Heat exchangers are commonly used for electrical cooling, and even basic designs can significantly help reduce overhead costs associated with electrical cooling. However, heat exchanger designs have evolved significantly over the years to meet more advanced electrical cooling requirements, making choosing the right one more difficult than ever. Scroll down to see about the latest designs and their applications.
Table of Contents
Heat exchanger market analysis
What are heat exchangers
What to consider when selecting a heat exchanger
Conclusion
Heat exchanger market analysis
The global heat exchanger market was valued at US $17.58 billion in 2022 and is projected to grow at a CAGR of 5.1% between 2023 and 2030. The increasing demand for improved thermal management in different sectors, such as food, oil and gas, petrochemicals, energy production, and refrigeration, is expected to boost growth during the forecast period.
Furthermore, technological advancements to enhance heat exchangers’ durability, cost, energy efficiency, and compactness will fuel sales over the coming years. The US emerged as the top market in 2022, owing to industrialization and rapid investments in renewable power generation. Other significant power markets include Japan, China, India, and Russia.
What are heat exchangers?
Heat exchangers are devices that transfer heat energy from one fluid liquid to another to control the temperature of a substance. Heat exchangers typically separate two liquid streams, one cold and one hot, using a thermally conductive plate, moving thermal energy from one stream to another. Common heat exchangers include boilers, furnaces, refrigerators, air conditioners, and automotive radiators.
Heat exchangers are commonly classified into three types based on their design: plated, shell and tube, and ACHEs. These three types differ greatly in design, complexity, and applications.
Plated or plate-type heat exchangers
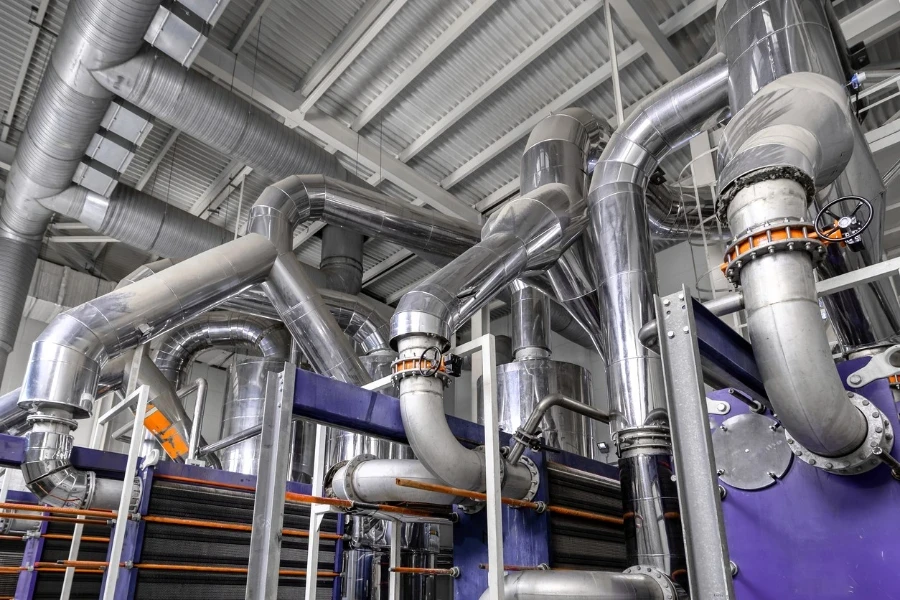
The metal plates used in these heat exchangers act as a thermally conductive barrier between the fluids. Cold and hot liquids circulate between the plates, while fixed vanes known as baffles direct the heat exchanger selection guide between them. Because of their larger surface area, plates are more efficient than tube exchangers. However, sealing large gaskets between these plates is difficult, limiting these devices to small-scale production and low-viscous applications with minimal-to-moderate operating pressure and temperature requirements, typically under 150 °C.
Advantages
Plate heat exchangers are thought to be five times more efficient than shell and tube designs because they can recover more heat. They also take up less floor space, have a longer service life, and require little maintenance. The plates can also be easily inspected or cleaned. Furthermore, plate heat exchangers have low operating costs thanks to being able to achieve high heat transfers via a small surface area. The main expense comes from the replacement of gaskets and, on occasion, plates.
Plate exchangers are an excellent choice because they use a close-temperature approach, in which cold fluid is heated to a temperature close to an entering hot fluid, allowing for more regeneration and heat recovery. They also make a good choice for areas with limited space.
The modularity of this product is an additional benefit: they are easy to assemble and disassemble on-site because they weigh only 6% as much as shell and tube units.
