In the modern-day manufacturing industry, CNC turning centers and lathes have become two of the most important pieces of equipment. Demand for these tools has been significantly increasing due to the need for high-quality and precise components for multiple industrial applications.
This blog explores their features and differences, providing insights for improved decision-making when it comes to selecting between these two industrial solutions.
Table of Contents
Turning center and lathe market outlook
Key types of turning centers and lathes
Turning centers vs. lathes: what are the differences?
Conclusion
Turning center and lathe market outlook
Turning centers and lathes have revolutionized how manufacturers produce precision components. These machines have advanced features and components that improve efficiency and productivity, resulting in increased demand.
Turning centers’ market size and potential
The ongoing development in the industrial machinery sector has led to increased demand for turning centers. This is evidenced in the global market growth for CNC machines, which was valued at US$ 82.5 billion in 2022 and is projected to grow at a compound annual growth rate (CAGR) of 8.7% to reach US$ 185.4 billion by 2032.
The demand for turning machines has been accelerated by multiple factors, including:
- Increased industrial activities requiring turning centers to manufacture engine parts, shafts, gears, valves, and connectors
- Higher levels of automation resulting in greater efficiency and productivity, reduced labor costs, and faster cycle times
- Integration of advanced technologies, such as CNC systems and controls, which offer higher speed and increase the quality of products
- High levels of precision and accuracy.
Lathes’ market size and potential
The demand for lathes continues to grow due to the worldwide industrial growth and expansion of manufacturing activities. In 2022, the global lathes market was valued at US$ 24.0 billion and is projected to grow at a CAGR of 5% through 2023-2028 to reach US$ 32.7 billion by 2028.
Various factors are driving the lathes market growth, including:
- Increased demand in manufacturing industries such as automotive, aerospace, construction, and energy
- Manufacturers are looking for flexibility through technologically advanced lathes
- Integration of CNC integration and automation, which increase productivity and setup times.
Key types of turning centers and lathes
Turning centers and lathes are often designed to cater to different machining needs. There are multiple models available in the market, each with unique features, allowing manufacturers to choose the most suitable machine for their requirements and production processes.
Turning centers
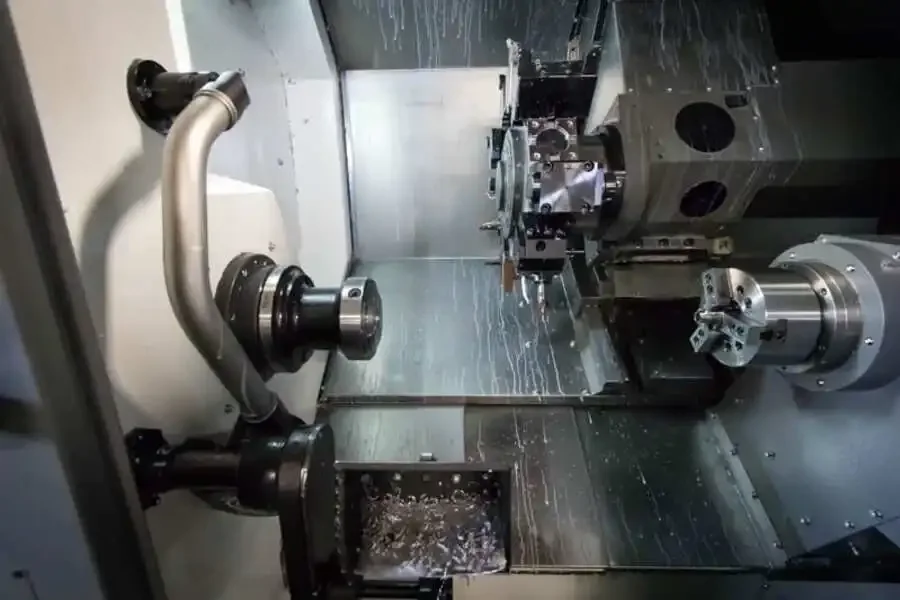
Turning centers are advanced computer numerically controlled (CNC) machines for various industrial operations. They typically have 3-5 axes and multiple cutting capabilities, including turning, milling, drilling, and tapping.
There are two main types of turning machines, horizontal and vertical.
