The ultrafast laser is a type of ultra-intense, ultra-short-pulsed laser with a pulse width below or within the picosecond level (10-12s), which is defined based on the energy output waveform.
The name of the laser is based on the “ultrafast phenomenon,” which refers to a phenomenon where the microscopic system of matter changes rapidly in a physical, chemical, or biological process. In the atomic and molecular system, the time scale of the motion of atoms and molecules is on the order of picoseconds to femtoseconds. For example, the period of molecular rotation is on the order of picoseconds and the period of vibration is on the order of femtoseconds.
When the laser pulse width reaches the level of picosecond or femtosecond, it largely avoids any influence it has on the overall thermal motion of molecules, which is the microscopic essence of the temperature of matte. Additionally, the material is influenced and generated by the time scale of molecular vibration, meaning that while processing, the thermal effect is greatly reduced.
Table of Contents
Types of ultrafast laser
Components of an ultrafast laser
Ultrafast laser applications
Pros and cons of an ultrafast laser
Types of ultrafast laser
There are many classification methods for lasers, with the four most commonly used classification methods being classification by working substance, classification by energy output waveform (working mode), classification by output wavelength (color), and classification by power.
According to the energy output waveform, lasers can be divided into continuous lasers, pulsed lasers, and quasi-continuous lasers:
Continuous laser
A continuous laser is a laser that continuously outputs stable energy waveforms during working hours. It is characterized by high power and its ability to process voluminous materials with a high melting point, such as metal plates.
Pulsed laser
Pulsed lasers output energy in the form of pulses. According to the pulse width, these lasers can be further divided into millisecond lasers, microsecond lasers, nanosecond shutdown devices, picosecond lasers, femtosecond lasers, and attosecond lasers. For example, if the pulse width of the output laser is between 1-1000ns, it would be classed as a nanosecond laser. For picosecond lasers, femtosecond lasers, attosecond lasers, and ultrafast lasers, the power of the pulsed laser is much lower than that of the continuous laser but the processing accuracy is higher. In general, the narrower the pulse width, the higher the processing accuracy.
Quasi-CW laser
The quasi-CW laser is a pulse laser that can repeatedly output a relatively high-energy laser within a certain period.
The energy output waveforms of the above-mentioned three lasers can also be described by the parameter “duty cycle.”
For a laser, the duty cycle can be interpreted as the ratio of the “time of laser energy output” relative to the “total time” within a pulse cycle. So, CW laser duty cycle (=1) > quasi-CW laser duty cycle > pulsed laser duty cycle. Generally, the narrower the pulse width of the pulsed laser, the lower the duty cycle.
In the field of material processing, pulsed lasers were initially a transitional product of continuous lasers. This is because the continuous lasers’ output power is unable to reach very high due to the influence of factors including the bearing capacity of core components and the level of technology in the early stage, as well as the fact that the material cannot be heated to the melting point. These factors are what achieve the purpose of processing, meaning the need for innovation.
The innovation came with certain technical means being used to concentrate the output energy of the laser on a single pulse. This stopped the total power of the laser from changing but allowed for the instantaneous power at the time of the pulse to greatly increase and so satisfy the requirements of material processing.
Later, continuous laser technology gradually matured and it was found that the pulsed laser has a great advantage in processing accuracy. This is because the thermal effect of pulsed lasers on materials is smaller; the narrower the laser pulse width, the smaller the thermal effect; and the smoother the edge of the processed material, the higher the corresponding machining accuracy.
Components of an ultrafast laser
Two of the core requirements for a laser to be considered an ultrafast laser are a high stability ultrashort pulse and high pulse energy. Generally, ultrashort pulses can be obtained by using mode-locking technology, while high pulse energy can be obtained by using CPA amplification technology.
The core components involved include oscillators, stretchers, amplifiers, and compressors. Among them, the oscillator and amplifier are the most challenging, but they are also the core technology behind any ultrafast laser manufacturing company.
