Una mirada a las tendencias actuales y los problemas de la cadena de suministro para el sector automotriz
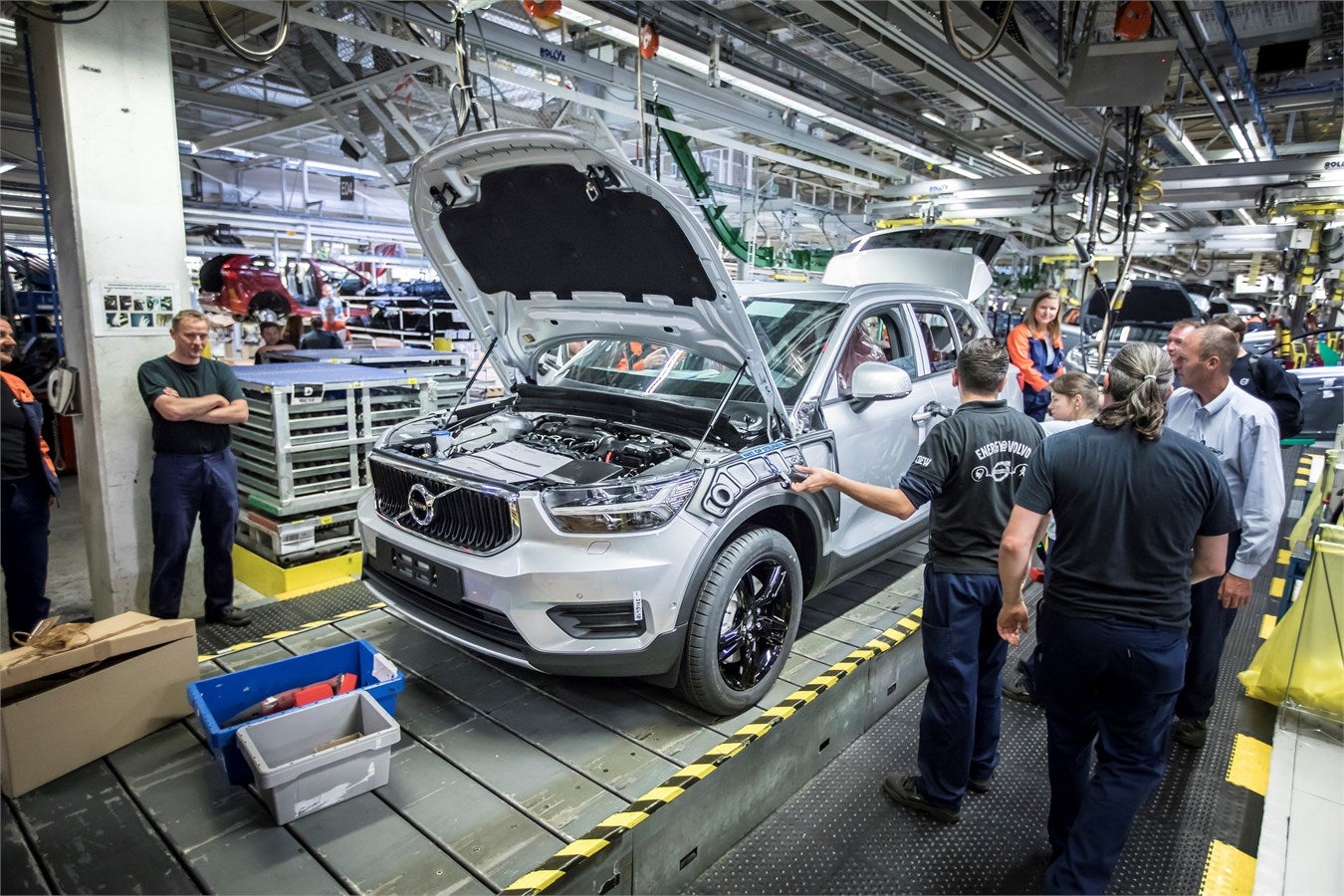
Un vehículo de motor típico puede contener entre 15,000 y 25,000 componentes, dependiendo de cómo se midan y de la ingeniería de diseño de sus sistemas principales. Es mucho material para reunir y proporcionar integridad al producto final. De hecho, no es tarea fácil reunir todas esas piezas en el orden correcto. Cada automóvil que existe es un tributo a la planificación de procesos, la organización, la ingeniería de producción y la logística de fabricación. Érase una vez, los fabricantes de vehículos estaban altamente integrados verticalmente, pero ese enfoque dio paso a proveedores de piezas desinvertidas (¿alguien recuerda de dónde vino Visteon y la maraña de empresas que componían el Grupo de Componentes Automotrices de General Motors?) y especialistas que podían centrarse en desarrollar productos y operar de manera más eficiente a mayor escala para más de un cliente.
