Using the right chilling equipment increases the accuracy of the production process and speed. Also, these chillers can reduce the total costs and water consumption. Failing to find the right chilling equipment means the results will not be as expected, and the price may be too high. Since there are so many of these chillers in the market, it is essential to gather all the necessary information before making a purchase.
This article will look at the different types of chilling equipment available and how to select the perfect chillers. Additionally, it will discuss the chilling equipment market’s share, size, and expected growth.
Table of Contents
Overview of the chilling equipment market
Types of chilling equipment
How to select the perfect chilling equipment
Summary
Overview of the chilling equipment market
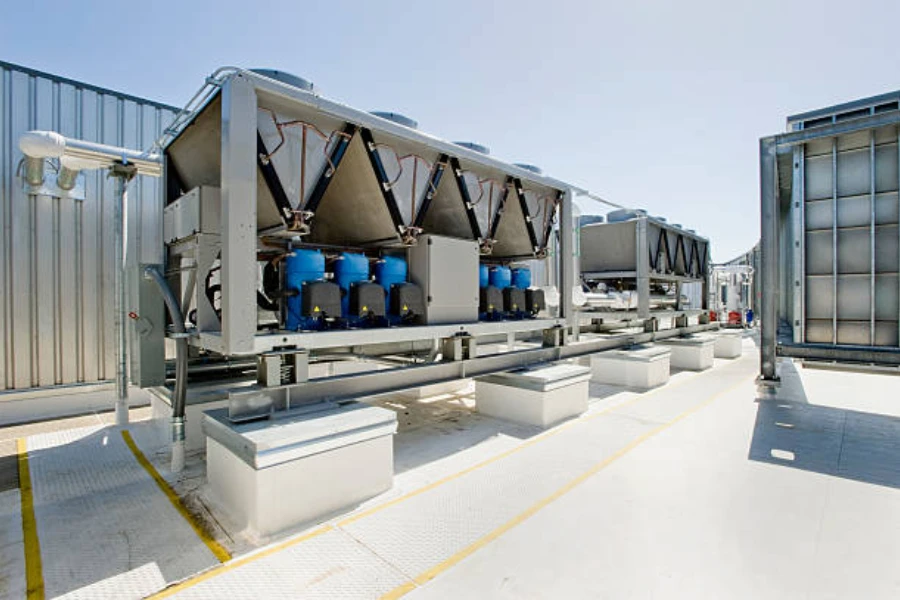
The global chilling equipment market is differentiated based on type, end-use industry, and region. It is predicted to expand due to demand from several end-use industries. Generally, the demand for chillers has grown because of their benefits and the healthy competition created by the major manufacturers. Some of these manufacturers include Daikin Industries, Trane Technology, and KKT Chillers.
Markets and Markets research estimated that the global chilling equipment market size at USD 4.1 billion in 2021. It was projected to reach USD 4.8 billion by 2026, registering a CAGR of 3.0%. The driving force for this growth is the recovery of major end-use industries during this forecast period.
In 2020, the scroll chillers segment dominated the chilling equipment market with a share of over 40.0%. This is because the scroll chillers cool using water and heat transfer fluids, making them more efficient.
Regionally, the Asia Pacific market dominates the global chiller market because of increased adoption in India, China, and Southeast Asia.
Types of chilling equipment
1. Vapor absorption
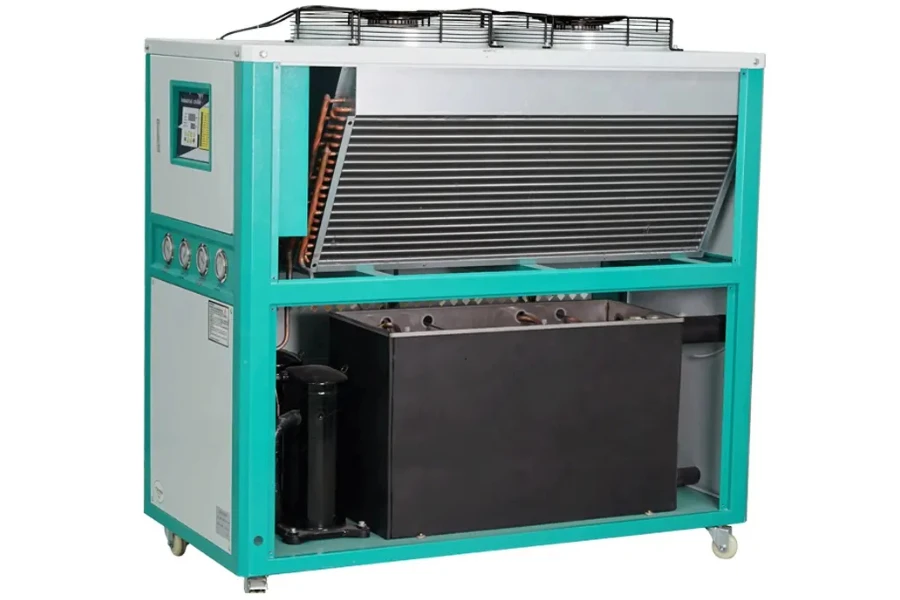
Vapor absorption machines (VAM) produce chilled water using heat sources like hot water, steam, oil, and gas. The commonly used refrigerant is ammonia. In absorption cooling, three principles are applied:
– The liquid is heated to boil or vaporize, and the gas is cooled to condense.
