Plastic blowing machines help produce thermoplastic products through blow molding. In blow molding, manufacturers use different techniques to mold plastic products in different shapes and sizes. The different types of molding include extrusion, compression, injection, and injection stretch blow molding.
In each technique, manufacturers may need help choosing which plastic blowing machine works best. Picking the best machine should be easy. Therefore, this article will examine the tips for choosing the right machine for an effective blow molding process.
Table of Contents
Global market overview of plastic blowing machines
8 tips for selecting plastic blowing machines
Types of plastic blowing machines
Conclusion
Global market overview of plastic blowing machines
The global blowing machine market was valued at US$ 13.08 billion in 2022. It projects to reach a US$ 17.33 billion value by 2030, growing at a CAGR rate of 3.5%. The vast market size mainly comes from the need for plastic containers in the medical industry. Plastic manufacturers depend on blow molding tools to produce containers such as bottles and syringes for medicine storage.
The need to recycle plastic to meet the high demand from food and beverage has also fueled the need for blow molding tools. Food manufacturing plants heavily invest in recycled plastic to package food and beverage products.
8 tips for selecting plastic blowing machines
Production capacity
Businesses investing in plastic blowing machines should be keen on considering the limit the machines can produce. Blow molding tools have a limit to how many thermoplastic products they can produce at a specified time. Therefore, it is important to research and learn more about the available plastic blowing machine models and how much they can produce.
They should also consider how much plastic they need to manufacture before deciding on a plastic blowing machine with the right production capacity. Large-scale producers may need machines with a high production capacity, while small-scale producers can acquire blow molders with a lower output.
Product type
Considering the type of plastic product is essential for businesses shopping for plastic blowing machines. The machines use heat to produce different types of plastic. For example, an extrusion blow molding tool is appropriate when making HDPE or LDPE plastic bottles with a wide neck. Compression blow molding machines will help to manufacture bottles with a wide body and thin neck.
Energy efficiency
When purchasing a plastic blowing machine, take into account the energy it consumes. Buyers should always focus on acquiring equipment that is low on energy consumption. The machines will help to save not only on the energy costs of operating the tools but also on the overall cost of production.
Auto-deflashing
In molding, unwanted residue can form on the plastic product. Workers used to cut the extra flesh with a sharp tool, such as a knife, from the bottles or containers in a method called deflashing.
Since manual deflashing is labor-intensive, tedious, and time-consuming, businesses should consider acquiring a machine with an auto-deflashing feature.
Auto-deflashing machines ensure precision and accuracy in bottle production. Also, they increase the efficiency of the production lines.
Advanced machine design
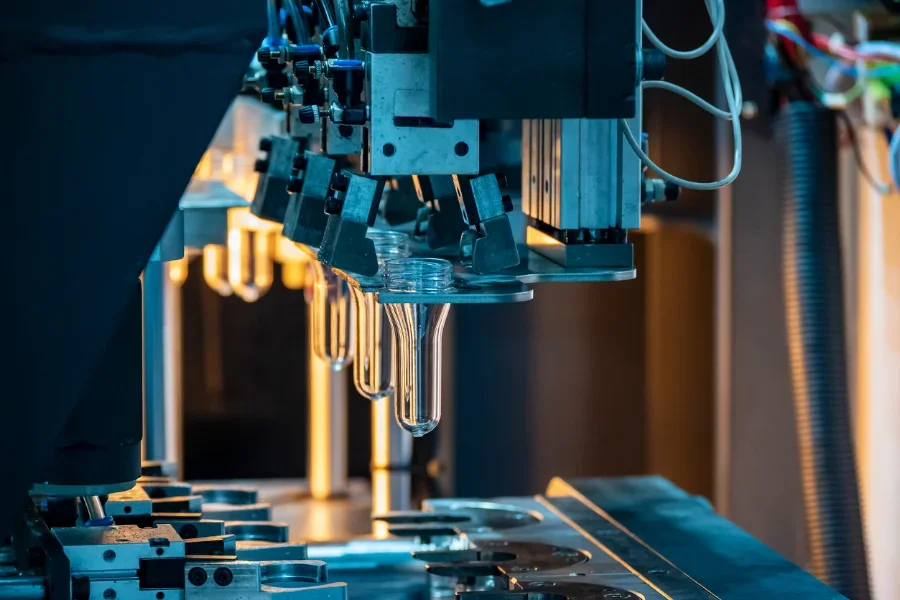
The designs of plastic blowing machines will differ, potentially affecting the machine’s productivity and end product of the molding process. For instance, outdated machine designs cannot operate as effectively as new designs with advanced features. Plastic blowing models that use old technology have some flaws. They are slow, consume more energy, and may be costly to maintain.
