Table of Contents:
The evolution of prefab homes
Different types of prefab homes on the market
How to find the best prefab home
Not long ago the idea of pitching a prefabricated home to potential homeowners would have been a hard sell. But today, with some of the world’s top architects getting into the game, this is no longer the case. There has been a boom of creativity and innovation in the prefab housing industry, and the benefits of this spill over to prospective buyers.
Besides offering a variety of appealing designs, prefab, or ‘modular’ homes as they’re sometimes called, are faster to build, and tend to come at a lower price tag. This competitive edge owes a lot to how they are made, with much of the process happening in a factory setting. This gives architects access to novel methods of production that allow them a wider range of design possibilities.
With housing frames being constructed off-site, designers can capitalize on new technologies such as 3-D printing, while the modular construction process allows designers to combine aspects of conventional home design and layout with industry innovations in production that wouldn’t be feasible for on-site construction.
This factory-controlled production process also results in less waste, and allows for better construction oversight, which means they can be reproduced consistently and affordably at scale. Also, with the initial construction of prefab homes taking place under strictly controlled plant conditions, prefab homes can be built to the same codes and standards as traditionally built homes. The result is that prefab homes are not only more affordable than traditional homes, but they’re often better looking, and typically more sustainable, without any compromise on quality or safety.
The evolution of prefab homes
Although mobile homes are also built in factories, and so are technically also a type of prefab home, they were distinguished from modern prefab homes in 1976 when the prefab housing industry saw increased oversight and regulation.
Today, these new building codes and standards have given rise to a whole new era of beautiful, structurally sound manufactured homes that use eco-friendly materials to blend in with their environments.
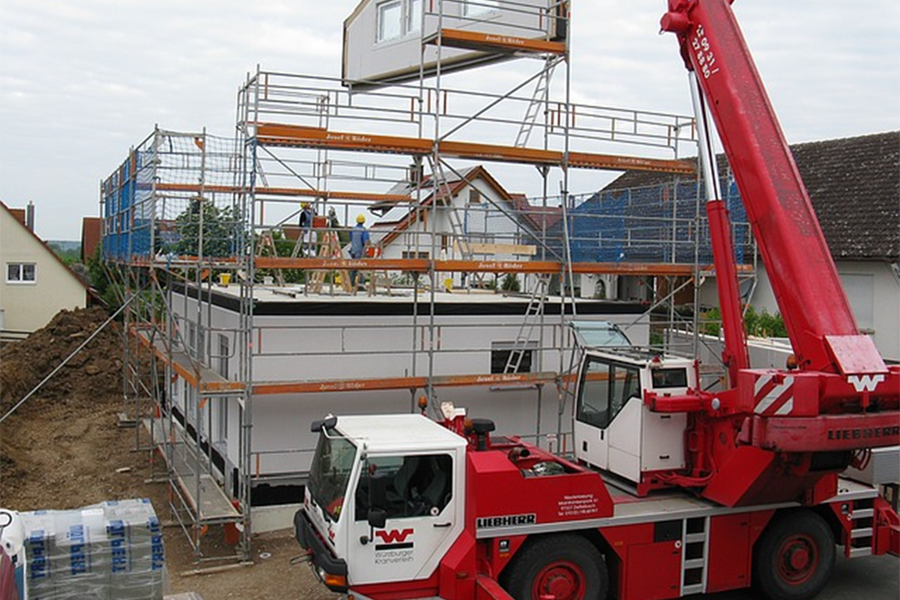
It’s also important to note that even though construction takes place in a factory, prefab homes are typically built according to the state and local building codes where the house will be built. Coming in customizable package options, prefab homes are able to match not only the quality of traditional houses, but also the diverse regulation standards.
For a list of the advantages of prefab homes, it’s worth considering that:
● They are greener than conventional homes because they generate less waste, reducing the demand for raw materials and the amount of energy used in the production process.
● They also have better energy efficiency overall, allowing homeowners to reduce their utility bills and carbon footprint.
● They offer improved air quality in homes because fabrication takes place in factory-controlled settings, limiting the potential concern of high moisture retention in the walls.
● They are budget-friendly because prefab companies can standardize production processes resulting in more affordable homes and a more straightforward building process for new homes.
● They offer a faster construction schedule because homes can be completed to code and using the same conventional materials in just half the time. For investors, this means that buildings can be occupied sooner, resulting in a faster return on investment.
● There are limitless design opportunities that can be customized to various tastes, or to fit in with the aesthetics of homeowner association requirements.
● Once assembled, prefab homes are virtually indistinguishable from their more traditional counterparts.
● And finally, prefabrication allows for a safer construction process reducing the risks of accidents and related liabilities for workers and homeowners.
Different types of prefab homes on the market
Prefab homes come in four major categories: manufactured, kit, modular, and shipping container homes.
