MIG and TIG welding methods join metals by using an electric arc and shielding gas that create the weld. Although they are similar in many ways, they have features that distinguish them. Since each of these methods has its own pros and cons, it is important to have all the information before deciding on what method to use.
This article will highlight the key differences between MIG and TIG welding methods. Additionally, it will discuss their respective pros and cons.
Table of Contents
What is MIG welding?
What is TIG welding?
The difference between MIG and TIG welding
Conclusion
What is MIG welding?
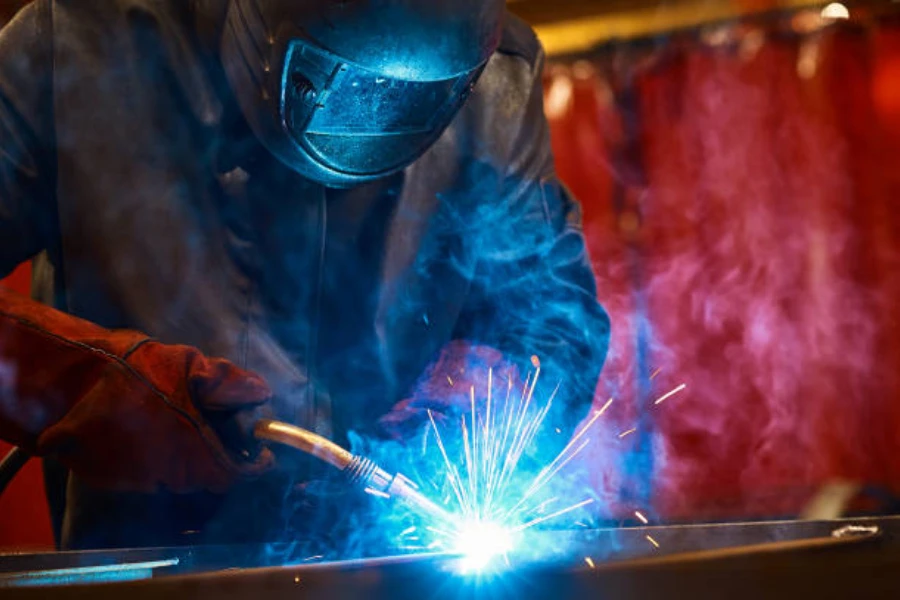
Metal inert gas welding is also called gas metal arc welding (GMAW). This process uses a semi-automatic or fully automatic arc to generate the weld with a consumable wire electrode filler material. It also employs a shielding gas to protect the weld, enhance weld penetration, and minimize weld bead porosity.
The shielding gas and electrode are fed through the welding torch or gun. A combination of the shielding gas includes 75% argon and 25% carbon dioxide. Other mixtures can be used depending on the materials in the welding process and other variables like the size and thickness of the workpieces. The diameter of the continuous consumable wire electrode varies according to the metal types being joined, joint configuration, and part thickness. The electrode is fed into the weld at a pace that is determined by the wire feed speed (WFS) settings to give enough weld to join the metal.
Pros
– Shorter production time for welds
– Lower costs as materials are readily available
– Easier to learn and weld at difficult angles
– Easier to create welds that need little to no cleaning and finishing
Cons
– Less durable welds due to less precision and strength
– Less aesthetically pleasing welds
– Harder to control the weld beads
– Welders require protection from fumes
What is TIG welding?
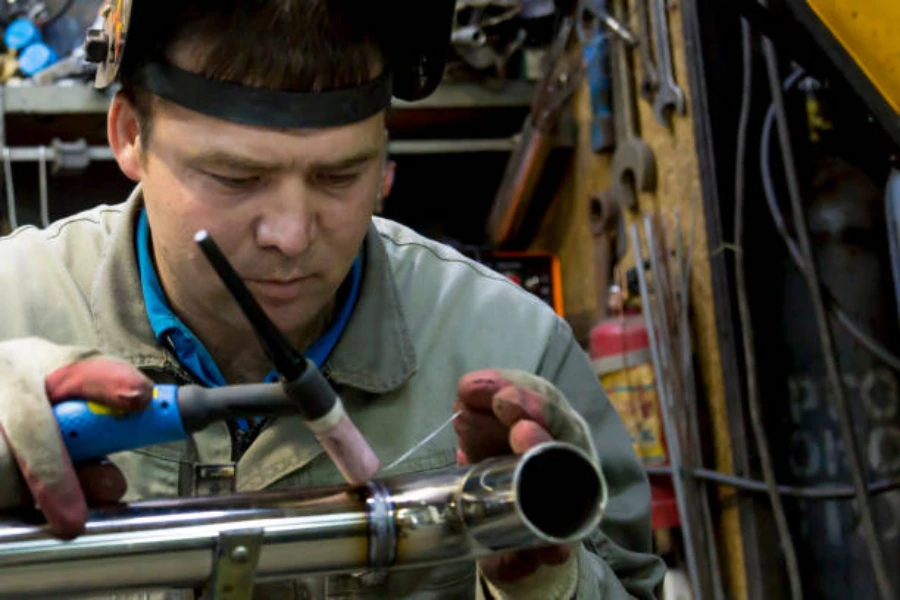
Tungsten inert gas welding is also called gas tungsten arc welding (GTAW). The process uses an arc and a non-consumable tungsten electrode together with a separate consumable filler material. This filler is a rod that is manually fed into the weld pool; thus both hands are used, where one holds the tungsten and the other, the filler rod.
