Interested in learning about the fundamentals of FDM 3D printing? This article explores the underlying principles of FDM technology and explains why it is a viable and cost-effective option for rapid prototyping. Keep reading to gain insights about the latest 3-dimensional printing technology in order to make an informed decision when looking at 3D printing options.
Table of Contents
The growing FDM 3D printing market
A comprehensive understanding of FDM 3D printing technology
Advantages and disadvantages of the FDM 3D printing method
Applications of FDM 3D printing
The growing FDM 3D printing market
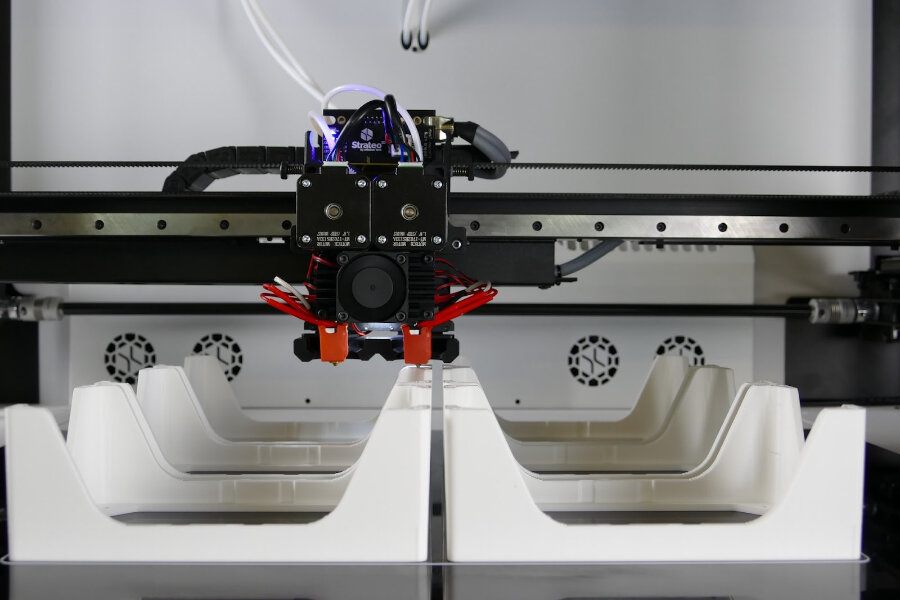
The global 3D printing market was worth US $13.84 billion in 2021 and is projected to grow at a compound annual growth rate (CAGR) of 20.8% between 2020 and 2030. The market has grown due to significant investment in R&D in 3D printing and rising demand for prototyping applications in the automotive, healthcare, and defense industries.
FDM 3D printing has grown in popularity in recent years due to its high performance at a lower cost, saving businesses up to 50% on their tooling process. Other benefits include rapid prototyping, on-demand printing, design flexibility, minimal waste, and so on.
Continue reading to learn about the fundamentals of FDM 3D technology, its characteristics, and its advantages over other printing methods.
A comprehensive understanding of FDM 3D printing technology
What is FDM technology for 3D printing?
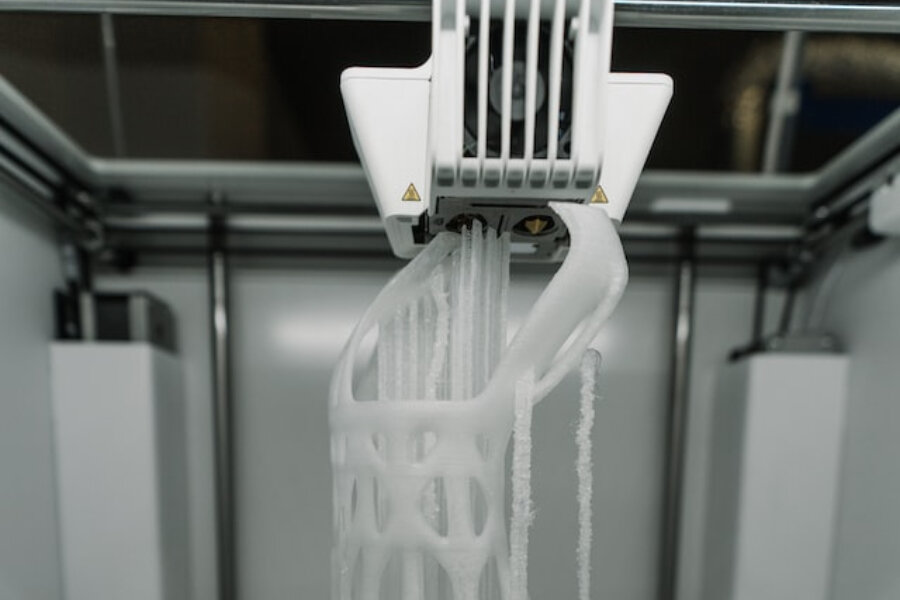
Fused deposition modeling (FDM) is an additive manufacturing technique that involves extruding materials through a nozzle and fusing them to produce three-dimensional objects. Compared to concrete and food 3D printing, the standard FDM process differs from other material extrusion techniques. It uses thermoplastics as feedstock materials, usually in the form of filaments or pellets.