Businesses should consider buying machines that have an updated design. These machines are fast, energy efficient, and cheap to maintain. This ensures a hassle-free operation while producing quality products with high speed and accuracy.
Parison controller
Buyers looking for reliable plastic blowing machines should consider the parison controller feature. A parison controller helps to control the thickness of plastic products in the blow molding processes, allowing for the production of more accurate products.
Moreover, a parison controller helps in quality control and compliance with industry standards for the required axial and radial product thickness.
Maximum working capacity
When choosing a plastic blowing machine, the maximum working capacity is essential. The working capacity of the machine is dependent on the requirements for production. Blow molding machines are categorized into fully auto, semi-auto, and partial auto machines.
For businesses looking for a machine that can deliver a quick, precise, and high production rate, they can pick fully auto plastic blow molders.
Semi-auto and partial auto plastic blow molding machines offer speed and time customization intervals for mold production. Their benefit is that they comprise a compact size and can deliver production levels based on specific requirements. These machines are, therefore, suitable for small-scale manufacturers.
Clamping force
The clamping force is crucial when buying a plastic blowing machine. It is the force required to compress and keep the mold together. Buyers should purchase a machine capable of withstanding the required maximum clamping pressure.
If the plastic blowing tool has less clamping force than the needed pounds or kilograms, it may produce low-quality molds. Also, if the machine produces a lot of force, more operational capacity goes to waste while consuming too much power.
Types of plastic blowing machines
Injection blow molding machine
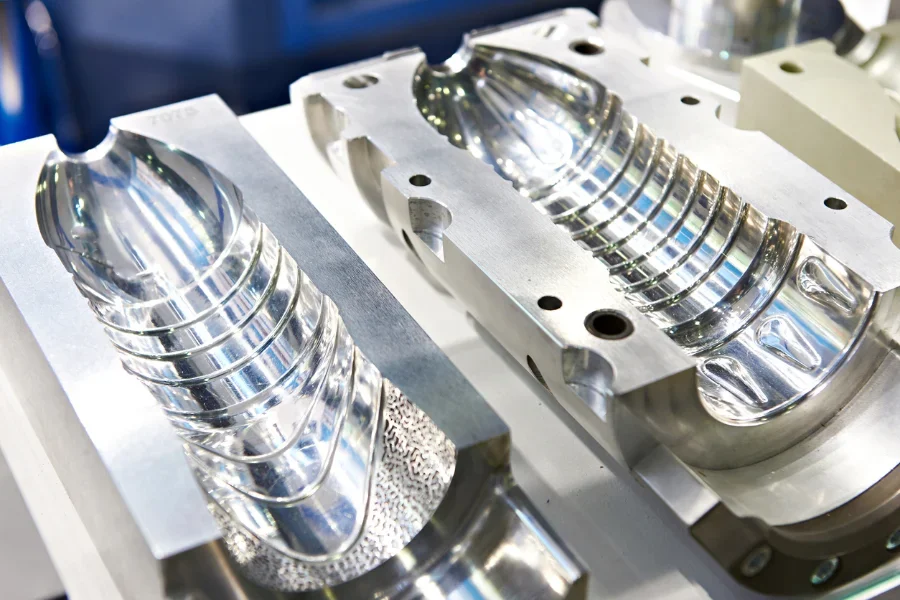
These plastic blowing machines use a long screw to inject heated resin and compress it into a mold. As the resin melts, it becomes a preform. It then injects air into the preform to form the desired shape.
