Miniature welders are used in jewelry making, as well as for medical, aerospace, and technological applications. These small welders provide a precise and tidy weld in tiny spaces that larger welders cannot access. Purchasing miniature welders for resale caters to a large customer base working across multiple industries, from a hobbyist with DIY tasks or an artistic creation to a welding workshop or large-scale manufacturer.
Read on for an overview of everything you need to know to select the best options for your buyers in 2025.
Table of Contents
What is a miniature welder?
Advantages of using a miniature welder
Types of miniature welder
Key features of miniature welders
Limitations and challenges
How to choose a miniature welder
Future trends in miniature welding
Conclusion
What is a miniature welder?
Miniature welders are compact, high-precision welding machines designed for accurate and delicate small-scale welding tasks. These tiny welders offer a variety of options, such as resistance welding, laser welding, ultrasonic welding, and micro TIG welding, depending on the model and application.
Advantages of using a miniature welder
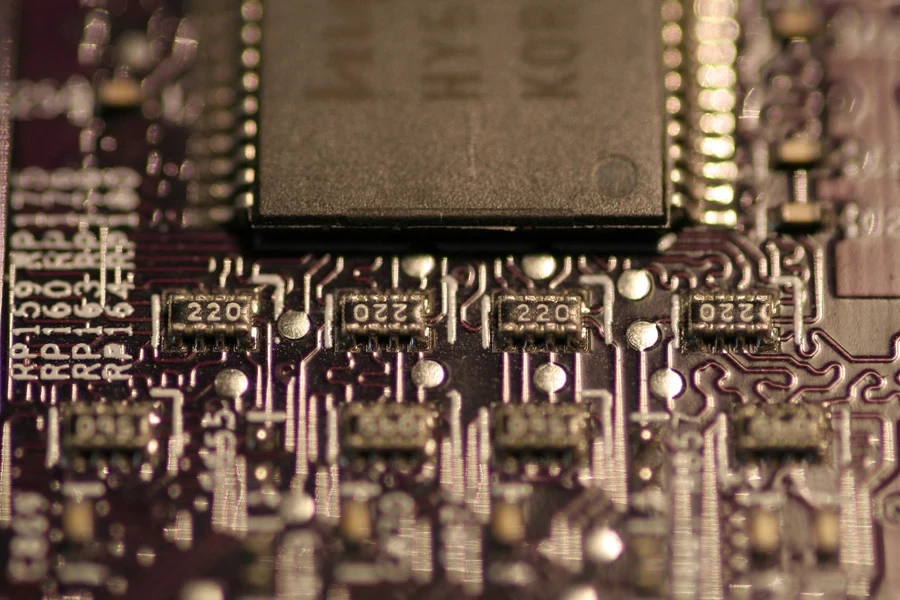
When used in precision work, miniature welders offer many advantages over traditional welders.
Increased precision
Miniature welders are maneuverable and slim, making them ideal to fit into awkward spaces, target small areas effectively, and work with thin workpieces for precise welds. The thin size of the nozzle also means the operator has visibility around the targeted area to ensure they are not welding or damaging other parts.
Cost-effectiveness
Miniature welders are less costly than traditional welders and also have lower power consumption, meaning immediate cost savings. Their compact size also enables operators to work in smaller areas, or even at home, meaning they are cost-effective in a business environment. Additionally, due to their great precision, there is lower material waste than when using a traditional welder.
Versatility
Despite their specialty being small-scale welding, the miniature welder is a very versatile tool that can overcome many problems. Miniature welders can weld a variety of materials, including different kinds of plastic and different types of metal, making them an essential tool in multiple industries.
Ease of use
Miniature welders have a user-friendly interface, with simple and easy to use controls. Functions include the adjustment of heat input or a temperature control box, and other options to control the weld. Consequently, even a beginner operator can use them, so long as they have a steady hand, meaning reduced training time and increased productivity.