Los grandes integradores de sistemas de nivel 1 suministran directamente a los fabricantes de vehículos, a menudo desde parques de proveedores convenientemente ubicados cerca de las instalaciones de ensamblaje y fabricación de vehículos, pero hay múltiples niveles de proveedores más pequeños por debajo del nivel superior, cada uno de los cuales desempeña funciones vitales en el largo camino desde la materia prima. materiales hasta el producto terminado.
El abastecimiento internacional de componentes se ha convertido en un modo de operación estándar de la industria durante muchas décadas, a medida que los OEM y los proveedores más grandes han buscado comparar precios en el mercado global en busca de piezas e insumos de materiales que cumplan con los umbrales de calidad necesarios al menor costo. Las distancias (y los costos) del transporte y los arreglos para el almacenamiento también son parte del panorama, pero las mayores eficiencias y los avances tecnológicos en el transporte internacional de carga han apuntalado un crecimiento fenomenal en los envíos internacionales de piezas.
El crecimiento de la industria automotriz china durante las últimas dos décadas también ha sido un factor importante en el abastecimiento global de componentes automotrices, especialmente lo que podrían denominarse piezas universales o mercantilizadas que se venden principalmente a precio de costo. Los proveedores chinos se han beneficiado de grandes contratos locales que impulsan las economías de escala, así como de subsidios ocultos que surgen de complejas estructuras de propiedad que involucran a matrices OEM, empresas estatales y participaciones diversificadas. A principios de la década de 2000, los fabricantes de vehículos estadounidenses, en particular, optaron por obtener más repuestos de bajo costo en Asia, lo que debilitó a algunas empresas establecidas desde hacía mucho tiempo en la base de proveedores estadounidenses.
En todo el mundo, los flujos comerciales internacionales de productos automotrices (tanto vehículos terminados como componentes) son ahora enormes. Estimaciones compiladas por GlobalData Alemania es, con diferencia, el líder mundial en exportaciones de productos de la industria automovilística. Esas exportaciones se reflejan en las importaciones y en una maraña de bienes intermedios que se utilizan como insumos para sistemas de componentes que se refinan y diseñan en diferentes etapas del proceso de fabricación y que pueden enviarse a través de fronteras internacionales varias veces.
Otra característica estructural importante de las cadenas de suministro en la industria automotriz es la importancia de una filosofía de gestión de la cadena de suministro que minimice los costos de inventario y mejore la eficiencia de los procesos y los circuitos de comunicación de retroalimentación para mejorar los estándares de calidad. Conocida como "fabricación ajustada", comenzó con Toyota y su esencia se resume en el término "justo a tiempo" para describir los métodos y principios de suministro ajustado. El auge de las tecnologías digitales y conectadas que reúnen todas las partes del proceso de fabricación y venta minorista ha apuntalado aún más estas formas de trabajar durante la última década.
