Different brands of mixing equipment are available out there, making it hard to know which one is ideal for the mixing process. Some of this mixing equipment has existed for years, while others are new in the market. A better understanding of what makes good mixing equipment will always put you ahead when purchasing these machines.
This article will highlight the demand for mixing equipment, before discussing how to select the right equipment, as well as the different types of mixing equipment available on the market today.
Table of Contents
The mixing equipment market
Types of mixing equipment
How to select the right mixing equipment
Conclusion
The mixing equipment market
The demand for industrial mixing equipment has been rising due to the need for more efficient and higher-performance mixing tools in production. Manufacturers strive to achieve equipment adaptability, flow maximization, and energy-efficient devices. Some key companies include EKATO, SPX Flow, and Alfa Laval. The mixers market is segmented based on type, mixed material, distribution channel, end-line use, and region.
The global industrial mixing equipment market was valued at USD 2.4 billion in 2022. The Future Markets Insights projected a further expansion at a compound annual growth rate (CAGR) of 7.8% to reach USD 5.1 billion by 2032. At the end of 2021, the demand increased by USD 2.255 billion and was expected to register a year-on-year growth of 6.3% in 2022.
China is anticipated to be the biggest market for industrial mixers during the forecast period. The growth is ascribed to the surge in applications in the pharmaceutical and chemical industries. Other countries expected to have a steady increase in demand are Germany and the U.S. Also, there will be maximum industrial mixers sales from the food and beverage industry during the forecast period.
Types of mixing equipment
1. Tumble blender
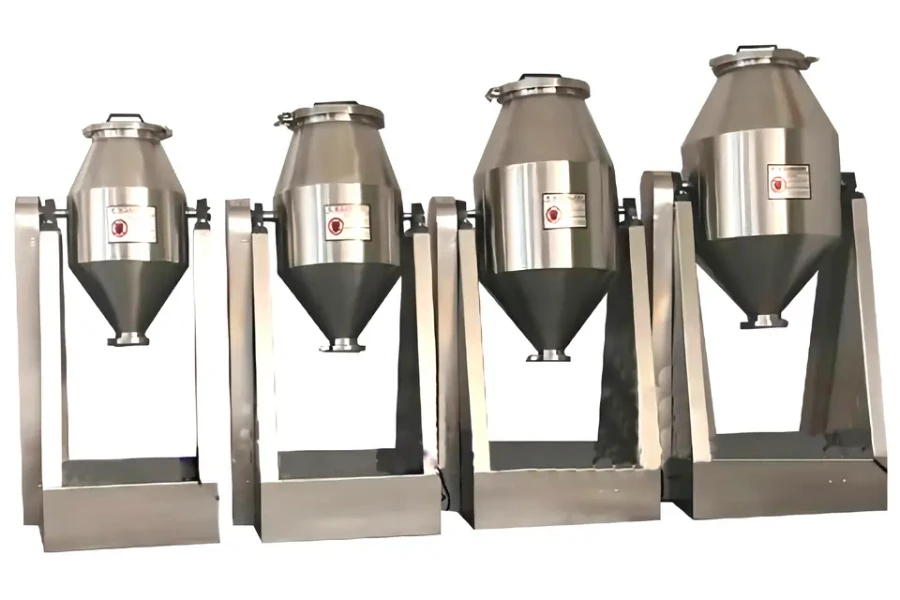
Tumble blenders mix slurry-type and low-viscosity applications where solids and liquids are added via the vessel cover. They are available in different geometries, the most common being the V-shaped or double-cone design. The vessel is partially loaded with products and rotated at speeds ranging from 5 to 25 revolutions per minute. Through diffusion, the primary mixing mechanism, the materials stream down to distribute particles over freshly exposed surfaces as the vessel rotates on a horizontal axis. Some of the end products of this mixer include metal powders, detergents, plastics, fertilizers, and ceramic powders.
