Inventory is the backbone of any organization. It is the lifeblood that keeps the company running, and it needs to be managed with care and precision. Maintaining an adequate level of inventory can make or break the success of any business.
Unfortunately, 46% of small and medium-sized businesses (SMBs) either don’t track inventory or use a manual method. This can lead to a variety of issues, like the inability to fulfill orders on time, loss of sales due to out-of-stock items, and wasted cash flow from excess inventory.
By reducing stock-outs and overstocks through effective inventory management, businesses can lower inventory costs by as much as 10%. But how exactly do businesses achieve this level of efficiency in managing their inventory? And which inventory management technique is the perfect one?
Keep reading to learn the role of inventory management in the supply chain, and how to create an effective inventory management system using tried-and-proven strategies!
Table of Contents
What is inventory management in the supply chain?
What are the types of inventory in supply chain management?
6 methods for effective inventory management
How to develop an effective inventory management system?
Leverage Alibaba Cloud to automate inventory management
What is inventory management in the supply chain?
Inventory management is a core facet of supply chain management that deals with maintaining the right balance of stock in a business. At its heart, it’s a systematic process of planning and controlling the ordering, production, and storage of items needed to run a business, from raw materials to finished goods.
Inventory management allows businesses to ensure all parts and components are available in the right amount at the right time, preventing overstocking or understocking scenarios. By reducing excess stock, businesses eliminate unnecessary costs and free up resources otherwise tied up in storerooms.
Strategic inventory and logistics planning enable businesses to anticipate high-demand periods, minimizing the need to overproduce or rush orders through production processes. Moreover, avoiding shortages by carefully monitoring inventory levels means there’s no need to scramble to find products at the last minute, leading to a smooth flow of goods.
What are the types of inventory in supply chain management?
In supply chain management, understanding the different types of inventory is essential for effective planning and decision-making. There are four primary categories of inventory that are critical to manufacturing businesses: raw materials, work-in-process, finished goods, and MRO items (maintenance, repair, and operations).
Raw materials
Raw materials are the first components in the production process, sourced from suppliers and used as inputs to create finished products. These materials are not sold directly to customers. For example, a pastry shop might purchase flour, sugar, and eggs as raw materials required in baking their goodies.
Work-in-process
Work-in-process inventory represents parts that have been produced but not yet completed. These items may be waiting for packaging, labeling, or additional processing before they’re ready to be sold. An example would be products on an assembly line, such as partially assembled bicycles or smartphones awaiting the installation of screens.
Finished goods
Finished goods encompass the final products ready for sale. They may be sold directly to customers, or they might be shipped to another party for further processing before being sold. A clothing store, for instance, would have finished goods like shirts, pants, and jackets neatly displayed on racks for customers to purchase.
MRO items
MRO items include parts, tools, and equipment necessary for the operation, maintenance, and repair of machinery and processes. They can range from small parts like screws and bolts to consumables like printer ink and miscellaneous office supplies, like pens and paper clips. For example, a printing company would require ink cartridges, paper, and various replacement parts for their machines to ensure smooth operation.
6 methods for effective inventory management
Inventory management can be a real pain in the neck—it’s time-consuming, tedious, and confusing for even the most seasoned managers. But with the right techniques and strategies, it’s actually a lot simpler than you might think. Here are six common inventory management techniques that can help businesses keep track of their inventory:
First-In, First-Out (FIFO)
The First-In, First-Out (FIFO) inventory management method operates on the principle that items received first should be sold/utilized first, ensuring a systematic and efficient rotation of stock. This approach not only helps maintain product quality but also contributes to reducing storage and spoilage costs. Moreover, the FIFO method provides accurate stock records, which in turn simplifies inventory tracking and evaluation processes.
A practical example of the FIFO method in action is evident in coffee shops that sell fresh pastries. By placing pastries baked earlier in the day at the front of the display case, the coffee shop encourages customers to purchase them first. As a result, the shop maximizes freshness, reduces waste due to stale or expired baked goods, and efficiently manages its inventory to maintain the quality and appeal of its offerings.
