Manufacturing is a lengthy process requiring machine efficiency to boost productivity while cutting labour costs. Sheet metal is a flexible material that can be bent, cut, or stretched to form the desired shape of a final product.
With that in mind, continue reading to learn about the market for sheet metal fabrication equipment and important things to consider when sourcing these machines.
Table of Contents
Demand and market share of sheet metal fabrication process machines
Factors to consider when choosing a sheet metal fabrication process machine
Types of sheet metal fabrication process machines
The target market for sheet metal fabrication process machines
Final thoughts
Demand and market share of sheet metal fabrication process machines
The market for metal sheet fabrication equipment is at US $66 billion as of 2022 and is projected to hit US $103.43billion by 2027. It’s expected the market share will grow at a compound annual growth rate (CAGR) of 9.62%.
The demand for sheet metal is soaring with an increasing world population and industrial expansion. The Asia Pacific leads with the demand for metal sheet fabrication equipment.
This demand is due to a constant need for technological equipment incorporating sheet metals that require shearing, cutting, bending, and punching. Some of the industries that are fueling the demand include:
- Aerospace
- Agriculture
- Automotive
- Medical equipment
- Electronics
- Construction
- High-speed trains
- Ship building
Factors to consider when choosing a metal sheet processing machine
Material type
Some machines work best in the lower range of metal sheet thicknesses of 0.5mm to 2mm. Others are suitable for metal sheets between 2mm and 6mm. A metal sheet is any metal between 0.5mm and 0.6mm.
Processing length and thickness, roughness and accuracy level
Metal sheets come in varying lengths, widths and thicknesses. Sometimes a part of the processing may include cutting a long metal sheet into pieces, punching holes, or rolling them. If the metal sheets are long, a set up of machines in a production line is the preferred option.
Large operations with little variations favor automated production lines that don’t need the presence of persons. The worker’s responsibility is to monitor the process and perform quality checks.
For lightweight processing, some plate roll machines are manually operated. They can handle metal sheets with a thickness of 1.5mm, a width of 915mm, and a length of 1300mm. Such machines are suitable for manual conical rounding of metal sheets.
Heavy-duty metal sheet fabrication involves the use of computer numerical control (CNC) machines. CNCs are best for accurate, quick processes over a long period to meet high quantity production demands.
Purchasing needs
How heavy or light the fabrication will inform the type of metal sheet machine needed. For heavy-duty metal sheet fabrications, laser CNC cutters are highly recommended. Less demanding and slow low-carbon steel fabrication will work well with manual metal sheet machines.
After determining how heavy or light the fabrication needs to be, other factors include volume, variation, and speed. Therefore, metal sheet fabrication can be classified into three automation categories that usually inform the purchasing needs:
- High volume with a bit of variation: Fully automated and doesn’t allow manual operations
- Average volume with variation: Automated but allows intermittent manual operations
- Low volume with high variation: Allows a lot of manual operation, mostly shifting positions.
Machine’s tonnage
Metal sheets that are 6mm thick fall under the category of heavy sheet metal. Specific machines work best with such thickness. A good balance between how heavy the fabrication is, speed, and quantities of production expectations will determine a machine’s tonnage.
For thick metal sheets, automated machines are efficient in enhancing the accuracy and quality of fabrication. Essential automated metal sheet machines can feature:
Shears: Prevalent for cutting metal sheets and can use pneumatic or electric power
Press brakes: Typically used to form by bending to achieve bumps on metal sheets or churn out conical shapes
Turret punch: A machine that accurately punches many holes simultaneously on a sheet. It is mainly used for low volume production and accommodates retooling to facilitate other types of metalwork other than sheets.
For light work, manual metal sheet machines are a perfect fit. They are suitable for low quantity and low rate production.
Material grade
Different metal sheet grades are suitable for specific fabrications. The varying components in the metal determine its grade, advantages, and disadvantages, plus its suitability for fabrications.
For instance, stainless steel comes in three categories, mainly:
Austenitic: Easy to form, non-magnetic, and contains high amounts of chromium and nickel. It’s well known for being corrosion resistant.
Martensitic: It has different hardness levels, is heat treatable, and is corrosion resistant.
Ferritic: It has magnetic properties, features a lot of chromium, and is not suitable for heat treatment but is highly corrosion resistant.
Machines engineered for stainless steel fabrications are best suited to produce products made of the same. Stainless steel sheets are ideal for producing items that need high corrosion resistance.
The same principle applies to high carbon and low carbon metal sheets. High-carbon steel contains 0.6 – 2.5% carbon, while low-carbon steel has a maximum of 0.2% carbon.
High carbon metal sheets are suitable for products that require durability and high resistance to warping under harsh conditions. Also, the sheets need coating since they are prone to corrosion.
Low-carbon metal sheets are easy to fabricate and easily corrode. So, for the best outcome, carbon metal sheet machines are best suited for fabrication.
