Table of Contents:
Do you know the difference between PA6 and PA66?
Filling and blending, how much do you know about PA6 and PA66 modification methods?
Do you know the difference between PA6 and PA66?
Polyamide resin, also known as nylon (Nylon), is a general term for polymers containing amide groups. It is one of the five major engineering plastics with the largest production volume, the widest variety, and the widest range of uses, and is widely used as a replacement for traditional materials such as metal and wood.
The two main varieties of nylon are nylon 6 (PA6) and nylon 66 (PA66), which occupy an absolutely dominant position in the nylon industry. So what is the essential difference between PA6 and PA66?
Firstly, there is a basic difference in physical properties. Nylon 6 is polycaprolactam, while nylon 66 is polyadipic acid adipic acid, so PA66 is 12% stiffer than PA6. Although PA6 has very similar chemical-physical properties to PA66, it has a lower melting point and a wide range of process temperatures. In addition, PA6 has better impact resistance and solubility resistance than PA66, but it is also more hygroscopic.
PA66 is a semi-crystalline material with a higher melting point, which maintains its strength and stiffness at higher temperatures.
The second difference is in product performance. PA6 has excellent thermal stability and heat resistance, good dimensional stability, high surface quality, and good anti-warping properties. PA66 has good abrasion resistance and high impact resistance, and its dimensional stability is also very good.
The last difference is in their usage. PA6 is generally used in automotive parts, mechanical parts, electronic and electrical products, and engineering accessories. PA66 is more widely used in the automotive industry, instrument shells, and products with high impact and high strength requirements, such as marine propellers, gears, rollers, pulleys, pumps impellers, fan blades, high-pressure sealing enclosures, valve seats, gaskets, bushings, a variety of handles, support frames, and wire packages, such as the inner layer.
Filling and blending, how much do you know about PA6 and PA66 modification methods?
PA6 and PA66 are common polyamide materials, also known as nylon. They have strong polarity and hydrogen bond forming ability and can react under certain conditions. These materials have excellent mechanical properties, abrasion resistance, oil resistance, self-lubrication resistance, as well as good moldability and corrosion resistance. However, due to the strong polarity of PA, it has high water absorption, which affects electrical properties and dimensional stability, and there is also a need to improve its heat resistance and low-temperature impact strength.
PA materials are easily modified and can be prepared into composites or alloys by fiber reinforcement, inorganic filling, and blending with other polyamides.
For filler modification, three methods can be used: fiber reinforcement, natural mineral reinforcement, and synthetic filler filling. Fiber reinforcement can use glass fibers, carbon fibers, and asbestos fibers. Natural mineral reinforcement can use calcium sulfate, calcium carbonate, kaolin, talc, and zeolite. Synthetic fillers such as molybdenum disulfide, graphite, silicone powder, and polytetrafluoroethylene can also be used. The simultaneous use of fiber and filler reinforced nylons usually results in a well-balanced product with a superior combination of properties.
The nature of the filler affects the properties of the resin. The shape, particle size, and surface area of the filler all have an effect on processing properties, mechanical properties, dimensional stability, and appearance quality.
Filler modification and application of PA66
For PA66 material, it is a commonly used polyamide material, also known as nylon 6-6. Similar to PA6, they are both polymers containing amide groups. PA66 has the largest production volume, the widest variety, and the widest range of applications among engineering plastics. It has excellent coloring ability and shrinkage control. In addition, it is resistant to many solvents, but less resistant to acids and some chlorinated agents. PA66 also has excellent flame retardant properties, and different levels of flame retardancy can be achieved by adding different flame retardants.