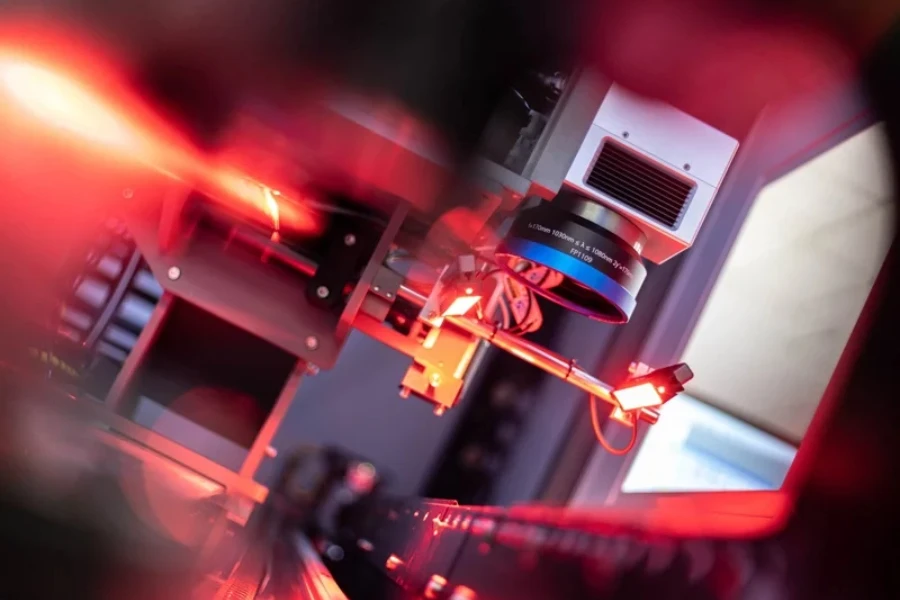
Oscillator
A mode-locking technique is used to obtain ultrafast laser pulses in the oscillator.
Stretcher
The stretcher stretches the femtosecond seed pulses apart in time by using different wavelengths.
Amplifier
A chirped amplifier is used to fully energize the now-stretched pulse.
Compressor
The compressor unites the amplified spectra of the various components and restores them to the femtosecond width, thereby forming femtosecond laser pulses with extremely high instantaneous power.
Ultrafast laser applications
When compared with nanosecond and millisecond lasers, ultrafast lasers have lower overall power, however, since they directly act on the timescale of the material molecular vibrations, ultrafast lasers realize “cold processing” in the true sense, meaning greatly improved processing accuracy.
Due to their different characteristics, high-power continuous lasers, non-ultrafast pulsed lasers, and ultrafast lasers all present great differences in the downstream application fields:
High-power continuous lasers (and quasi-continuous lasers) are used for cutting, sintering, welding, surface cladding, drilling, and the 3D printing of metal materials.
Non-ultrafast pulsed lasers are used to mark non-metallic materials, process silicon materials, clean and carry out precision engraving on metal surfaces, precision weld metals, and micromachine metals.
Ultrafast lasers are used to cut and weld hard and brittle materials, as well as transparent materials such as glass, PET, and sapphire. In addition, they are used for precision marking, ophthalmic surgery, microscopic passivation, and etching.
From the point of view of their usage, high-power CW lasers and ultrafast lasers have almost no mutual substitution relationship. They are like axes and tweezers, and their sizes have both their advantages and disadvantages.
The downstream applications of non-ultrafast pulsed lasers do have some overlap with those of continuous lasers and ultrafast lasers. However, judging by the results achieved when under the same applications, the power of a non-ultrafast pulsed laser is not as good as that of a continuous laser and its accuracy is not as good as that of an ultrafast laser. Its most prominent feature is cost performance.
The nanosecond ultraviolet laser in particular, although having a pulse width that does not reach the picosecond level, has much higher processing accuracy than other color nanosecond lasers. The nanosecond ultraviolet laser is widely used in the processing and manufacturing of 3C products and as the cost of ultrafast lasers decreases in the future, it may occupy the nanosecond ultraviolet market.
