Stamping and punching are common metal-working processes employed in the creation and shaping of metal sheets. The use of these processes has significantly increased in recent years due to the increased demand for metal sheets resulting from global economic growth, industrialization, and urbanization. Metal sheets are often used in multiple industries, including automotive, electronics, construction, and medical.
While stamping and punching may sound similar, each procedure uses a specific piece of equipment to achieve different purposes and outcomes. Read on to discover the differences between these processes and their impact on the quality and shape of the metal sheets processed.
Table of Contents
Metal stamping market overview
Metal punching market overview
Major differences between stamping and punching
Choosing between stamping and punching
Conclusion
Metal stamping market overview
The global metal stamping market was valued at US$ 211.79 billion in 2022. It is projected to reach US$ 218.60 billion in 2023 and US$ 310.69 billion by 2030, growing at a compound annual growth rate (CAGR) of 4.9%. The Asia Pacific region is projected to record the highest CAGR due to the growing demand for cars and consumer electronics such as phones.
The numerous factors driving this market growth are:
- Increased demand for industrial machinery
- Growing demand for electrical and electronic products
- Ongoing emphasis on lightweight but structurally strong materials for use in industries such as aerospace, electronics, and consumer goods
Metal punching market overview
The global punching machine market size was projected to grow by US$ 318.65 million between 2021 and 2026, at a CAGR of 3.47%. It is estimated that 62% of this growth will originate from the Asia Pacific region, with China, South Korea, and Japan as the key markets. This region’s continued establishment of manufacturing facilities will drive growth and demand, while factors driving punching machine market growth and demand globally include:
- Rising global industrial automation
- Higher investments in emerging economies to support the manufacturing sectors
- Increased interaction with advanced technologies, including 3D printing
Major differences between stamping and punching
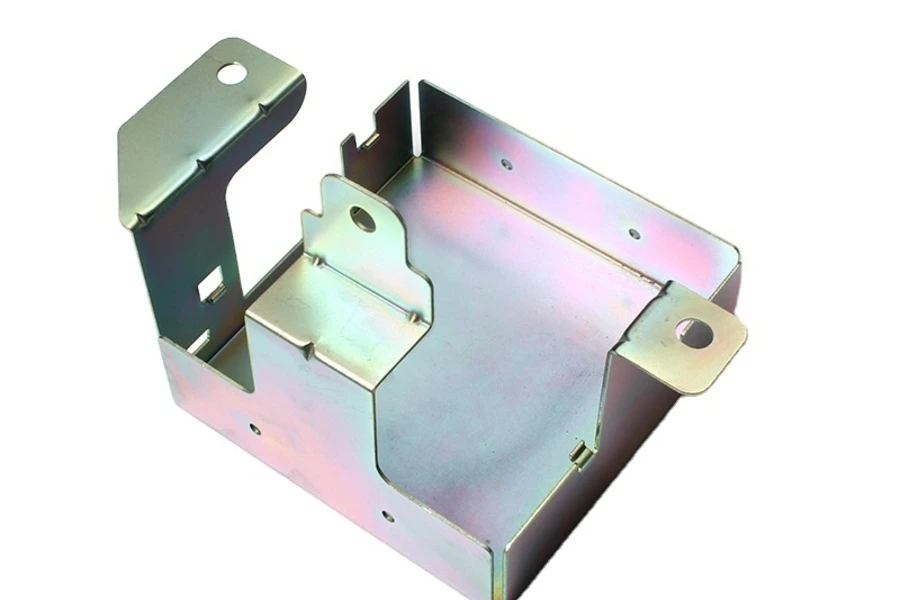
Stamping and punching are two distinct metalworking procedures for shaping, cutting, or forming sheet metal. While stamping involves applying force to shape or deform the metal sheet using a die, punching entails creating holes or simple shapes using a punch and die. This section explores the major differences between these procedures.
Typical processed parts
While stamping and punching are both metal processing techniques, they differ in the types of parts they produce.
