Piling is the engineering process of driving or drilling vertical structures deep into the ground to support construction above ground. Piling has been used for thousands of years and is necessary to provide strength and stability to carry the heavy loads of buildings, bridges and other large construction projects. Piling is especially necessary to prepare the ground when the subsoil is weak or water-saturated, and for tall construction such as skyscrapers. However, piling is a noisy and invasive process. This article looks at the current trends in piling technology and how they will improve construction.
Table of Contents
The growing construction and piling market
The trend to more eco-friendly piling
Making use of technology to develop intelligent piling
Embracing new methods of piling
Final thoughts
The growing construction and piling market
The global construction market is estimated to grow from a value of US$10.7 trillion in 2020 to US$15.2 trillion by 2030, with around 58% of that coming from emerging markets, particularly the US, China, India and Indonesia. Supporting this, the global construction piling machine market is projected to grow at a compound annual growth rate (CAGR) of 3.6% from 2021 to 2028, from a 2020 valuation of US$5.08 billion. Asia Pacific was the dominant region in the global piling machine market to 2020, with 49.7% market share by volume, and the US and Europe following. With such high growth, there is increasing pressure on construction companies to meet new environmental standards and leverage technology for greater efficiencies.
The trend to more eco-friendly piling
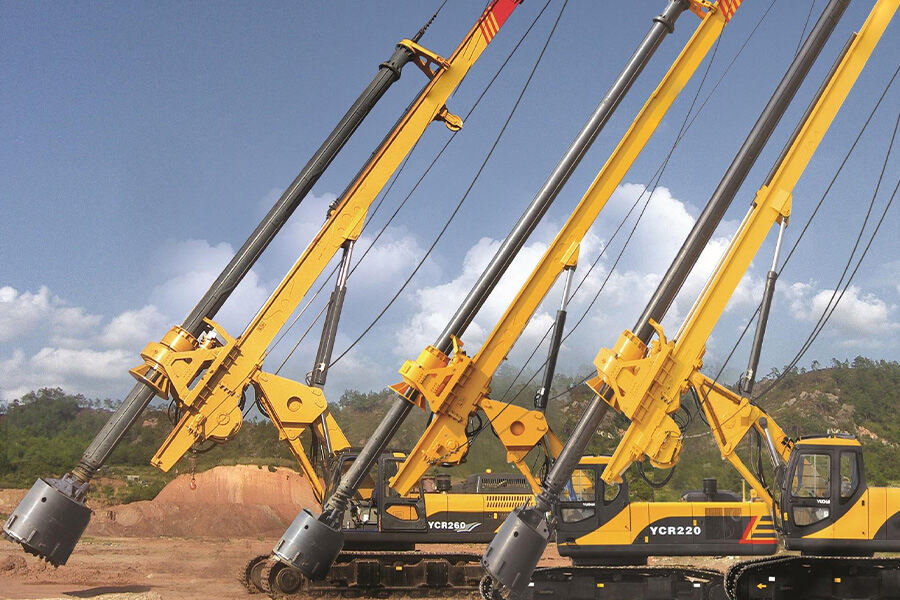
Anyone who has been unlucky enough to live near to a large construction site will be familiar with the heavy thump-pause-thump of nearby piling machines hammering piles into the ground at all hours. Hammer piling, driving steel or concrete piles into the ground, remains one of the most popular methods of choice for constructors, but is not popular for those that live nearby and suffer the loud repetitive banging.
In urban areas, hydrostatic piling is often used instead of hammer piling, using vibration to drive down the piles, but vibration is pervasive and disturbs residential and office occupants almost as much as hammer piling.
A variation on driving in precast piles, is to use hollow tube piles that are augured (screwed) into the ground. The inner material is extracted and then filled with concrete and cast into position. Bored piles create less vibration than other methods, so are sometimes preferred in urban construction.
Each of these typical methods have their own impact on the environment or come up against local regulations, so manufacturers are looking for solutions that are more environmentally friendly, yet cost effective.
From diesel to hydraulic
Pile drivers have historically been diesel powered, but increased concerns on the hazards of diesel as an ecological pollutant have pushed a movement to replace diesel power with hydraulic power. Although this is a positive move, hydraulic oil does leak and is also considered a pollutant.
Added to that, neither diesel nor hydraulic hammers address the environmental impact on the surrounding community from the noise of hammering. Many cities have noise controls to limit the noise emission from construction sites, which will push construction companies to use quieter options.
Reducing vibrations
To reduce the noise from hammer piling, hydrostatic or vibration piling is preferred in residential and commercial office areas. This reduces complaints of noise and also brings down dust pollution, but then adds the environmental impact of excessive vibration.
In marine construction, this vibration affects aquatic life, prompting the U.S., Europe and Australasia to bring in strict regulatory measures to protect the marine ecosystem. This has created a trend for manufacturers to introduce piling machines with lower vibrations.