– When the pressure is lowered above a liquid, its boiling point reduces.
– During the chilling process, heat moves from warmer to cooler surfaces.
2. Vapor compression
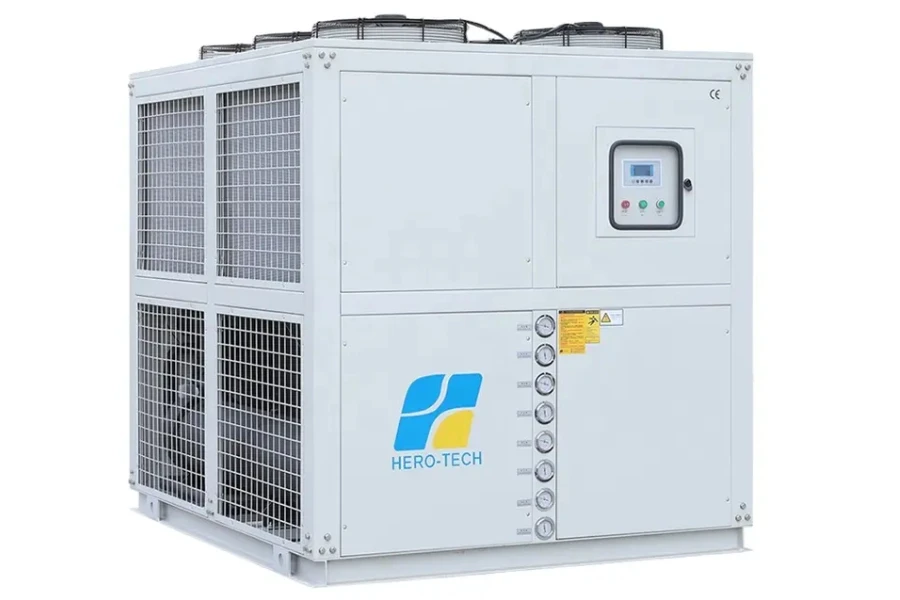
In vapor compression chilling equipment, the cycle consists of four components: condenser, compressor, evaporator, and expansion/throttle valve. This compression process aims to raise the pressure of the refrigerant (R-717) as it flows from the evaporator. The high-pressure refrigerant moves through a heat exchanger/condenser before attaining the initial pressure and flowing back to the evaporator.
The chilling process involves:
– Compression: The temperature and pressure of the refrigerant is raised.
– Condensation: Heat is transmitted from the refrigerant to a water flow.
– Throttling and expansion: The refrigerant expands in the throttling valve to release pressure and drop the temperature.
– Evaporation: The refrigerant evaporates and absorbs the latent heat of vaporization.
How to select the perfect chilling equipment
1. Size
The correct size of a chiller is crucial as it determines its performance level. There are frequent problems experienced when using undersized chillers. This is because they are unable to efficiently cool the process components, and the water temperature might not be stable.
On the other hand, oversized chillers cannot run at their most efficient levels and are usually costly to operate and maintain. Buyers choose the suitable size by considering the flow rate and the amount of heat the process equipment contributes to the chilling medium. Typical scroll or screw chillers can range from 30 to 85 tons.
2. Operation features
Operation features, production levels, and timing are considered when selecting the chilling equipment. The size of a chiller determines its effectiveness and cooling capacity. Some chillers have various independent chilling departments that provide improved flexibility, versatility, and efficiency.
Also, most chillers are designed to chill items immediately. Buyers would opt to acquire oversized chillers to accommodate the changes in cooling capacity requirements. They should select chillers based on the batches of items they intend to cool.
3. Cooling capacity
A chiller’s cooling capacity measures the system’s ability to remove heat. Generally, the SI units for cooling capacity are watts (W), tons of refrigeration (RT), or British Thermal Units per hour (BTU/hr). The cooling capacity of chilling equipment decreases with the setpoint temperature.
