With the surge in electric vehicle adoption and the increasing demand for advanced automotive technologies, battery terminal connectors are more essential than ever in ensuring reliable power transmission. This article provides a comprehensive overview of the latest market trends, key selection criteria, and innovations in battery terminal connectors, equipping professional buyers with the insights needed to make informed purchasing decisions.
Table of Contents:
– Market Overview of Battery Terminal Connectors
– In-Depth Analysis of the Battery Terminal Connectors Market
– Key Factors When Selecting Battery Terminal Connectors
– Types of Battery Terminal Connectors
– Latest Technology Features in Battery Terminal Connectors
– Pricing and Budget Considerations
– Installation and Maintenance Tips
– In Summary
Market Overview of Battery Terminal Connectors
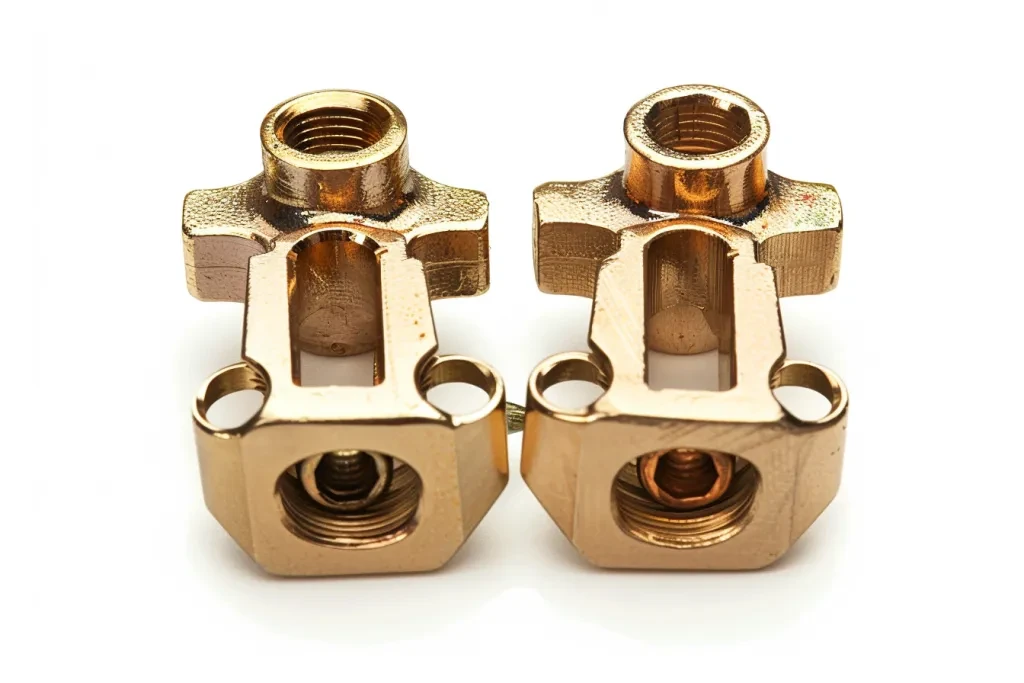
The global automotive terminals market has seen significant growth due to the rising adoption of electric vehicles (EVs) and the demand for advanced automotive technologies. The market is expected to continue growing at an annual rate of 11.90%, reaching USD 52.64 billion by 2030. This growth is due to the crucial role battery terminal connectors play in maintaining effective connectivity within automotive electrical systems.
Battery terminal connectors are mainly made from materials like brass, phosphor bronze, and plated steel, known for their high conductivity and corrosion resistance. The increase in electric and hybrid vehicle adoption, along with the integration of advanced safety features and infotainment systems, has driven the demand for reliable automotive terminals. Regulatory standards for improved vehicle safety and reduced carbon emissions also support market growth.