En el pasado, los desastres naturales y sus impactos concentrados en ubicaciones afectaron a las empresas automotrices e ilustraron la fragilidad de las cadenas de suministro automotrices. Después del terremoto y tsunami de 2011 en Japón, hubo varios ejemplos notables de perturbaciones. Un fabricante mundial de automóviles premium tuvo problemas en términos de suministro de un pigmento de pintura roja de origen japonés. Las inundaciones en Tailandia de ese mismo año provocaron una escasez de suministro de pantallas LCD para mostrar información de vehículos. Los fabricantes de equipos originales y los distribuidores tuvieron que adaptarse a la escasez en consecuencia. La guerra en Ucrania ilustra cómo acontecimientos geopolíticos inesperados también pueden alterar las cadenas de suministro.
El desafío de los semiconductores
Todas las empresas se vieron afectadas negativamente directamente por la crisis de salud pública de 2020 e indirectamente por muchos más efectos en las cadenas de suministro globales. Además, la recuperación de las ventas mundiales en 2021 se vio gravemente perjudicada por una consecuencia imprevista de la crisis de Covid un año antes. Cuando los fabricantes de vehículos cerraron fábricas por orden del gobierno y redujeron drásticamente los pedidos de piezas en 2020, los fabricantes de semiconductores encontraron negocios alternativos en áreas como la electrónica de consumo.
Cuando las plantas automotrices en recuperación aumentaron sus pedidos de chips en el primer trimestre de 2021, rápidamente se hizo evidente un problema de escasez de suministro.
La escasez de semiconductores tampoco se iba a superar fácilmente debido a los largos plazos para agregar capacidad de fundición de chips en las fases iniciales. Una pieza ausente que es crítica para la seguridad o que de alguna otra manera se considera necesaria para el producto terminado significó que algunas líneas de modelos se vieron más afectadas que otras. Los fabricantes de vehículos podían cambiar la combinación de mercado en algunos casos, pero un viejo dicho se estaba volviendo realidad nuevamente: las cadenas de suministro son tan buenas y robustas como su punto más débil.
En toda la industria, los métodos y procesos de adquisición están siendo objeto de escrutinio como nunca antes.
Vale la pena señalar también que hay un elemento estructural en juego que significa que algunas presiones en el suministro de semiconductores probablemente sigan siendo un riesgo en el futuro: el contenido de electrónica avanzada de los vehículos está aumentando debido a la instalación cada vez mayor de características tecnológicas más sofisticadas. Esto está haciendo que algunas empresas opten por alianzas estratégicas con fabricantes de chips. Esto no sólo puede ayudar a asegurar el suministro futuro de microprocesadores críticos, sino que también puede facilitar futuras relaciones colaborativas beneficiosas para el desarrollo de productos en lo que se está volviendo obvio es un área de componentes estratégicamente valiosa.
Otras presiones sobre las cadenas de suministro provienen de otras fuentes, como la escasez imprevista de mano de obra y los precios mucho más altos de los envíos internacionales de contenedores a medida que los precios de la energía se han disparado.
El debate entre fuentes duales y múltiples
La fragilidad de las cadenas de suministro automotrices viene acompañada de la prevalencia de múltiples niveles, flujos de abastecimiento internacionales y una tendencia a un abastecimiento único para maximizar las economías de escala en todos los programas globales de vehículos. En muchos casos, esta estructura tradicional también está integrada y arraigada en una cultura de socios preferidos en todos los niveles de suministro. Las ventajas también pueden incluir sistemas compartidos y costos de logística, con costos repartidos entre volúmenes en otros modelos y sistemas también.
La tecnología también ha desempeñado un papel en el fomento del abastecimiento único, ya que las empresas (incluidas las de los niveles 3 y 4) generalmente han podido centralizar la experiencia y la inversión en una instalación dedicada a la fabricación de alto volumen. Los problemas surgen cuando algo sale mal y echa por tierra los planes (el incendio de una planta de microprocesadores de Renesas el año pasado, por ejemplo).
