To obtain the perfect product, there are a lot of machining processes and operations that are undertaken in the manufacturing process. These processes and operations help to remove any excess materials. There are many of these machining processes and operations.
Read to find out the most common machining processes and operations.
Table of Contents
What is machining?
The most popular machining processes and operations
Conclusion
What is machining?
Machining is a process where materials (usually metal) are cut into the required or desired sizes and shapes by a controlled process for material removal. There are three principal machining processes which include drilling, turning, and milling.
The most popular machining processes and operations
1. Turning
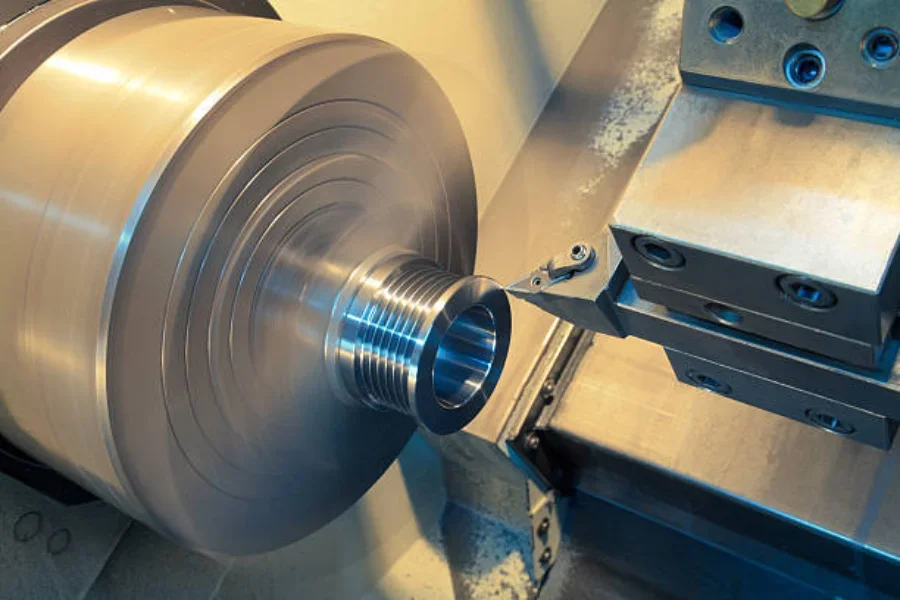
Turning is the machining operation applied to producing round objects. This process uses machines like the lathe with a general size of about 15-inches swing and 36 to 48 inches between the centers. The lathe has three main operations which include driving, clamping, and linear motion. The linear movement happens in two directions. A workpiece is positioned in the center and has the cutting tool moving back and forth around it. Turning is mostly used in concentric cutting tasks.
The process begins with the clamping of the object at the center while being driven radially. This object provides the required power for the machining process. Additionally, the cutting tool’s dimensions vary based on the application. Both the inside and the outside have a chisel to be used during the machining process. The center moves linearly to create holes at the center of the axis beginning with drilling and then clearing. Lathe functionality can be automated fully. Generally, turning machinery has a precision level of about IT8-IT7 and a working speed of 35 m/min.
2. Milling
Milling is a machining process that cuts radially moving workpieces in contact with a piece of cylindrical cutting equipment that has sharp cutting teeth on its circumference. The cutting tool rotates in a linear movement to contact the product’s surface. Through this movement, the milling process is initiated and the unwanted material is cut away from the surface of the workpiece.
Various materials have detailed geometrical shapes that can be milled easily when using a milling machine. Nowadays, the milling process has been integrated with computer software; thus making it an automated process. Most manufacturers can now operate and control the milling machines with computer numerical controls (CNC).
Furthermore, milling equipment has been developed with some having a 5-axis operational competence. This means the machine can move freely in five axes without re-tensioning during machining activities. Most milling operations have a cutting depth of 1-4 mm while end milling depths range from 1 to 2 mm. They have a precision level of about IT8-IT7 with an average working speed of 16.5 m/min.
3. Boring
In machining, boring is used in refining the accuracy and dimensions of a drilled hole. The machines used for boring have several variations based on the size of the task. Vertical boring mills can machine heavy and large castings with the work turning while the boring bar remains stationary. On the other hand, jig borers and horizontal boring mills hold the work stationary and rotate the cutting tool. Using a single point in machining, the boring cutter acts on the side of a hole compared to a drill bit. For instance, cored holes in castings are finished by the boring process. This machining process requires a general diameter size of 75 to 150 mm, a precision level of about IT7-IT6, and the working speed may range from 60 to 120 m/min.
4. Tapping
Tapping is a machining operation involving a thread application inside a drilled hole. In this case, the cutting tool used in tapping is referred to as a tap. A tap is a cross-shaped tool positioned inside an imaginary cylindrical structure. The endpoint of the cross has cutting grooves on the circumference that assume the shape of a wire. These cutting grooves go deeper as the stud’s depth increases; thus if it rotates once it does not cut the whole thread.
