The global market is changing drastically with new technology coming in. For the plastic industry to stay in business, some things must change, and new technologies must be adopted.
For instance, according to research by Ellen Macarthur Foundation, only 14% of plastics are recycled using various recycling machines, meaning that more than 85% of plastics are left in our environment.
This article will focus on the latest trends in the plastic industry and the industry’s market share. Additionally, the article will discuss the expected growth of the plastic industry in the next three to five years.
Table of Contents
Overview of the global plastic industry market
Latest trends in the plastic industry
Conclusion
Overview of the global plastic industry market
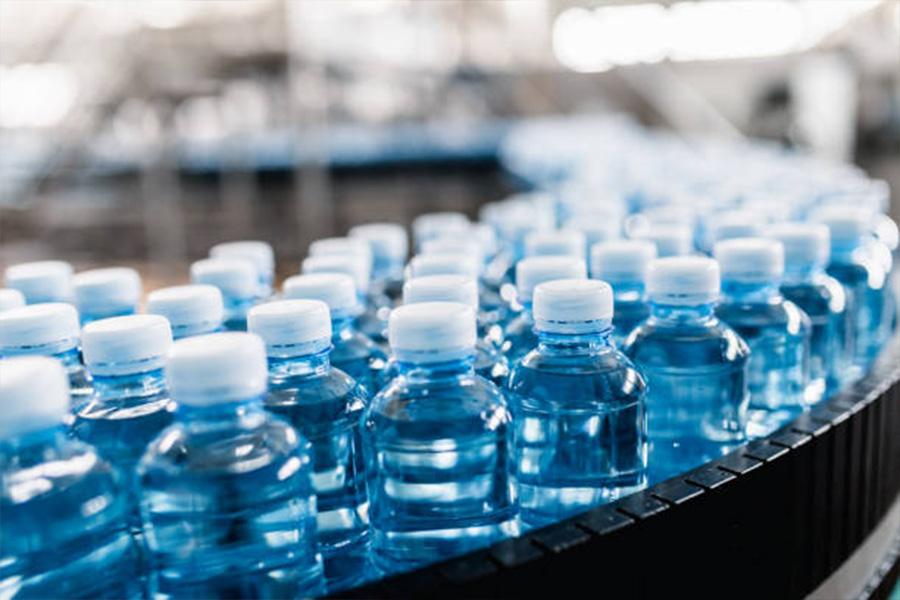
According to ReportLinker, the global plastic industry was estimated to be worth US $593 billion in 2021. It is predicted to expand at a compound annual growth rate (CAGR) of 3.7% between 2022 and 2030.
Rising demand from the electrical and electronics, automotive, building and construction industries continues to drive growth of the plastic industry market. Advanced industrial plastic machines are used to make plastic products in different parts of the world.
Currently, plastic is increasingly used as a substitute for steel and aluminum in the automotive industry due to legislation requiring that companies manufacture lighter vehicles to boost fuel efficiency and ultimately cut carbon emissions.
Latest trends in the plastic industry
High demand for plastics from the packaging industry
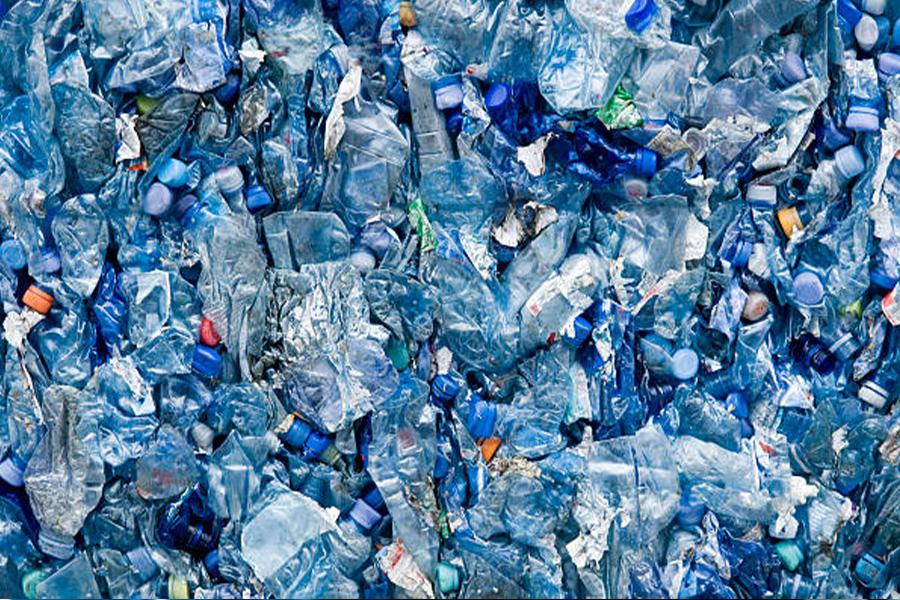
Most companies utilize plastic packaging because plastics enable a better product-to-packaging ratio due to their lightweight. Plastics are also resistant to scratching and impact, meaning there will be less waste from breakage.