Pros
– They have high production speeds and efficiency.
– They maintain consistent product quality and dimensions.
– They can produce a wide range of bottle sizes and shapes.
– They can produce bottles with thick walls, suitable for packaging various products.
Cons
– Long lead times to produce the mold slow down production.
– Scrap rates can be high when making complex parts or poorly designed molds.
Extrusion blow molding machines
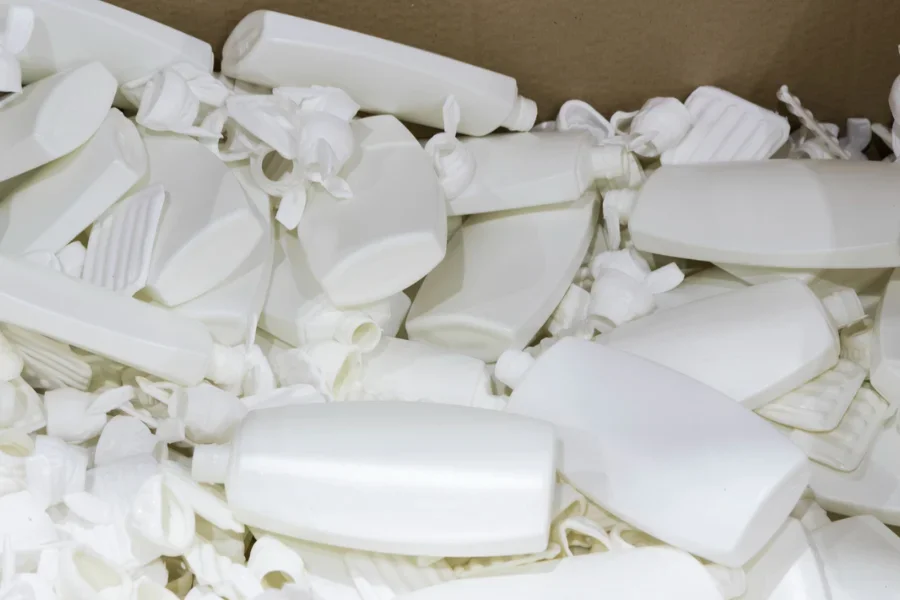
An extrusion blow molding machine produces hollow plastic parts using a continuous process. The process involves forcing melted plastic material continuously into a hollow tube (parison), which is then transferred to a mold where it is inflated and formed into a desired shape.
Pros
– They support high production speeds.
– They can produce complex shapes.
– They allow for the efficient use of raw materials.
– They can be automated.
Cons
– They produce plastic parts with a limited size.
– There can be long setup times for tooling changeover.
– They have higher scrap rates compared to injection molding.
Stretch blow molding machines
A stretch blow molding machine works similarly to an injection blow molder, but the difference is that it uses air to stretch a preform over a mold to form the final product shape.
Pros
– They can produce large numbers of parts in a short period of time.
– They can produce parts with consistent wall thickness and high clarity.
– Manufacturers can use a wide variety of materials with stretch blow molding, including PET (polyethylene terephthalate), PVC (polyvinyl chloride), and PP (polypropylene).
– Stretch blow molding machines use less energy compared to other molding processes.
Cons
– The machines and tooling can be expensive to purchase and install.
– The process is typically limited to producing cylindrical parts, and it can be difficult to produce complex shapes or intricate details.
– Stretch blow molding requires the production of preforms, which adds a step to the manufacturing process and increases production costs.
Conclusion
Plastic-blowing machines are essential for the precise production of plastic for various packaging uses. Businesses having challenges finding machines can use the above tips to choose reliable blow molding equipment.