Lathe machines are instrumental in any metal workshop, performing tasks that go from shaping workpieces to chipping, knurling, and cutting tools. Because of their importance, their maintenance is paramount if a workshop is to function seamlessly for a long period. This guide explains how businesses can maintain lathe machines by themselves.
Table of Contents
Why it is important to maintain a lathe machine
Structure of a lathe machine
How to maintain a lathe machine
Final thoughts
Why maintenance of a lathe machine is important
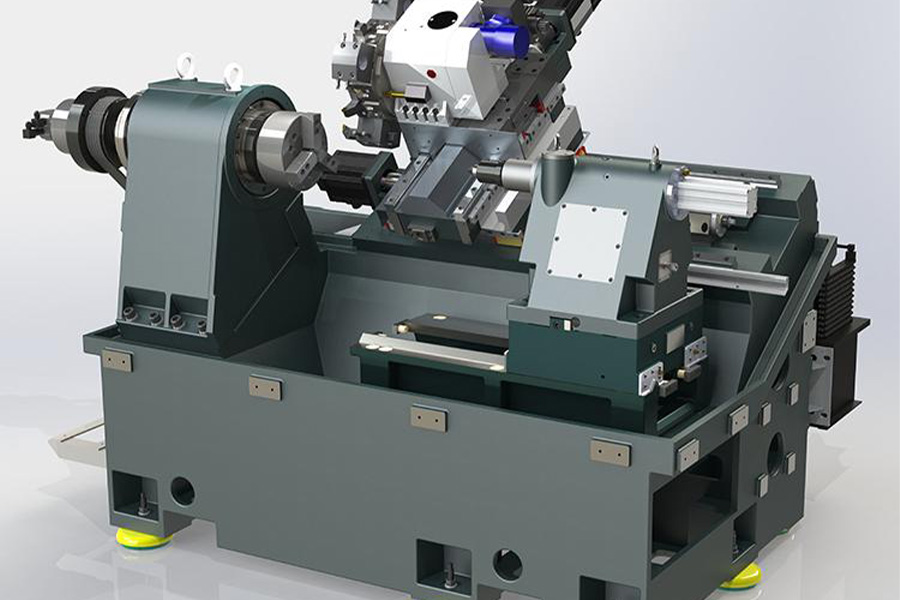
Lathe machines require frequent maintenance because they are susceptible to wear and tear when they are used. Maintenance ensures that this wear is managed and the machine is in good working condition. Besides, it reduces the cost of repair compared to when the machine breaks down due to lack of maintenance and can also reduce the number of repairs that a machine requires. Lastly, maintenance also helps increase the work safety of the machine operators. While personnel safety is dependent on the personnel, maintenance prevents sudden breakdowns that may injure personnel.
Structure of a lathe machine
Bed: It is the basic part of the precision guide and holds all the parts of the lathe machine.
Spindle box: It transmits power from the motor to the spindle through transmission mechanisms.
Feed box: It is used to change the speed of the motor before transmitting the power to the tool holder.
Tool holder: It is used to install the cutter and drive the tool. It consists of slide plates, a knife frame, and a bed saddle.
Tailstock: It is mounted on the guide rail of the bed and moved around to adjust the working position.
