La versión totalmente eléctrica del MINI Countryman ya está saliendo de las líneas de producción de la planta de BMW Group en Leipzig, cuatro meses después del lanzamiento de producción del MINI Countryman con motor de combustión.
Tras abandonar la producción del BMW i3, la cuna de la movilidad eléctrica del Grupo BMW fabrica ahora cuatro modelos con tres tipos de propulsión de dos marcas, todos en una única línea de producción: el BMW Serie 1, el BMW Serie 2 Active Tourer (incluido versión híbrida enchufable), el BMW Serie 2 Gran Coupé y el MINI Countryman tanto en su versión totalmente eléctrica como en su versión de combustión.
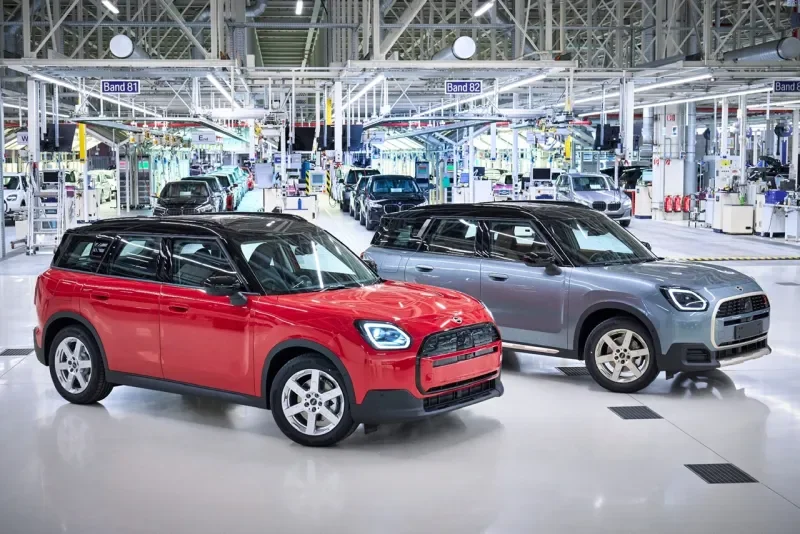
El MINI Countryman Electric representa un paso importante en la transición de la marca MINI hacia la electrificación total para 2030 y combina una sensación de kart electrificado con movilidad con cero emisiones locales. Viene en dos variantes totalmente eléctricas: el Countryman E (150 kW, 204 CV | consumo eléctrico 17.4 – 15.7 kWh/100 km) y el Countryman SE ALL4 con tracción total más potente (230 kW, 313 CV | consumo eléctrico 18.5 – 16.8 kWh/100 kilómetros).
Para permitir una producción de hasta 350,000 unidades al año (100,000 más que antes), la planta de Leipzig se ha mejorado continuamente desde 2018, con importantes ampliaciones y mejoras en el taller de carrocería, pintura, montaje y logística.
En los últimos años, BMW Group ha invertido alrededor de 1.6 millones de euros en la planta de Leipzig para producir vehículos y componentes eléctricos adicionales y ahora también estamos aumentando el volumen de vehículos, lo cual es una gran noticia para nuestra planta.
—Petra Peterhänsel, directora de planta
El principal impulsor del aumento de volumen es el MINI Countryman. En el transcurso de 2024, la producción aumentará a casi 500 unidades por día, además de los aproximadamente 800 vehículos BMW que produce la planta. Con su sistema de producción flexible, la planta de Leipzig está en condiciones de responder rápidamente a las demandas de los clientes, por ejemplo aumentando la proporción de vehículos totalmente eléctricos.
Las estructuras de montaje flexibles también permitieron que el MINI Countryman Electric pudiera integrarse sin problemas en la producción. La situación es similar con las diferentes unidades motrices, que se producen en una misma línea en conjunto y preparadas para unirse con la carrocería.
Los propulsores eléctricos, las transmisiones y la electrónica de control (conocidos colectivamente como topología de propulsión eléctrica altamente integrada, o HEAT) de los dos modelos totalmente eléctricos están conectados directamente en la planta. Sólo se necesitaba una nueva línea de producción para la electrónica de control.