Ultrafast lasers realize cold processing in a real sense and have significant advantages in precision processing. In addition, as production technology gradually matures, the cost of these ultrafast lasers will decrease. For these reasons, it is expected that these lasers will be widely used in medical biology, aerospace, consumer electronics, lighting display, energy environment, precision machinery, and other downstream industries in the future.
Medical cosmetology
Ultrafast lasers can be used in medical eye surgery equipment and cosmetic devices. For example, the femtosecond laser is used in myopia surgery and is known, after wavefront aberration technology, as “another revolution in refractive surgery.”
The eye axis of myopic patients is larger than a normal eye axis, meaning that when in a state of relaxation, the focus of the parallel light rays by the eye’s refractive system after refraction falls in front of the retina. Femtosecond laser surgery can remove excess muscle in the axial dimension and restore the axial distance to its normal length. Femtosecond laser surgery has the advantages of high accuracy, high safety, high stability, short operation time, and high comfort, which has led it to become one of the most mainstream myopia surgery methods.
In terms of beauty, ultra-fast lasers can be used to remove pigment and native moles, remove tattoos, and improve skin aging.
Consumer electronics
Ultrafast lasers are suitable for hard and brittle transparent material processing, thin film processing, and precision marking, as well as providing other functions within the manufacturing process of consumer electronics. Sapphire and tempered glass, such as that used in mobile phones, are considered hard, brittle, and transparent materials among the raw materials used in consumer electronics.
Sapphire in particular is widely used in items such as smart watches, mobile phone camera covers, and fingerprint module covers. However, due to its high levels of hardness and brittleness, the efficiency and yield rate of traditional machining methods are very low. Due to this, nanosecond ultraviolet lasers and ultrafast lasers are the main technical means for cutting sapphire, with the processing effect of the ultrafast laser being better than that of the ultraviolet nanosecond laser. In addition to the above functionalities, nanosecond and picosecond lasers are also the main processing methods used by camera modules and fingerprint modules.
Ultrafast lasers will also most likely become the mainstream technology for the cutting of flexible mobile phone screens (foldable screens) and the corresponding 3D glass drilling in the future.
Ultrafast lasers also have important applications in panel manufacturing, with uses including cutting OLED polarizers, and the peeling and repairing processes during LCD/OLED manufacturing.
The polymer materials in OLED manufacturing are particularly sensitive to thermal influences. Additionally, the size and spacing of the cells currently made are very small, as is the remaining processing size. This means that the traditional die-cutting process is no longer suitable. The production needs of the industry and the application requirements for special-shaped screens and perforated screens are now beyond the capabilities of traditional crafts. Thus, the benefits provided by ultrafast lasers are obvious, especially when considering picosecond ultraviolet or even femtosecond lasers, which have a small heat-affected zone and are more suitable for flexible applications such as curve processing.
Micro welding
For transparent solid media components, such as glass, various phenomena including non-linear absorption, melting damage, plasma formation, ablation, and fiber propagation will occur when an ultrashort pulse laser propagates in the medium. The figure shows the various phenomena that occur during an interaction between an ultrashort pulse laser and solid material when under different power densities and time scales.
Ultra-short pulse laser micro-welding technology is very well suited to the micro-welding of transparent materials such as glass since it does not need to insert an intermediate layer, has high efficiency, high precision, no macroscopic thermal effect, and presents ideal mechanical and optical properties following micro-welding treatment. For example, researchers have successfully welded end caps to standard and micro-structured optical fibers using 70 fs, 250 kHz pulses.
Display lighting
The application of ultrafast lasers in the field of display lighting mainly refers to the scribing and cutting of LED wafers, which is another example of how ultrafast lasers are suitable for processing hard and brittle materials. Ultrafast laser processing has good accuracy and efficiency, as well as high cross-section flatness and significantly reduced edge chipping.
