Metal casting machinery is essential for any industry that produces metals to be used by consumers across various sectors. The equipment can change the form and shape of various metals to the required specification.
However, many businesses struggle with choosing metal casting equipment. For this reason, the article below will provide selection tips so businesses can have an easy time making their choices.
Table of Contents
Metal casting market overview
4 selection tips for metal casting machines
Types of metal casting machines
Conclusion
Metal casting market overview
Allied Market Research estimated the global market for metal casting machines to be worth $129.5 billion in 2021. The market is expected to grow and reach a valuation of $226.8 billion by 2031 at a CAGR rate of 5.8% from 2022 to 2031.
The vast market size comes from the massive industry reliance on machines. The industries depending on metal casting machines for their processes include building and construction, aerospace, automotive, electronics, heavy machinery, and marine sectors.
4 selection tips for metal casting machines
Casting needs
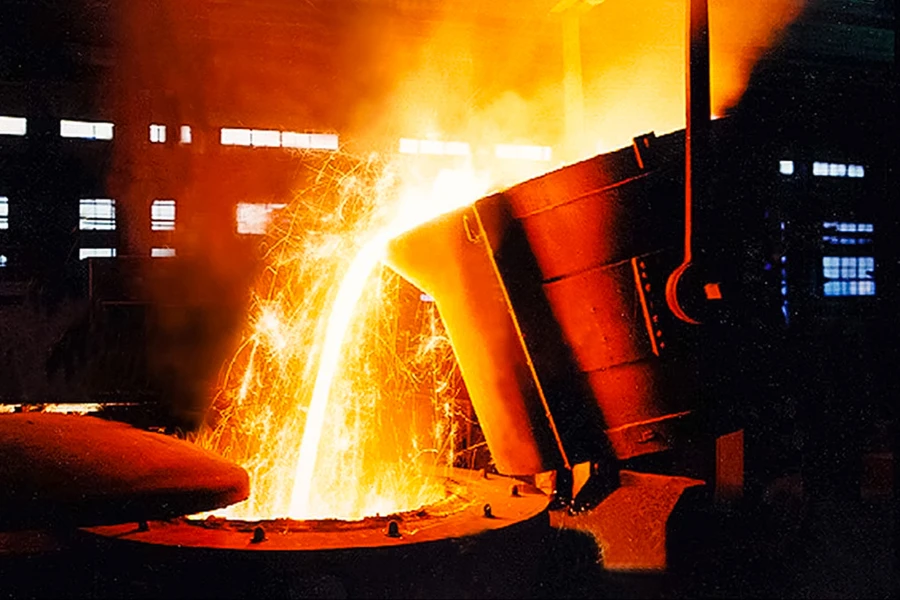
Manufacturers should consider their metal casting needs when buying machinery. Machinery shopping may depend on the type of casting process as well as the production volume.
When it comes to the casting process, various types of casting techniques are used to manufacture metal components, such as die casting, investment casting, sand casting, and centrifugal casting. There is equipment to suit each casting process appropriately.
In terms of production volume, businesses producing a large bulk of parts should consider choosing powerful machinery to keep up with the demand. A smaller casting machine works well when dealing with the production of smaller pieces in smaller quantities.
Machine capabilities and limitations
The extent of work the metal casting machine can do and the limits it can push are essential to consider. Metal casting is a versatile process that businesses can use to create a wide range of parts, from intricate jewelry components to large automotive parts.
Businesses can pick metal casting equipment depending on the size and weight of components. Moreover, they should choose machinery based on production volume.
Material being cast
When choosing metal casting machinery, the type of material being cast is an important consideration to keep in mind. Different casting equipment is used for different kinds of metals.
Metal casting machinery for iron differs from machinery for metals like aluminum, steel, or copper. Therefore, businesses should get machinery suitable for the material they want to cast.
Cost and efficiency of the machinery
Businesses should choose metal casting machinery based on cost-effectiveness and efficiency. The materials used to make the machinery as well as the casting process should be conscious of the environment.
The cost of the machinery should be fair. Moreover, businesses should ensure that the equipment saves the metal’s overall price.
Casting molds
The casting process involves adding hot liquid into a mold to make the product. Some types of molds are permanent, that is, they will be used in the next casting process, while others get destroyed while in the casting process.
The temporary casting molds include sand, vacuum, and ceramic, which shatter after the casting material hardens. Permanent molds are often made of iron or steel, which do not get destroyed after the material is cast.
