Imagine you own a store that sells products online. You want to ensure it always has enough items for your customers, but you also don’t want excess products taking up space, expiring or spoiling. How do you decide how many items to order and when to order them? That’s where the reorder point (ROP) and safety stock come in. Read on to learn how to calculate your ROP and safety stock for your store.
Table of Contents
What is a reorder point?
How to calculate a reorder point?
Benefits of accurate reorder points and safety stock
Key takeaways: Reorder point and safety stock calculations
What is a reorder point?
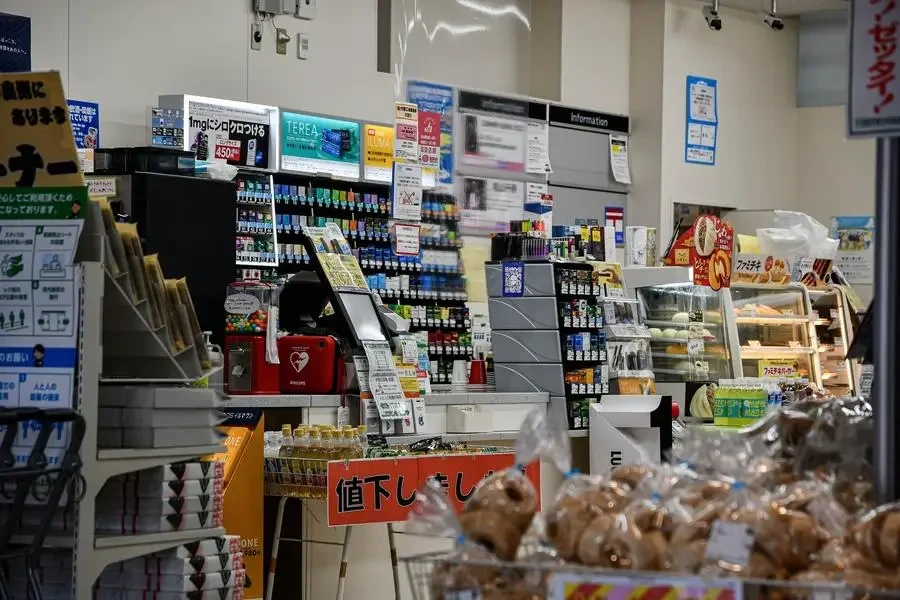
The reorder point is like a signal for when you need to restock your inventory. Think of it as a fuel gauge in a car: when it hits a certain point, you know it’s time to refill. It’s calculated based on three things: lead time, daily average usage, and safety stock.
1. Lead time
Lead time is the period taken by the supplier to fulfill an order. You determine this by calculating how long it takes for your orders to get to you after you place them. For instance, if it typically takes Supplier Y 10 days from when you order until they deliver 100 units of Product X, that’s a lead time of 10 days.
2. Daily average usage
Daily average usage is the quantity of a specific item sold on an average day. To calculate it, add up all units sold over time, then divide by the number of days. For instance, if you sold 300 phone cases within thirty days, then your daily average usage turns out to be ten units per day.
3. Safety stock
Safety Stock is the extra inventory kept on hand to avoid stockouts. It is some extra product that you keep in case of emergencies, like a sudden increase in demand or a delay in delivery. There are several methods used to calculate safety stock. The most common formula for calculating it is:
Safety stock = (maximum daily sales × maximum lead time) − (average daily sales × average lead time).
For example, if your maximum daily sales are 20 units, your maximum lead time is 7 days, your average daily sales are 10 units, and your average lead time is 6 days, your safety stock would be (20×7) − (10 × 6) = 80 units.
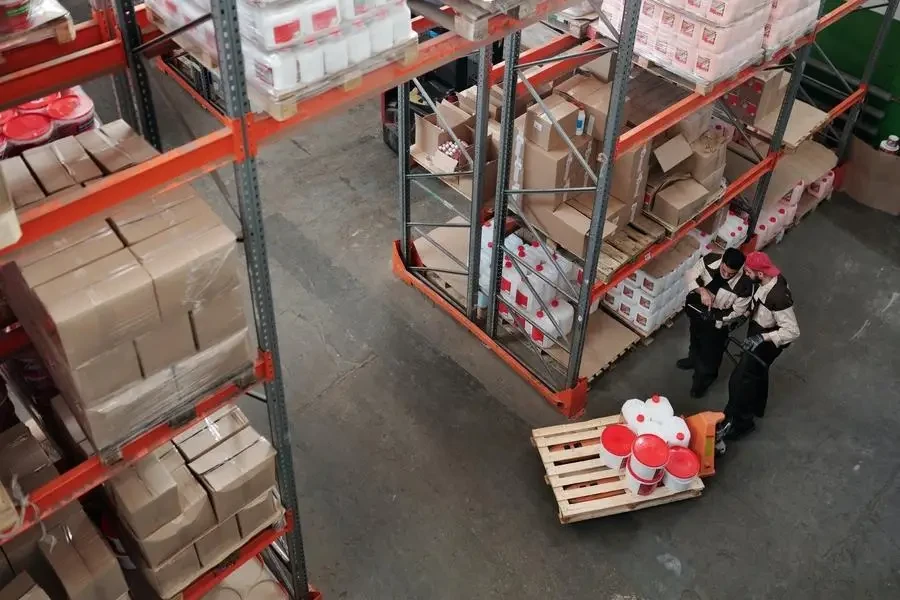
How to calculate a reorder point?
