A critical step in creating a molded plastic product is determining the right manufacturing technique. Injection and blow molding are two standard procedures, each with their own pros and cons. Wholesalers and retailers in this domain should evaluate the market needs and stock the right machinery for their prospective clients.
Injection molding and blow molding are two methods to make plastic products quickly. They can both create plastic objects in various shapes and sizes. This article dives into the key differences between the two machines to help readers confidently select the right machine for their needs.
Table of Contents
The global market size of plastic processing machines
What is injection molding?
What is a plastic blowing machine?
Injection molding vs. blowing machines
Final words
The global market size of plastic processing machines
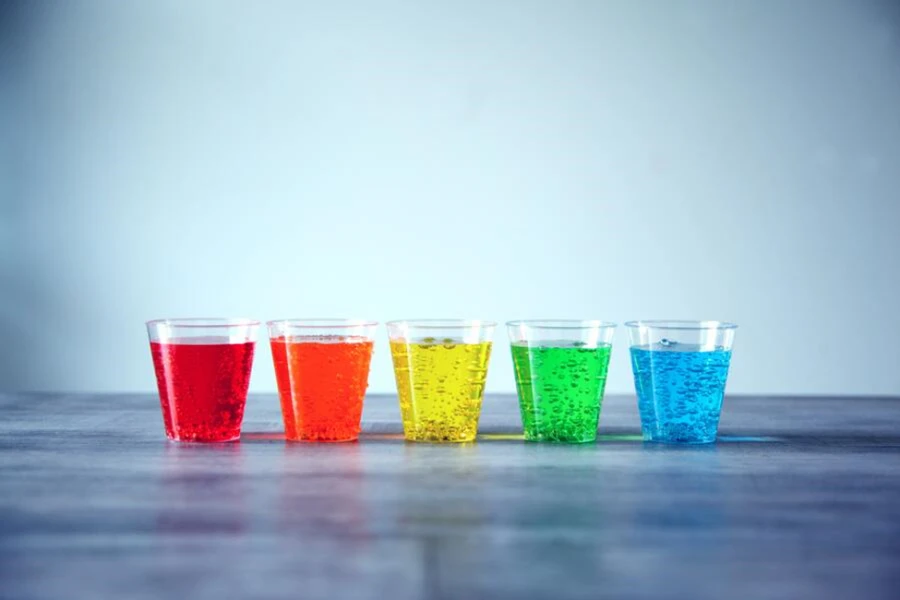
The market for machines used to process the plastic is divided into many categories like injection molding machinery, blow molding machinery, and extrusion machinery. The global market for plastic processing machinery is expanding rapidly because people are realizing the many advantages of plastic processing techniques, like the ability to create flexible designs. Industries such as food and beverage stand out for adopting this machinery at a large scale due to their needs for a range of plastic products.
The demand for plastic products is increasing, which leads to a greater need for plastic processing equipment. Developing countries are upgrading and modernizing their plastic processing plants, which drives the demand for machinery like injection molding machines. Technological advancements are also making the equipment more affordable in markets where price is a significant factor.
What is injection molding?
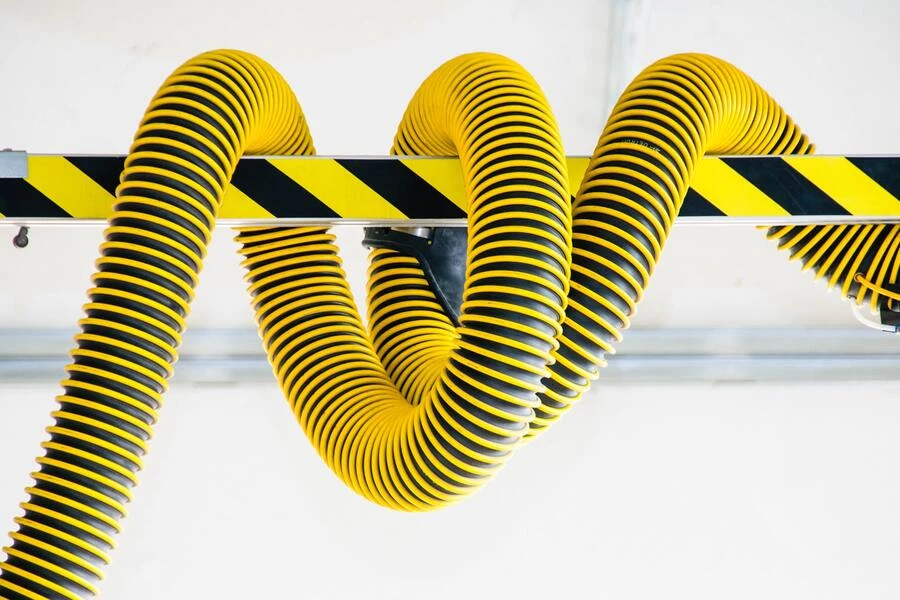
Injection molding involves creating solid plastic parts with precision models. The plastic is melted and pushed inside the cavity under pressure until the mold is full. Cooling water then flows through the channel to solidify the plastic, which is later ejected from the mold opening.
An injection molding system has attached channels from which the plastic flows. Flow rate and cavity capacity are maintained at the cross-section of these channels. It consists of two essentials – the injection and the ejection unit.