Last-In, First-Out (LIFO)
The Last-In, First-Out (LIFO) method works in reverse to the FIFO concept, stipulating that the most recently received items should be sold first. This approach helps businesses reduce costs related to rotation, storage, and handling of inventory, particularly for non-perishable and identical-looking goods. LIFO is particularly advantageous when dealing with items that have high storage costs or are bulky, making them difficult to move frequently.
Using the LIFO method provides businesses with a way to counteract inflation in the cost of goods, as it assumes the latest, and possibly more expensive units, are sold first. A practical example of this can be seen in a lumber yard. Since new shipments of wood are typically stacked on top of older ones, workers grab the topmost pieces first for customers, thereby following the LIFO method.
Just-In-Time (JIT)
The Just-In-Time (JIT) inventory management method, first introduced by Toyota Motor Corporation, emphasizes keeping minimal stock levels and ordering items precisely when they are needed. This approach relies on accurate demand forecasting and well-coordinated supply chain partnerships, allowing businesses to reduce storage, carrying, and obsolescence costs associated with overstocking.
A prime example of JIT implementation can be seen in automotive manufacturing companies. For instance, an assembly line could receive essential components like engines, transmissions, or braking systems right before they are installed on the vehicles. This approach reduces the need for extensive on-site storage, minimizes carrying costs, and ensures a smoother, more responsive supply chain.
ABC Analysis
ABC analysis is an inventory management technique that classifies inventory items into three categories based on their value and importance: A-items are high-value, B-items are of moderate value, and C-items are low in value.
This categorization method follows the Pareto principle, or 80/20 rule, suggesting that 20% of items may account for approximately 80% of the inventory value. The goal is to help businesses focus more resources on the most valuable items (A-items) while reducing unnecessary expenditure on low-value goods (C-items).
To illustrate this method, consider a bookstore that carries a wide range of products. High-value items, such as limited-edition books and costly study materials, could be categorized as ‘A‘ items and given priority for placement and restocking.
Meanwhile, moderately priced bestselling novels could be ‘B‘ items and lower value items like stationery and bookmarks fall into category ‘C‘. With this approach, the bookstore can better manage its inventory, optimize its shelf space, and enhance profitability.
Materials Requirement Planning (MRP)
Materials Requirement Planning (MRP) is an inventory management method that uses a bill of materials (BOM) to determine the exact quantities of each component needed based on sales forecasts and estimated production timelines.
The BOM lists all necessary components for a finished product, allowing MRP systems to break down the product, identify required raw materials, and distribute them accordingly. MRP manages these materials, tracking them from receipt to delivery and throughout their life cycle.
Implementing MRP allows for better coordination of production, purchasing, and delivery schedules, resulting in minimized stock levels and carrying costs. It also provides a structured approach to planning, minimizing stockouts, and reducing lead times.
To exemplify, consider an electronics manufacturer producing smartphones. The MRP system would account for the multitude of components needed, such as microchips, processors, and casings. Based on sales forecasts and production goals, the system determines the required quantities and timing for each item and informs relevant departments to procure or manufacture components accordingly.
Economic Order Quantity (EOQ)
Economic Order Quantity (EOQ) is an inventory management technique that determines the optimal quantity of items to order from suppliers to minimize the total costs associated with ordering and carrying inventory. This method assumes a steady demand for products but, in the unpredictable and fluctuating real world, can adjust accordingly.
The EOQ model strives to balance the costs of ordering too frequently (which increases ordering costs) and ordering too much (increasing carrying costs), aiming for the most cost-effective balance between the two.
For instance, imagine a retail store ordering a line of T-shirts from a supplier. Using the EOQ model, the store could calculate the optimal order quantity that minimizes cumulative costs related to ordering, delivery, and storage. Say, for example, they determine that their EOQ is 500 units. This means that whenever they need to restock this particular line of T-shirts, they should ideally order 500 units at a time to achieve the lowest total cost.
How to develop an effective inventory management system?