1) Horizontal turning centers
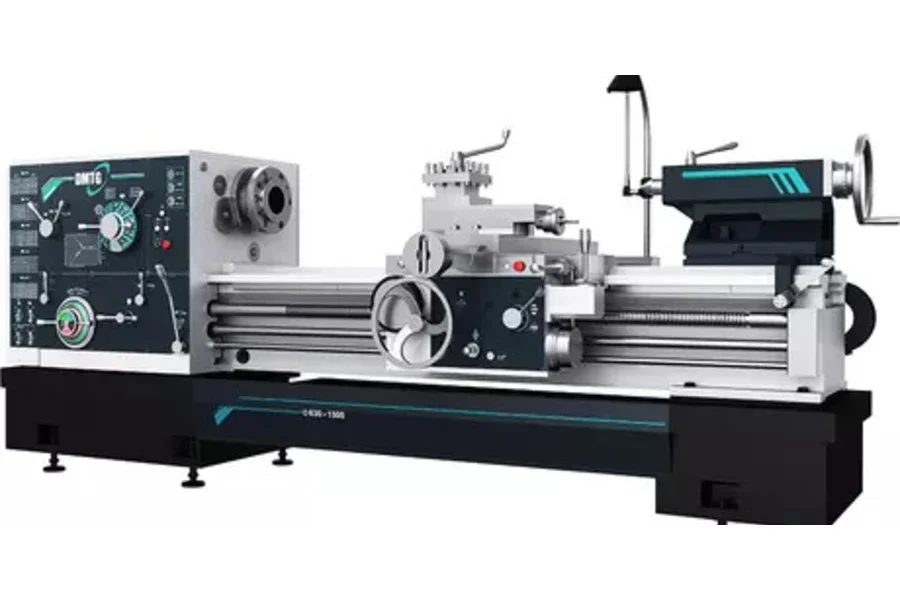
Horizontal turning centers are the most common turning machines across different industries. They are characterized by a horizontally-oriented spindle and tool holder used to mount the cutting tools.
Features
- A horizontally-oriented spindle
- X and Z axis movement
- Tool turrets
- Multi-axis machining capabilities, such as live tooling and Y-axis movement
- CNC control systems
- Adjustable tailstock
Pros
- Excellent stability and rigidity, resulting in improved accuracy and surface finish
- Multi-axis machining, which helps expand the range of operations
- Improved surface finish
- Increased productivity and operational efficiency
Cons
- Horizontal turning machines have larger footprints than vertical turning centers, thus requiring more floor space
- Limited accessibility and maneuverability
2) Vertical turning centers
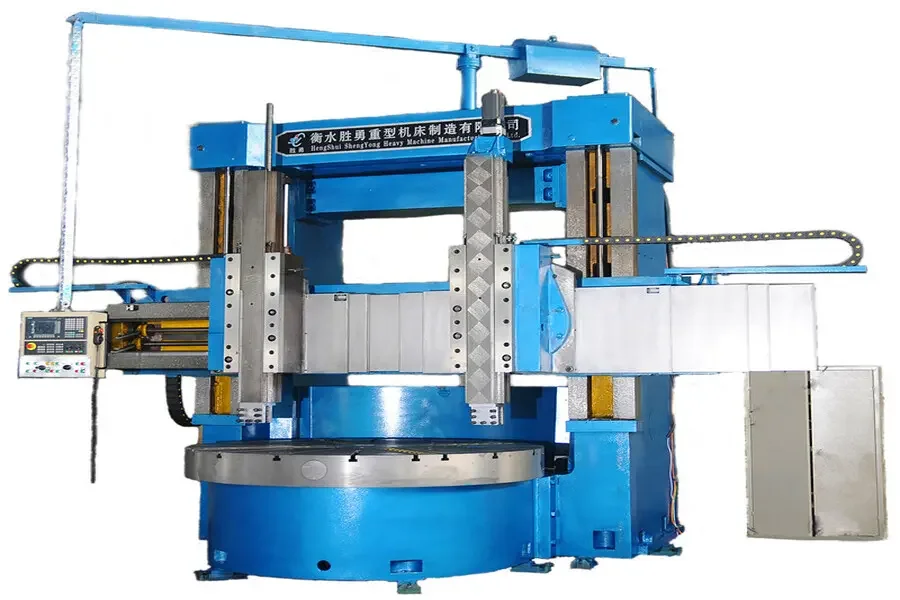
Vertical turning centers rotate a workpiece on a vertical axis. These machines are ideal for manufacturing shorter components that do not require a sub-spindle, tailstock or bottom turret.