Typically, an FDM 3D printer melts materials by pushing polymer-based filament through a heated nozzle; the materials are then deposited on the build platform in 2D layers. These layers eventually fuse to form 3D parts.
Overall, an FDM printer is the fastest way to 3D printing and is accessible and efficient. These printers dominate the 3D printing market because they are easier to use than resin 3D printers and less expensive than powder-based counterparts such as SLS.
When was FDM technology introduced?
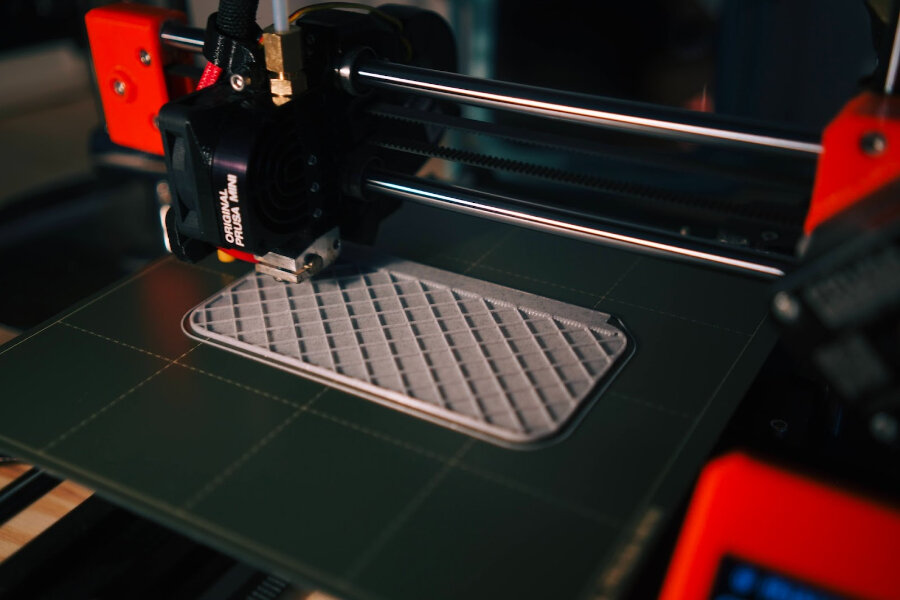
Although FDM is currently the most widely used 3D printing technique, it wasn’t the first 3D technique to be created. A few years after the patents for stereolithography (SLA) and selective laser sintering (SLS) were filed, Scott Crump submitted the first FDM patent in 1989.
The FDM technology was only popular among non-commercial users, such as academicians at the University of Bath, who were primarily interested in creating self-replicating devices. The FDM patent, however, expired in 2009, and the individuals who pioneered this technology founded MakerBot Industries to commercialize 3D printers.
How does FDM 3D printing work?