Regionally, the Americas, especially the United States, lead the market due to advanced automotive manufacturing and strict safety regulations. The Asia-Pacific region, with its rapid vehicle production and growing automotive electronics sector, shows significant growth potential, particularly in China and India. Europe, known for its luxury automotive segment, continues to invest in high-quality, advanced terminals to support electric vehicle technologies.
In-Depth Analysis of the Battery Terminal Connectors Market
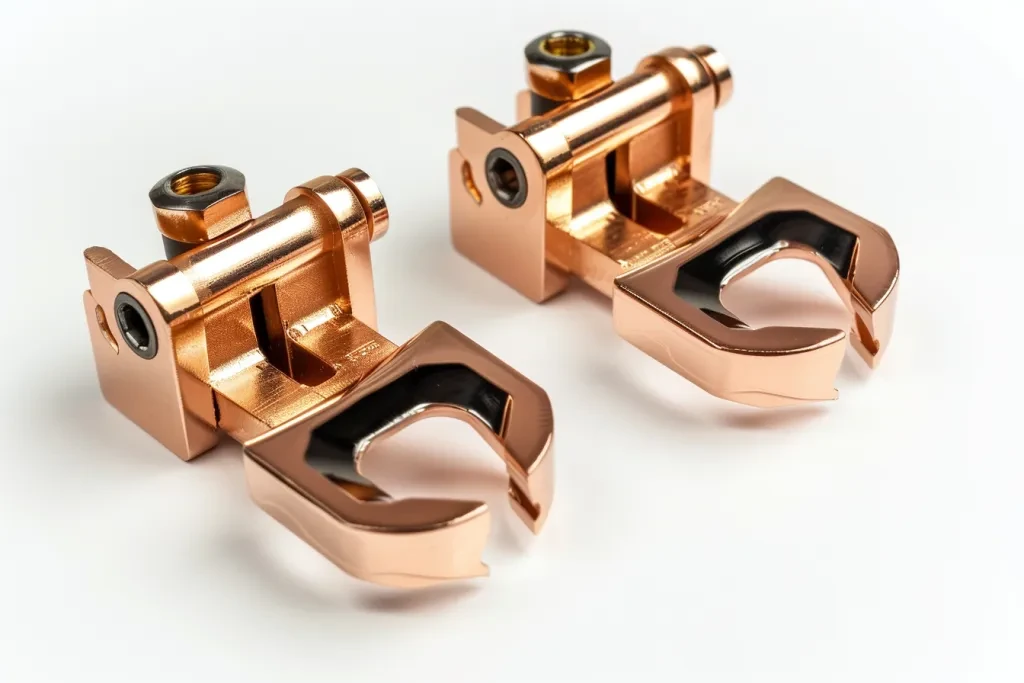
Key Performance Benchmarks and Market Share Dynamics
Battery terminal connectors are vital components in automotive electrical systems, ensuring reliable power transmission and connectivity. These connectors must meet high performance standards, such as high current carrying capacity, durability, and resistance to environmental factors. The market is competitive, with key players like Amphenol Corporation, TE Connectivity, and Yazaki Corporation holding significant shares.
Market dynamics are influenced by the growing demand for EVs, government mandates for enhanced vehicle safety, and the need for advanced automotive electronics. The integration of autonomous driving technologies and the trend toward vehicle electrification also drive market growth. However, challenges such as wear, corrosion, and the need for robust terminal designs persist.
Economic Influences and Consumer Behavior Shifts
Economic factors like rising disposable incomes and increased consumer awareness of environmental sustainability are driving the demand for electric vehicles, boosting the need for battery terminal connectors. The shift towards greener technologies and EV adoption, supported by government incentives and subsidies, further propels market growth.
Consumer preferences are shifting towards vehicles with advanced safety and infotainment systems, requiring sophisticated electrical frameworks. Seasonal demand patterns, particularly in regions with extreme weather, affect the need for connectors with enhanced durability and corrosion resistance.