Types of miniature welder
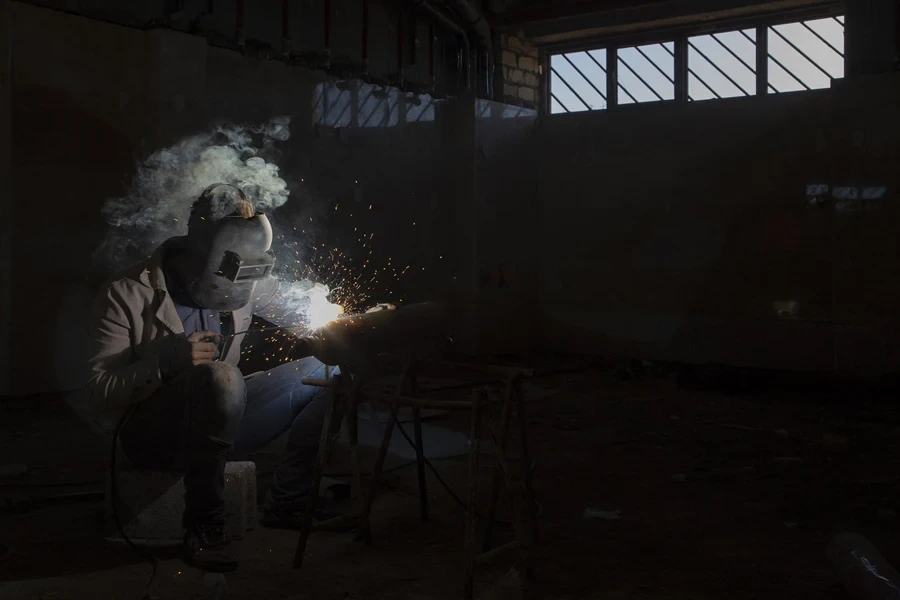
Depending on the task at hand, a person will choose a different type of miniature welder. The best choice will depend on the area and type of welding needed.
Resistance welders
Resistance welders generate heat via electric resistance welding (ERW). This process applies pressure to the two parts, joining them together, and then passes an electrical current through them to weld the materials together. This type of welder is particularly effective for joining thin metals, making it an ideal choice for welding in the electronics and jewelry industries.
Laser welders
Laser welders are able to create a weld without any contact with the material, since they use a concentrated light energy. This means laser welders are able to create high-precision welds without damaging the surrounding area, however, the user must be very skilled and be able to hold the laser very still so as not to weld unwanted components. Laser welders are often used in aerospace, electrical, and medical applications.
Ultrasonic welders
Ultrasonic welders are specialized welders, as they are able to weld via high-frequency sound waves that create friction between two components to generate enough heat to bond the materials. This welding method is particularly effective for welding plastics and certain metal types, making them ideal for medical equipment assembly and the bonding of electronic equipment.
Micro TIG Welders
Micro TIG welders are mini welders used for the smallest welding jobs available. They are used for very small projects, including jewelry making and the manufacturing of medical and electronic equipment.
Key features of miniature welders
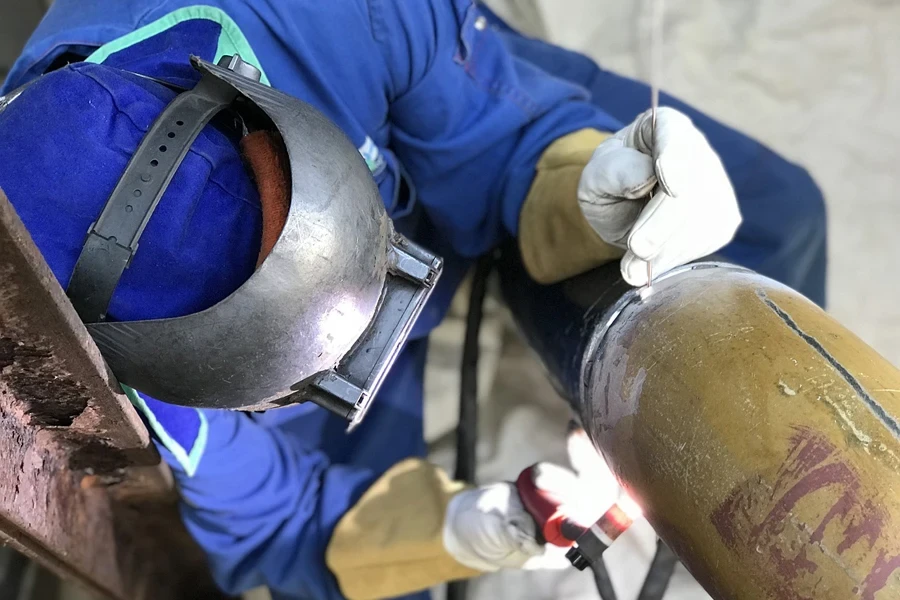
Size and portability
Miniature welders are renowned for their small size, low weight, and portability, making them easy to carry on a shoulder strap while working with multiple tools for specialized micro welding. Their size allows for work in tight spaces, such as in automotive work, or small production areas where there are many people welding in a small area.
