In recent years, manufacturing activities have increased in order to meet the global demand for plastics and metals. As a result, the use of injection molding and extrusion processes has also grown significantly. These processes are used to mass produce plastics at a competitive speed.
However, the two methods have considerable differences. For instance, injection molding is more suitable for three-dimensional shapes, while extrusion is better for two-dimensional shapes. This blog further compares these processes, exploring their use in plastic manufacturing, their pros and cons, and the major differences.
Table of Contents
Injection molding process
Extrusion process
Differences between injection molding and extrusion
Conclusion
Injection molding process
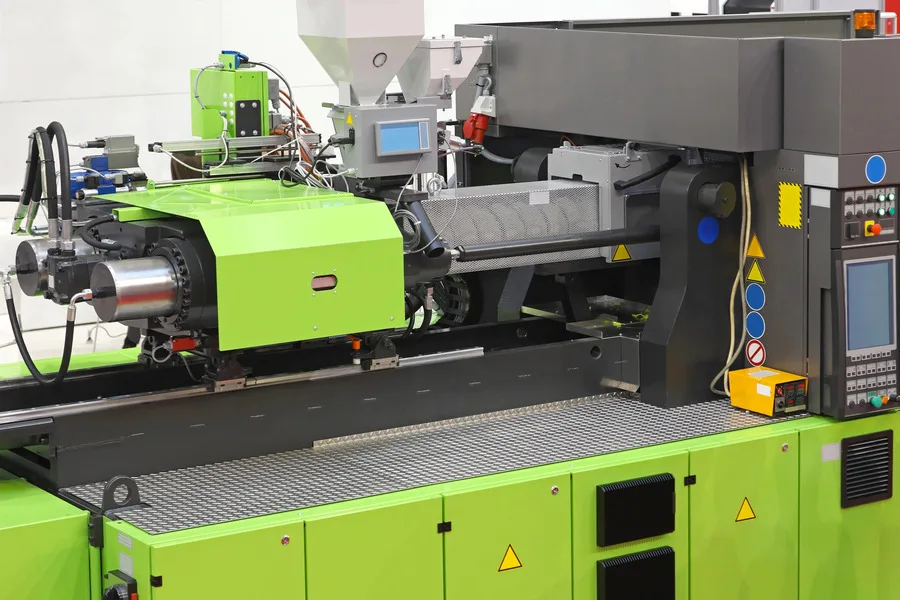
Manufacturers worldwide are embracing processes and innovations that facilitate low-cost mass production. As a result, injection molding has become the go-to process for most manufacturers since it uses low-cost technology to enable high-volume production and wide applications. This is evidenced by the rapidly growing global injection market size, which was valued at US $261.8 billion in 2021 and is projected to grow at a CAGR of 4.8% between 2022-2030.
The injection molding process converts the plastic resin to complex plastic products using heat, pressure, an injector, and a mold. In this case, solid plastic is melted at a specific melting point and injected into a mold structure at a given speed. The injection machine provides the needed pressure, while the waterway facilitates cooling to obtain the desired product.
Advantages of injection molding
- High precision and accuracy
- Compatibility with most plastics
- Cost-effective for high-volume production
- High efficiency and productivity
- Consistent performance
Disadvantages
- Long initial lead times
- Unsuitable for low-volume production
- High set-up costs
Extrusion process
Growth in the global manufacturing sector is fueling the demand for extrusion machinery. This demand is reflected in the global extrusion machinery market, which was valued at US $8.33 billion in 2022 and is projected to grow at a CAGR of 4.3% between 2023-2030.
Extruded products are in huge demand as they are used in multiple world-spanning industries, including automotive, consumer goods, and packaging. While the extrusion process can be used in metals and ceramics, it is primarily used with plastic materials, which accounted for 76.9% of the global revenue share in 2022.
The extrusion process involves feeding thermoplastic materials into an intruder, where they are heated, melted, and then forced through the die to create a continuous, specific shape. The extruder typically consists of a rotating screw that pushes the molten material forward, providing the necessary pressure for extrusion. As the material exits the die, it solidifies and retains the desired shape. This process is suitable for creating products such as blown films, plates, tubes, rods, and shaped materials.
Advantages
- Ideal for high-volume production
- Highly versatile
- Low cost
- Great surface finish
Disadvantages
- Inability to handle deviations in the cross-section or size
- Potential environmental concerns
Differences between injection molding and extrusion
Despite the perceived similarities between injection molding and extrusion processes, they differ in various aspects, including the process fundamentals, level of precision, and compatibility.
Process
Injection molding and extrusion use different processes to produce the final product.
1) Injection molding process
The injection molding process begins with melting the material and injecting it into a mold structure with cavities of the required shape, where it then cools and solidifies. The process occurs in a specific cycle consisting of the seven main stages described below.