Sometimes, tapping becomes difficult because of material hardness. In such situations, the tapping process can be done repeatedly. Multiple tapping processes can be executed with the increasing depth of the groove after each tapping. The machines are designed to produce a general diameter of about 0-25 mm and the required speed for tapping falls between 150 and 250 rpm. This machining operation has an estimated precision level of IT8-IT7.
5. Drilling
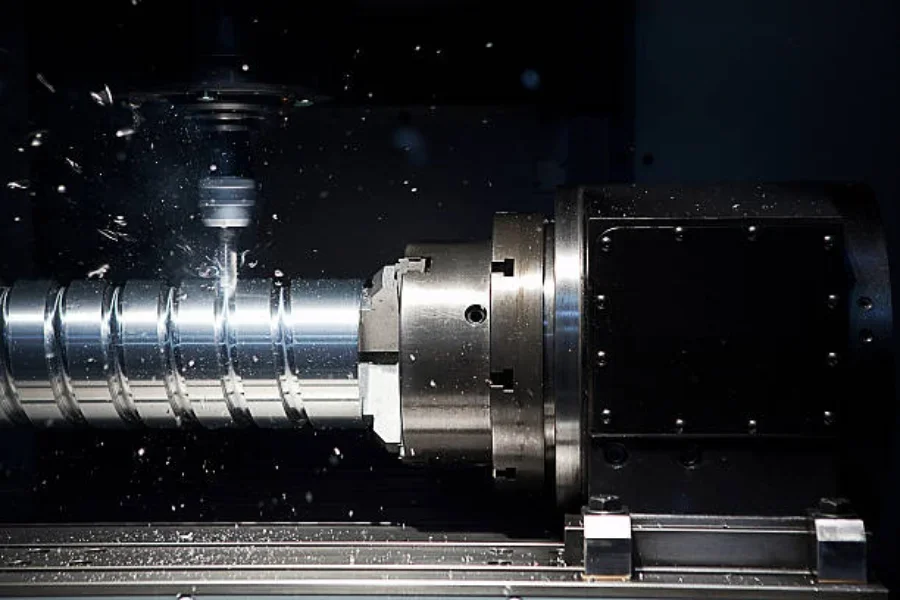
Drilling involves a cutting tool that has two cutting edges moving radially around an axis and linearly in a one-way direction. Through this machining process, round holes are created on a workpiece. As the machine drills, the chips being removed from the material move upwards. There is a sub-type drilling process that creates holes that are 35 times larger in diameter. The process is called deep-hole drill or long-hole drill. Generally, the machining precision reaches IT10. A 12 mm drill produces a 0-125 mm hole size, and a 22 mm drill gives 0-5 mm oversize with a drilling speed of 5 to 6 m/min for high-temperature alloys and 110 m/min for magnesium and aluminum alloys.
6. Grinding
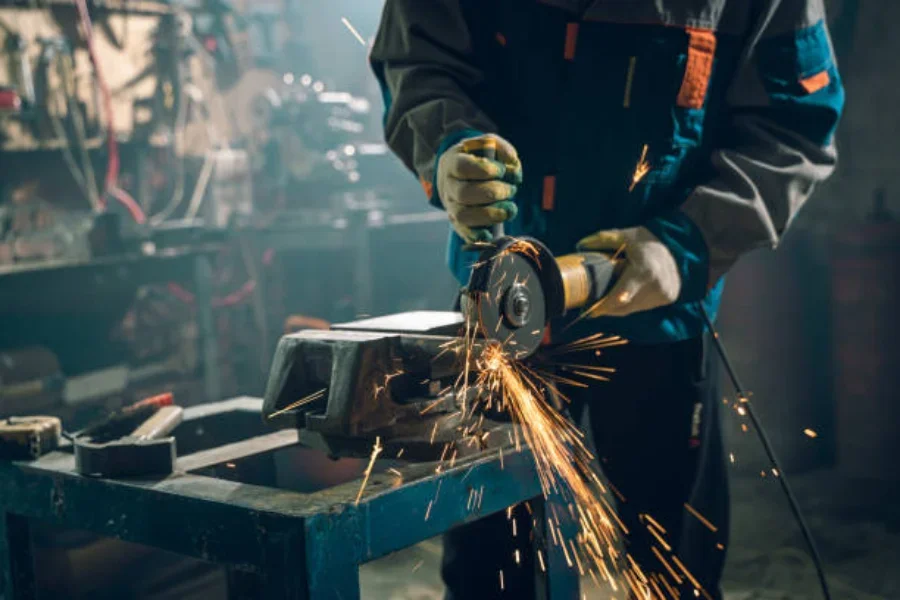
Grinding is the process of removing material from a surface to obtain a clean and smooth finish. Considering metallic grinding, the unwanted material is gotten rid of from the surface as chips. Afterward, the roughness of the surface is reduced, and the surface can reflect light vertically and more uniformly making it appear shinier. Among most machining operations, grinding achieves a higher level of accuracy.