Shell and tube heat exchangers
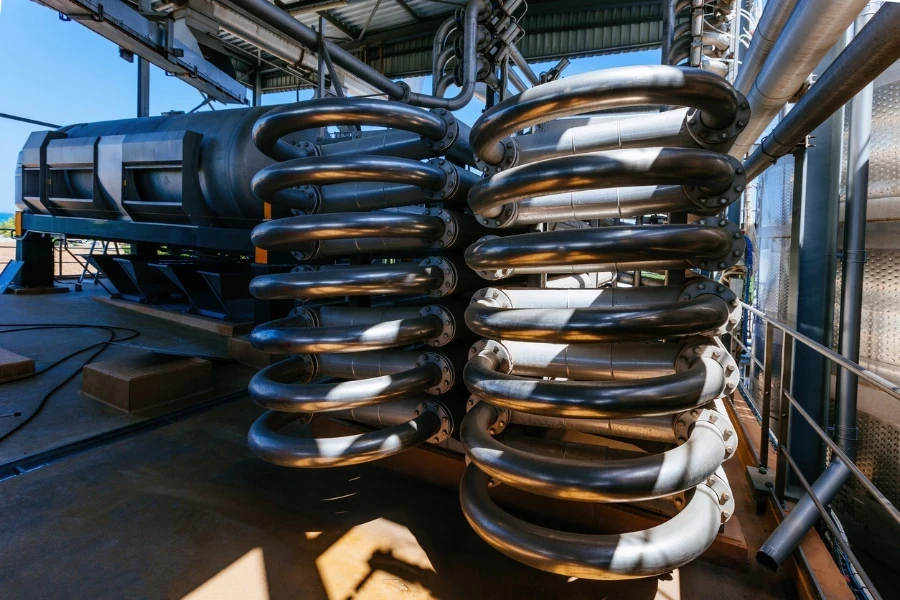
In shell and tube heat exchangers, a series of rectangular or round tubes are enclosed in a larger, cylindrical-shaped casing. The fluid to be heated or chilled flows through these tubes, while the secondary (heat transfer) fluid flows over them inside the shell. This flow is directed by baffles, which also support the tube bundles.
This type of exchanger is quite popular, accounting for 60% of all heat exchangers. They can be used in both low and high-pressure and temperature environments, but their robust construction makes them best suited for high-pressure applications. They also have a high weight-to-volume ratio for heat transfer. Shell and tube types are commonly used in steam generators, power plants, and oil and hydraulic fluid cooling applications in engines.
Advantages
Because of the large clearances between the shell and the tubes, this design is well-suited for fluids containing particulates. They can also handle higher-pressure heat transfers better than other models because they have a large pressure vessel shell with tube bundles inside.
In addition, fluids are less likely to foul the equipment in shell and tube designs. Fouling refers to the accumulation of deposits from the fluids that pass over during the heat transfer. Furthermore, when processing high-fouling liquids, baffles can be added to the tube to increase turbulence and reduce the possibility of particles sticking to the insides of the tubes.
Air-cooled heat exchangers (ACHEs)
Air-cooled heat exchangers, also known as fin fans, use air to reject heat from a fluid stream directly. Fans push air over the surface of the tube bundles or plates, which contain the processing fluid. They are a great alternative to standard water-cooled shell and tube heat exchangers, especially when water is scarce.
This type of heat exchanger is used in a variety of applications. They are easy to operate and maintain because air does not cause corrosion or contaminate the fluid. Furthermore, environmental issues are also considered less of a concern with air cooled heat exchangers.
Advantages
ACHEs are thought to be more efficient than shell and tube designs. Because they have a closed-loop system, they pose little risk of fluid contamination. Additionally, they don’t require the use of any water, preventing water shortages and eliminating the need for a water treatment facility. Furthermore, they require little maintenance and don’t need frequent cleaning.
What to consider when selecting a heat exchanger
The first step is to thoroughly analyze the heat exchanger’s design and applications from various perspectives. This includes examining its electrical system, thermal management properties, design, and other aspects. Furthermore, the system should be the right size to fit into the available space and provide optimal cooling efficiency. The results of this analysis will aid in determining the best type of heat exchanger for the application at hand.
Ambient cooling
When choosing heat exchangers, it pays to learn about the benefits of ambient cooling:. the process of maintaining the electrical enclosure’s internal temperature just above the external ambient temperature. In many cases, ambient cooling meets a system’s cooling requirements.
Cooling can be accomplished using environmentally friendly methods, such as using cooling fluids to absorb and transfer waste electrical heat. Furthermore, switching from traditional methods, such as air compression units, to natural ambient cooling can result in more energy-efficient and low-maintenance operations.
Thermal management
As outlined above, a more streamlined cooling system has numerous advantages, including lower operating costs. Businesses should, however, consider other areas where thermal management can be streamlined and whether a suitable heat exchanger can make that possible.
For instance, many use in-house wastewater treatment processes that necessitate the consistent use of heat. If possible, heat exchangers can be designed to repurpose waste electrical heat for other applications, such as wastewater treatment.
Applications
Shell and tube exchangers are used in a variety of industrial processes, including steam generation, oil refining and cooling, and industrial cooling. Plated heat exchangers, on the other hand, are commonly used in furnaces and chemical processing plants.
Air-cooled heat exchangers are widely used in the oil and gas industry, petrochemical plants, and refineries in high-pressure and high-temperature conditions, as well as corrosive fluid environments.
Conclusion
Heat exchangers are widely used across industries to transfer heat from one medium to another. Understanding the advantages of each heat exchanger design enables individuals to make better choices when it comes to selecting the right one for them, increasing productivity and precision. Visit Alibaba.com to see all of the latest innovations.