Choosing the right die casting machine is not as easy as it sounds. These machines are available in different types and brands, and they are suitable for different products and molds. The right die casting machine will not only end up reducing the energy consumption level but also produce die casting parts of high quality. To avoid future regret as a buyer, you need to have all the facts and information about die casting machines.
This article presents the top tips that will help in selecting the right die casting machinery. The share of the die casting market and the different types of die casting machines will also be discussed.
Table of Contents
Market share of die casting machines market
Die casting machine and process
Types of die casting machines
Top tips for selecting die casting machines
Summary
Market share of die casting machines market
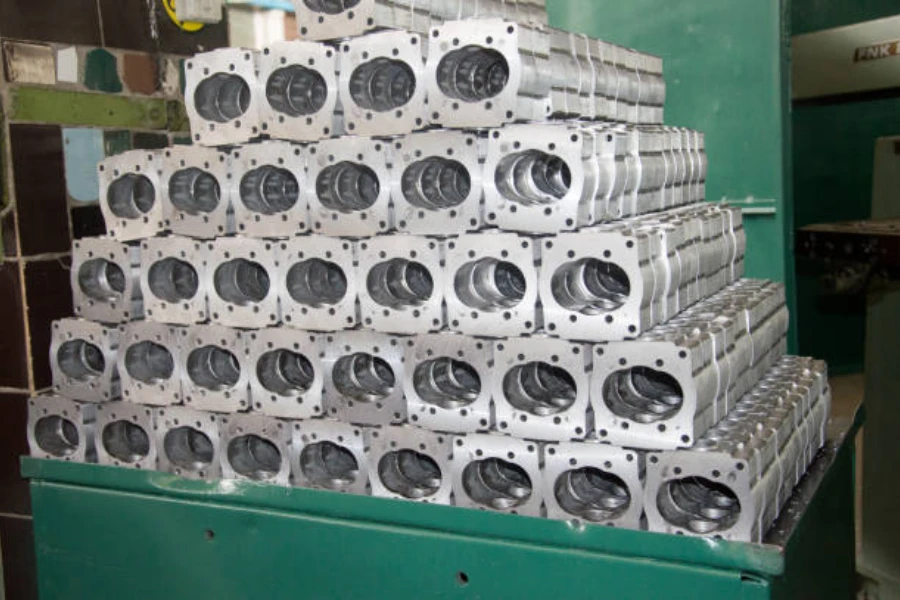
Global economies are experiencing a rise in demand for die-cast parts, especially in the automotive industry. This is due to the change in consumer preference toward lightweight vehicles. The die casting worldwide market is segmented based on the applications, processes, raw materials, and region.
Currently, the global die casting machines market is valued at USD 61.12 billion according to Mordor Intelligence. It is anticipated to expand at a CAGR of 5.92% and reach USD 86.3 billion by 2027. This growth is mainly driven by the surge in the automotive market, increased penetration of die-cast industrial machinery parts, and the frequent use of aluminum casts on electrical components.
During the forecast period, the Asia Pacific region is expected to experience the largest market share growth. This will be accelerated by the cheap labor and low costs of manufacturing in China and India. Also, aluminum will play a key role in the die casting process due to its increased application in numerous industrial processes. The major competitive producers continue to expand their presence worldwide. Some of these players include Neamk, Linamar Corporation, Alcoa Corporation, and Dynacast.
Die casting machine and process
Die casting entails a metal casting process where molten metal subjected to high pressure is passed through a metal mold into a mold cavity. When the metal cools afterward, it hardens into a finished product. It is an efficient way of producing a wide variety of metal-engineered parts in bulk. The metal molds referred to as dies are well fabricated to produce castings with intricate shapes while ensuring repeatability and accuracy. Most manufacturers use non-ferrous metals like aluminum, zinc, lead, and copper.
The most common types of die casts are:
– Single-cavity die: It creates solid uni-body parts.
– Multiple cavities die: It produces identical components at once.
– Unit die: It casts different components simultaneously.
– Combination die: It casts numerous unique parts used in future assembly.