Types of metal sheet fabrication process machines
Metal sheet fabrication machines come in different types that suit specific operations like cutting, bending, rolling etc. They each have their respective pros and cons, which determine their ideal use. Read on for a rundown of the main types.
Hydraulic press brakes
Hydraulic press brake machines bend sheet metal repeatedly to form a desired shape or design. Two factors define the hydraulic press brakes; their bending length and the punch capacity to bend metal.
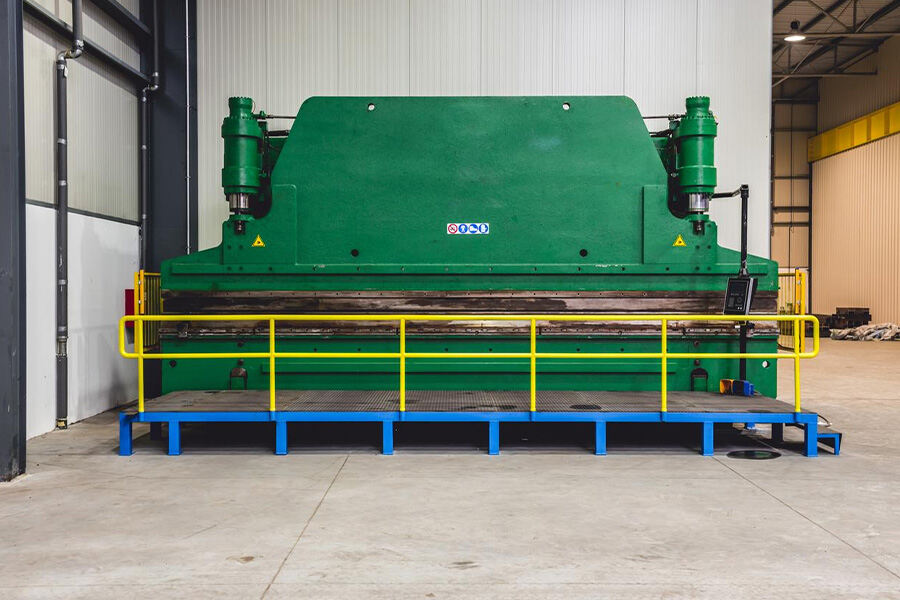
Pros
- They are more flexible than electric ones and offer versatility in terms of programming.
- The material wastage is minimal.
- They offer options of manual, semi and full automation.
Cons
- Prone to leaks.
- High temperatures in the hydraulic chambers cause oxidation of hydraulic fluid, affecting the system’s lubrication.
- They lack speed.
- They consumes a lot of energy.
Swing-beam shears
The shears machine is used to cut metal sheets by using top and bottom blades with a pivoting movement. When cutting the sheet metal, the top blade moves away from the lower blade to avoid rubbing against each other.
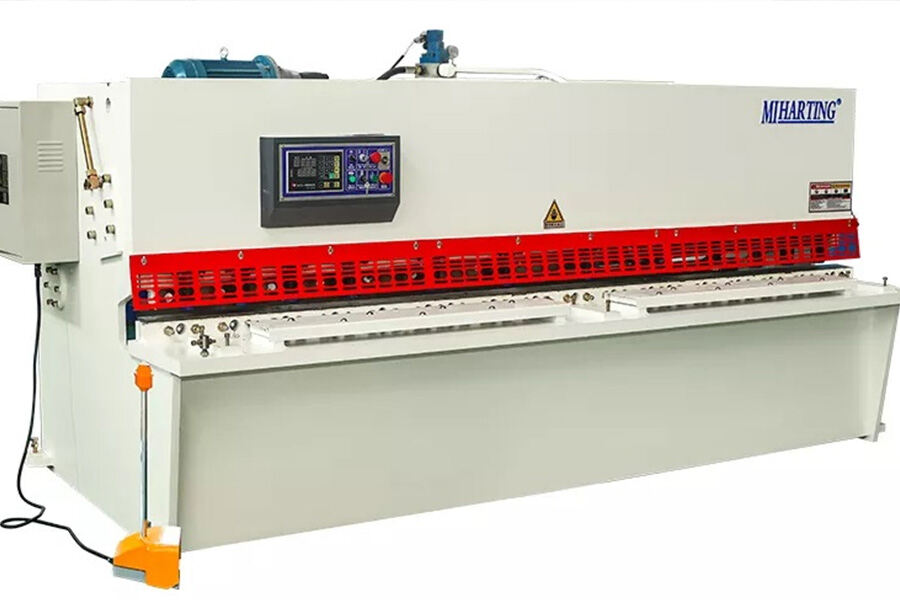
Pros
- Suitable for heavy industrial use where large quantity production is expected.
- Very precise for metal sheet cutting.