Features
- Vertical spindle orientation
- Automatic tool change (ATC)
- Turret interface
- Larger vertical turning centers can handle components with a diameter of up to 300–800 mm (11.81–31.50 inches)
- Pick-up lathes are suitable for components with a diameter of up to 300 mm diameter (11.81 inches)
- CNC systems
- Multi-axis machining
Pros
- Gravity-assisted machining and clamping, which improve stability, rigidity, and accuracy
- They typically have a smaller footprint than horizontal turning centers, increasing space efficiency
- Multi-axis machining makes them applicable in various operations
Cons
- Unsuitable for long workpieces
- Higher initial investment costs compared to simpler machining tools
Lathe
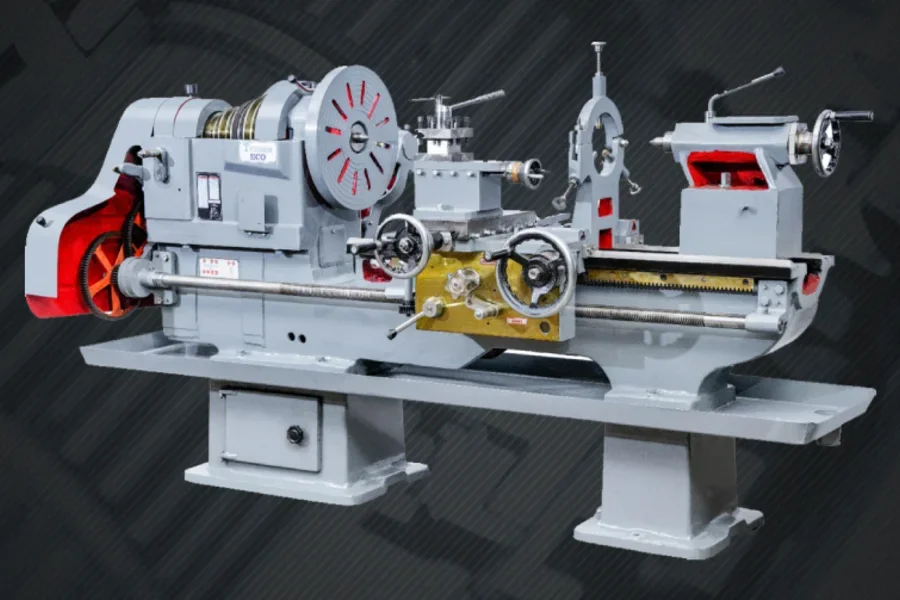
Lathes are multi-purpose machines used in production and repair for operations such as shaping, cutting, turning, facing, drilling, grooving, and threading. Examples of the different types of lathes in the market include:
1) CNC lathe machine
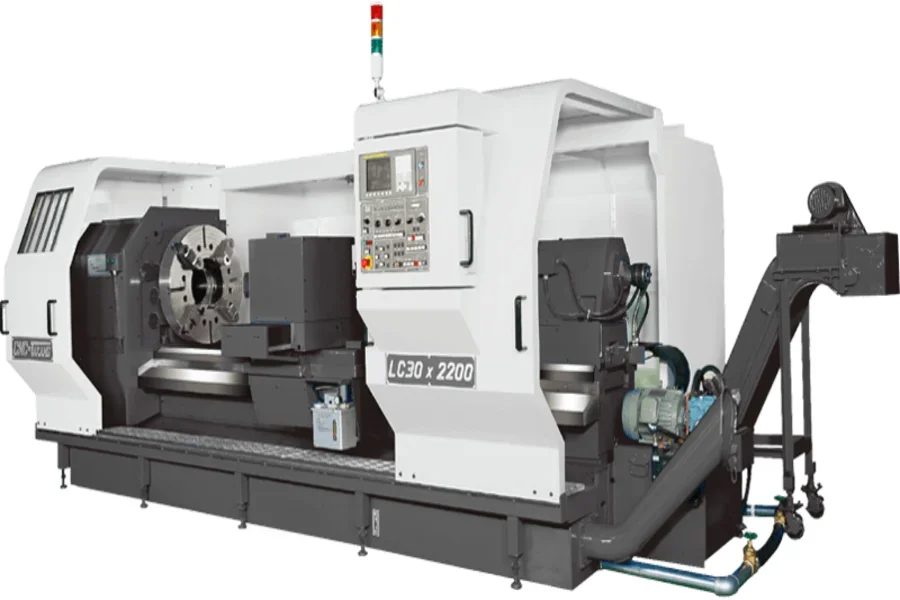
The CNC lathe machines have similar features as manual lathes, including spindle, headstock, chuck, tailstock, tool turret and centers. However, they have an additional CNC control panel component used to run programs and provide input instructions.