1. Manufactured homes
Manufactured homes are made up of panels – a whole wall, for instance – that are then assembled by professionals, often with the use of heavy machinery, on-site. It’s for this reason that they’re also referred to as panelized homes. Since these houses are pieced together on-site, they require quite a bit of finishing work, such as painting and installation of flooring, cabinetry, and stairs.
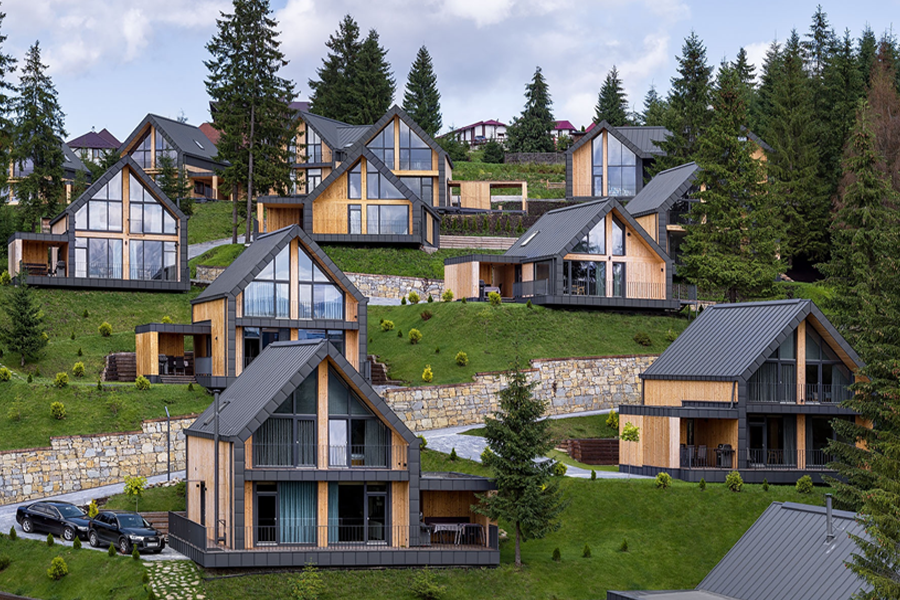
2. Kit homes
Kit, or pre-cut homes, follow a similar build to manufactured homes but feature simpler designs, such as log cabin kits or dome homes. They’re designed for motivated homeowners who’d like to DIY the assembly process using the materials and instructions supplied by the manufacturer.
The significant difference between kit and other prefab homes is that kit homes are typically less complicated to assemble. These homes are cut to design specs in-factory, and fit together much like a puzzle.
3. Modular homes
These are prefab homes where one or more modules are built in a factory. These homes feature much more personalization. This customization means there’s little finishing work to be done on-site as each module comes fully outfitted with interior fittings from plumbing and electrical wiring to closet doors and stairs. Modular homes differ from kit and manufactured homes in that they have an immovable foundation.
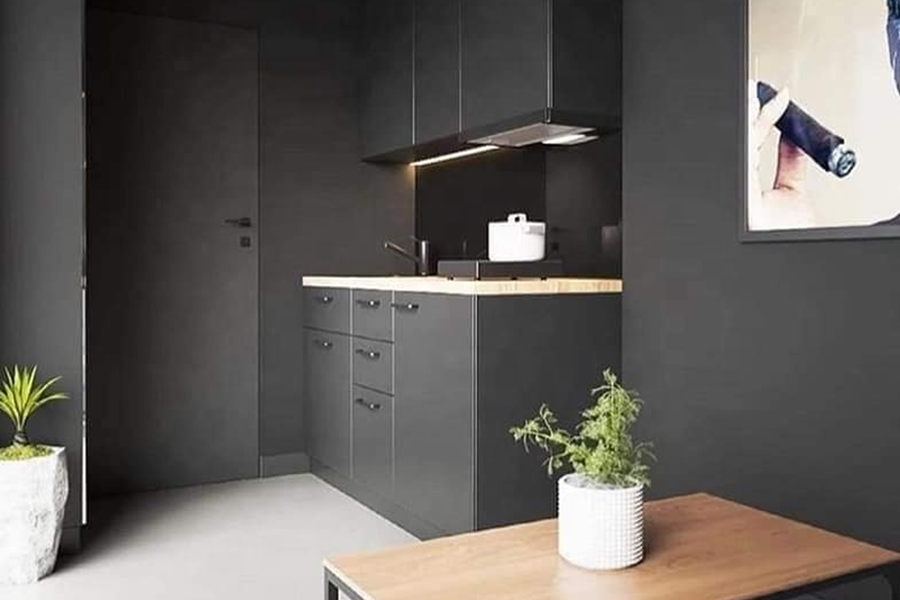
Modular homes can be designed for larger upscale housing developments thanks to stacking and multistory options. These allow designers to take advantage of height to create open living spaces. Modular prefab houses can also come custom with upgrades such as hardwood floors and marble countertops.
4. Shipping container homes
These homes are exactly what they sound like: homes made from steel shipping containers. Because of their versatility, shipping container homes have become popular, and are used by architects to create beautiful homes that really stand out.