2. Paddle mixer
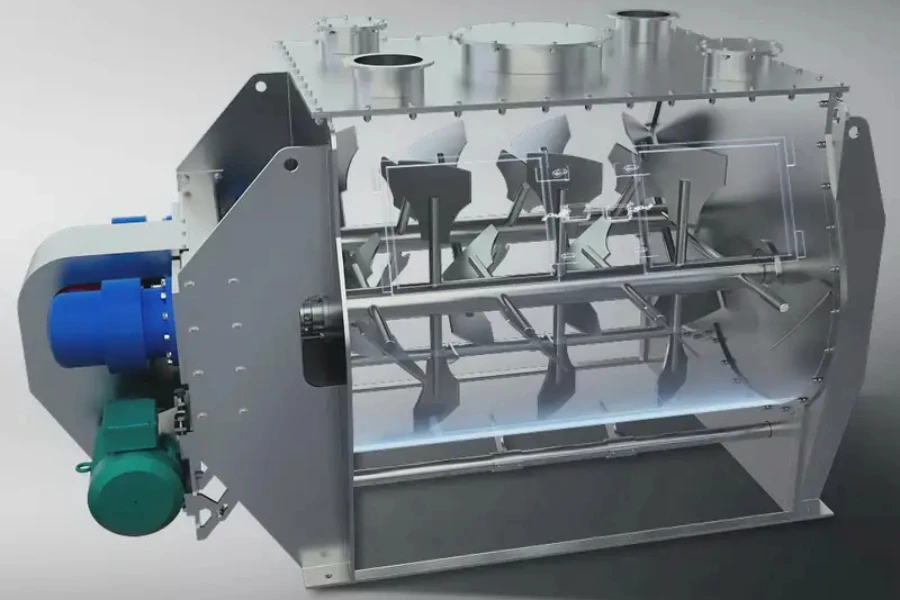
Paddle mixers are used as stand-alone agglomeration machines or in mixing steps in more extensive agglomeration processes by utilizing agglomeration drums or disc palletizers. These mixers use dual rotating shafts with pitched paddles to produce a kneading and folding-over movement inside the trough. Usually, the material and applicable binder are fed into the mixer continuously. As such, the pitched paddles move material from the trough bottom, up the middle, and back to the sides. This results in an intimate mixture of the materials. The products include scrubber sludge, agricultural chemicals, cement, etc.
3. Emulsifiers
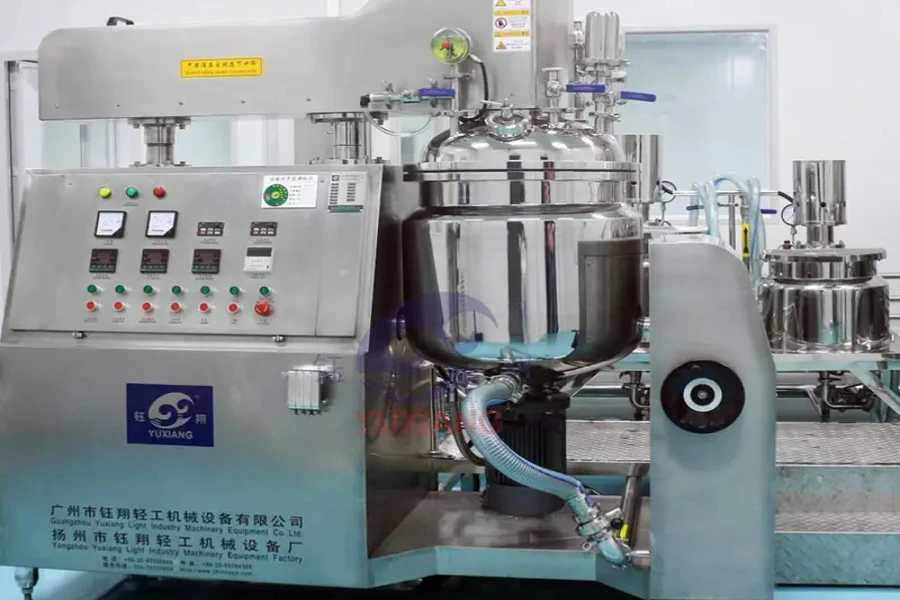
Emulsifiers are used to mix two or more immiscible liquids. There are vital considerations when selecting the emulsifying system, which include cooling or heating requirements, the need for wall scrapers, overpressure or vacuum requirements, design of the mixing head, desired droplet size, and viscosity of the liquids. Typically, emulsifiers are used in the food industry to produce creams, batters, and sauces. They are also used in the pharmaceutical, cosmetics, and chemical industries to produce creams, lotions, and paint emulsions.