Typically, glass is heavier than plastic. Companies that use glass packaging must take more trips transporting their packaged items, translating to greater environmental impact.
Most end consumers also prefer plastic packaging, which is easier to carry than glass. That is the reason why most plastic packaging companies in Europe and North America are under pressure to continue producing more plastic packaging.
Competitive landscape
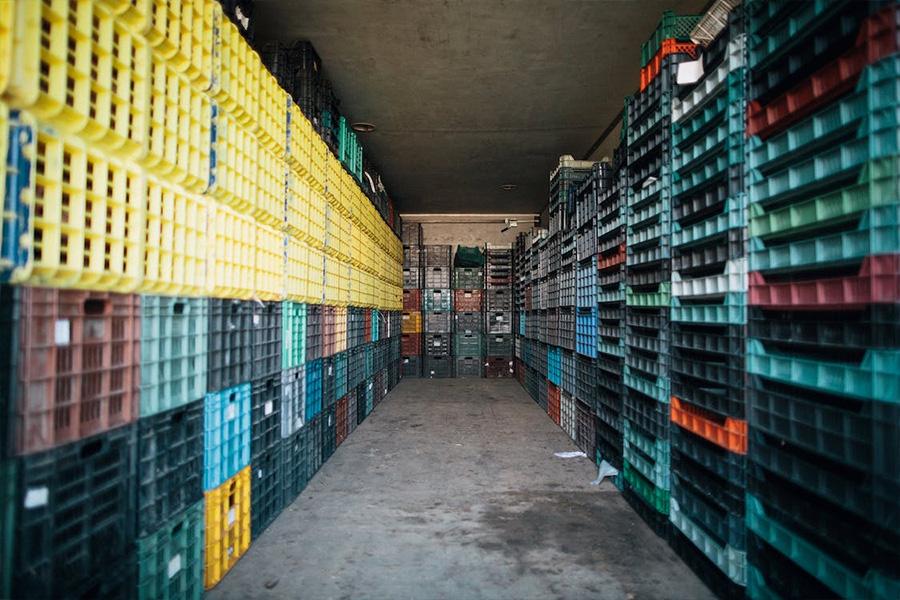
Several major companies, including Brown Machine Group and Haitian International Holding Limited, compete fiercely in the global market for plastic gear processing. These two companies have invested in R&D, allowing them to stay ahead of their competitors by consistently improving their products such as the blow moulding machine.
With the help of new products and strategic mergers, these companies have expanded their reach and pushed state-of-the-art technology forward. In September 2020, Engel Austria pushed the e-speed mould injection series down into the lower clamping force levels to cater to the needs of manufacturers of thin-walled containers, buckets, and matching lids.
The largest share is expected to be held by Asia-Pacific
As a rising economy in the Asia-Pacific region, China is experiencing meteoric growth in the amount of industrial activity. Industrial activity will demand high-performance components made from plastic for use in various end-user sectors. As a result, it will significantly boost the growth of the plastic industry.
It is anticipated that injection molding machinery will hold a considerable part of the market for the various types of plastic processing machinery. Several well-known companies, including Haitian International Holdings Limited, Cosmos Machinery Enterprises Limited, and The Chen Hsong Group, are expected to participate actively in this market.
Increased demand for low-carbon-footprint products
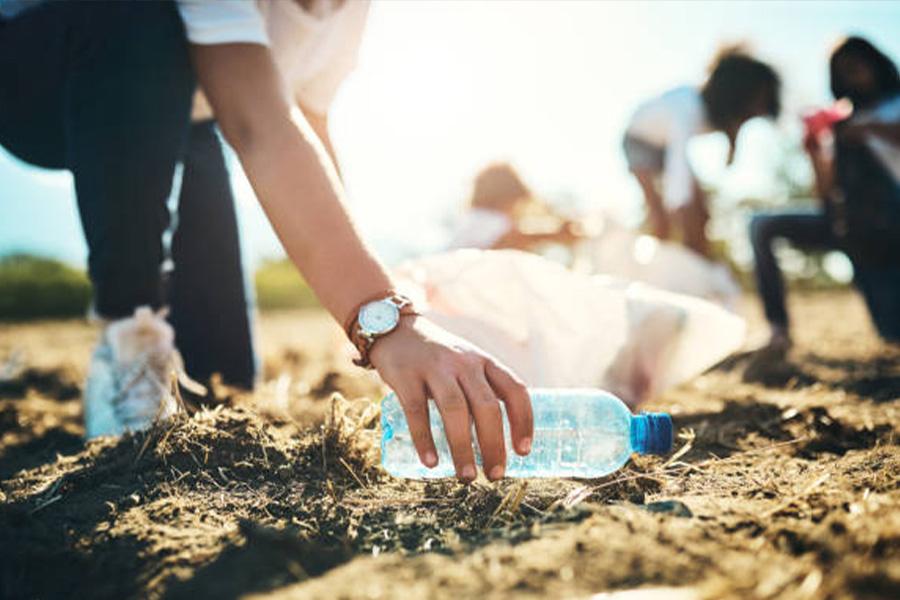
Consumer spending is increasingly predicated upon a growing understanding of how carbon emissions affect the supply chain and the environmental cost of purchasing disposable products at every stage of production and distribution.