A finales de 2024, la planta de Leipzig empleará a unos 7,000 empleados de BMW. Será necesario ajustar los horarios de trabajo en todas las tecnologías: en septiembre de este año comenzarán por primera vez los turnos de noche en el montaje y los automóviles se producirán las XNUMX horas del día en tres turnos.
Con el lanzamiento de la producción del MINI Countryman Electric, las tres etapas del proceso de producción de baterías de alto voltaje Gen 5 ahora están representadas en la planta de BMW Group en Leipzig: revestimiento de celdas, producción de módulos y ensamblaje de baterías. Las operaciones en los tres se están intensificando actualmente, con cinco líneas de revestimiento de celdas, tres de producción de módulos y dos de producción de baterías de alto voltaje.
Estamos en medio de la transformación hacia la movilidad eléctrica. A partir de este año, la planta de Leipzig llevará a cabo cada etapa de nuestro proceso interno de producción de baterías de alto voltaje. Es nuestro próximo gran paso adelante.
—Markus Fallböhmer, jefe de producción de baterías de BMW Group
La capacidad de producción de componentes electrónicos de la planta de Leipzig ha ido aumentando desde 2021. Ahora fabricará no solo las baterías de alto voltaje para el MINI Countryman Electric, sino también componentes eléctricos para el BMW iX1, BMW iX2, BMW i4, BMW i5 y BMW iX. realizados en otros sitios. La unidad de producción de componentes electrónicos de Leipzig emplea actualmente a unas 1,000 personas.
Para permitir la producción de baterías de alto voltaje, se han reformado los espacios utilizados anteriormente para el BMW i3 y el BMW i8 y se han añadido nuevos edificios. Uno de ellos es una nueva nave con una superficie de unos 61,000 m2. Este alberga dos líneas capaces de producir hasta 300,000 baterías de alto voltaje al año. Hasta la fecha, BMW Group ha invertido más de 900 millones de euros en la producción de componentes eléctricos en la planta de Leipzig.
Procesos de pintura que ahorran recursos. En el lanzamiento, el MINI Countryman totalmente eléctrico viene en tres colores de carrocería adicionales: British Racing Green, Chili Red y Blazing Blue, y con el techo de contraste característico de MINI, si se desea. Esto se pinta utilizando un nuevo método sin exceso de pulverización que ahorra recursos y actualmente se está preparando para su funcionamiento en serie.
El término "overspray" se refiere a la niebla de exceso de partículas de pintura que se forma cuando las carrocerías se pintan de forma convencional. Con la nueva técnica, esta niebla ya no se produce. Esto hace que sea más fácil pintar en varios colores, ya que ya no es necesario el laborioso proceso de enmascarar. Pintar sin exceso de pulverización también ayuda a ahorrar CO2 emisiones, ya que los gases de escape de la cabina requieren menos limpieza. Además, requiere considerablemente menos aire acondicionado, es decir, aire que alcanza la temperatura y humedad exactas necesarias para pintar. Como resultado, se necesita menos energía para templar el aire y tratar los gases de escape.
La tecnología de quemadores utilizada para secar la pintura en los techos contrastantes también se modificó al inicio de la producción del MINI Countryman y ahora consiste en un sistema bivalente. Los quemadores de combustible flexible pueden funcionar tanto con hidrógeno como con gas (metano) e incluso alternar entre ambos mientras están en funcionamiento. Para fabricar los techos contrastantes del MINI Countryman se utilizan cinco de estos quemadores bivalentes con capacidad de hidrógeno.
Otros quemadores del taller de pintura también pasarán gradualmente al funcionamiento bivalente y ya se acaban de instalar los siguientes seis quemadores con capacidad de hidrógeno. Esto convierte a Leipzig en pionera en la industria del automóvil y la acerca cada vez más a reducir las emisiones de CO2 las emisiones.
Nuestra visión en la Planta de Leipzig es descarbonizar la producción en la medida de lo posible sustituyendo los combustibles fósiles por hidrógeno verde.
—Petra Peterhansel
Esto requerirá suficiente hidrógeno verde de una red. Actualmente se está planificando una red regional de hidrógeno, de la que se beneficiará la planta de Leipzig.
Fuente de Congreso de coches ecológicos
Descargo de responsabilidad: La información establecida anteriormente es proporcionada por greencarcongress.com independientemente de Alibaba.com. Alibaba.com no representa ni garantiza la calidad y confiabilidad del vendedor y los productos.