It is well known that the pure resin properties of some polymers are not very excellent, and they mostly cannot be used directly. They need to be modified to meet the requirements of the products. When we talk about modified plastics, what exactly has been modified? What properties can be changed, such as density, transparency, hardness, processability, strength, and toughness? In this article, we will delve into the eight major directions of plastic modification and the revolutionary impact of modified plastics in home appliances.
Table of Contents:
What is the modification of plastics?
Eight major directions of plastic modification
Endless potential of modified plastics in home appliances
Six major trends in modified plastics for home appliances
What is the modification of plastics?
Simply put, the modification of plastics is to change the original properties of plastics through physical, chemical, and other methods, to increase or improve their original properties, making them more suitable for end products.
Eight major directions of plastic modification
When it comes to modification, what properties of materials are generally modified in modified plastics? In summary, there are roughly eight types:
Density
Changing the density of plastics can be divided into two types: one is to reduce the density of plastics, and the other is to increase the density of plastics, depending on the choice of the end application. Here, we mainly introduce the methods to reduce the density of plastics.
Reducing plastic density: According to the high school formula M=ρV, this means that when the density of the material is reduced, the mass will also decrease under the premise that the original volume of the product remains unchanged. This is commonly used in the lightweighting of end applications such as automobiles. Common methods to reduce the density of plastics include adding lightweight fillers or resins, but the reduction in density is relatively small; another method is foaming technology, which has a larger range of weight reduction but is slightly more difficult.
Transparency
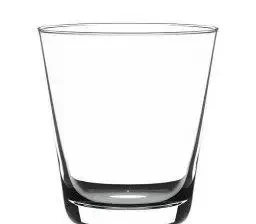
Regarding the transparency of plastics, it is generally about utilizing the relationship between crystallinity and transparency. The transparency of plastics is related to the crystallinity of the products. By controlling the different structural forms of the products, their transparency can be improved.
To measure the transparency of a material, many performance indicators need to be considered. Commonly used indicators include: light transmittance, haze, refractive index, birefringence, and dispersion. A good transparent material requires these performance indicators to be excellent and balanced.
Common methods to change the crystalline form include:
- Controlling the quality of crystallization, such as the control of crystalline form, spherulite content, crystal size, and crystal regularity.
- Increasing the refractive index, mainly by adding high refractive index organic or inorganic substances that do not affect transparency.
- Reducing birefringence, which can be achieved by controlling the orientation during processing, i.e., reducing the degree of orientation to lower birefringence.
- Adding substances to improve the transparency of plastics, which refers to the method of adding small molecular substances to transparent resins to improve their transparency. This method can increase light transmittance and refractive index and reduce birefringence.
- Adding nucleating agents, which is the most effective method to increase the light transmittance of transparent resins. Nucleating agents are small molecular substances that can promote crystallization. They act as nucleation sites in the resin, changing homogeneous nucleation to heterogeneous nucleation, increasing the number of nuclei in the crystalline system, increasing the number of microcrystals, reducing the number of spherulites, thereby refining the crystal size and improving the transparency of the resin.
- Adding high refractive index inorganic substances
- Adding substances that can reduce birefringence
- Adding anti-fogging agents
Hardness and flexibility
Hardness
Changing the hardness of plastics involves modifying both surface hardness and overall hardness, generally by adding hard additives to the plastic, usually rigid inorganic fillers.
Surface hardness: This improves only the surface hardness of the plastic products, while the internal hardness remains unchanged. It’s a lower-cost method mainly used for decorative materials and daily necessities. The main methods include coating, plating, and surface treatment.
Overall hardness: This is usually achieved by blending plastics, i.e., mixing low-hardness resin with high-hardness resin to enhance the overall hardness.
Commonly used blending resins include: PS, PMMA, ABS, and MF. The resins that mainly need modification include PE types, PA, PTFE, and PP.
Flexibility
Flexibility is generally altered by adding plasticizers. The main function of plasticizers is to improve the processability of the resin, i.e., lowering the processing temperature and improving processing fluidity. However, their addition to the relevant resins can also impart flexibility to the products. Resins suitable for flexibility improvement with plasticizers include: PVC, PVDC, CPE, SBS, PA, ABS, PVA, and chlorinated polyether.