A good inventory management system can be the difference between a thriving business and one that is plagued by stockouts, overstocks, and excess inventory. To make things easier, here is a 4-step process that will help businesses create an effective inventory management system for their warehouse operations:
Evaluate your inventory state
The first step in developing an effective inventory management system requires a thorough understanding of the inventory’s current state. This evaluation is not a simple tally of items, but rather an in-depth analysis that considers the types of inventory, quantities of each item, sales data, storage conditions, and the efficiency of shipping and receiving processes.
Here’s a simple breakdown of how to evaluate the inventory state:
Cataloging inventory
First and foremost, identify and list every type of inventory in the business. This could range from:
- Raw materials
- Work-in-process items
- Finished products
- MRO supplies
Determine inventory levels
Next, calculate the precise amount of each type of inventory. By doing so, businesses will be putting down actual figures against each inventory category.
Analyze sales and demand
Now it’s time to analyze sales data and projected future demand. This bit of detective work will help businesses predict which products are likely to be in high demand and which may stagnate.
Evaluate shipping and receiving processes
Finally, evaluate the shipping and receiving processes. Are there areas where delays often happen? Do you notice any inefficiencies that could be ironed out?
Select an inventory management method
After comprehensively evaluating the inventory state, the next step is to determine the appropriate inventory management method to implement. The table below illustrates the ideal business scenarios for various inventory management techniques:
Inventory management method | Business use-case |
FIFO (First-In, First-Out) | Suitable for businesses dealing with perishable goods |
LIFO (Last-In, First-Out) | Suitable for goods that don’t get obsolete over time |
JIT (Just-In-Time) | Optimal when demand is predictable and businesses want to save on holding costs |
ABC Analysis | Ideal for businesses with a range of items varying in value |
MRP (Material Requirements Planning) | Best for businesses with complex production management |
EOQ (Economic Order Quantity) | Works best for businesses wanting to find a balance between order cost and holding cost |
Another way to determine the best strategy for inventory management is through logistics KPIs. The table below matches various key performance indicators and the corresponding types of inventory methods for easier comparison:
Inventory KPI | Explanation | Inventory management method |
Inventory turnover | A high turnover means frequent sales and effective inventory operations | FIFO (First-In, First-Out), LIFO (Last-In, First-Out) |
Warehouse utilization | A high utilization means efficient space usage | JIT (Just-In-Time), ABC analysis |
Order cycle time | Short cycle time means quick order fulfillment | MRP (Material Requirements Planning), EOQ (Economic Order Quantity) |
Implement a warehouse management software (WMS)
After having thoroughly assessed the inventory state and having determined the most fitting inventory management method, it’s now time to introduce a technology that will seamlessly connect and streamline all aspects of inventory tracking.
Warehouse management software (WMS) is a software application designed to optimize warehouse functionality and distribution center management. It helps businesses in controlling and managing warehouse operations from the time goods or materials enter a warehouse until they move out.
Review and refine on a regular basis
Inventory management is not a set-and-forget formula; it’s a constant process. Regular inventory analysis involves a series of pertinent questions that help assess the efficiency and effectiveness of the current inventory management system. Here are some questions to consider:
- Are you meeting your inventory turnover goals?
- How often do you encounter out-of-stock situations?
- Are warehouse spaces optimized?
- How much are you spending on storage costs?
- Are any items in stock obsolete or spoiling?
Remember, the goal here is not to achieve perfection in one sweep but engage in continuous, incremental improvement.
Leverage Alibaba Cloud to automate inventory management
The need for real-time inventory tracking, location accuracy, and automatic replenishment is more crucial than ever, particularly for businesses with multi-location warehouses. With Alibaba Cloud solutions, it’s now possible to redefine the way inventory management is handled.
For instance, the Elastic Compute Service (ECS) allows businesses to smoothly adapt their warehouse management systems to growing needs, backed by high-performance computing capabilities and the latest Intel CPUs.
In addition, Alibaba Cloud’s fully managed Relational Database Services (RDS) not only assist businesses in building heavily organized inventory databases but also ensure that they’re easily accessible.
And for businesses looking at predictive measures, Alibaba Cloud’s serverless and high-performance Data Lake Analytics (DLA) service provides a data-processing powerhouse. DLA can be used for sales and demand forecasting, predicting inventory inflows and outflows, and optimizing inventory levels by processing vast amounts of structured, semi-structured, and unstructured data.