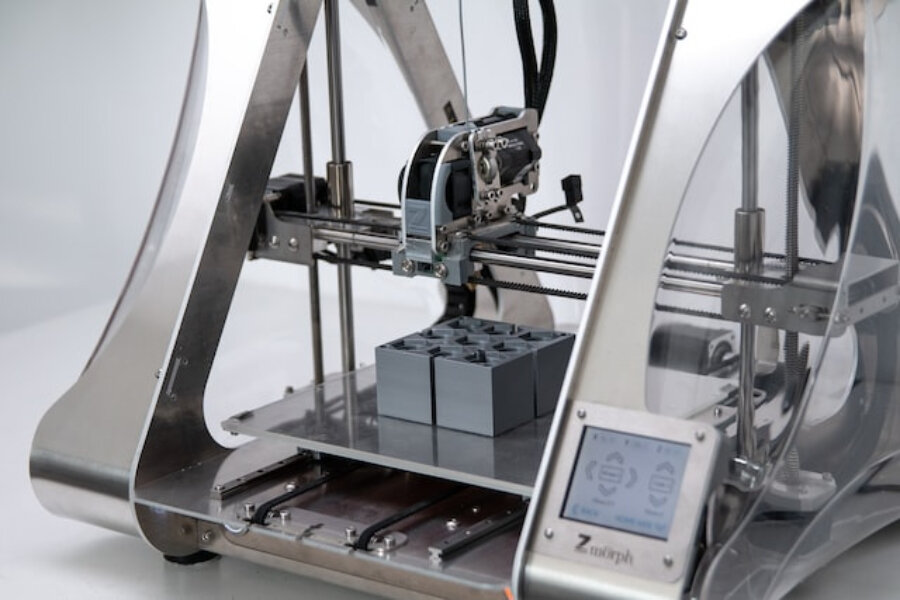
An FDM 3D printer creates objects by depositing melted filament materials over a build platform layer by layer until you have a complete part. They utilize the digital design files uploaded to the machine to get the physical dimensions. These printers use polymers such as PLA, ABS, PEI, and PETG, which are transferred as threads through a heated nozzle.
A spool of thermoplastic filament is loaded into the printer to get the printer started. Once the nozzle attains the desired temperature, the filament passes through an extrusion head and nozzle.
This extrusion head is linked to a three-axis system and can move along the X, Y, and Z axes. The machine then extrudes melted material in thin stands, deposited layer by layer into the predetermined design. Eventually, the material cools and solidifies.
It takes several passes to finish a project. The build platform descends, and the printer begins working on the next layer after finishing the previous layer. In some machines, the extrusion head moves up and down until the piece is completed.
What are the features of FDM 3D printing?
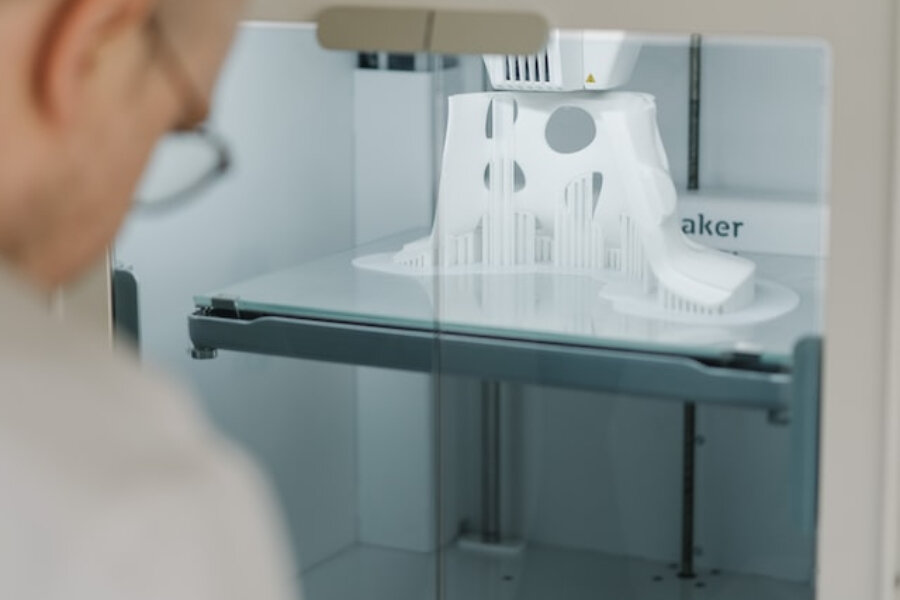
Although FDM 3D printers differ in terms of the part quality and their extrusion systems depending on the brand and model, a few characteristics are consistent across every FDM printer.