Processability
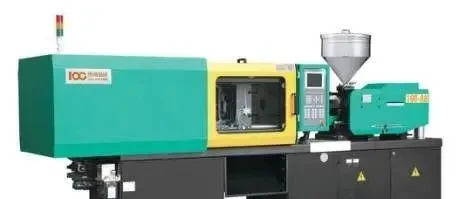
Improving the processability of plastics generally involves: increasing the thermal decomposition temperature of the resin; lowering the melting temperature of the resin; improving the process flowability of the resin; and enhancing the melt characteristics of the resin.
Common modification methods include the addition of modifying agents, plasticizers, and lubricants. Plasticizers can increase the plasticity of polymers. The role of lubricants is to reduce the friction between materials and between the material and the surface of processing equipment. This helps to decrease the flow resistance of the melt, lower the melt viscosity, improve the fluidity of the melt, prevent the melt from adhering to the equipment, and enhance the surface smoothness of the products.
Endless potential of modified plastics in home appliances
With the development of plastic modification technology and the improvement of people’s living standards, the application of modified plastics in the home appliance industry has become increasingly widespread. Modified plastics are used in kitchen utensils, personal care products, and more.
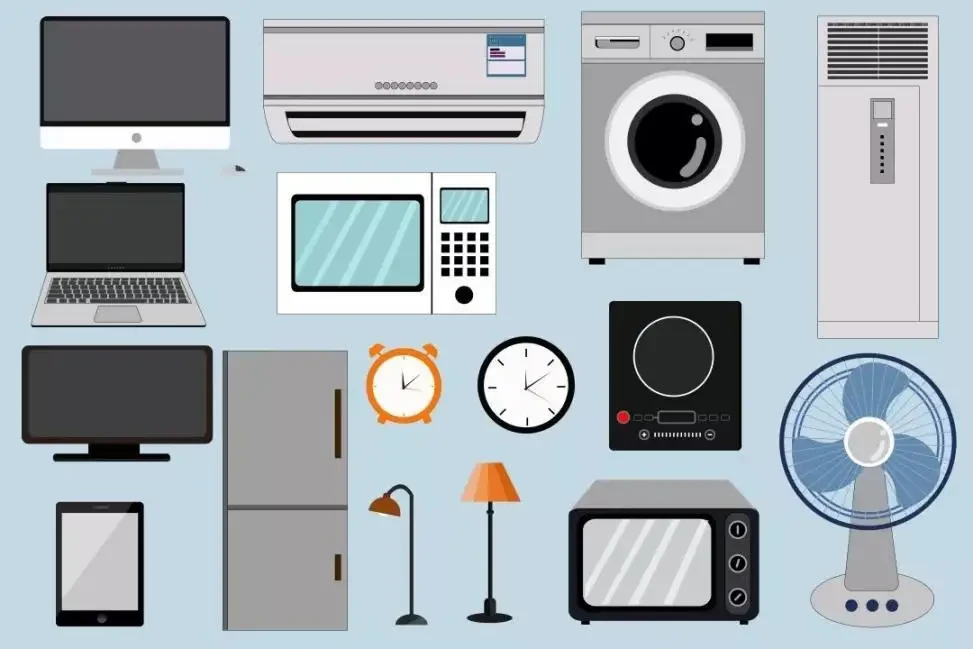
Taking small household appliances as an example, common products include electric pressure cookers, induction cookers, noodle makers, steamed bun makers, soy milk machines, food processors, juicers, electric kettles, hair dryers, straighteners, shavers, and more. These small household appliances frequently come into contact with users, are prone to wear, are regularly exposed to water, oil, and salt which can lead to corrosion, are used at high temperatures which can cause aging, and are often exposed to light which can lead to discoloration and loss of luster. Therefore, the materials used need to have strong aesthetic appeal, good scratch resistance, be easy to process, and offer a good cost-performance ratio. How to reasonably apply modified plastic materials to reduce the cost of small household appliances while ensuring product quality is one of the important ways for products to occupy the market.
Key plastic choices for common small home appliances
- Microwave oven
Plastic components mainly include exterior parts like the outer shell, base, handle, knobs, etc., requiring heat resistance. Materials used include heat-resistant ABS, flame-retardant HIPS, heat-resistant PP, PC/ABS alloy, etc.