La electrónica y los sensores son ejemplos de componentes críticos para subconjuntos que pueden tener grandes implicaciones en la fase posterior de la fabricación de vehículos si se produce alguna interrupción en la fase anterior. Encontrar proveedores alternativos con capacidad excedente en muy poco tiempo es un gran desafío.
Mantener algunas reservas de piezas en stock tiene un coste y va en contra de los principios rectores de la fabricación ajustada. Por supuesto, se puede tomar la decisión de absorber o cancelar cualquier costo de interrupción atípico a medida que ocurra; en última instancia, depende de la cuantificación de la evaluación de riesgos.
La experiencia de los últimos años al menos indica que las empresas se preguntan cada vez más si el abastecimiento único es tan deseable como lo fue antes. Un mundo acosado por mayores riesgos e incertidumbres tal vez exija un cambio de enfoque. La duplicación dentro de la cadena de suministro, incluso si significa acercarse a compartir con un competidor, puede ofrecer una mejor solución –al menos para algunos componentes– que el abastecimiento único. Una mayor seguridad del producto sería el beneficio del abastecimiento dual. Como siempre, es una cuestión de costo total.
Electrificación y nuevos patrones de cadena de suministro
La electrificación trae nuevos desafíos a las futuras cadenas de suministro en el sector automotriz. Los fabricantes de equipos originales se han enfrentado a considerables incertidumbres sobre el suministro de componentes nuevos y clave –en particular, las baterías del tren motriz– que están tratando de resolver. También existen cuestiones estratégicas sobre el grado de integración vertical que es deseable para mitigar riesgos futuros y ejercer control sobre los aspectos comerciales de los acuerdos de suministro. Se han creado empresas conjuntas con especialistas en baterías. Otros componentes clave para los vehículos eléctricos, como motores, piezas del sistema de propulsión, inversores de alto voltaje, también estarán sujetos a una inversión cada vez mayor junto con consideraciones de la cadena de suministro.
Las ambiciosas estrategias de electrificación harán que la demanda de celdas de baterías de iones de litio se dispare. Los productores de baterías de todo el mundo se están comprometiendo a estrategias de expansión multimillonarias, abriendo nuevas "gigafábricas" para suministrar celdas a los fabricantes de automóviles.
Un ejemplo notable de profunda colaboración OEM-Tier 1 en esta área es la firma de un MoU entre Volkswagen y Bosch. Las dos empresas planean suministrar sistemas integrados de producción de baterías, aceleración in situ y soporte de mantenimiento para fabricantes de celdas y sistemas de baterías. Dicen que su objetivo es alcanzar el liderazgo en costes y tecnología en la tecnología de baterías a escala industrial y la producción en volumen de "baterías sostenibles y de vanguardia".
Sólo en Europa, el Grupo Volkswagen planea construir seis fábricas de celdas para 2030 y otros fabricantes están tomando medidas similares para asegurar el suministro futuro de celdas y paquetes de baterías. La región debería tener una capacidad total anual de baterías de alrededor de 700 gigavatios hora para 2030.
Mirando hacia arriba, Toyota ha formado una empresa conjunta con Panasonic (Prime Planet Energy & Solutions – PPES) que ha firmado un acuerdo con el gigante minero BHP para el futuro suministro de sulfato de níquel, la base del níquel presente en el cátodo de la mayoría de los iones de litio. celdas de batería. Tesla también firmó un acuerdo similar con BHP, lo que ilustra que las materias primas también están muy presentes para la futura seguridad del suministro.
Estos acuerdos resaltan la necesidad de que los actores automotrices miren más arriba en la cadena de suministro de baterías, para garantizar que tengan acceso a suficientes materias primas para abastecer el enorme crecimiento de capacidad necesario dentro del sector de baterías de iones de litio para la nueva ola de vehículos eléctricos de batería que se lanzará en el próximos años. El reciclaje también es una consideración clave en muchos de los acuerdos que se han cerrado.