Types of die casting machines
1. Hot chamber machines
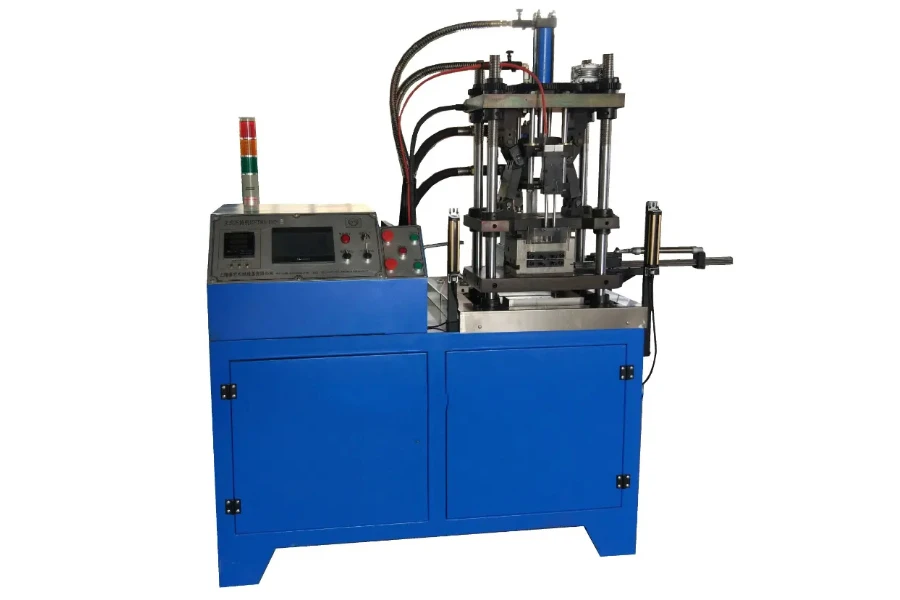
The hot-chamber die casting machines have a pressure chamber that is directly connected to the mold cavity. This allows a continuous flow of the molten metal into the pressurized compartment. They are also called gooseneck machines because of their metal feeding system’s shape. When the cylinder of the chamber reverts to an unpressurized position, the molten metal is in turn fed into the casting die.
This process is usually rapid and faster than in cold-chamber die casting machines. These machines are suited for alloys that have low melting points to prevent damage to the injection cylinder. The metals include zinc, copper, magnesium, and lead.
2. Cold chamber machines
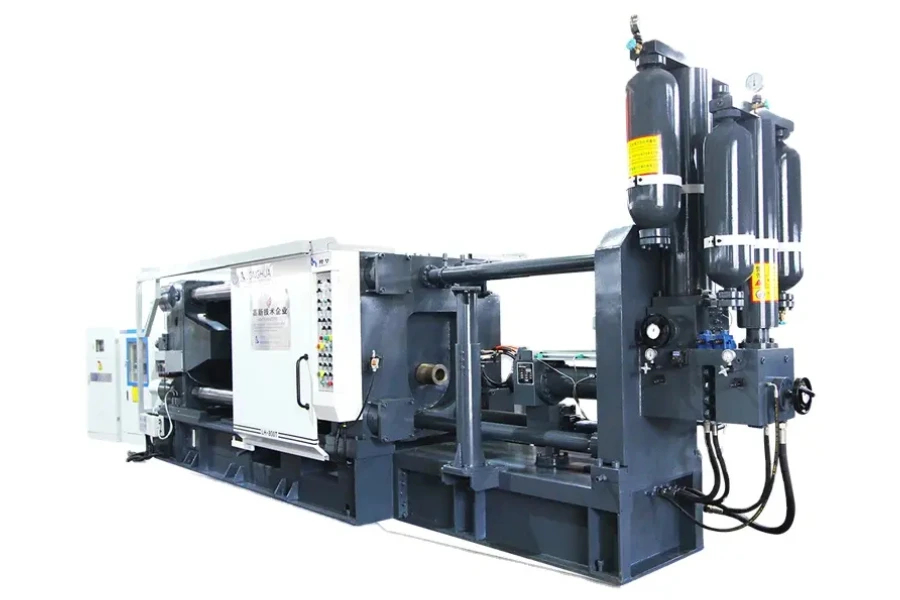
Cold chamber die casting machines need molten metal to be automatically ladled or hand-ladled into the chamber. A hydraulically operated plunger closes the pressure compartment afterward and forces the metal into a die. The machines minimize the heat amounts and thus reduce the chance of corrosion in the plunger and any other surrounding parts. Also, these machines are suitable for producing aluminum parts. Sometimes aluminum alloys can destroy the plungers and metal cylinders, which reduces the service life of the dies.