Types of casting machines
Die-casting machines
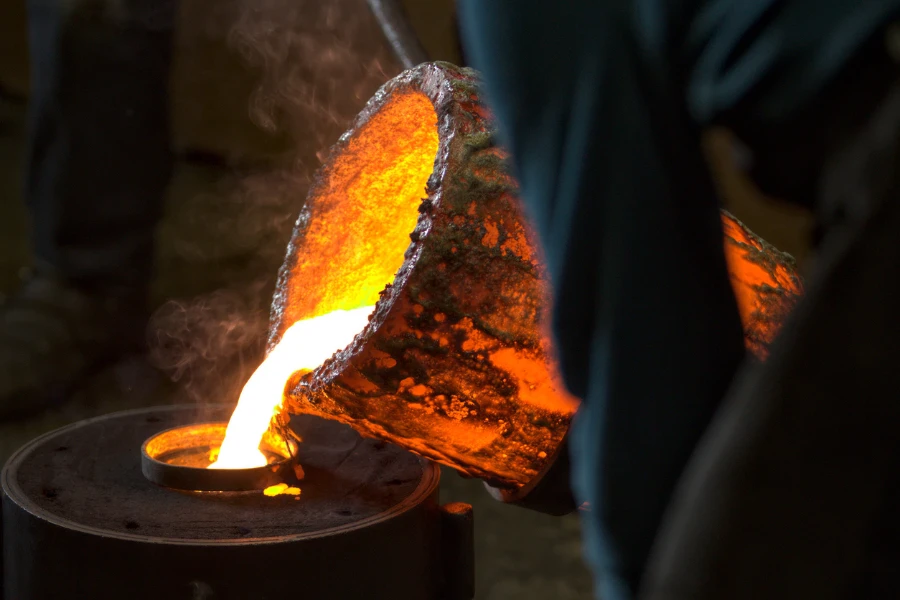
Die-casting machines create metal parts by forcing molten metal into a mold cavity. The machines are typically made of metal and are designed to withstand the high temperatures and pressure involved in the die-casting process. Die casting is mostly used for aluminum metals.
Pros
– Die-casting machines offer a cost-effective method of producing metal parts. They require minimal finishing operations.
– The machines can create high-quality parts with smooth surfaces and precise dimensions.
Cons
– The main disadvantage of die casting is that it is limited to casting certain metals, such as aluminum, zinc, and magnesium, and is not suitable for casting metals like iron or steel.
– Die casting is a relatively expensive process and requires specialized equipment.
Vacuum casting machines
Vacuum casting machines produce high-quality plastic and rubber components using two-component polyurethane resins. The process involves placing a sheet of plastic inside vacuum casting machines and heating the sheet until it is soft. The melted plastic is then poured into the mold to cool and solidify. This quick and efficient process is ideal for short runs and limited orders.
Pros
– The machines offer low costs and quick turnarounds.
– They can produce large parts repetitively.
Cons
– The process is limited to producing relatively thin walls and simple designs.
– Porosity is easily generated in the castings, affecting their performance when exposed to harsh conditions.
Centrifugal casting machines
Centrifugal casting machines produce hollow parts like pipes and cylinders using centrifugal force. The process involves pouring molten metal into a spinning mold, which throws the metal outward from the center with a centrifugal force. The process offers high material soundness and is the metal casting process of choice for jet engine compressor cases, petrochemical furnace tubes, and many military and defense components.
Pros
– Centrifugal casting machines have high production rates and high material soundness.
– They produce symmetrical shapes.
Cons
– The machines are limited to producing simple shapes.
– The products can be costly due to the need for high-precision machinery.
Continuous casting machines
Continuous casting machines are used to produce metal objects in a variety of shapes and sizes. The process involves using multiple rollers and molds to reshape and harden the molten metal. This process is often used to create steel ingots and offers several advantages over traditional casting processes.
Pros
– Continous casting machines offer the uniform production of metal objects.
– They are cost-effective for large-scale manufacturing applications.
Cons
– Continuous casting is limited to producing relatively small objects.
– The machines can generate high levels of vibration and noise.
Ingot casting machines
Ingot casting machines produce metal objects in the form of ingots. The process involves pouring molten metal into a permanent mold made from cast iron isolated by ceramic material.
Pros
– Ingot casting machines increase the strength of the metal.
– They can produce larger quantities of metal and improve its handling.
Cons
– The structure of the center of the ingot can get coarse, which decreases the strength of the metal.
– The process can be complex when casting larger quantities of metal.
Conclusion
By acquiring metal casting machines correctly, businesses can manufacture metal parts effectively. This article covers all the factors and types of machines metalwork shops can consider when choosing the best equipment for their needs.