG welder is suitable. Thin metals are good to work on with machines that consume less power.
Types of TIG welders
AC/DC TIG welder
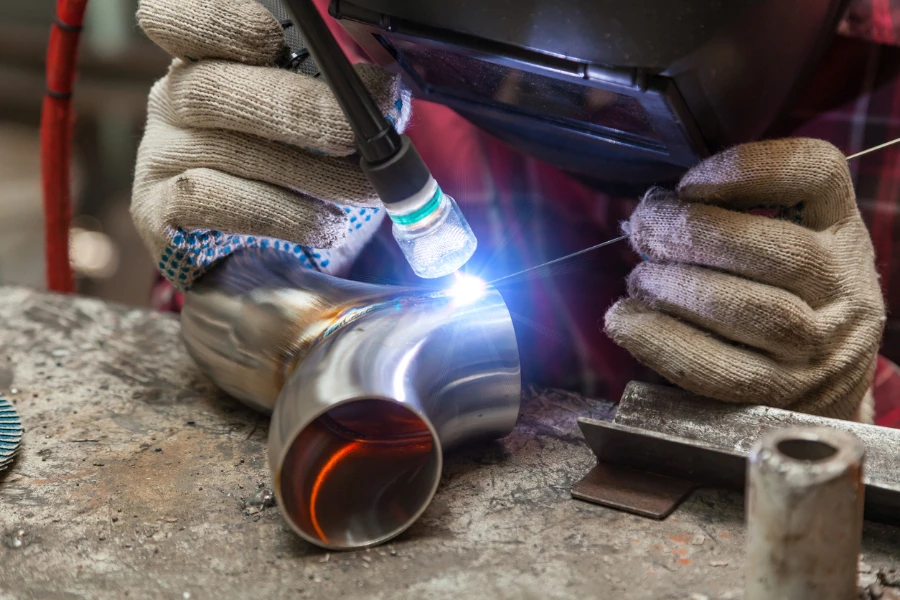
AC/DC TIG welders are versatile machines that can switch the current depending on the metal one is working on. They deliver reliable and consistent performance and can be used for various applications, including pipework, joint work, and automotive repairs.
AC welding is used for welding aluminum and magnesium while DC welding is used for mild steel and stainless steel. AC/DC welders offer variable current settings, up/down slope settings, a foot pedal, and several time controls, allowing welders to create a variety of welds and work on different types of metals.
Pros
– They can weld various metals, including steel, aluminum, and exotic metals.
– Switching between AC and DC gives one confidence to work with the machine.
Cons
– They can be more expensive than DC welders.
DC TIG welder
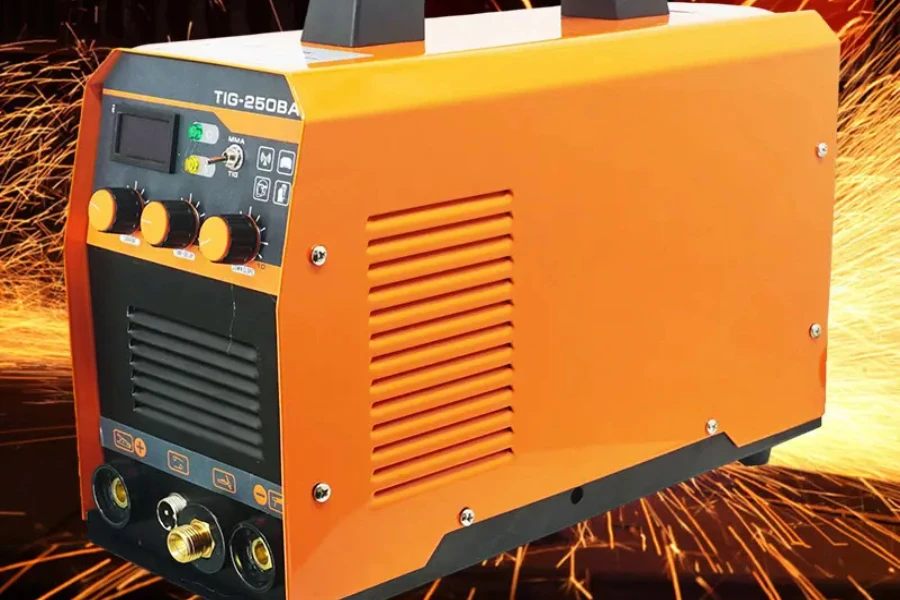
A DC TIG welder is a welding machine that uses DC to weld metals such as mild steel, stainless steel, and carbon steel. This means the current flows only in one direction to create high-quality welds.
Pros
– They can produce good-quality steel welds.
– They produce less smoke and fumes when welding.
Cons
– Overheating is a big problem with DC machines.
– The formation of too many craters leads to welds cracking upon cooling down.
Pulse TIG welder
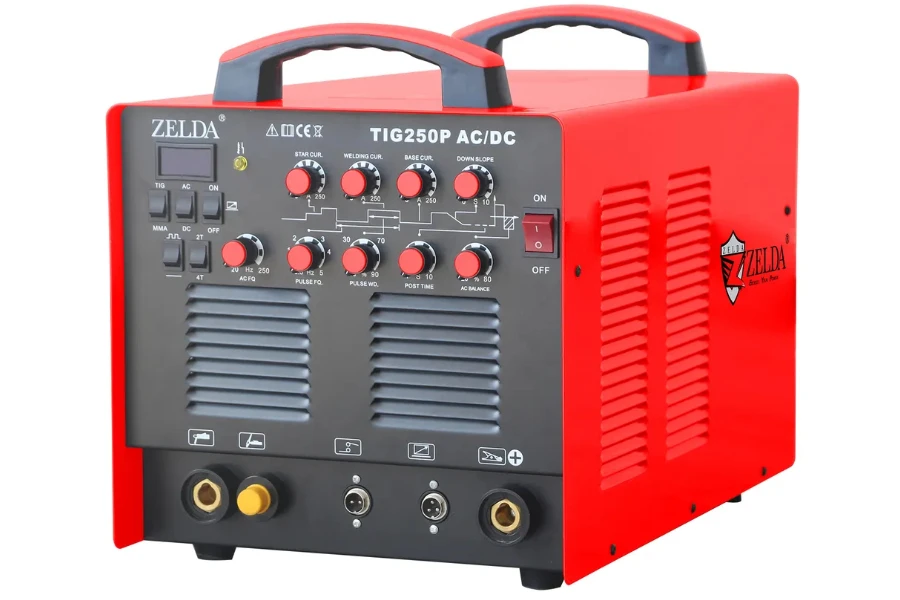
These technologically advanced TIG welding machines alternate between high and low power, giving welders more control and precision while welding the metals.
Pros
– They can produce clean and precise welds even on difficult-to-reach surfaces.
– They produce welds faster due to their ability to precisely control the duration and shape of the welding arc.
– They are highly energy-efficient.
Cons
– They are typically more expensive than traditional welding techniques.
– It requires a high level of skill to use them correctly.
– They produce intense heat and generate several potentially dangerous gases and fumes. Therefore, they require appropriate safety measures to be taken when operating them.
Conclusion
TIG welders provide accurate and precise welds as compared to traditional welders. If choosing a suitable welder is challenging, businesses can follow the above tips for making an educated decision. They should therefore have an easy time choosing a TIG welder that offers quality and durable welds.
Also read: The Differences Between MIG and TIG Welding