- Pre-molding preparations
Manufacturers looking to create quality products and aiming for a smooth plastic injection molding process adopt various preparation activities. These include:
- Pretreating the raw materials
- Cleaning the barrel
- Preheating the insert
- Selecting a release agent
- Adding material
The first step in the injection molding process is adding the materials. The materials should be added quantitatively by keeping the volume constant to ensure operational stability and plasticization uniformity, resulting in high-quality products.
- Plasticizing
The barrel in the injection molding machine is used to heat, press, and mix the molding material, thus transforming it from granular solid or loose powder into a continuous homogenized melt.
- Injecting
The plunger or screw exerts significant pressure through the injection cylinder and piston, propelling the plasticized plastic melt through both the barrel’s front nozzle and the mold’s nozzle.
- Cooling
Once the plastic melt is injected into the closed mold cavity, cooling materials such as water, air, or oil are introduced to further cool the mold.
- Demolding
At this point, the cooled plastic is pushed out of the mold using an ejection technique, such as via ejector pins or plates. This phase marks the end of the injection molding process by ensuring that the finished part of the mold is separated without causing any damage or distortion to its shape.
- Product post-processing
This post-processing phase includes various activities, such as removing residual stress in molded parts reflected in variations in thickness, cracks, or distorted shapes. It may also involve humidification, which entails stabilizing the molded part’s color, performance, and size.
2) The extrusion process
During extrusion, the polymer material is forced through a die using a screw or plunger under pressure. The extrusion process is divided into three stages:
- Material plasticization and pressurization
This stage entails feeding the raw material, in the form of pellets or granules, into the extruder through the hopper. A screw is then used to push the material into the barrel, exposing it to heat and mechanical action to initiate plasticization. This transforms the material into a molten or plasticized state. Simultaneously, a rotating screw generates heat, promotes mixing, and applies pressure to ensure consistent plasticization of the material.
- Shaping
In this phase, the extruded material passes through the shaping elements of the die, which include specially designed openings or channels. These help the extruded material take the desired form, shape, and dimensions.
- Cooling
As the extruded material leaves the die it enters a cooling zone, exposing it to cooling mechanisms such as ambient air, water sprays, or cooling baths. This helps reduce the material’s temperature and solidifies it, thus transforming it from a molten state to a solid form.
Compatibility with plastics
While some types of plastics used in injection molding and extrusion may overlap, certain materials may be better suited to one process or the other due to variations in properties and compatibility. For instance, injection molding is compatible with all kinds of plastics, including thermoplastics and most thermoset plastics. This compatibility is based on the process’ ability to process materials with complex chemical compositions.
On the contrary, most extruders are mainly compatible with thermoplastics with excellent melt flow properties and stability. This is because the process mostly relies on the continuous flow of material for smooth extrusion.
Precision
Injection molding offers higher precision and tighter tolerance than extrusion. It is known for its ability to produce highly precise and intricate parts with excellent dimensional accuracy. This is because the process involves injecting the molten material under high pressure into a closed mold cavity, thus facilitating precise control over the final product’s shape, size, and surface finish.
Extrusion involves the continuous flow of the molten material through a die. While the extrusion dies can be precisely engineered, the level of precision is lower than that of injection molding. However, extrusion can achieve acceptable precision levels, especially with simpler shapes and projects requiring less stringent tolerances.
Material fluidity
Material fluidity is a critical component for both processes. However, injection molding requires higher material fluidity to ensure proper mold filling, especially for intricate and thin-walled products. The molten material used in this process must have excellent fluidity to spread easily into the mold cavities’ complex contours, corners, and thin sections.
Conversely, extrusion has less stringent material flow requirements due to its continuous and open-ended nature. For this process, there is no need to fill complex mold cavities, meaning that the materials only require sufficient fluidity to flow smoothly through the die and maintain a consistent shape and dimensions along the length of the extruded product.
Melt strength
Both processes require different degrees of melting strength. For instance, injection molding does not require high melting strength since the plastics are molded in a die, thus subject to geometrical limitations. In addition, the materials are injected into controlled cooling, allowing quick solidification.
In extrusion, the material exits the die freely and may require subsequent processes such as thermoforming and hollow blow molding. These processes may result in distortions such as sagging and stretching, which may lower the quality of the finished product. Thus, the needed metal strength is higher in extrusion than in injection molding.
Conclusion
Growth in the manufacturing sector has significantly enhanced the adoption of injection molding and extrusion. While both processes are used in plastic production, they have considerable functional differences and attributes. For instance, injection molding is suitable for 3D products, while extrusion is suitable for 2D products. In addition, injection molding is compatible with a wide range of plastics compared to extrusion. Thus, choosing between the two should be based on careful consideration and planning of the process, materials, and efficiency.
To find thousands of products and machines related to injection molding and extrusion, visit Alibaba.com.