4. Agitator
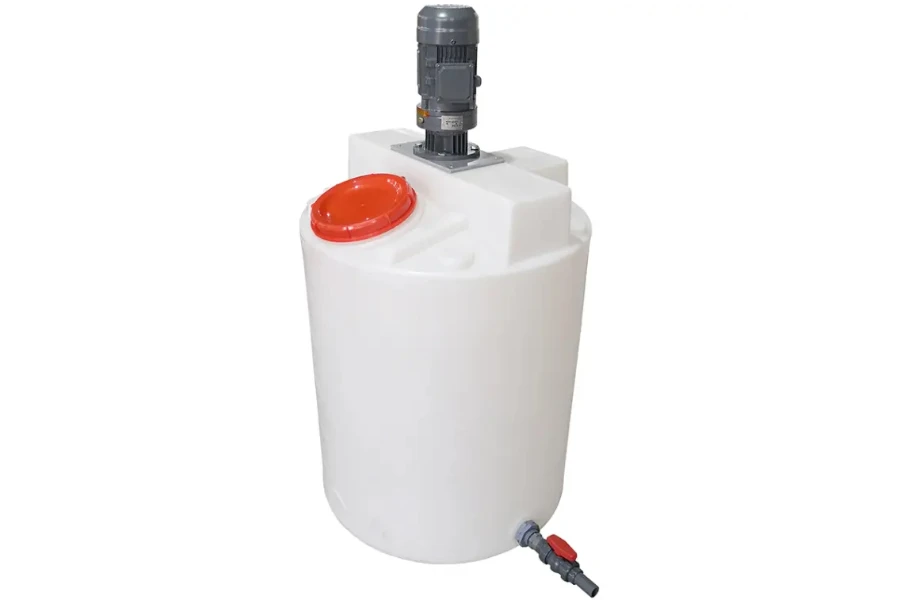
An agitator is equipment used in a tank to mix different process media together. The media may include gasses, liquid types, and solids like powders, salts, and granules. This machine imparts energy via mechanical means by rotating a shaft that has an impeller. The impeller can be designed for various functions like axial pumping, flocculating, gas induction, low and high shear mixing, etc. It can also be used in the water industry to add various chemicals to elevate the water source to the water drinking standards.
5. Ribbon blender
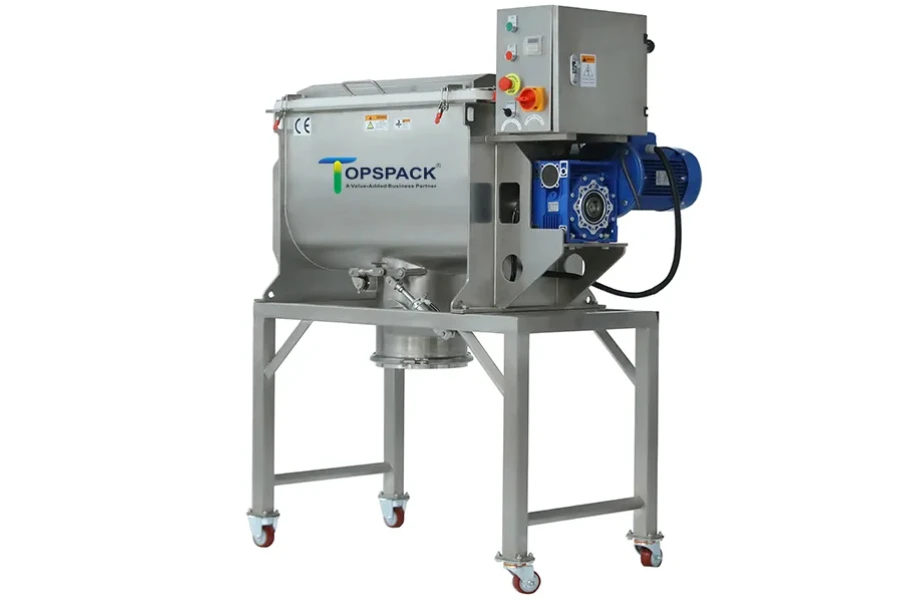
Ribbon mixers are used in mixing powders. They have two parts mounted on a central shaft. The mixing medium has inner and outer helical ribbons designed to move particles both inwards and outwards. In this case, the external helical ribbons pull materials from the sides of the mixer into the middle. Afterward, the internal ribbons push the particles back to the sides. This back-and-forth folding movement of products to be blended produces a convective mixture. They can be used to produce nutraceuticals, polymers, cosmetics, etc.