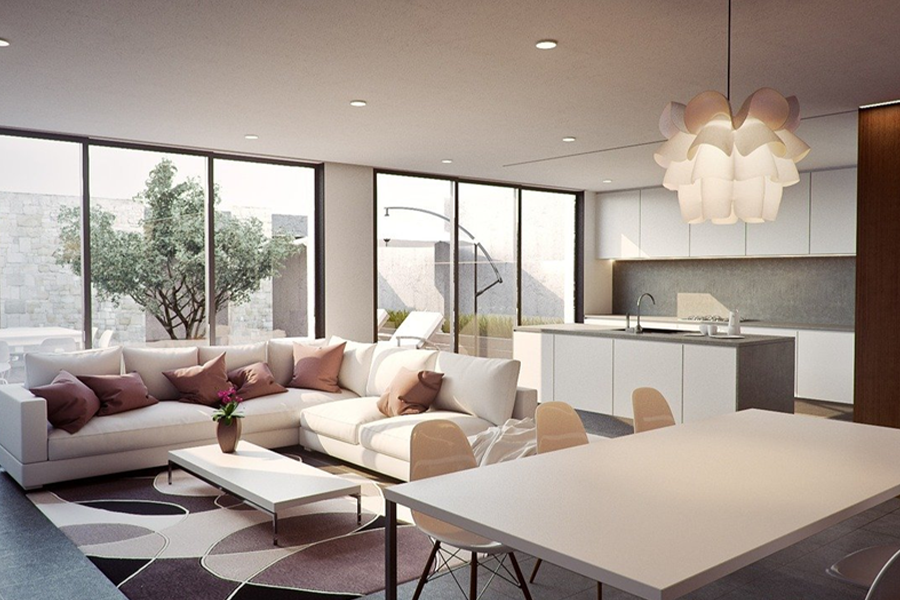
Contrary to how it may seem, it’s relatively easy to execute a shipping container home from design to construction on site. Also, there’s no limit to the form shipping container homes will take as they can be stacked together creatively, just like Lego bricks.
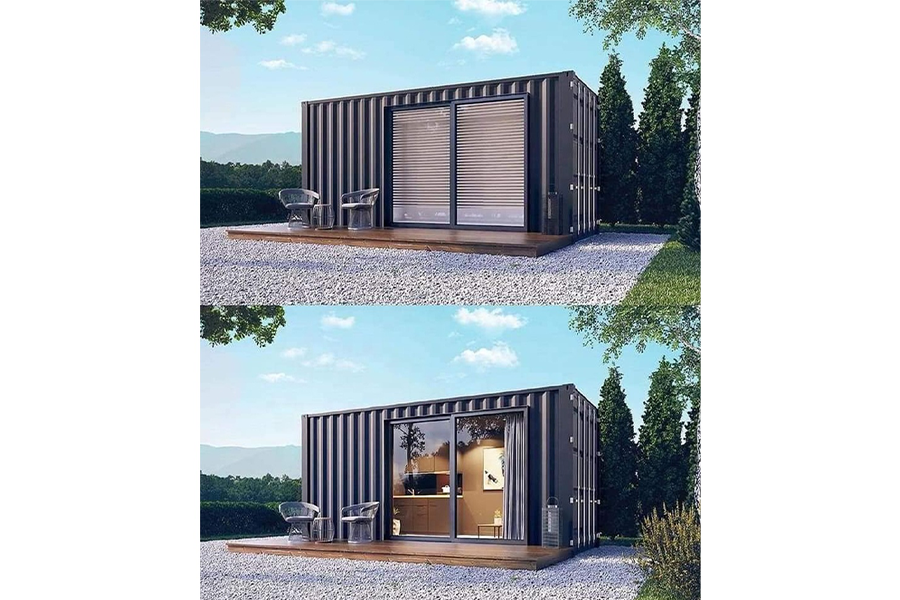
Container homes often come built with simple materials and minimalist designs. Skylights can be used to allow light to stream in from above, and paired with Large windows they can create a bright atmosphere indoors.
How to find the best prefab home
In order to make the best possible choice when choosing a prefab home, always pay close attention to what is and isn’t included in the overall housing package. This is because different companies have diverse features and fixtures in their home designs. Modular homes, for instance, can come with a full package of fixtures, including windows, flooring, and cabinetry. Kit homes, on the other hand, may come with just the necessary framing components, such as the walls and a roof.
Also, it’s important to understand that the base price of a prefab home doesn’t include features such as the foundation of the house, landscaping, and driveways.
Very interesting of prefab homes design I need more ideas about that can you help me
I would like to buy your beautiful container two bed room house with shower unit and toilet and wash bacon, and solar panels iwill need transportation to Philippines port of Zamboanga city and all the help I can get from you to make this project successful thank you from Charlie clay.
I like prefeb home. Because
It build in less time then other domestic constraints.
It is heat proof. It is very important in Gilgit Baltistan.
It it beautiful then othet.