- Rice cooker
Plastic components mainly include external parts like the outer shell, base, lid, handle, switch, etc., requiring heat resistance. Selected plastic types include non-spray ABS, high-gloss PP.
- Air Humidifier
Materials used include dyed ABS, non-spray materials, transparent parts (PC, GPPS), high-gloss PP.
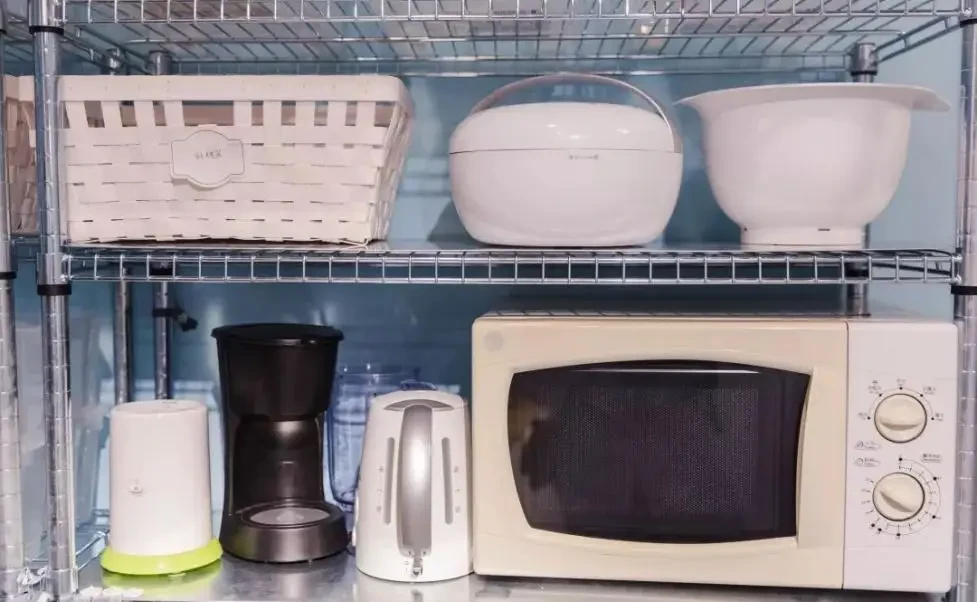
Main materials for exterior parts
Dyed ABS: Heat resistant, high surface gloss, dimensionally stable, easy to process, and easily sprayable. Can be made into different colors as per requirements.
PP with filler: Low cost, good fluidity, dimensionally stable, and easy to process.
PC material: High strength, high temperature resistance, and good transparency.
PC/ABS alloy: Heat resistant, good surface gloss, dimensionally stable, and easy to process.
Main materials for decorative parts
Transparent materials: Transparent ABS, PMMA, PC, etc.
Electroplating materials: Electroplating-grade ABS.
Non-spray materials: High-gloss non-spray ABS, non-spray AS, non-spray PC/ABS, non-spray PP.
Non-spray materials feature high gloss, metallic colors, good processability, bright colors, good fluidity, and scratch resistance.