How to select the right mixing equipment
1. Performance
Various factors affect the performance of mixing equipment. Mainly, the mixing process and the products to be mixed determine how efficiently the mixer will operate. Buyers should seek mixers that meet the requirements and industry standards to ensure the safety and quality of products. Mixers should perform various mixing functions like reducing particle size, manipulating rheology, and enabling chemical reactions. Moreover, they should have high repeatability and scalability for easy validation of mixing parameters choice in various applications.
2. Speed
Regarding speed, some mixers can achieve a perfect blend in as little as 15 minutes. Others are designed to run at speeds of around 4800 and 5500 FPM. A slower speed means the mixer cannot generate the required shear to disperse and mix products. Over prolonged periods, the machine could overheat as it is not running fast enough to cool itself adequately. Also, a higher speed than the optimal is less effective as they consume much more motor power. The ingredients’ size and density are considered to determine the mixing time. Buyers could speed up the mixing time and achieve efficiency by creating recipes with similar size and density ingredients. They should simply ensure the mixer is properly sized for the product being processed.
3. Budget
Buyers should acquire mixing equipment based on their production lines and within favorable budgetary plans. Generally, most industrial mixers have a starting price of about USD 3,000. Some mixers are more complex and thus can cost up to way above USD 30,000. Also, buyers should know the maintenance cost level, which depends on the mixer’s design. Operational costs are minimal when maintenance is simple. The result is reduced downtime and improved machinery efficiency.
4. Efficiency
The efficiency of mixing equipment depends on several factors that buyers should consider while purchasing. Selecting suitable horsepower is an ideal way of enhancing efficiency. The ingredient density, required agitator speed, and batch volume will help buyers arrive at the correct horsepower. Also, a mixer that has optimized processes like loading, unloading, and cleaning has maximized efficiency. For instance, buyers can make loading material onto the mixer faster and more manageable by getting an opening cover with a big charging port.
5. Applicable material
The amount and composition of materials influence the choice of the type of mixing equipment. This includes additions like powders, hazardous materials, and highly viscous liquids. Firstly, powders require super sack handling equipment, screw augers, specialized raw material storage, and additional rotary valves. Secondly, viscosity determines the types of pumps used and the pipe size to start. Also, it determines whether there will need to use a high-shear mixer or ribbon blender. Integration of hazardous materials affects the electrical classification of the instruments and the design of the mixing tank. Lastly, the amount of materials determines the number of tanks, mixers, pumps, and other accessories used in the mixing process.
6. Automation
Various buyers desire different levels of automation on machines they intend to purchase for mixing purposes. Opting for highly automated systems increases consistency by eliminating human error. Generally, raw material additions and final product handling are affected by the option to invest in automated or manual mixers. In automated circumstances, most materials are fed into the mixing system using automatic pumps and flow meters. In contrast, material mixing with less automation has most tasks executed manually. Notably, automation increases efficiency and improves the quality of the final product.
7. Working capacity
Industrial mixers are generally large vehicles. Mostly, the typical capacity for mixers ranges from 100 to 10,000 liters. Usually, buyers should calculate the product’s size and the vessel’s capacity. The working capacity of the vessel shows the time used on loading, emptying, and cleaning, which results in downtime. As such, the batch height, the diameter of the vessel, and the volume should be well thought through. The factors aid in the choice of the most suitable mixer for the products being to be mixed.
Conclusion
Generally, it can be challenging to select the appropriate mixing equipment. Many mixing technologies overlap in function and use. As a result, specific formulations can be achieved in more than one type of mixer. Nonetheless, buyers should ensure that the selected mixer’s mechanical aspects enhance mixing safety and efficiency. The above guide provides a deeper understanding of various components that should be understood before investing in mixing equipment. To learn more, and to browse listings of high-performance mixers, visit Alibaba.com.