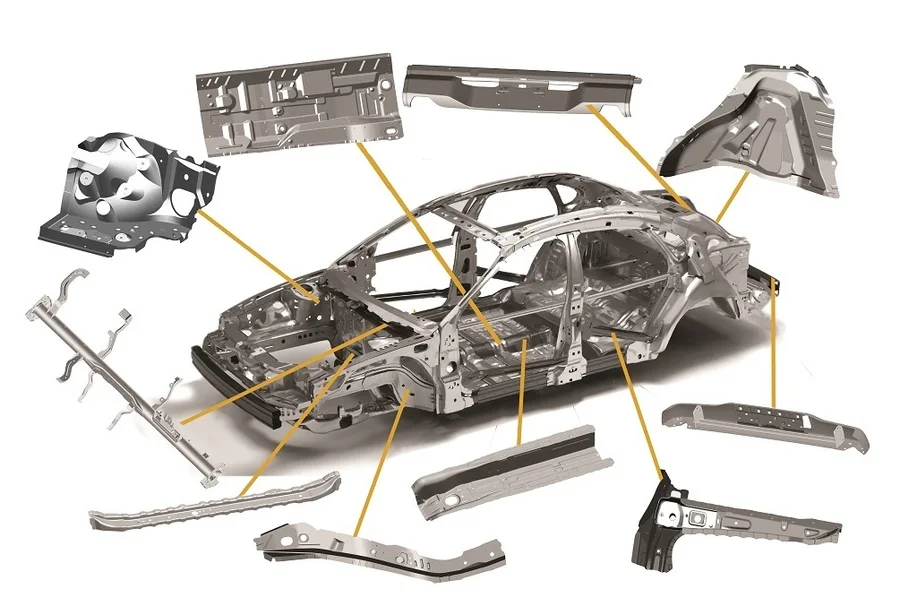
Stamping is a more versatile process used to produce complex shapes and features. As a result, it is often applied in multiple industries, including:
- Automotive industry: Stamping is used to manufacture body panels for automobiles such as doors, roofs, fenders, and engine components.
- Aerospace industry: Stamping is also used in the aerospace industry to produce components such as wing panels, aircraft fuselage sections, seat components, airframes, fasteners, and screws.
- Home appliance industry: it is used to manufacture various parts such as oven doors, washing machine drums, refrigerator door panels, and dishwasher racks.
- Electronics industry: metal stamping techniques are used to fabricate components in electronic devices such as cellphone housings, connectors, and computer cases.
- Medical industry: metal stamping is used to manufacture various parts found in medical devices, such as surgical equipment and implantable devices.
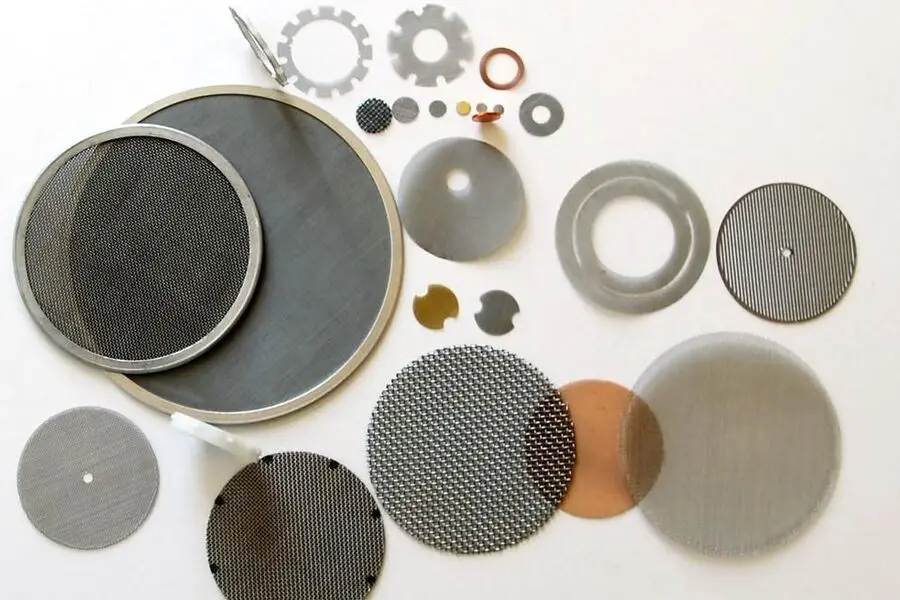
Punching, on the other hand, is used to produce various components in industries such as:
- Packaging and printing: metal punching is used in the packaging and printing industry to create specialized shapes, perforations, and functional features, such as tear strips and perforations for easy opening.
- Automotive: punching technique is used in the automotive sector to fabricate components such as mounting plates and brackets.
- Filtration and sieving: hole punching and perforation methods are highly used to produce sieves, filters, and screens in water, air, and industrial filtration systems.
Purpose and operations
Stamping is a metalworking procedure that uses a press machine and dies to shape or deform sheet metal. The metal sheet is placed between 2 die components, and a mechanical or hydraulic press is then used to apply force. This force causes the sheet metal to take on the shape of the die cavity. Stamping is more suitable for projects that require creating complex shapes, contours, or patterns in sheet metal.
Punching is a technique used to create holes or simple shapes in sheet metal using a punch and die set. The operator cuts through the sheet metal to remove the material in a single-step process, where the punch strikes the metal, and the die provides the desired shape or opening.
Process applications
Stamping utilizes highly specialized computer-aided drafting and manufacturing (CAD/CAM) software to shape the metal sheet with precision and expertise. It is often performed in a multi-step process that requires precise control and coordination. The various processes that can occur during metal stamping include:
- Forming
- Blanking
- Piercing
- Drawing
This process is suitable for creating intricate parts, deep-drawn components, and embossed designs. It can be applied in various industries, including automotive, renewable energy, medical, industrial hardware, and home improvement.