Making use of technology to develop intelligent piling
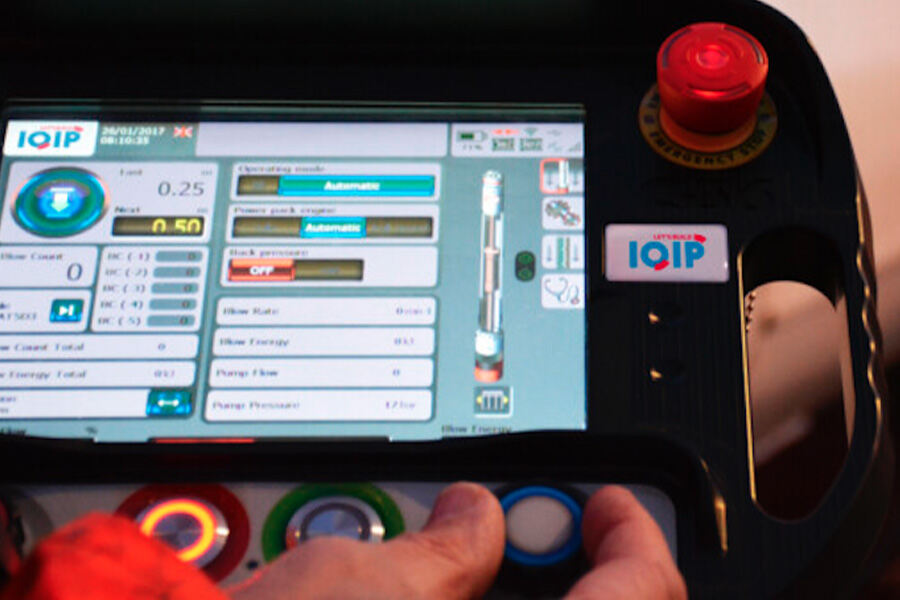
Manufacturers are leveraging technology to develop intelligent pile driving systems, to bring greater efficiencies in their machines. These innovations use advanced monitoring systems, Internet of Things (IoT), WiFi and remote access for control and reporting, and even GPSS systems for tracking. Some of the advanced applications include:
- WiFI connectivity features that provide immediate data communication between the operator and equipment to make adjustments quickly
- Advanced control systems and algorithms allow the operator to stay in control of piling, optimize the hammer energy and strike rate of the hammer in real time, to decrease energy consumption and increase efficiency of the machine
- With immediate data feedback, vibration and sound levels can be monitored
- Improved data and efficient reporting provide continuously monitoring of the piling process to detect any unstable movement and prevent equipment damages
- Biofuels and oils are more usable options to provide cleaner combustion
Embracing new methods of piling
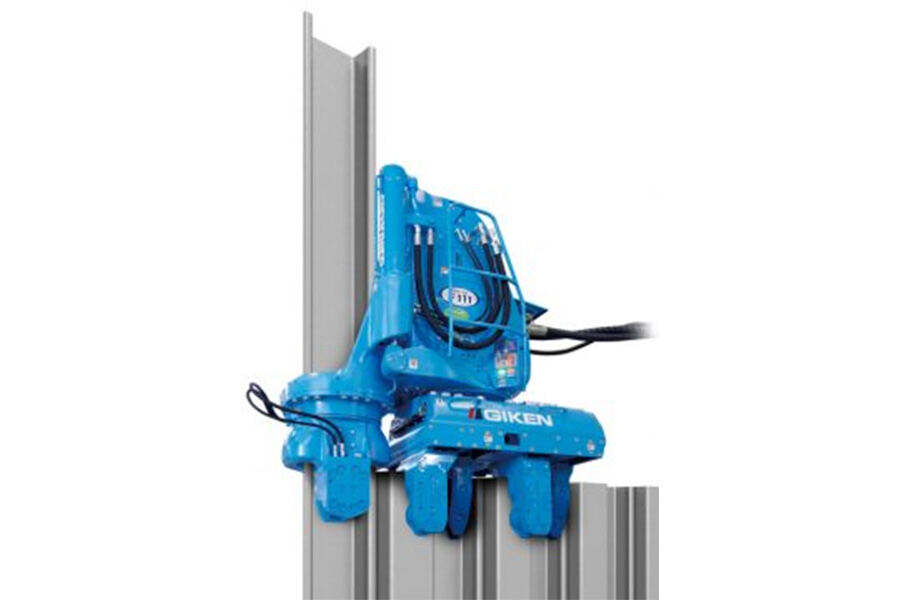
Press-in piling
Press-in piling uses a static penetration method that doesn’t create the same noise and vibration issues as the dynamic penetration methods of hammering or vibratory piling. Press-in piling is an innovative method to install sheet piles that is environmentally friendly and safer than other methods.
Press-in piling machines are compact and can operate in limited space. Sheet piles are installed using the reaction forces from fully installed piles to generate a static load and a press-in force instead of a dynamic force. This approach offers a noise and vibration free method of installing piling.
Vacuum evacuation (zero trim) piling
A new vacuum excavation technique for piling reduces noise and provides a safe approach to piling. Traditional concrete piling has the issue that concrete is overpoured and the excess concrete must then be broken out. This has health and safety issues for the workers and there are frequent injuries, as well as taking unnecessary time and effort. The method, also called a ‘zero trim’ method, involves sucking out the excess concrete while it is still wet, using a vacuum extraction technique that has not previously been applied to construction in this way. Zero trim uses less concrete, and the extracted concrete is used elsewhere on site as fill, saving on costs and environmental impact.
Final thoughts
The global demand for more residential and infrastructure construction also creates the need for more piling, with the consequential impact on the environment. Governmental regulations and overall environmental and ecological concerns are pushing the need for machines that are more efficient and more environmentally friendly.
The challenge for construction companies is that piling machines are very durable and do not need to be replaced frequently, can be purchased second hand and used for an extended machine life. Do those companies continue using the same approaches, and perhaps to find small step improvements in those methods, such as the switch from diesel to hydraulic, and then to keep pushing up against environmental groups and local complaints.
Alternatively will construction companies make the investment choices to embrace intelligent piling technology, to provide more control, better usage and cost efficiencies and be more environmentally acceptable? Or will they make the bigger change to embrace new piling methods, with new machines and piling structures? These are choices ahead for manufacturers and construction companies alike.