Features
- CNC control system
- Automatic tool changer (ATC)
- Programmable tailstock
- Live tooling
Pros
- In-process monitoring and quality control facilitated by the CNC control systems
- Higher accuracy and efficiency
- Reduced setup time
- Ideal for mass production
Cons
- Requires specialized knowledge and training
- Limited flexibility for small-batch productions
- Requires regular maintenance and repair, which results in longer downtime
2) Bench lathe machine
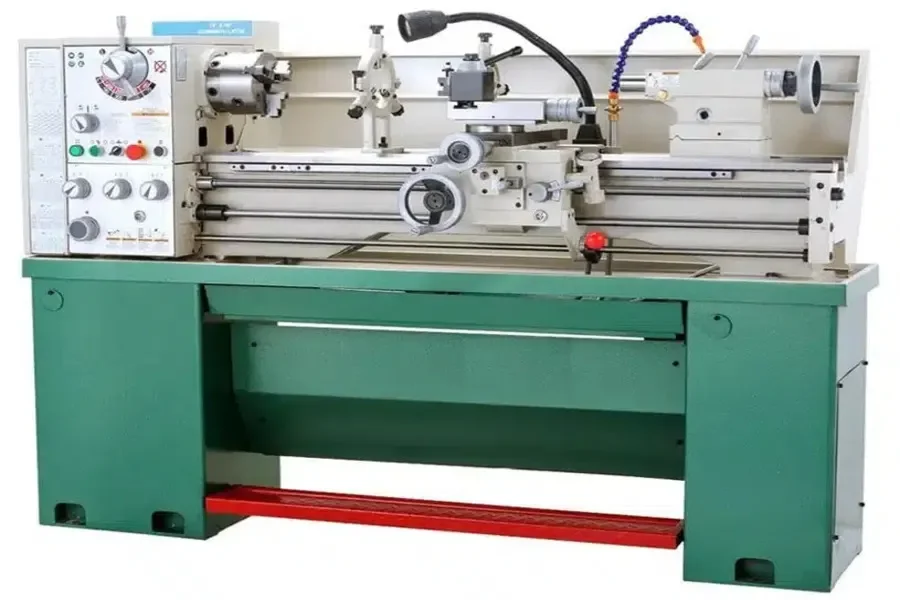
Bench lathe machines are compact and smaller-sized lathes designed for use on a workbench or table. They are typically used for smaller workpieces or lighter-duty applications, making them suitable for hobbyists, small workshops, or educational settings.
Features
- Adjustable speed control
- Lightweight and portable
- Adjustable tailstock and tool rest
- Some bench lathes offer variable chuck sizes.
Pros
- Ideal for workshops with limited space
- Can perform multiple operations despite their small size
- Affordable compared to other industrial lathes
Cons
- Unsuitable for heavy-duty or larger workpieces.
- Less power and rigidity due to their small size, which affects their ability to handle demanding cutting projects
3) Automatic lathe machine
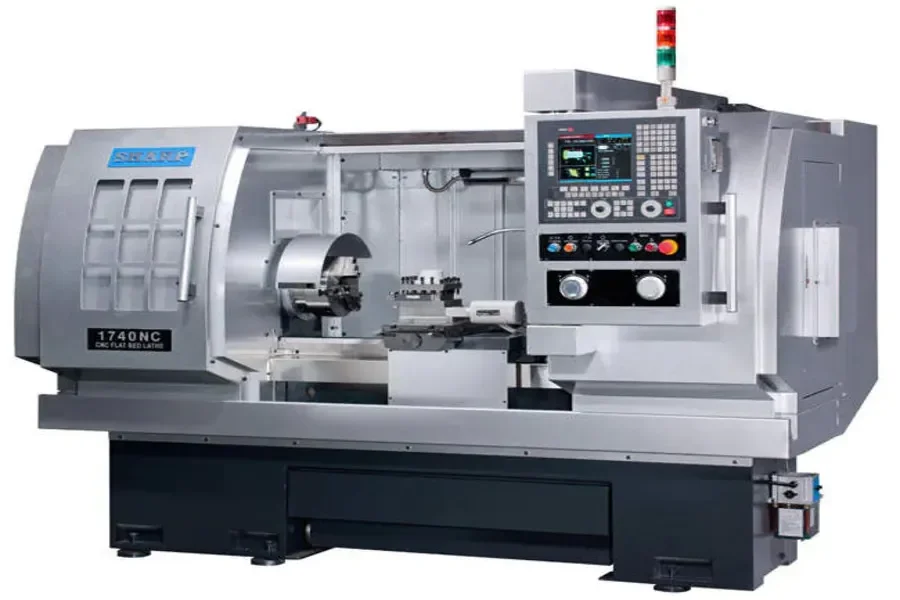
Automatic lathe machines are advanced machining tools designed for high-speed, automated production of turned components. These highly automated lathe machines can execute machining operations without constant manual intervention.