1. Build speed and temperature
Almost all FDM systems allow users to change the temperature, build speed, cooling fan speed, and layer height as needed. These are typically determined by the printing service provider and vary depending on the material.
2. Build volume
Build volume refers to the size of the part that the printer can create. A DIY 3D printer typically has a build volume of 200 x 200 mm, whereas an industrial machine can have a build volume of 1000 x 1000 x 1000 mm. Users must consider the printer’s build volume and their proposed design before making a purchase. Large models can, however, also be printed in smaller chunks.
3. Layer adhesion
In FDM printing, tight adhesion between the deposited layers of a part is essential. The previously printed layer is fused with molten thermoplastic that the printer extrudes through the nozzle. This layer remelts under high pressure and temperature, allowing it to bond with the prior layer.
Additionally, the shape of the molten material changes to an oval as it presses against the previously printed layer. No matter what layer height is used, the FDM parts always have a wavy surface, and small features like threads or small holes might need post-processing.
4. Layer height
In an FDM machine, the layer height can be between 0.02 mm and 0.4 mm. Smoother parts are produced, and curved geometrics are accurately captured with lower layer heights. On the other hand, printing parts with a higher layer height is quicker and less expensive. A layer height of 0.2 mm is typically a good balance between time, cost, and quality.
5. Infill and shell thickness
FDM printers typically do not produce solid parts to expedite print time and waste materials. Instead, the printer traces the shell’s outer perimeter several times before filling the interior, known as the infill, with an internal, low-density structure.
The strength of the printed parts is determined by the infill and shell thickness. Most desktop FDM printers have a default infill density of 20% and a shell thickness of 1 mm. This results in a perfect balance of strength and speed for quick prints.
6. Warping
Warping is one of the most prevalent FDM flaws- when extruded materials solidify, it shrinks in size. Furthermore, different sections of the printed part cool at varying rates, and their dimensions also change at different speeds. Due to the internal stress buildup brought on by this differential cooling, the underlying layer moves upward and warps.
There are, however, various methods for preventing warping. One approach is to closely monitor the temperature of the system, particularly the build platform and chamber. The second step is to improve adhesion between the build platform and the part.
Advantages and disadvantages of the FDM 3D printing method
Advantages
Performance
- Unlike other methods like resin 3D printers, FDM printers can be scaled easily to any size, with the only restriction being the movement of each gantry.
- Regarding printing materials, FDM filaments are affordable, especially compared to the materials required for other methods, such as SLS and resin printing.
- Compared to their rivals, FDM printers are more flexible. With only a few improvements and modifications, they can print a wide range of thermoplastic materials, which is not possible with other methods where the material must be resin or a fine powder.
Print quality
- The FDM printer is flexible and can accommodate different FDM materials. It can create parts with varying properties and appearances simply by changing the filament type.
- Print quality refers not only to appearance but also to its mechanical performance. Compared to fragile resin 3D prints, FDM produces solid and durable parts.
- FDM printers are also versatile in that print quality can be sacrificed for speed and dexterity, making them an ideal tool for creating both aesthetically pleasing and functional parts.
Disadvantages
- FDM 3D printing is best suited for the production of small-sized parts, but the finished products are likely to have rough surfaces and need post-processing to have a smoother finish.
- Because FDM printers place the filaments layer by layer, they are prone to breakage, causing the prints to be anisotropic.
- FDM printing requires the use of support structures, which can raise costs.
Applications of FDM 3D printing
Architectural modeling: 3D printers are widely used to create architectural models because they are faster and relatively cheaper than conventional methods. One roll of filament can produce three to four models, saving costs.
Automotive manufacturing: 3D printing is commonly used to design the car’s internal structure. Users can create precise measurements for automobile manufacturing using 3D software.
Surgical models: the FDM 3D technology has enabled doctors to better plan surgeries by providing them with organs that are a replica of the patient. They have a precise structure, can be made solid or hollow, and can be printed in hours.