Punching, in contrast, occurs when the punch exerts pressure on the sheet metal, removing a piece of the material due to the cutting force. In this case, the final workpiece takes the shape of the punch and die. While the primary goal in stamping is to shape or deform the sheet metal, punching aims to create holes or basic shapes.
Material thickness
Thickness in stamping and punching processes is measured in gauge, where the lower the gauge, the thicker the material.
Stamping is suitable for both thin and thick sheet metal. The sheet metal thickness can range from the thinnest, 38 gauge (0.0063”/0.16 mm thick) foil to the thickest 7-gauge (0.5”/12.70 mm thick) plate steel. Sheet metal steel above 25 gauge (0.020”/0.56 mm thick) is considered a heavy gauge.
However, punching is more suitable for projects involving relatively thin sheet metal. The material thickness in this process should be between 10-34 gauge.
Material utilization
There is minimal material waste in stamping since complex shapes can be formed from a single piece of sheet metal. The multi-step process allows the stamping engineer to utilize the entire surface of the sheet metal.
In contrast, the punched-out sections in punching become scrap materials. However, using an efficient tooling design can help reduce waste.
Choosing between stamping and punching
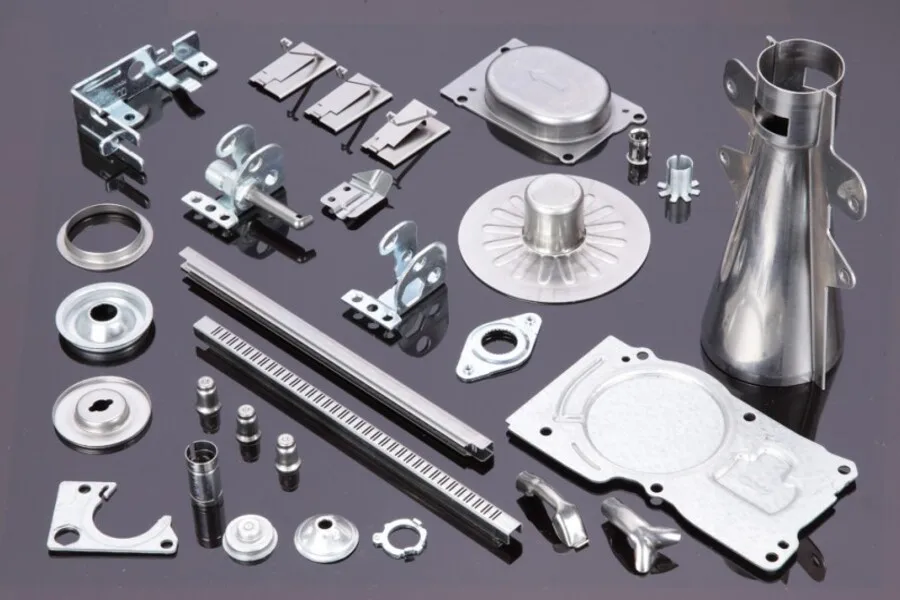
There are various factors to consider when choosing between stamping and punching, especially because the two processes are better suited to different outcomes. It is therefore crucial to consider the desired end result before opting for one technique over the other. Other considerations include the following:
1) Design complexity
Stamping is more suitable for projects involving complex shapes or contours. The process facilitates automated material handling integration, where the coil feeders and blank sheet destackers can be configured to improve flexibility and efficiency. This automation helps streamline the process and improve productivity.
Punching is more appropriate for projects that involve simple shapes or creating holes. The design of the punched products is limited since the size of the punch determines the maximum hole diameter. However, additional punch tools and adjustments can be fitted to achieve the desired hole sizes.
2) Target markets and industry preferences
When selecting punching or stamping for metal work processes, it is crucial to consider the target market and industry needs and preferences. This is because different industries have varying standards or requirements for stamping or punching.
For example, automotive, chemical, and construction are the top three industries in demand for punching machines. On the other hand, the top three industries with demand for stamping are automotive, industrial machinery, and consumer electronics. Therefore, it is crucial to align manufacturing capabilities with customer expectations.
3) Production capacity
Companies weighing between stamping and punching must consider the expected production capacities and capabilities. For instance, stamping offers high-speed production capabilities, making it suitable for projects involving large volumes of parts within tight timelines.
However, punching is ideal for those projects with smaller volume requirements or prioritizes quick turnaround times for smaller batches.
Conclusion
Stamping and punching procedures are crucial in most industrial sheet metal processes. However, in terms of their key applications stamping is generally used for complex shapes or patterns, while punching is used for creating simple shapes or holes. Understanding the project’s scope and desired results helps determine the most appropriate process for optimal results. To explore listings of quality machines that aid both processes of metal stamping and punching, go to Alibaba.com.