Distribution Channel Preferences and Recent Innovations
Distribution channels for battery terminal connectors include original equipment manufacturers (OEMs) and the aftermarket. OEMs dominate the market due to the high demand for quality terminals in new vehicle production. The aftermarket also plays a significant role, catering to replacement and maintenance needs.
Recent innovations include terminals with improved corrosion resistance and advanced plating techniques. Companies like I-PEX and Littelfuse are introducing cutting-edge products to meet the growing demand for reliable automotive terminals. For example, I-PEX’s AP-TSS10 and AP-LT10 terminals handle high currents and elevated temperatures, while Littelfuse’s IXTY2P50PA MOSFET offers ultra-low on-state resistance and robust performance in harsh environments.
Environmental Regulations and Market Opportunities
Stringent environmental regulations aimed at reducing carbon emissions are driving the adoption of electric vehicles, increasing the demand for battery terminal connectors. The development of autonomous and semi-autonomous vehicles presents significant market opportunities, as these vehicles require advanced electrical systems with high-performance connectors.
The trend towards miniaturization of automotive terminals is driven by the need for compact and lightweight components for modern vehicles. This trend is especially relevant for electric and hybrid vehicles, where space and weight constraints are crucial.
Customer Pain Points and Brand Positioning Strategies
Despite growth prospects, the market faces challenges related to the durability and reliability of automotive terminals. Harsh environmental conditions can lead to wear and corrosion, causing unreliable connections and potential system failures. Manufacturers address these issues by developing more robust terminal designs and materials with better corrosion resistance.
Brand positioning strategies focus on differentiation through innovation and quality. Leading companies emphasize the reliability and performance of their products, leveraging advanced materials and technologies to gain a competitive edge. Niche markets, such as high-performance and luxury vehicles, offer additional opportunities for specialized terminal connectors.
In conclusion, the battery terminal connectors market is poised for substantial growth, driven by the increasing adoption of electric vehicles and the demand for advanced automotive technologies. Regulatory standards, consumer behavior shifts, and recent innovations will continue to shape the market landscape, presenting opportunities for manufacturers to innovate and expand their product offerings.
Key Factors When Selecting Battery Terminal Connectors
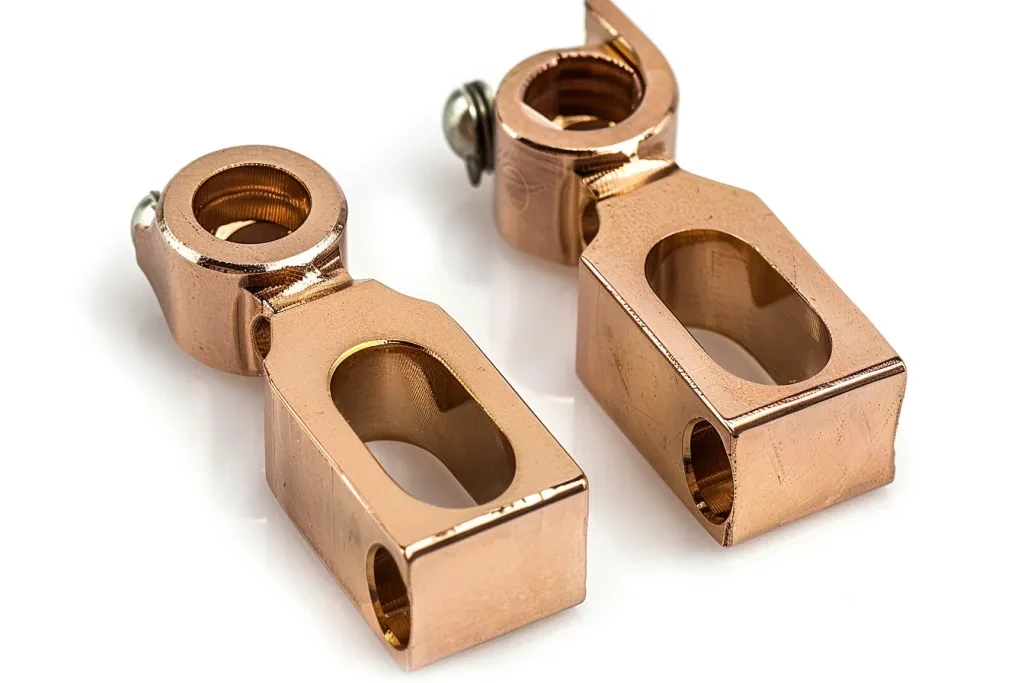
When selecting battery terminal connectors, it’s crucial to consider various factors to ensure optimal performance, compatibility, and safety. These factors include material, design, size, current rating, and environmental resistance. Understanding these aspects will help in making an informed choice for your specific needs.