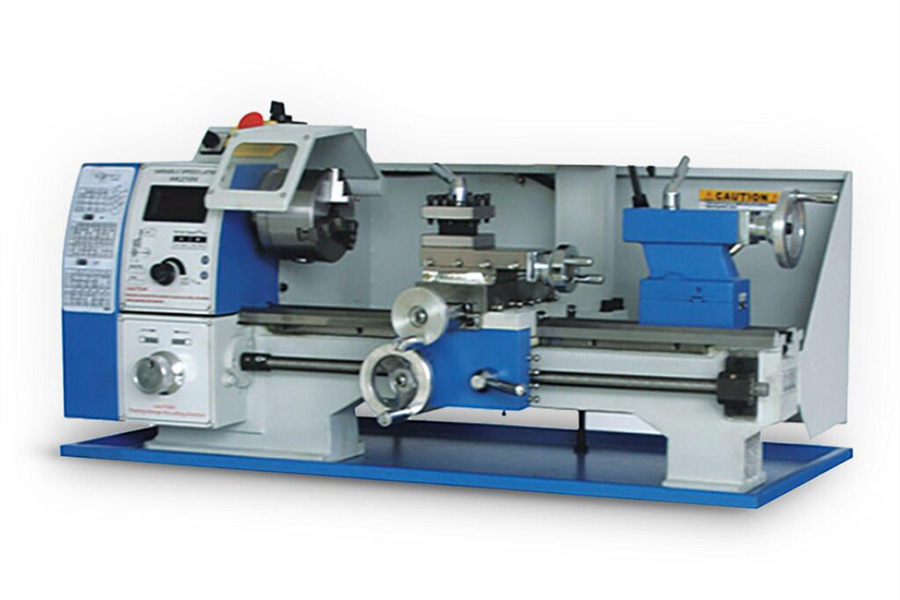
Cooling device: It releases the cutting fluid to the cutting area to reduce the temperature of the workpiece, clean it and lubricate it.
How to maintain a lathe machine
There are several things to be considered when maintaining a lathe machine. Maintenance should ideally happen every 40 hours to ensure it functions well.
Use a lathe board
A lathe board helps hold materials from falling. When the operator is changing components of the lathe machine, such as chucks, centerpieces, or the workpiece, and they slip, the lathe board holds them. It prevents them from falling to the ground, which would result in significant damage to the pieces.
Keep tools off the lathe ways
Any tools necessary while working with the lathe machine should be placed on a separate table and not on the lathe ways. While it may seem convenient to put tools on the lathe ways, the vibration when running may cause them to fall into the lathe machine. This is a health hazard to the personnel and can also cause severe damage to the machine.
Lubricate
The lathe machine is primarily made of metal components. Lathe operators should always ensure that the machine is well lubricated before operating. Failure to do so could lead to severe compromise in the precision of the metal cutting tools. The oil level in the reservoir tanks should be checked frequently and topped up if it has dropped below the halfway mark. The feed screws, moving joints, and bearings should also be lubricated to work smoothly before any project. In addition to lubrication, the coolant reservoir should be inspected periodically. While the coolant may not be as frequently used as the oil, it is recommended to ensure that its reservoir is filled.
Clean spindle tapers
Spindle tapers can experience axial or radial runout. Axial runout occurs when the spindle rotates outside its axis. Radial runout is an error that occurs in the motion perpendicular to the spindle axis. The spindle tapers should be inspected and cleaned with a soft, lint-free cloth when tools are being changed. A coat of all-purpose machine oil should also be applied.
Clean dust
Working with cast iron, plastic or wood will produce dust. This dust can cling to workpieces and on the lathe machine. Dust from cast iron is abrasive and can stick to the machine’s lubrication. Operators need to wipe off the dust on the machine, workpieces, and way wipes. The way wipes should be replaced once they are worn out. Fine metal chips can cause damage to the chuck if not removed. The lathe jaws should therefore be detached before inspecting the chucks for any fine metal chips lodged there during operation.
Protect the machine from rust
Rust is always a big factor to consider when working with metallic machines. Proper protection has to be made for machines. It is essential with machines near large sea bodies because of the high humidity levels. Rust can cause weakening of the lathe machine structure, corrosion, and damaged parts. To guard against rust, lathe machines should be cleaned regularly and coated with oils that inhibit corrosion. The machine should also be covered when not in use. The cover should be ventilated if the lathe machine will remain in storage for long.
Calibrate the precision level after maintenance
After maintenance of the lathe machine, some of the settings may have been tampered with. Recalibration of the machine is recommended after maintenance. This will also allow the operator to understand the limits of the accuracy of the lathe machine. Regular maintenance and calibration also result in the production of accurate workpieces.
Final thoughts
In addition to describing the lathe machine and its features, this guide has looked at essential tips that a business can use to ensure their lathe is in good working condition throughout. More information on lathe machines can be obtained on Alibaba.com.