Usually, there is the utilization of a fine-grained grindstone during this process. The grains have sufficient hardness and brittle specs of abrasives that act like cutting tools. Eventually, the grains break down into needle-like sharp abrasive grains that carry out the grinding process. The grindstones are hard and cannot be made blunt easily; therefore they are not substituted easily. Being a finishing operation, a 5 mm grinding wheel has precision dimensions in the order of 0.000025mm. The wheel speed should be maintained in a range of 5,000 to 6500 ft/min.
7. Planning
Planning is a process of material extraction that reciprocates a workpiece against a stationary cutting tool that creates a sculpted layer or a plane. This process is similar to shaping only that they have opposite movements of the workpiece. During the planning process, the cutting tool repetitively moves linearly while the workpiece is fed into the cutting tool’s movement line. This results in a smooth, flat, and sculpted surface. After every stroke, the tools are elevated manually or hydraulically to avoid chipping of the cutting tool as it travels back across the workpiece surface. The planning process can create flat surfaces on the workpiece length and cross-sections with notches and grooves. The machining precision for planners ranges from IT9-IT7 at a speed of 9000 rpm to produce a general cut diameter varying from 56 to 160 mm.
8. Broaching
Broaching utilizes a broached tooth tool to get rid of material in either linear or rotary movements. The linear broaching process is the common one where the broach runs linearly against a workpiece to create a cut. On the other hand, rotary broaching cuts an axisymmetric shape by rotating the broach and forcing it into the workpiece. A rotary broach can be used in a screw machine or a lathe. Broaching creates a general diameter of 10-100 mm; thus it is required for odd shapes like circular and non-circular shapes, keyways, splines, and flat surfaces. The general precision level of broaching is IT7-IT8 with a generally low speed of 18 m/min.
9. Honing
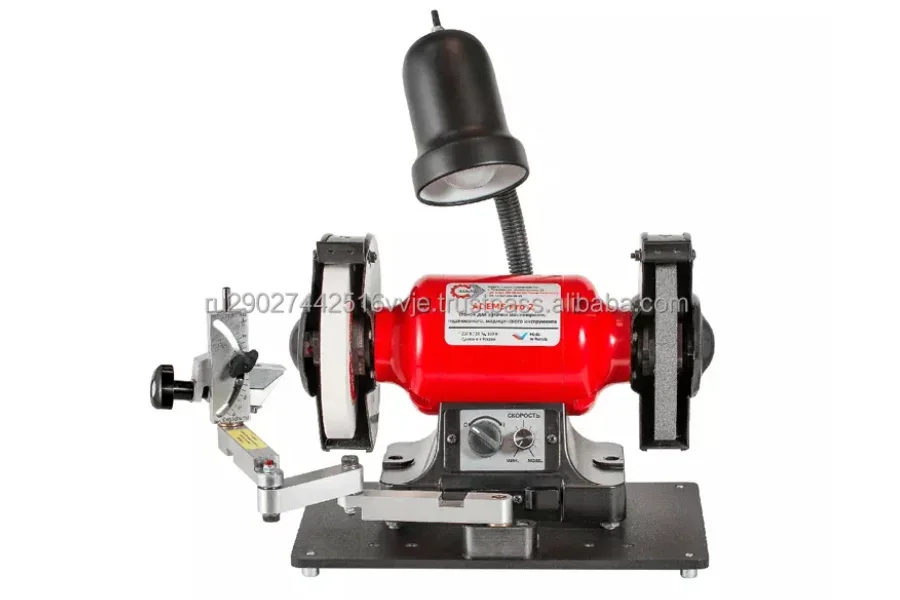
Honing as a machining process utilizes three grinder stones inside a hole being pressed outwards. It is a generally low-speed grinding process ranging between 45 and 90 m/min. The honing precision level falls between 0.8 to 2.0 micrometers while creating a range of diameter that is 1.55-1,880 mm and lengths of up to 27,000 mm. The grinding wheels are driven radially in combination while moving on a vertical axis. In this case, grooving occurs on the cylindrical surface. For instance, engine cylinders are smoothened by the process of honing.
10. Lapping
Lapping is a post-machining process. It involves round objects being put between two rotating cast-iron groovy discs. One of the discs is stationary while the other rotates with a spherical object inside. The addition of pasta increases the pressure to grind the spherical objects. The lapping process ensures that the required roughness and accuracy of the shape are achieved. As a result, multiple cutting tool types are used to achieve the mentioned parameters.
Some of the items produced through the lapping process are winches and bearing bushes. The general operation size ranges from 300 mm to 2000 mm in diameter. On average, a rotary speed of 70 rpm generates a speed of 165 m/min and a precision level of 0.0000254 mm for flatness and 0.000254 mm for parallelism.
Conclusion
Machining operations are quite complex. This is because the processes involve many machines, features, and various functions to produce the desired products. All these should be well coordinated to execute the intended task. Some of the factors buyers should consider are the tool geometry and design, the selection of the material, and the rate of feed. To find quality equipment for various machining processes, visit Alibaba.com.