Last but not least, Alibaba Cloud’s Blockchain as a Service (BaaS) ensures end-to-end transparency in tracking inventory items from their origin to their destination. By employing BaaS, businesses gain confidence that no duplicate orders are being made before items reach warehouse shelves.
As we have seen, the challenges of inventory management are many, but the solutions lie in smart automation systems and optimized warehousing. From better tracking of the inventory to refined shipment handling, here is all you need to know about warehouse management systems!
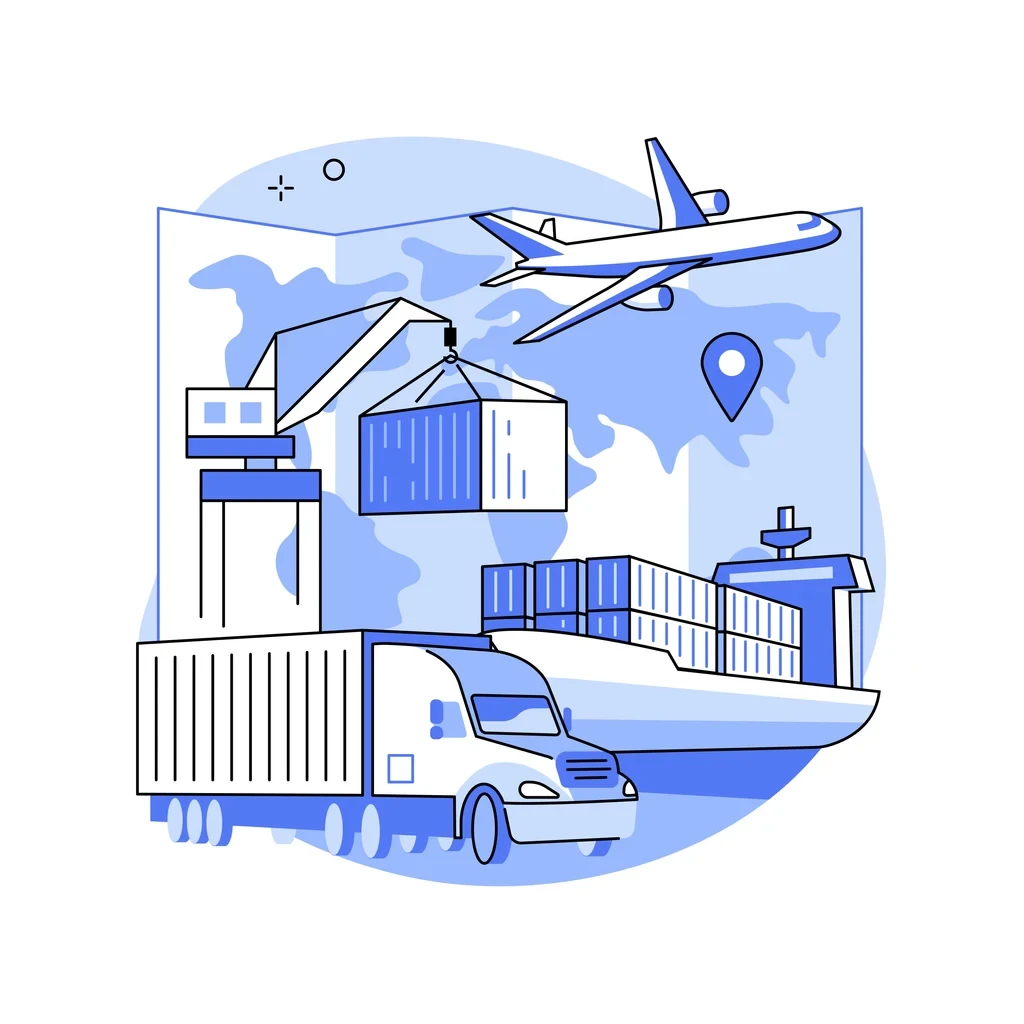
Looking for a logistics solution with competitive pricing, full visibility, and readily accessible customer support? Check out the Alibaba.com Logistics Marketplace today.