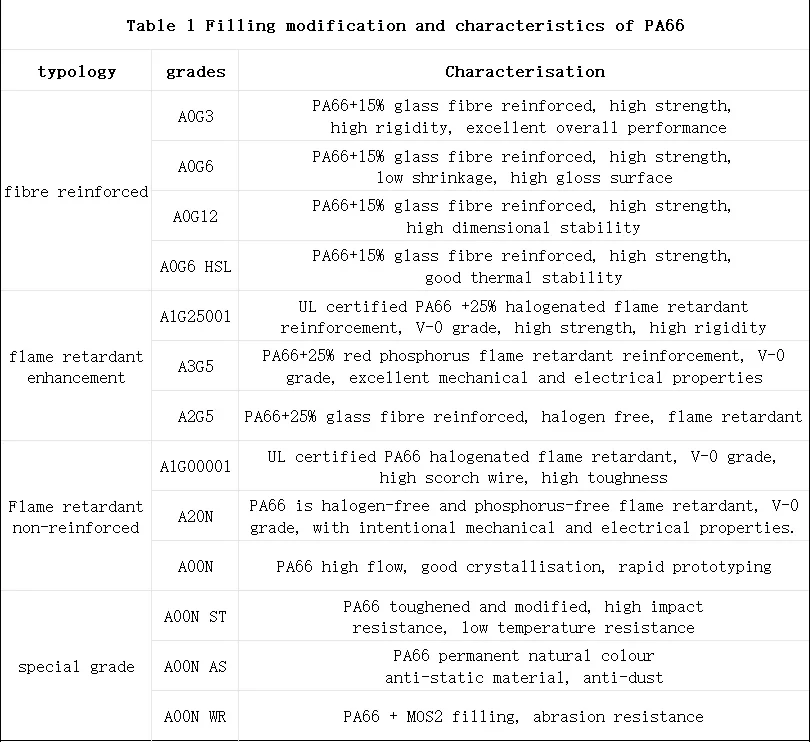
Modified PA66 is widely used in machinery, instrumentation, automotive parts, electrical and electronic equipment, railway industry, home appliances, communications, textile machinery, sports and leisure goods, fuel pipes, fuel tanks, and precision engineering products. Specifically, in the automotive field, PA66 is mainly used for cooling fans, door handles, fuel tank covers, air intake grilles, water tank covers, lamp bases, and other parts. In the field of electronic and electrical appliances, PA66 is often used in connectors, spools, timers, circuit breaker covers, switch housings, and other equipment. In the consumer and industrial fields, PA66 is commonly used in the manufacture of bicycle frames, skate bases, textile shuttles, pedals, pulleys, bearings, fan blades, and other products.
Filler modification and application of PA6
PA6 is a polyamide material, also known as nylon 6. It is a translucent or opaque crystalline polymer with a density ranging from 1.12 to 1.14 kg/m3. PA6 has the characteristics of strong thermoplasticity, light weight, good toughness, chemical resistance, and durability. It also has the following features:
Firstly, PA6 has high mechanical strength and good toughness, allowing it to withstand high tensile and compressive forces. Secondly, it has excellent fatigue resistance, maintaining its original mechanical strength even after repeated bending. In addition, PA6 has good corrosion resistance, making it resistant to alkaline solutions, most salt solutions, weak acids, oils, gasoline, aromatic hydrocarbons, and general solvents.
PA6 has a smooth surface, low coefficient of friction, and is resistant to wear. It is self-lubricating and produces low noise in moving mechanical components. For applications with moderate friction, lubricant may not be necessary. Additionally, PA6 is self-extinguishing, non-toxic, odorless, weather-resistant, inert to biological erosion, and has good antibacterial and anti-mold properties.
PA6 also exhibits excellent electrical properties, including good electrical insulation and high volume resistance. It can be used as an industrial frequency insulating material in dry environments and still maintain good electrical insulation properties even in high humidity environments.