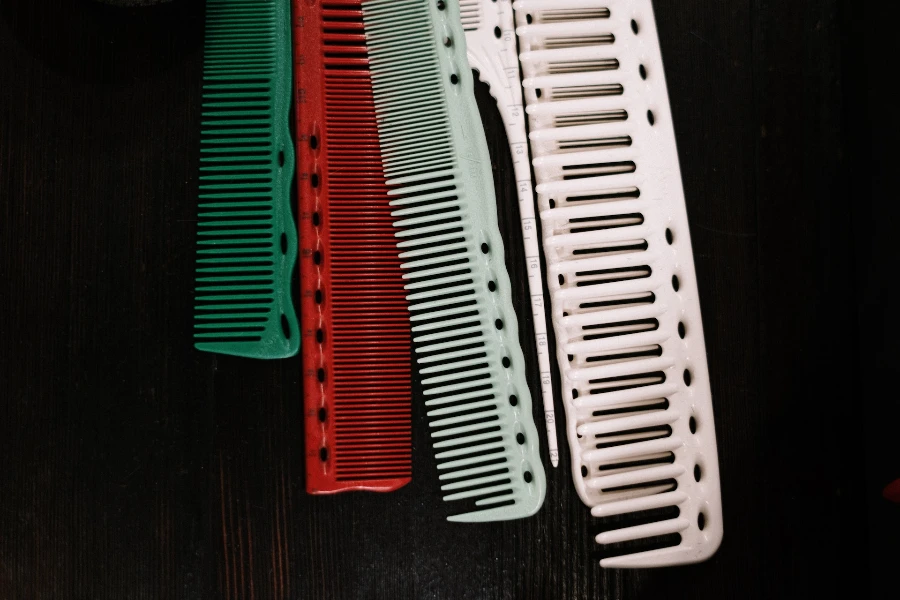
Injection molding is an excellent way to mass-produce customized, solid plastic products with its systematic structure. Its common uses are items that require high precision but are produced in bulk like combs, bottle caps, and plastic phone covers.
A few benefits of using injection molding are:
- Low labor costs
- Efficient and quick production
- Provides many color options and material flexibility
- Compatible with many high-precision materials
What is a plastic blowing machine?
Plastic blow molding is used to manufacture hollow and thin plastic materials. The process starts by heating raw plastic to a specific temperature according to the plastic type used. Next, an extrusion machine extrudes the hot plastic to create hollow tubes.
This parison or hollow tube is then placed in a mold where the air is blown. Consequently, the pipe expands in the mold and takes its shape. The plastic becomes solid when cooled and creates hollow parts according to the mold design.
Plastic blowing has three main types:
- Extrusion blow molding – There are two ways to do this: continuously or intermittently. The continuous keeps feeding the material to make the shape and cuts it off when it cools down. The intermittent method involves removing the shaped part before adding more material.
- Injection blow molding – A special rod is used to put the material into the mold. The material takes the shape of a test tube. Then, the air is blown into the material to make it take the form of a mold.
- Injection stretch blow molding – This combines injection molding and blow molding. First, a solid pre-form is made using injection molding. Then, the pre-form is heated, and the air is blown into it using a machine. This makes it take the desired shape.
Overall, blow molding is a highly functional and effective process. It is useful for making hollow and uniform products in industries like automotive, pharmaceuticals, and consumer products that require the production of bottles, tanks, etc.
Some benefits of using plastic blowing machines are:
- Requires low capital investment
- Offers excellent design flexibility
- Automated production reduces labor costs
- Multiple production methods
Injection molding vs. blowing machines
Understanding the differences between blow and injection molding can help retailers stock relevant products. Here is how each machine differs from the other in terms of:
Molding process
Injection molding involves sealing the plastic in an injection chamber and allowing it to pass through a readymade mold. Meanwhile, plastic blowing is the process that heats the plastic and lets it pass through an extrusion machine, where the air is blown to form hollow shapes.
Material consumption
Blow molding can make containers with thin walls, which means they use less material and are lighter than containers made by injection molding. This not only makes them more efficient but also reduces transportation costs.
Machine size and cost
Both injection and plastic blowing machines are large. However, the former tends to be more expensive due to the multiple forces involved.
Manufactured parts
Their application is the primary distinctive factor between the two machines. Plastic blowing machines are used to produce hollow parts while injection molding machines are used to create solid parts.
Material and color compatibility
Both production methods are compatible with a vast range of materials. The final machine selection depends on the complexity and properties of the desired product.
Blow molding is usually chosen for soft and flexible plastics. This includes Polypropylene (PP), Acrylonitrile Butadiene Styrene (ABS), Low-Density Polyethylene (LDPE), and High-Density Polyethylene (HDPE). Other materials like acrylic, urethane, and acetal are suitable for both injection molding and plastic blowing.
How to choose between plastic blowing and injection molding?
Knowing the differences between plastic blowing and injection molding is essential to ensure the right machine selection. The available capital and the desired products are major contributors to this decision. Injection molding, for example, is the right choice when the aim is to mass-produce solid plastic products that demand high precision. On the other hand, plastic blowing is the perfect pick when working with hollow parts like bottle caps or pipes.
Final words
Both blow and injection molding can produce massive quantities of uniform products. When investing in either, factors like material compatibility, cost, and process should be considered. Success in the market depends on properly scrutinizing current demands and partnering with manufacturers who can develop solutions for current challenges.