- The mechanical ones can run all day. Ideal for industrial setups.
Cons
- Not ideal for more challenging types of metals.
- Not ideal for clean cuts. It leaves burrs on the cut edges.
- Prone to causing deformation on long metal sheets.
Ironworkers
An ironworker machine combines several machines for bending, punching, shearing, cutting, and other functions designed for sheet metal. Ironworkers are multipurpose and can perform several functions simultaneously.
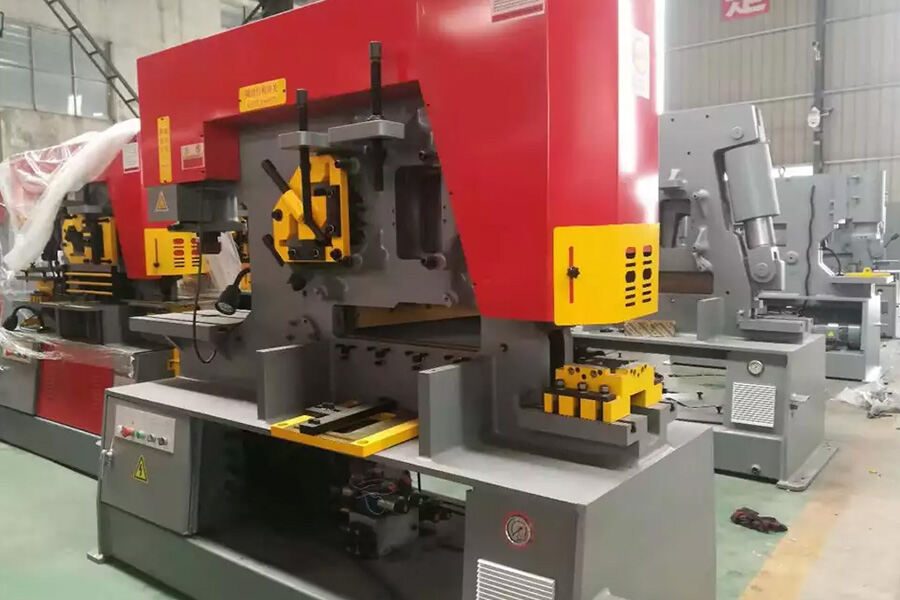
Pros
- It’s versatile: it can shear, punch holes, form, bend, and notch.
- Typically lightweight.
- Utilizes less space because of its versatility.
- Reduces the workforce and person-hours needed at every stage of the process. One individual can conduct different processes.
Cons
- It’s not suitable for heavy industrial use.
- When retooling, some configurations reduce the amount of cargo.
- It has limits in terms of the tonnage it can be subjected to.
Plate rolls
A plate roll machine bends sheet metal to cylindrical or conical forms. The sheet metal slides in between two, three, or four rollers to churn out the envisioned design.
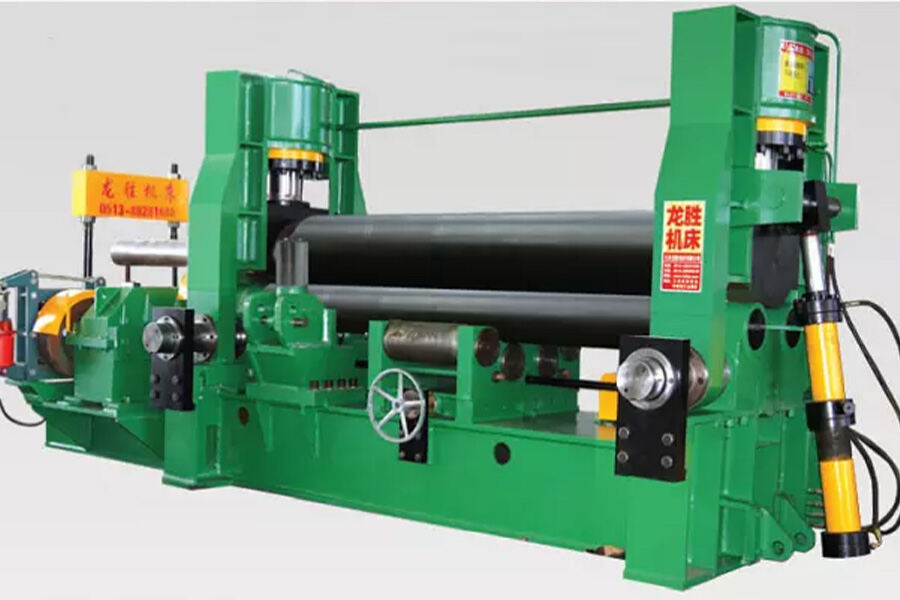
Pros
- Makes cone rolling easier.
- Accurately bends difficult shapes.
- Easy to operate.
Cons
- It can produce deflection problems when the rolling force subjected to a piece is a lot.