Blockchain para visibilidad de la cadena de suministro
Cada vez más, las empresas automotrices utilizan la tecnología blockchain para ganar transparencia en cuestiones de la cadena de suministro, como las emisiones de CO2 y la fuente de cobalto para las baterías (lo que puede plantear cuestiones éticas en torno a la extracción de minerales preciosos).
El concepto original de blockchain, como sugiere el nombre, es una cadena de bloques o registros con marca de tiempo (bloque = información digital; cadena = la base de datos pública/comunitaria). Los bloques almacenan información sobre transacciones. Cuando un bloque almacena nuevos datos (una transacción), se agrega a la cadena de bloques y, una vez verificado por una red de computadoras de igual a igual, cualquiera puede verlo (o puede estar sujeto al permiso de una red privada como la cadena de suministro de un OEM (el 'libro mayor distribuido').
Sin embargo, todas las partes sólo tienen acceso a la información para la que tienen permiso de ver. Cada computadora en la red blockchain tiene su propia copia de blockchain. Sin embargo, en principio, la idea es crear un sistema altamente transparente con cero costos de transacción entre las dos partes creando un bloque.
Podemos esperar ver más empresas automotrices adoptando procesos blockchain – especialmente del tipo de libro mayor distribuido (es decir, red privada) – como un medio para mitigar el riesgo de "rupturas" en la cadena de suministro y comprender las fortalezas y debilidades a lo largo de la cadena, pero también como una manera de demostrar las crecientes demandas de cumplimiento en áreas regulatorias como la sostenibilidad.
Lecciones de Toyota
En general, se considera que Toyota es uno de los que tiene mejor desempeño en la industria automotriz en lo que respecta a la gestión de la cadena de suministro. Además de ser el creador de los métodos de fabricación ajustada que luego se convirtieron en las mejores prácticas generalizadas adoptadas por la mayoría de los OEM y los principales proveedores, también ha perfeccionado sus sistemas y procesos de acuerdo con las circunstancias cambiantes con respecto a las medidas de mitigación de riesgos. Además, en ocasiones ha trabajado muy estrechamente con sus proveedores y en aras de objetivos sectoriales más amplios ante emergencias.
Después del terremoto y tsunami de Kioto de 2011, Toyota trabajó junto con proveedores en Japón para producir una base de datos integral de información sobre la cadena de suministro para apoyar al sector manufacturero de Japón. Toyota también introdujo una estrategia para el abastecimiento múltiple de piezas clave, lo que significaría organizar el suministro de tres fuentes diferentes, pero con el proveedor principal preparado para realizar casi dos tercios del pedido para garantizar economías de escala. Múltiples proveedores comprometen las economías de escala, pero también significa que existen alternativas si es necesario.
Toyota también cuenta con un sistema bien desarrollado para monitorear su vasta red de proveedores y un sistema de alerta temprana en caso de escasez. De hecho, algunas empresas están recurriendo a la IA para evaluar la evolución de sus cadenas de suministro, aunque para ello se requiere, en primer lugar, poseer una base de datos confiable, extensa y detallada.
Otra opción para las empresas es embarcarse en el mantenimiento de existencias de emergencia o de reserva de piezas clave, en particular aquellas que pueden provocar la parada de una línea de producción. Una vez más, implica un costo adicional en almacenamiento o almacenamiento, pero es una cuestión de decidir qué nivel de costo o "prima de seguro" vale la pena pagar. Además, no será una solución permanente. Es posible que Toyota haya almacenado algunos semiconductores, pero la gravedad de la escasez mundial de chips significó que, finalmente, también se vio obligada a recortar la producción. Quizás el aprendizaje más significativo de Toyota es la necesidad de revisión constante y adaptabilidad a circunstancias e incertidumbres cambiantes.
Fuente de Solo coche
Descargo de responsabilidad: La información establecida anteriormente es proporcionada por just-auto.com independientemente de Alibaba.com. Alibaba.com no representa ni garantiza la calidad y confiabilidad del vendedor y los productos.