Features
- Equipped with advanced automation features
- Facilitates high-speed machining, enabling rapid production cycles and increased productivity
- CNC control systems
- Multiple spindles and tooling
- Automated part ejection and sorting systems
Pros
- High versatility and productivity
- The automated machining process reduces the labor costs
- Advanced control systems and rigid machine construction that increase precision and accuracy
- Suitable for mass production
Cons
- Complex programming and setup that may require specialized knowledge and training
- Unsuitable for projects involving larger or heavier components
4) Capstan/turret lathe machine
Turret lathes, also known as capstan lathes, are a type of lathe machine that incorporates a turret or tooling station. These machines are known for their rapid tooling changes, allowing quick and efficient machining operations.
Features
- Turret or tooling station
- Indexing mechanism for precise positioning of the turret
- Automatic feeding and material handling
- Allows multiple tool positions on the turret, thus eliminating the need for manual tool changes.
Pros
- High production rate
- Precise tool positioning, which improves accuracy and consistency
- Automation reduces labor costs
- Quick and efficient tool changes
Cons
- Unsuitable for intricate machining tasks that require specialized tooling or multiple-axis movements
- Limited number of tools on the turret
Turning centers vs. lathes: what are the differences?
Despite their potential use in overlapping roles, turning centers and lathes have different features and operational capabilities. This section explores their major differences.
Machine design
Turning centers and lathes have varying machine designs, determining their applications and functionality. For instance, turning centers have full machine enclosures and have “slant bed” configurations compared to lathes’ “flatbed” design.
Turning centers have additional features like live tooling and tool turrets that can hold turning, drilling, and milling tools. Lathes, in contrast, have a simpler tooling system and are usually designed as two-axis machines, focusing primarily on turning operations.
RPM capabilities
RPM capabilities for both machines are influenced by multiple factors, such as equipment power and design, workpiece type and size, cutting tools used, and material machined.
CNC turning centers have higher RPM capabilities than lathes due to broad spindle speed options. For CNC turning centers, the RPM speed can range from low for threading and heavy machining operations to high speeds for fine finishing and high-speed cutting.
Production rate and prototyping
Lathes are more suitable for short production runs, quick repairs, and simple parts like pins and bushings. They are quick to set up and run, both manually and on CNC programs.
Turning centers are more suitable for large production since they have more efficiency and production capabilities. They can perform more automated tasks at a higher rate than lathes. Turning centers are characterized by automatic material feeding and tools changing within programmed cycles to improve production efficiency.
Costs
Turning centers are more expensive than lathes since they have more features and capabilities. These machines are designed to handle a broader range of machining operations, such as turning, milling, drilling, and more. As a result, they are usually equipped with advanced components to incorporate multi-axis capabilities, live tooling, sub-spindles, and advanced automation features, making them more expensive.
Shape of the processed parts
Lathes are primarily used in processing cylindrical shapes such as cylinders, cones, and spheres. However, they have limited capabilities for complex geometries and secondary machining operations.
On the other hand, turning machines can handle a wide range of part shapes and geometries. They can process cylindrical shapes, such as shafts, rods, tubes, contours, profiles, and features requiring secondary operations such as milling and drilling.
Conclusion
The choice between turning centers and lathes depends on the desired results and type of project. For example, turning centers are more suitable for large-scale production, while lathes are more suitable for short-run projects. Therefore, clients will have varying needs and opt for different turning centers or lathes based on the scope of their needs and projects.
It is crucial for businesses targeting the machining industry to have a diverse inventory. Unlock the potential of your business with cutting-edge turning centers and lathes available on Alibaba.com today!