Material
The material of the battery terminal connector significantly affects its performance and durability. Common materials include:
Copper: Known for its excellent conductivity and corrosion resistance, copper ensures minimal voltage drop and efficient power transfer.
Brass: Brass connectors offer good conductivity and are resistant to corrosion, making them durable for automotive applications.
Lead: Traditional but being phased out due to environmental concerns, lead connectors are still found in some older vehicles and equipment.
Nickel-plated: These provide enhanced corrosion resistance, suitable for harsh environments, and maintain conductivity over a longer period.
Choose the material based on the specific application requirements and environment.
Design
The design of battery terminal connectors influences their ease of use and reliability. Common designs include:
Top post: Widely used in automotive batteries, featuring a clamp that fits over the battery post for a secure connection.
Side post: Used in some automotive batteries where space is limited, providing a low-profile connection.
Lug-style: Used in industrial and commercial applications, offering a secure connection for high-current applications.
Quick-connect: Allow for easy installation and removal, ideal for applications needing frequent disconnections.
Each design offers unique benefits, and the choice should be based on the application requirements.
Size
Battery terminal connectors come in various sizes to accommodate different battery posts and cable sizes. Common sizes include:
Standard automotive sizes: Used in cars, trucks, and motorcycles.
Heavy-duty sizes: Used in industrial and commercial applications, accommodating larger cables and higher current ratings.
Custom sizes: Required for specific battery posts or cable configurations.
Ensuring the correct size is crucial for a secure and reliable connection.
Current Rating
The current rating indicates the maximum current a connector can safely carry. Match the connector’s current rating with the application’s requirements. Consider:
Maximum current draw: Ensure the connector can handle peak current without overheating.
Duty cycle: Continuous high-current applications require connectors with higher current ratings.
Safety margins: Select connectors with a higher current rating than the maximum expected current for reliability and safety.
Choosing the right current rating prevents overheating and potential damage.
Environmental Resistance
Battery terminal connectors must withstand various environmental conditions. Consider:
Corrosion resistance: Select materials or coatings that resist corrosion, like nickel-plated or brass connectors.
Temperature tolerance: Ensure connectors can operate within the application’s temperature range.
Moisture resistance: For applications exposed to moisture, choose connectors with seals or coatings that prevent water ingress.
Environmental resistance ensures longevity and reliability.