Top tips for selecting die casting machines
1. Die casting alloy
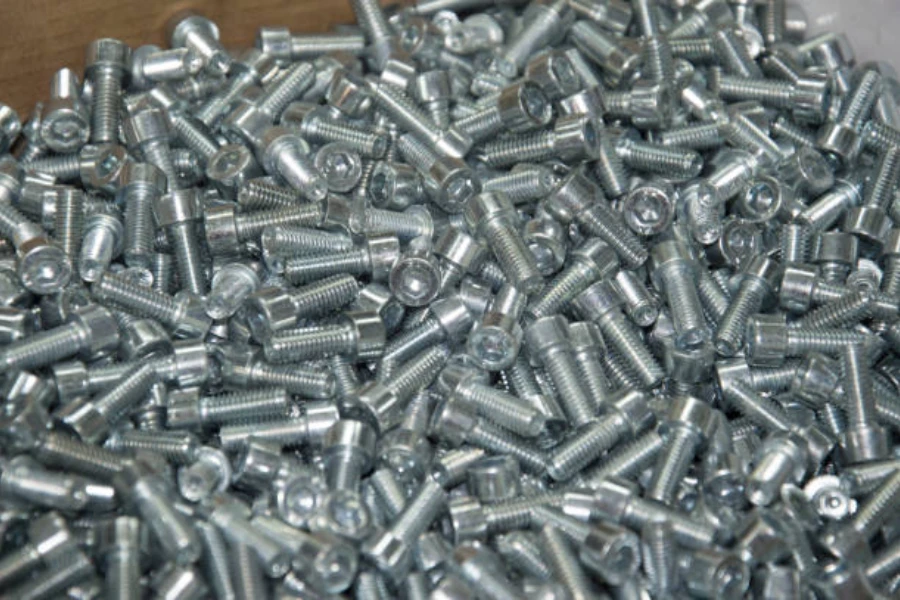
Generally, when using hot chamber die casting machines, zinc, lead, tin, and magnesium (small) are the preferred alloys. On the other hand, when buyers intend to employ cold chamber die casting machines, magnesium (large), aluminum, and copper are mostly used. Additionally, the vertical cold chamber die casting equipment is suited to create castings with central, cylindrical, and radial shapes.
Notably, if the product batch is large and the variety is small, buyers should consider using die casting machines with a high degree of automation and equipment completeness. In addition, other applications of die casting parts include the manufacture of consumer and industrial products, automotive products, and aerospace parts.
2. Size
Primarily, the size of the die casting mold should correspond with the installation size of the die casting equipment. Of importance is the thickness of the die casting mold and the distance separating the parting surfaces of the die. The standard minimum wall thickness for die casting machines ranges between 10.16 mm and 20.32 mm.
Buyers should make sure that the requirements of the basic parameters of die casting machines are met. Averagely, the die casting thickness (H) cannot be less than the minimum die thickness provided in the machine’s manual nor greater than the maximum given die thickness. Also, after the die casting machine is opened, the parting surface distance of the die casting machine should be greater or equal to the minimum distance that lets out the casting.
3. Cost
The costs associated with die casting include the machines’ purchase cost, costs during die casting production, secondary operations, and finishing. The process of die casting is quite cost-effective. This is because one part can be designed in replacement of multiple components. Other features are incorporated into the casting process to remove the need for secondary boring, milling, reaming, and grinding.
Also, hot chamber die casting machines vary in size ranging from 4 tons to 1200 tons, which affects their prices. On average, a 10-ton die casting machine can cost around USD 30,000 and a 1200-ton machine can cost up to USD 1,000,000. In this case, buyers should select the equipment based on their budget and production line needs.
4. Efficiency
On a general basis, manufacturers can achieve greater levels of efficiency by maximizing mold coverage. For instance, the use of traditional release agents that are water-based allows for rapid cooling of the mold surface, which results in extreme temperature fluctuations. This could lead to the formation of cracks on the surface of the mold due to the repetitive tensile and compressive stresses. Buyers need to understand that cracks might result in reduced life for the casted tool. Also, considering speed, the total cycle time during the die casting process lasts between two seconds and one minute. This is solely dependent on the complexity of the product.
Summary
Die casting has become an exact science due to advanced technology, improved casting materials, and the use of more efficient machines. Buyers should be aware of better-quality die designs and recent software that has enabled faster die fabrication, reduced waste, and improved machinery performance. They should also consider the above guide to select the most appropriate die casting machines that meet the demands of their production lines. To acquire sturdy and more durable die casting equipment that gives products with exceptional repeatability, visit Alibaba.com.