Precision and accuracy
Due to their thin nozzles, or their use of laser beams or ultrasonic waves, miniature welders are able to target areas with great precision and accuracy, all while not damaging the surrounding area. This is especially important when the surrounding area is prone to melting when subjected to heat.
Power and performance
Although miniature welders are very small in size, they can still conduct a great amount of heat through a high power output — enough to bind a great variety of materials. However, different miniature welders have different capacities based on the tasks they are built for, so it is important to ensure the right one is purchased.
Safety features
Welding can be dangerous, regardless of the size of the welder. For that reason, many miniature welders come with enhanced safety features, including controlled energy outputs (which should be considered when choosing a welder based on power and performance), automated shut-offs in case of overheating, and protective covers to ensure the personal safety of the operator. Welder operators should also consider wearing gloves, long sleeves, a welding apron and face and neck protection when welding.
Limitations and challenges
Miniature welders offer multiple benefits, however, they also pose some challenges and limitations.
Limited power output
Although powerful, miniature welders may not have the capacity to work on larger projects. An operator may find the job takes a long time if the material being welded is too wide, that the welder cannot reach the necessary heat level if the material is too thick, or that the welder shuts down automatically due to overuse. Miniature welders are much better suited to fine welding or small welding projects.
Maintenance requirements
Maintaining a welder and ensuring the parts are cleaned is vital for proper operation and welding efficiency. This is especially true for miniature welders, as due to their size, a small hindrance on the nozzle could affect the heat distribution, and as such the welding accuracy and performance.
Skill and training
Although many miniature welder designs cater to ease of use, it is still important that the operator has some skill and training for a specialized technique. Fine welding requires high levels of concentration and a steady hand but it is also very easy to get wrong. This is important as when working on items such as electronics or jewelry, one wrong move may mean the item loses its value or must be binned.
How to choose a miniature welder
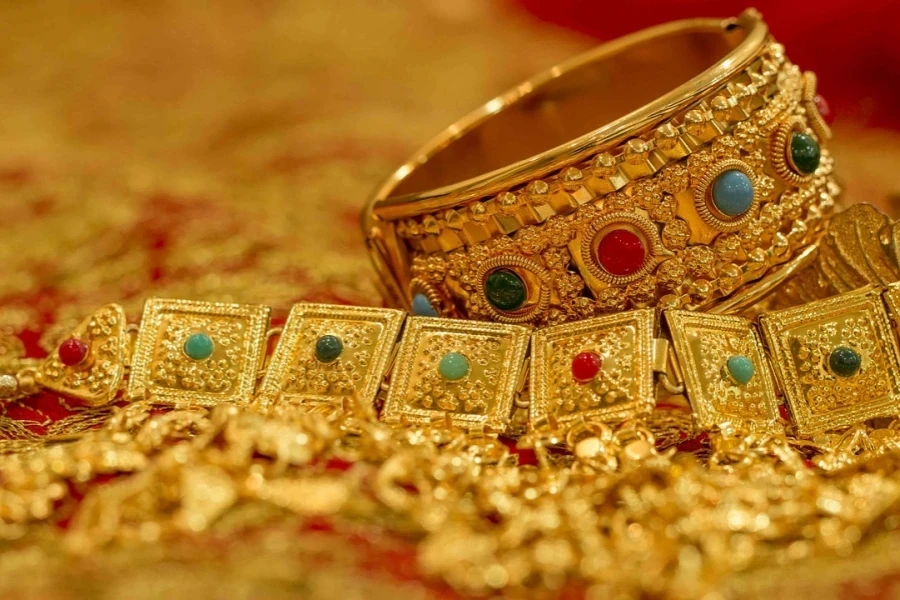
Once a buyer understands the advantages and limitations, types, and key features of miniature welders, it’s time to choose the right one to create a suitable weld in the tasks at hand.