Six major trends in modified plastics for home appliances
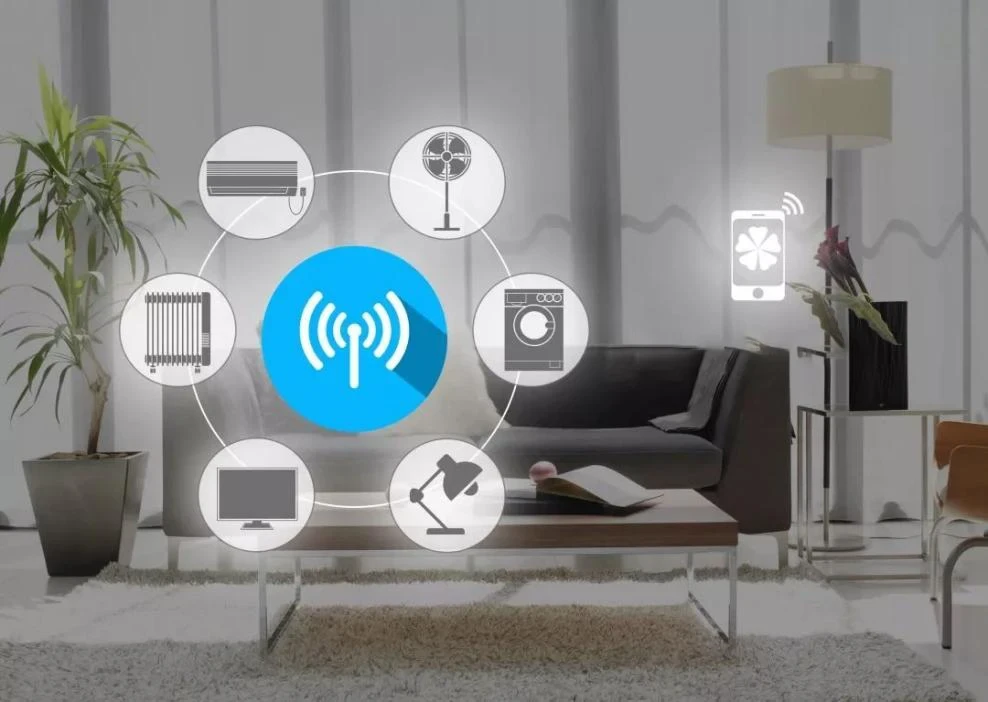
1. Appearance colour module solution
Technologically advanced, fashionable, and personalized colored home appliances have become an inevitable trend in current development. The main solutions include:
(1) Use of vivid, high-gloss, scratch-resistant materials, etc.
– Materials have richer colors, such as bright black, purple-red, tender green, bright red, ocean blue, etc.
(2) Non-spray series – Pearl and metallic colors, etc.
– Enables plastic products to achieve metallic effects like silver-white, luxury gold, silver-grey, etc., without the need for spraying or electroplating.
(3) Other special effects – Marble, crystal flow colors, etc.
– Achieves a marble or granite-like effect in the color of plastic products.
2. Safety material module solution
Safety appliances have become the basic element of current development.
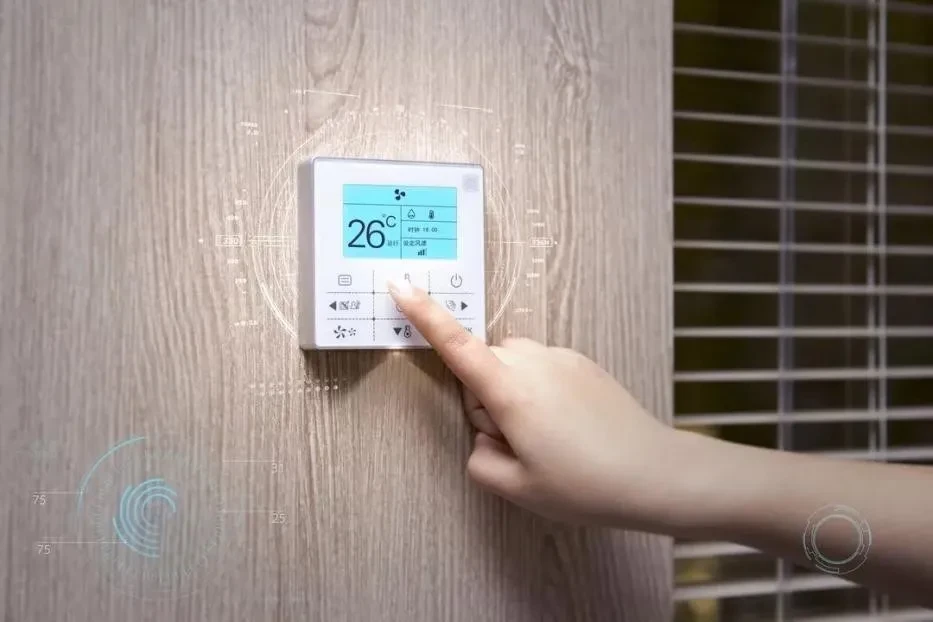
(1) Highly flame-retardant materials, halogen-free and low-smoke materials
For example, low smoke bromine-phosphorus synergistic high flame-retardant PP/ABS/PS or low smoke halogen-free flame-retardant PP/ABS/PS/PBT materials are used for internal parts or external parts such as motor boxes of refrigerators, air conditioners and washing machines to meet the requirements of 1.5mm 5VA, GWIT850℃, and so on.