Types of Battery Terminal Connectors
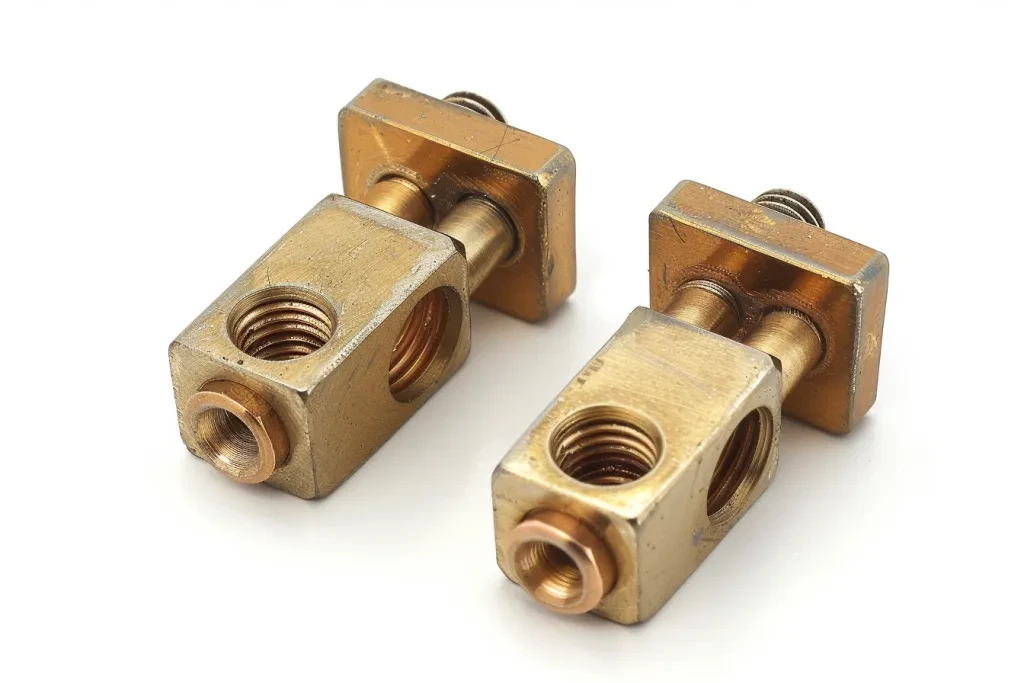
Battery terminal connectors come in various types, each designed for specific applications. Understanding the different types can help in selecting the most suitable connector.
Top Post Connectors
Commonly used in automotive applications, these connectors feature a clamp that fits over the battery post, providing a secure connection. They are easy to install and remove, available in materials like copper, brass, and lead, and designed to handle high current loads.
Side Post Connectors
Used in some automotive batteries where space is limited, providing a low-profile connection. Typically made of brass or lead, they offer good conductivity and corrosion resistance. Side post connectors are often found in General Motors (GM) vehicles.
Lug-Style Connectors
Used in industrial and commercial applications where high current loads are common. These connectors feature a lug or eyelet crimped or soldered to the cable, providing a secure connection. They are made of copper or brass, offering excellent conductivity and durability.
Quick-Connect Connectors
Designed for applications requiring frequent disconnections, these connectors feature a mechanism allowing easy installation and removal without tools. Commonly used in marine, RV, and portable power applications, they offer good conductivity and corrosion resistance.
Specialty Connectors
Designed for specific applications, including:
Military-grade connectors: Used in military and aerospace applications for high reliability and durability.
Heavy-duty connectors: Designed for industrial and commercial applications to handle high current loads.
Custom connectors: Required for unique battery post sizes or cable configurations.
Specialty connectors provide tailored solutions for demanding applications.