A lower setpoint means a smaller temperature differential between the chiller fluid and refrigerant. In this case, less efficient heat transmission will reduce cooling capacity. Buyers should always check the manufacturer’s specifications which state the cooling capacity at certain temperatures. For instance, cooling at 40 GPM from 70 to 58 degrees Fahrenheit requires a 25-ton chiller.
4. Cost
Several factors affect the chillers’ price, including model, power, temperature control accuracy, after-sales service, cooling capacity, and other technical parameters. As a result, buyers should carefully select chillers based on their actual production needs.
Opting for low-quality and cheap chillers might result in lower accuracy and precision disappointments. A good quality chiller has a required precision of around 0.1 degrees Celsius. The most popular chillers have an initial price of about USD 1.000.
5. Operating environment
Buyers should know the site conditions where the chillers they intend to acquire will operate. As such, they will essentially choose the appropriate products that fit their production lines. Primarily, spatial constraints and ambient temperature are the most important conditions to be considered. The chilling systems use ambient air/refrigerant temperature to induce heat transmission for the condensation process.
For instance, a rise in ambient air temperature reduces the temperature differential, decreasing total heat flow. Considering spatial constraints, it is vital to maintain a proper ambient air temperature. This is achieved by providing adequate circulation air space around the chilling equipment.
6. Process cooling temperature
Generally, a chilling equipment’s cooling capacity is directly affected by the equilibrium temperature. In other words, the temperature at which the chiller is set is its total cooling capacity. In this case, a decrease in temperature increases the load on the chilling system, while an increase in temperature reduces the load on the refrigeration system.
Generally, the temperature range required for a chilled water system is 6 to 12 degrees Celsius or 5 to 11 degrees Celsius with a six degrees temperature difference.
7. Fluid to be used
When selecting the fluid to be used in the chilling process, buyers should take into account its compatibility with the equipment and its performance. The most commonly used fluids include water, water-soluble oil, and oil. Their performance is majorly based on certain properties at a specified temperature. The components include viscosity, specific heat, and boiling & freezing points. With equipment compatibility, the materials and fluids used should complement each other to prevent corrosion risks and early seal degradation.
8. Refrigerant
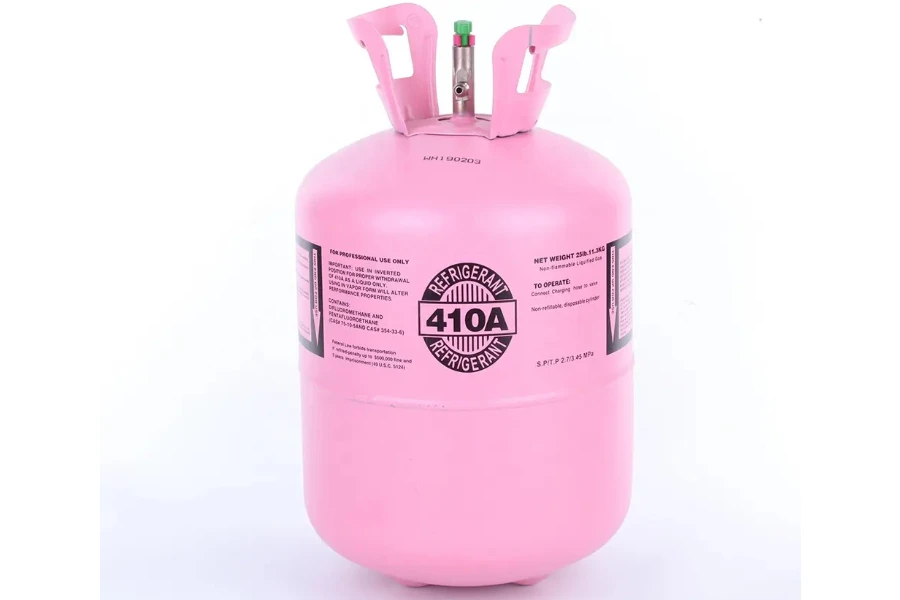
A refrigerant is a chemical compound that works on the basic principle of phase change from liquid form to gas and back to liquid and compression during the refrigeration cycle. Several refrigerants are used in various chilling applications based on their set point temperatures. The most commonly used refrigerant is ammonia (R717) which belongs to halogen-free chemicals. This is because it has the highest heat absorption rate, making it ideal to be used in smaller, portable amounts. Other refrigerants include water, R134 HFC, R744 CO2, R404A, etc.
Summary
Manufacturing machinery produces a lot of heat during operation due to the complex automation to achieve high precision and speed. Therefore, machines require cooling systems to function properly and efficiently. Buyers need to understand the conditions and the process for which the chilling equipment will be used. The above guide outlines the features that are most needed for various kinds of chilling systems. Moreover, to acquire quality chilling equipment, visit Alibaba.com.