(2) High performance materials
Permanent antistatic colored PP/ABS/PS, etc. are used in refrigerators, air conditioners and washing machine housings, etc.; high flame-retardant and high leakage tracing ABS/PP/PA/PBT, etc. are used in electronic control parts; conductive PP/ABS/PS/PBT, etc. are used in internal functional parts. These materials meet the requirements of white permanent anti-static 109, high CTI value (600V), etc.
3. Lightweight material module solutions
It is an inevitable trend for lightweight products to be extended from automobiles to home appliances.
(1) Plastic instead of glass, highly transparent and rigid materials
High transparency materials such as PP/ABS/PMMA/PETG/PES/PSF are used in components like observation windows. While ensuring transparency, these materials also meet food hygiene or scratch-resistant/strength requirements.
(2) Plastic instead of steel, rigid strength, high hardness dimensional stability materials
Materials with a high glass fiber content (>50%) and high strength, as well as long glass fiber reinforced materials (LFT-PP/PA), are used in technical structural parts of refrigerators, air conditioners, washing machines, etc. Glass fiber reinforced specialty engineering materials (PPS/PEI), etc., are used for wear-resistant parts. These materials meet the requirements for high strength, high wear resistance, boiling water resistance, and temperature resistance in structural components. In addition, microporous foaming materials can significantly reduce the weight of plastics used in home appliances while maintaining the same strength, and they do not exhibit warping or shrink marks, offering higher strength and processability.
4. Healthy material module solutions
The concept of health has become the current fashion in the development of home appliances.
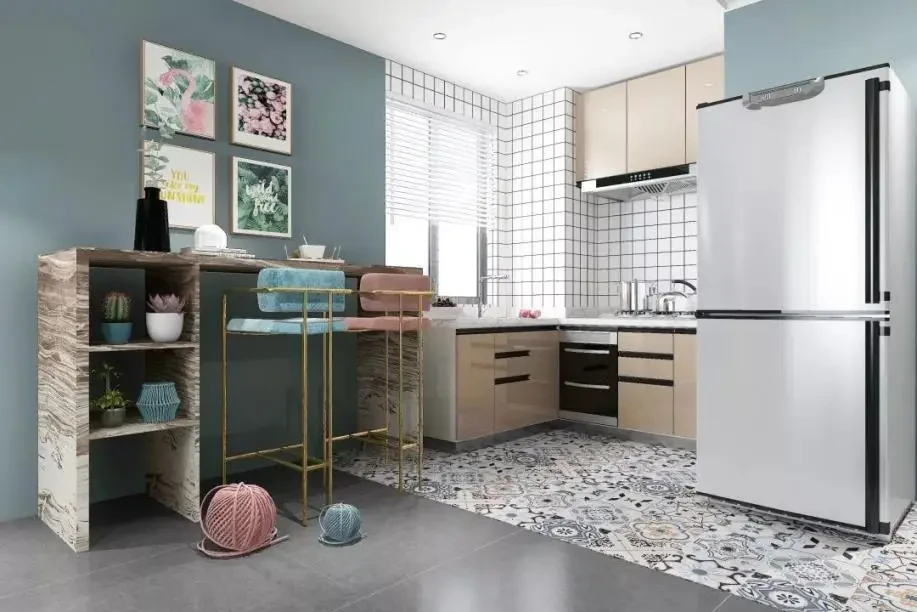
(1) Antibacterial / anti-mould materials
Incorporating inorganic eco-friendly composite antibacterial masterbatch or organic high polymer antibacterial agents, these materials meet antibacterial requirements without introducing secondary pollution (such as Ag, As ions) and can be used in internal or external parts of refrigerators, air conditioners, washing machines, etc.
(2) Non-toxic environmentally friendly materials
Use low VOC volatile materials (such as PP/PS/ABS) for internal and external components of home appliances; use plasticizer-free elastomer materials (TPE/TPV) for door seals and gaskets. Additionally, the standard requirements for VOCs in home appliances are being advanced.