Photovoltaic energy
Ultrafast lasers have broad application space in the manufacture of photovoltaic cells. For example, in the manufacture of CIGS thin-film batteries, ultrafast lasers can replace the original mechanical scribing process to significantly improve the quality of scribing, especially for P2 and P3 scribing links, where it can achieve almost no chipping, cracks, or residual stress.
Aerospace
Air film cooling technology is required when trying to improve engine performance and the performance and service life of the turbine blades used in aerospace. However, this means extremely high requirements for air film hole processing technology.
In 2018, the Xi’an Institute of Optics and Mechanics developed the highest single pulse energy in China: the 26-watt, industrial-grade femtosecond fiber laser. Additionally, they developed a series of extreme, ultra-fast, laser manufacturing equipment to achieve a breakthrough in the “cold processing” of air film holes in aero-engine turbine blades and thereby fill the domestic gap. This processing method is more advanced than EDM, its accuracy is higher, and the yield rate is greatly improved.
Ultrafast lasers can also be applied to the precision machining of fiber-reinforced composite materials, while improvements in machining accuracy will help expand the application of composite materials such as carbon fiber in aerospace and other high-end fields.
Research field
Two-photon polymerization (2PP) technology is a “nano-optical” 3D printing method similar to light-curing rapid prototyping technology. Futurist Christopher Barnatt believes that this technology may become a mainstream form of 3D printing in the future.
The principle of 2PP technology is to selectively cure photosensitive resin by using a “femtosecond pulse laser.” Although it seems similar to photocuring rapid prototyping, the difference is that the minimum layer thickness and X-Y axis resolution that 2PP technology can achieve are between 100 nm and 200 nm. In other words, 2PP 3D printing technology is hundreds of times more accurate than traditional light-curing molding technology and the printed things are smaller than bacteria.
The price of ultrafast lasers remains relatively expensive but as a pioneer in the industry, STYLECNC is already producing ultrafast laser processing equipment and has achieved good market feedback. Laser precision cutting equipment for OLED modules has been launched based on ultrafast laser technology, ultrafast (picosecond/femtosecond) laser marking equipment, glass chamfering laser processing equipment for picosecond infrared display screens, and picosecond infrared glass wafers.
The products launched thanks to these technologies include laser cutting equipment, LED automatic invisible dicing machines, semiconductor wafer laser cutting machines, glass cover cutting equipment for fingerprint identification modules, flexible display mass production lines, and a series of ultra-fast laser products.
Pros and cons of an ultrafast laser
Pros of an ultrafast laser
The ultrafast laser is one of the most important development directions within the laser field. As an emerging technology, it has significant advantages in precision micromachining.
The ultra-short pulse generated by the ultra-fast laser means that the laser itself only interacts with the material for a very short time and will therefore not bring heat to the surrounding materials. In addition, when the laser pulse width reaches the picosecond or femtosecond level, the influence on the molecular thermal motion can be largely avoided, resulting in less thermal influence. For this reason, ultra-fast laser processing is also called “cold processing.”
A graphic example that shows the advantages of a super-fast laser could be when we cut preserved eggs with a blunt kitchen knife. We often cut the preserved eggs into fine pieces, so if you choose a sharp knife edge that cuts quickly instead, the preserved eggs will be cut evenly and beautifully.
Cons of an ultrafast laser
High-end manufacturing industries, such as those making integrated circuits and panels, have extremely high requirements for laser processing equipment and there is a risk of new technological breakthroughs falling short of expectations.
The price of an ultra-fast laser is high and switching to a new laser supplier poses the risk of not being able to expand the market as was originally expected by both the laser equipment manufacturers and end-users.
Source from stylecnc.com
Disclaimer: The information set forth above is provided by stylecnc independently of Alibaba.com. Alibaba.com makes no representation and warranties as to the quality and reliability of the seller and products.