Consider your welding application
The first consideration is its application. Consider the type of material to be welded and the space available for the welding process. This will determine the size, shape, and type of welder needed. For example, a laser welder is ideal for medical devices, while ultrasonic welders are ideal for plastic components.
Evaluate specs and features
It may be that there are some key specifications and features needed for the task at hand. Consider the safety features, ease of use for the controls, the power output needed, the portability, and the level of precision attainable by the welder.
Budget considerations
When buying a miniature welder, cost will usually be a factor. Miniature welders come in a range of price points depending on the brand and features. Try to ensure there is a good balance between the price point and features.
Brand and support
As with most items, and especially tools, buying from reputable brands is advised due to the fact that these are tried and tested, and usually offer good after-sales care, long warranty periods, and customer support. However, if researching properly it is possible to find good deals on lesser-known brands with similar conditions.
Future trends in miniature welding
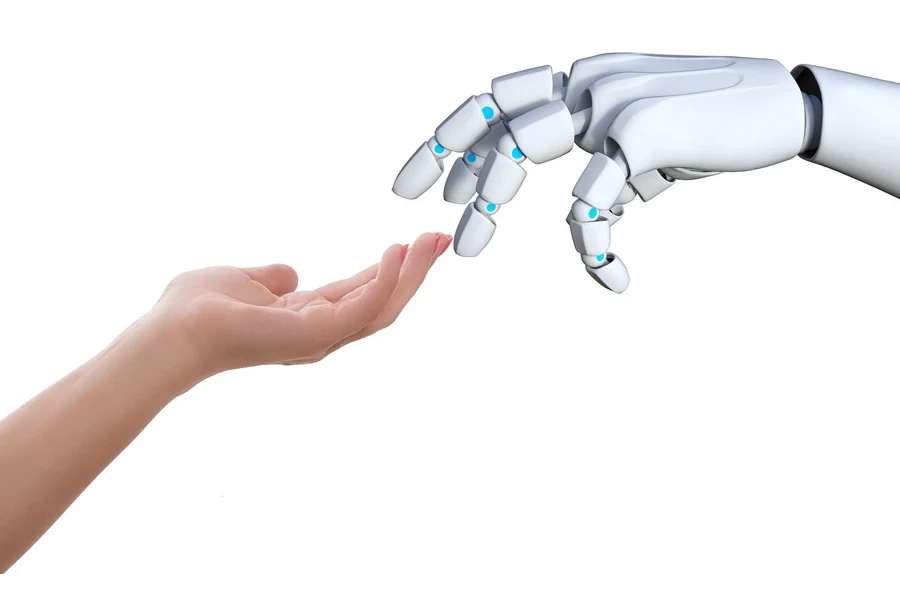
3D printing and a rise in demand
The rise of additive manufacturing, like 3D-printing, has meant increased demand for miniature welding to make post-manufacturing adjustments and finishes. This growth is present in both business and home use as individuals choose it as their weapon of choice to create great value, industry-standard welds with a nice easy setup. Moreover, thanks to these changes in manufacturing, there has been increased market competition and innovation, which has driven advancements in technology innovation.
Robotics and new welder technology
New and improved welder types and advanced automation solutions are driving precision and speed in welding, while new material types are opening the way for new welding opportunities. In addition, integration with robotics is opening a path to fully-automated line production welding. This means reduced downtime, reduced human error, and increased speed and efficiency — imagine a line of robots with miniature welders attached to their arms, performing repetitive welding tasks.
Conclusion
Miniature welding is a growing industry thanks to the changing manufacturing landscape and the fact that miniature welders are able to produce high-quality results with high precision in a limited space. Their portability, compactness, and welding accuracy mean miniature welders are ideal for many different applications, including small repair jobs, working with jewelry, electronics, automobiles, medical equipment and aerospace equipment, or even dental work. These are all growing and evolving industries and even as AI, robotics, and smart technology become increasingly ingrained, miniature welders will continue to play a key role within them.