Latest Technology Features in Battery Terminal Connectors
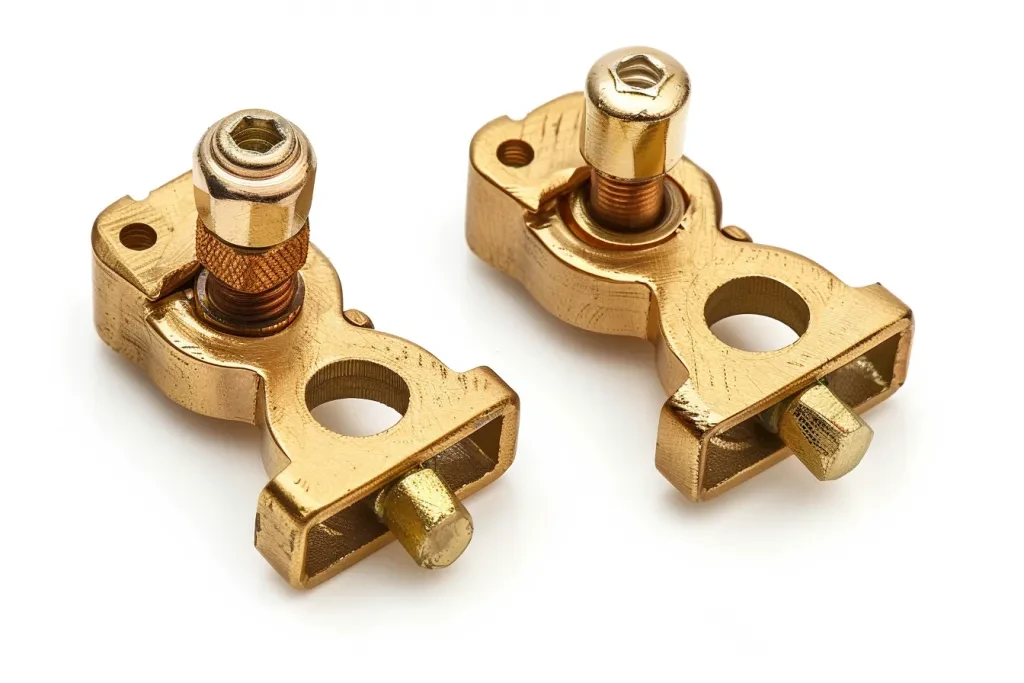
Advancements in technology have led to innovative features in battery terminal connectors, enhancing performance, safety, and ease of use.
Solid-State Battery Connectors
Developed for solid-state batteries, these connectors ensure efficient power transfer and reliability. Made of materials that withstand higher temperatures, they feature advanced sealing mechanisms to prevent moisture and contaminants.
Smart Connectors
Incorporating sensors and electronics, smart connectors provide real-time monitoring and diagnostics. They measure parameters like voltage, current, and temperature, enhancing safety and performance through proactive maintenance.
Quick-Release Mechanisms
Simplify installation and maintenance with tool-free connection and disconnection, ideal for applications requiring frequent battery changes or maintenance.
High-Temperature Connectors
Designed to operate in extreme temperature environments, these connectors are made of materials that can withstand high temperatures without degrading.
Corrosion-Resistant Coatings
Enhance durability and longevity with coatings that protect from moisture, chemicals, and environmental contaminants.
Pricing and Budget Considerations
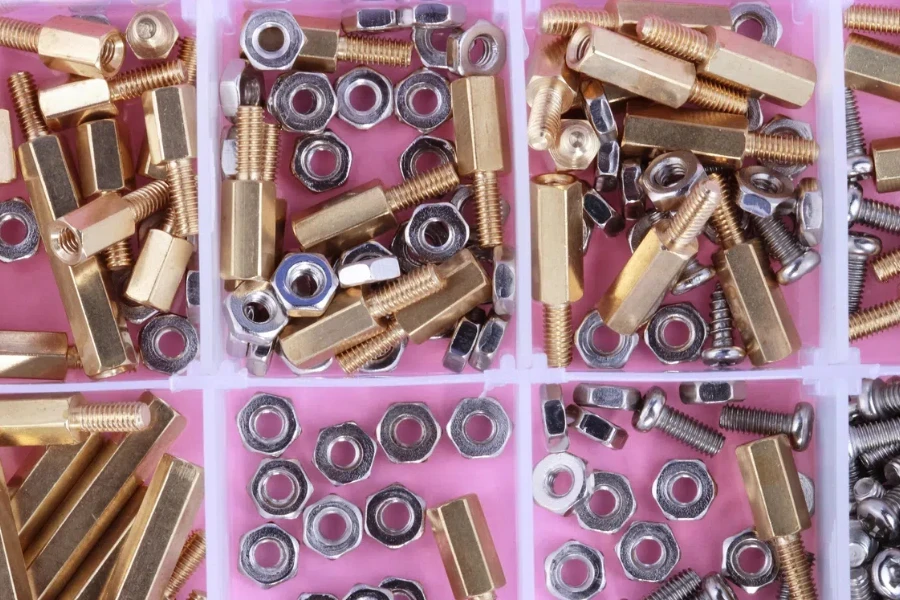
When selecting battery terminal connectors, consider the cost and budget. Prices vary based on factors like material, design, and features. Key considerations include:
Material and Quality
Higher-quality materials like copper and brass are more expensive but offer better performance and durability, resulting in long-term cost savings.