(3) Environmentally friendly adsorption materials
Internal and external components of home appliances can be equipped with:
- PM2.5 adsorption materials, such as Viscoelastic stone filler
- Formaldehyde adsorption materials, incorporating activated silicon or aluminum oxide fillers
- Materials that release negative ions
5. Low-cost material module solutions
Low cost has been the urgent need for the development of home appliances.
(1) New and inexpensive functional materials
Inexpensive polyolefin materials are used, such as high-gloss PP to replace ABS, and ABS/PVC to replace flame-retardant ABS. Functional parts use plastic instead of steel, copper, glass, or aluminum. Mirror-like high glass fiber content PPS replaces electroplated metal parts. Eco-friendly, high-performance recycled plastics (PP/PS/ABS, etc.) replace new materials and comply with the United States EPEAT (Electronic Product Environmental Assessment Tool).
(2) Reducing quantity while maintaining strength
Home appliance internal parts use microporous foamed structure materials (PP/ABS/PS, etc.). 3D printing materials (FDM/SLA/SLS) are used for rapid prototyping in home appliances to reduce R&D costs. Product structure design is optimized through CAD/CAE, improving the design of internal and external parts of home appliances and reducing material usage.
(3) Industry chain integration: petrochemical manufacturers customize modified plastics
Petrochemical manufacturers cooperate with modified enterprises to customize specific materials such as high-gloss ABS/PS/PP, transparent ABS/PS/PP, and self-flame-retardant PA6/PA66, long-chain nylon, ASA.
6. Energy-saving and low-carbon material module solutions
(1) New low-carbon functional materials
Low carbon has become an inevitable trend in the development of home appliances. Biodegradable materials and their alloys (starch, PLA) are used for appliance packaging or non-structural parts. Natural fiber-reinforced materials (PP) can replace glass fiber-reinforced materials. High heat-resistant, high-rigidity polypropylene can replace PS/ABS/PA, such as in the PS framework of air conditioners. Polypropylene has the lowest carbon emission index (1.95) in modified plastics for home appliances, supporting low-carbon development and cost reduction.
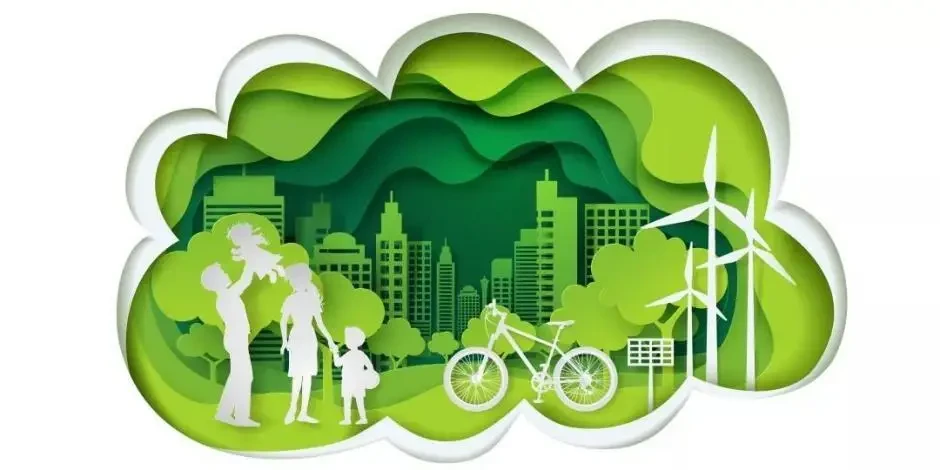
(2) Energy-saving and noise-reducing functional materials
Thermoplastic elastomer materials (PVC/TPV/TPE, etc.) are used for sealing and vibration damping components in home appliances. Low noise fans use microporous foaming materials to increase coaxiality and improve dynamic balance. Compressor vibration damping pads use high damping shock-absorbing elastomer materials to help reduce noise.
Disclaimer: The information set forth above is provided by Shanghai Qishen Plastic Industry independently of Alibaba.com. Alibaba.com makes no representation and warranties as to the quality and reliability of the seller and products.