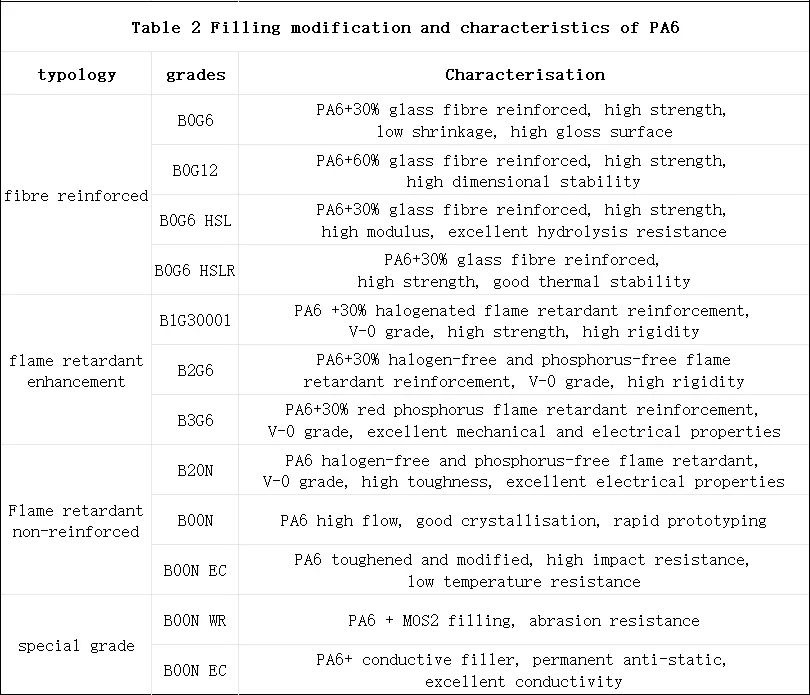
Modified PA6 has been widely used in automotive parts, mechanical parts, electronic and electrical products, engineering parts, and other fields. In the automotive field, PA6 is commonly used in radiator boxes, radiator blades, water tank covers, door handles, air intake grilles, and other parts. In the field of electronic and electrical appliances, PA6 is commonly used in coil frames, electronic connectors, electrical components, low-voltage electrical shells, terminals, and other parts. In the machinery industry, PA6 is commonly used in bearings, round gears, various rollers, oil-resistant sealing gaskets, oil-resistant containers, bearing cages, and other parts.
Blending modification refers to changing the properties of an already created polymer by adding other polymers to it. In blend modification, it is necessary to form an incompletely compatible multiphase system and achieve even dispersion between the two polymers to achieve the desired modification effect.
Blending PA with general-purpose plastic PE can improve the barrier properties of PE to oxygen, hydrocarbons, and other solvents. However, due to different molecular structures, the compatibility between PA and PE is poor. To enhance the interfacial interaction between HDPE and PA, Xu Xi et al. used UV radiation to introduce polar groups into the PE molecular chain, allowing it to chemically react with the amide or terminal amine groups on the PA molecular chain.
Blending PA with PP can improve coloration and air tightness. When blending different polymers, attention needs to be paid to their compatibility. When two polymers have poor compatibility, a third well-compatible component is often added as a bulking agent.
Nylon-6 and polypropylene are so poorly compatible that they cannot be uniformly blended using mechanical force alone. However, if a small amount of polypropylene grafted with maleic anhydride is added, the compatibility between nylon-6 and polypropylene can be greatly improved due to the chemical reaction between maleic anhydride and the amide groups of nylon-6.
Polyphenylene ether (PPO) is an excellent thermoplastic engineering plastic with good thermomechanical and physico-mechanical properties. However, it has drawbacks such as high melt viscosity, poor fluidity, difficult processing and molding, and high energy consumption, which limit its application. Blending modification is currently the most important method for improving the performance of PPO and expanding its application areas.
Although PPO/PS and PPO/HIPS alloys have excellent mechanical properties, their heat distortion temperature is low, and they have poor oil and solvent resistance. Therefore, the development of incompatible systems such as PPO/PA and PPO/PBT is necessary, with the key being to improve the compatibility between the polymers.
Nylon 6 and chitosan-silver/titanium dioxide composite antimicrobial agent were proportionally mixed, melted and co-mingled, cooled, pelletized, and dried using a conical twin-screw extruder to obtain antimicrobial modified PA6 pellets. These modified pellets have uniform size and good dispersion without obvious agglomeration, achieving the expected antimicrobial effect. Due to the doping effect of the composite antimicrobial agent, the structure of the modified pellets becomes more stable, the initial decomposition temperature increases, and the thermal stability improves.
Nylon antimicrobial fibers produced using the blended masterbatch method and the viscose method have wide antimicrobial spectra, strong and long-lasting antimicrobial effects. The manufacturing process is simple, and they can be produced using conventional spinning equipment. The physical properties of these fibers meet the requirements of conventional fibers, making them suitable for a wide range of applications.
Disclaimer: The information set forth above is provided by Shanghai Qishen Plastic Industry independently of Alibaba.com. Alibaba.com makes no representation and warranties as to the quality and reliability of the seller and products.