Design and Features
Connectors with advanced features like smart monitoring and quick-release mechanisms may cost more but enhance performance and ease of use.
Quantity and Supplier
Purchasing in bulk from reputable suppliers can lead to cost savings. Compare prices and consider overall value, including quality, performance, and after-sales support.
Long-Term Costs
Consider maintenance, replacements, and potential performance issues. Investing in high-quality connectors can result in better reliability and reduced downtime.
Installation and Maintenance Tips
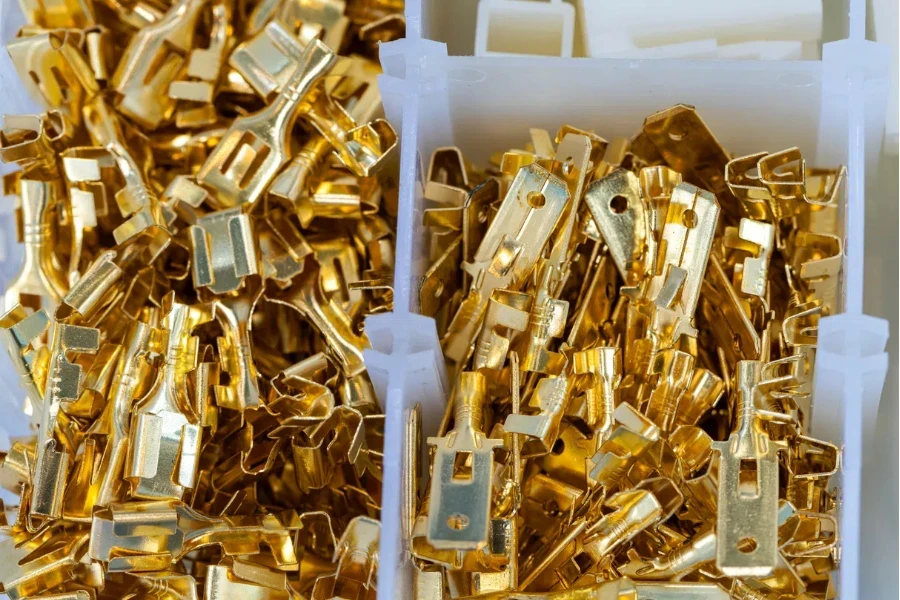
Proper installation and maintenance are essential for ensuring reliable performance and longevity. Here are some tips:
Installation Tips
Clean the battery posts and connectors: Ensure they are clean and free from corrosion.
Ensure a secure connection: Tighten connectors securely to prevent loose connections.
Use appropriate tools: Use correct tools for installing and tightening connectors.
Check polarity: Ensure positive and negative connectors are correctly installed.
Maintenance Tips
Regular inspection: Periodically inspect for signs of corrosion, wear, or damage.
Clean and lubricate: Clean regularly and apply dielectric grease to prevent corrosion.
Check tightness: Ensure connectors remain securely tightened.Replace damaged connectors: Replace any damaged connectors immediately.
In Summary
Battery terminal connectors are critical components in various applications. Selecting the right connectors involves considering factors like material, design, size, current rating, and environmental resistance. Understanding the different types and their features can help in making an informed choice.
Advancements in technology have led to innovative features, enhancing performance, safety, and ease of use. Cost and budget considerations are significant in the selection process, and investing in high-quality connectors can result in long-term cost savings. Proper installation and maintenance are essential for reliable performance and longevity.
By evaluating these factors and following best practices, you can select and maintain battery terminal connectors that meet your specific application requirements.