The realization that people’s shopping patterns are shifting is encouraging. Today, consumers make the best purchase decisions by considering their personal carbon footprint.
According to research conducted by The Carbon Trust, 70% of consumers said they would also adhere to simple energy-saving recommendations if they were provided on the packaging to help them lower their overall carbon footprint.
Automation
Printing in 3D is slowly becoming an appealing alternative due to the high component production rate as well as better manageability of the production process. Furthermore, it allows the production of small batches of plastics without using a mould. When a mould is not used, production costs are reduced.
Automation has significantly boosted the efficiency of the molding process by allowing quicker production, better machine utilization, improving fabrication sustainability, and increasing workplace safety. While not every portion of the molding process can be automated, sorting, stacking, assembly, loading and unloading, and quality control can be automated.
Internet of Things
The vast amount of data that most packaging companies possess can, just like in any other industry, provide considerable opportunity to identify efficiency opportunities and uncover chances for improvement.
The Internet of Things is responsible for everything that falls under its purview, including:
- Integrated smart systems
- Sensors
- Analytics
- Data
The above features of IoT are meant to help packaging manufacturers make intelligent decisions, achieve efficiency, and automate their operations.
Digitization
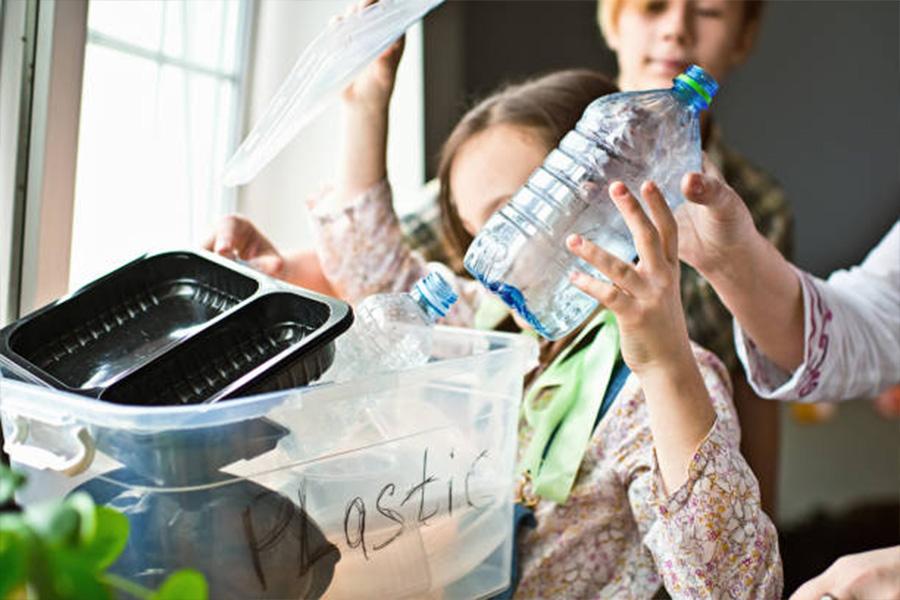
The rapid development of digitization opens up new prospects for mould technology, temperature control, and data processing conditions. The advancements in the information technology field have led to greater integration of process flow and increased transparency throughout production.
Recycling industries vastly benefit from digitization through efficiency building and creating consistency and quality in the process. Essentially, digitization bridges the demand-supply gap, helps in innovation, and creates a value chain.
Introducing new technologies including the use of a Manufacturing Execution System (MES) in plastic industries facilitates factors that lead to increased industrial productivity. These factors include: shorter setup and changeover times, reduced energy consumption, and improved product quality.
Conclusion
Since the global market is changing drastically and demand for plastic packaging is increasing, the plastics industry needs to embrace new technology to keep up with the high demand. Plastic companies can achieve this through automation of processes, digitization, and IoT.
Visit Alibaba.com to learn more about plastic packaging and receive the latest updates on the general plastic industry.