The reorder point can be calculated using the formula:
Reorder Point = (Lead Time x Daily Average Usage) + Safety Stock
Now, let’s consider a real-world example:
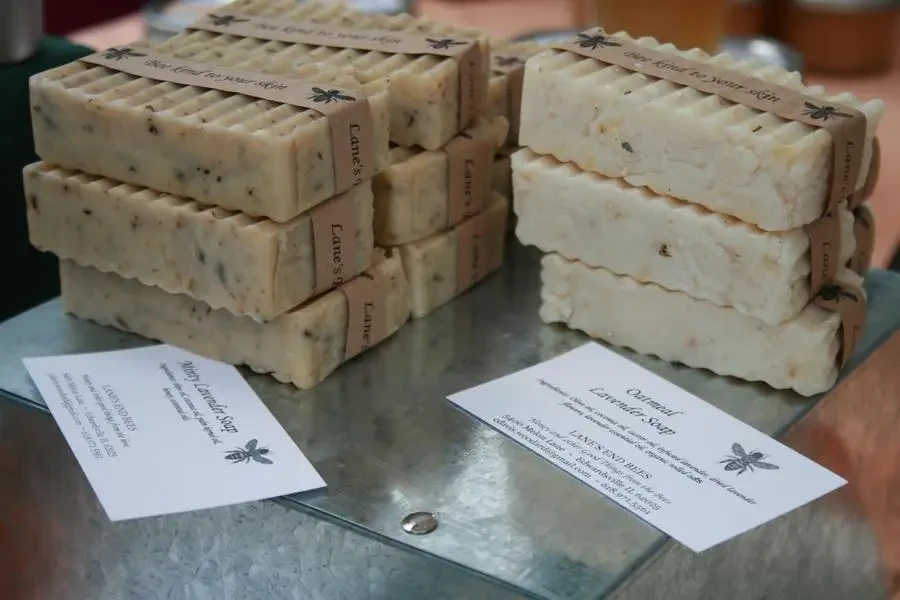
Suppose you run a small business selling handmade soaps. Your average sales volume is 50 bars of soap per day. The lead time for procuring more soap from your supplier is 7 days. To buffer against fluctuations in demand and lead time, you maintain a safety stock of 100 bars of soap.
Using the formula, the reorder point would be:
Reorder Point = (Lead Time x Daily Average Usage) + Safety Stock
Reorder Point = (7 x 50) + 100 = 450
So, when your inventory level drops to 450 bars of soap, that’s when you should place a new order. This ensures that you have enough stock to meet customer demand while waiting for the new order to arrive.
Benefits of accurate reorder points and safety stock
Avoid stock outs
Running out of stock means you can’t meet customer demands. This can harm your image and lose customers’ trust. Although running out of stock is unavoidable, it doesn’t have to affect your business operations. By setting a reorder point and a safety stock, you can avoid stock-outs, ensuring customer satisfaction even if supply fluctuates or is delayed.
Reduce holding costs

Holding costs are the expenses associated with storing and maintaining inventory, such as rent, utilities, insurance, taxes, depreciation, and obsolescence. They can consume a significant portion of your profits if you keep too much inventory. All these additional expenses can be avoided. By setting a reorder point and a safety stock, you can minimize the amount of inventory you need to hold, thus reducing your holding costs.
Improve cash flow
Cash flow, the vital pulse of your business, measures the money that flows in and out of your operations. With enough cash flow, your company could avoid bankruptcy or stagnation. One way to improve your cash flow is to optimize your inventory management.
By setting a reorder point and a safety stock, you can avoid having too much inventory that does not generate income. Instead, you can use your cash for other purposes, such as expanding your business, promoting your brand, or hiring more staff.
Increase turnover rate
Turnover rate is how often you sell and replace your inventory within a certain time. A high turnover rate means you are selling more products with less inventory, which indicates higher profitability and a lower risk of obsolescence. Setting a reorder point and a safety stock can increase your turnover rate by avoiding overstocking and understocking.
Enhance customer satisfaction
Customer satisfaction is how happy your customers are with your products and services. It is vital for keeping and attracting clients and boosting your sales and profits. Setting a reorder point and a safety stock can improve customer satisfaction by delivering your products on time, avoiding backorders or cancellations, and meeting their expectations.
Key takeaways: Reorder point and safety stock calculations
You learned two important concepts in this article: reorder point and safety stock. Reorder point tells you when to order more products from your suppliers. Safety stock tells you how much extra inventory to keep in case of emergencies.
You can use the easy formulas and examples we gave you to calculate these numbers for your products. This way, you can avoid running out of stock or having too much stock. This will make your business more profitable and your customers happier.