- They are pricier than other metal sheet machines.
Cutting machines
A cutting machine is used to cut sheet metal with precision. Some cutting machines use lasers, plasma, or water jets. Each works best for specific types of sheet metal.
Pros
- They are precise and accurate.
- They don’t wear out since there is no surface contact.
- They consume less power.
- They have low maintenance costs.
Cons
- They require experts to operate them.
- They’re limited to a certain metal thickness.
- They produce harmful fumes and gasses.
- They can cause some materials to evaporate because of the intense heat.
Plasma cutting machines
Plasma cutting machines use intensely heated gas and a process called the thermal cutting method.
In the cutting process, a high-temperature plasma contacts the metal and melts it while the high-speed gas blows off the molten metal. Plasma cutters are conducive for cutting thick plates.
Pros
- Able to cut metal that is 150mm thick.
- They offer the best quality cuts on metals that are 50mm.
- They’re affordable for doing cuts on medium size metal.
- They’re the best cutter for medium-sized aluminum and stainless steel.
Cons
- They don’t produce clean cuts on thinner sheets of metal.
- The kerf is wider than laser cutting.
- They leave behind larger heat-affected zones (HAZ) on the workpiece than laser cutters.
Laser cutting machines
The laser cutting machine is widely used for precision cutting. It features a highly concentrated laser beam to perform clean, accurate cuts with less burring or etching left on workpieces.
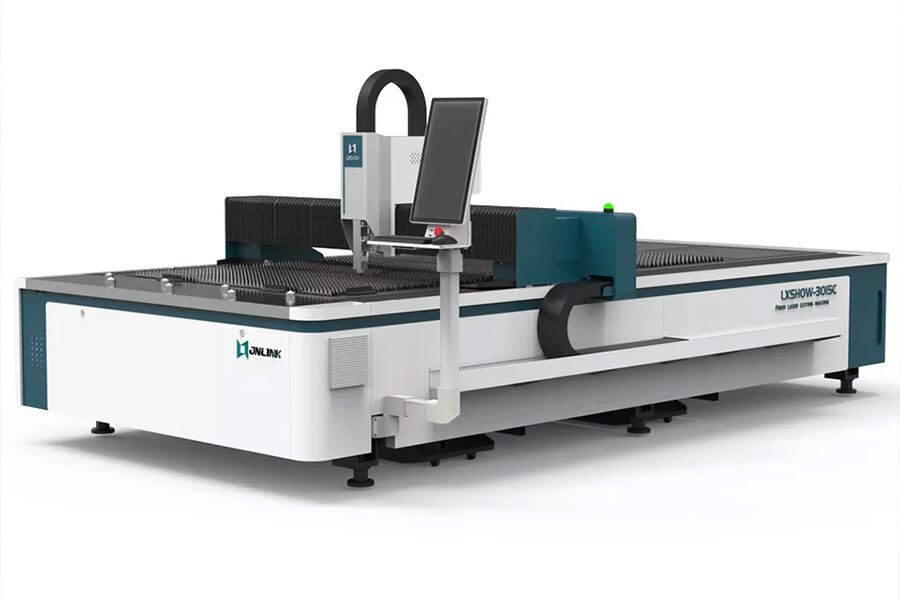
The machine uses the CNC and laser optics that control the laser’s intensity needed for a specific design. They come in varying capacities that will inform whether they will be suitable for small or large-scale use.
Pros
- Offers flexibility: There’s no need for retooling when working with different sizes of metal.
- They offer highly accurate cuts in comparison to other methods using thermal cutting.
- They guarantee high-speed cutting for complex cuts.
- They are highly automated and significantly reduce manpower.
- The cutting is contactless, avoiding any friction on the sheet metal.
Cons
- They produce gasses and harmful fumes because of the melting metal.
- They can cause evaporation of some workpieces.
- Recalibration costs are high if there’s a need for tailoring them to avoid evaporation when cutting workpieces.
The target market for sheet metal fabrication machines
Metal sheet machine fabricators come in different sizes and which can be selected based on whether the user wants to bend, roll, cut, or punch holes. The ironworker machine is convenient because of its versatility for less demanding industrial use. It’s ideal since more than one person can use it simultaneously to perform different tasks in minimal space.
On a larger scale, the automotive industry utilizes cutting, bending, and punching machines for heavy industrial use. Germany leads with the demand for metal sheet equipment in Europe because of their robust automotive industry and ancillary machinery.
Emerging economies like India, Indonesia, China, and the Philippines, as well as more developed economies like Japan and South Korea, contributed to the demand for metal sheet fabrication machines. It’s projected that the CAGR will be 3.9% until 2024.
Final thoughts
The demand for metal sheet fabrication machines is set to go up each year. An ever-increasing global population means more metal fabrication equipment is needed to keep up with the demand for products made with metal sheets.