The weld being made determines the composition and size of the filler rod. The TIG welding process uses a shielding gas that is 100% argon. Carbon dioxide is not used because it leads to tungsten oxide formation, which prematurely wears the electrode and contaminates the weld. This process also needs a foot pedal for the operator to control the amperage and adjust the heat during welding.
Pros
– Versatile welds capable of joining a broad range of thin and small metals
– More robust, aesthetically pleasing, and precise welds
– The filler material is optional
Cons
– Slower due to more preparation work, increasing production times
– Expensive process as it requires more components and time
– Hard to learn to deliver a precise and accurate weld
The difference between MIG and TIG welding
1. Cost
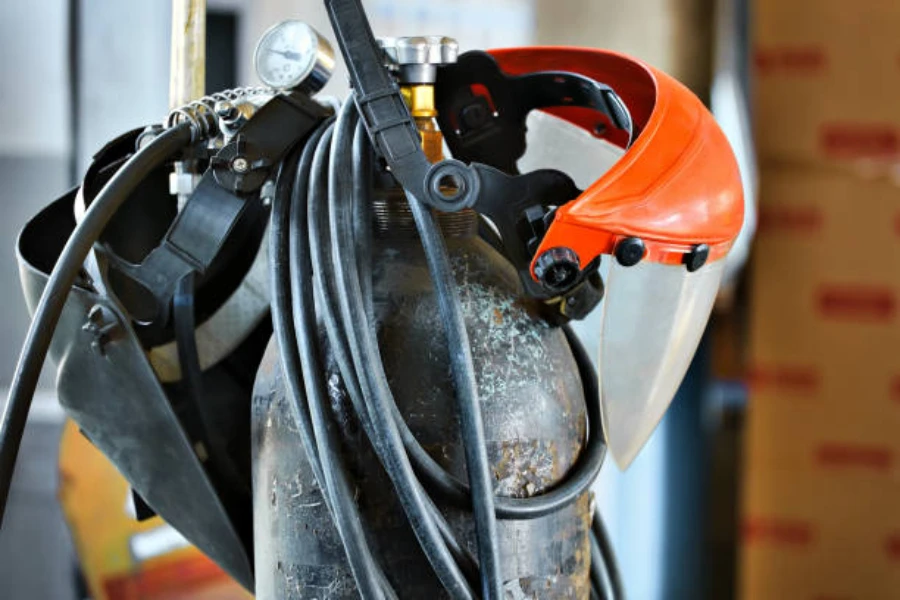
Considering the cost per foot of a bead, TIG welding costs more than MIG welding. There are lower deposition rates in TIG welds which need more experienced operators, who are costly to hire. The process also requires more preparation work, which raises the total cost. In addition, MIG welding supplies and equipment tend to be less expensive than in TIG. All these factors show that TIG welds are more costly compared to MIG welds.
2. Speed
The air-cooled MIG welders feed filler material automatically into the weld pool and have a broader and rounder arc that easily dissipates heat. As a result, the operators move the weld puddle faster while making longer runs without overheating.
On the other hand, TIG welders cannot supply enough filler rods to outdo MIG welding speeds as they cannot move the weld puddle as fast. Also, the air-cooled torches in TIG welding often get too hot during prolonged welding runs. Typically, they need to cool or be swapped for more expensive water-cooled torches.
3. Applicable material
There is a mild difference between TIG and MIG when it comes to material selection. Both arc welding methods are suited for a wide range of metals like carbon steel, aluminum, and stainless steel. However, TIG welding performs better with thin metals, while MIG welding is suitable for thick metals. Additionally, TIG welding offers better operational control, which limits the destruction of the workpiece.
4. Weld strength
TIG welds are stronger than those generated by MIG welding. This is because TIG welders create a narrow and focused arc that offers better penetration into the metal. Also, the TIG welds beads, if applied correctly, contain few holes and other possible defects that could weaken the weld.
Nonetheless, MIG welds can create strong welds with good metal penetration by cutting or grinding a V-shaped groove into the joint. This should be done before beginning the welding process to improve penetration. Additionally, a buyer can take advantage of good travel speed and torch to improve MIG welds’ strength.
5. Process difficulty
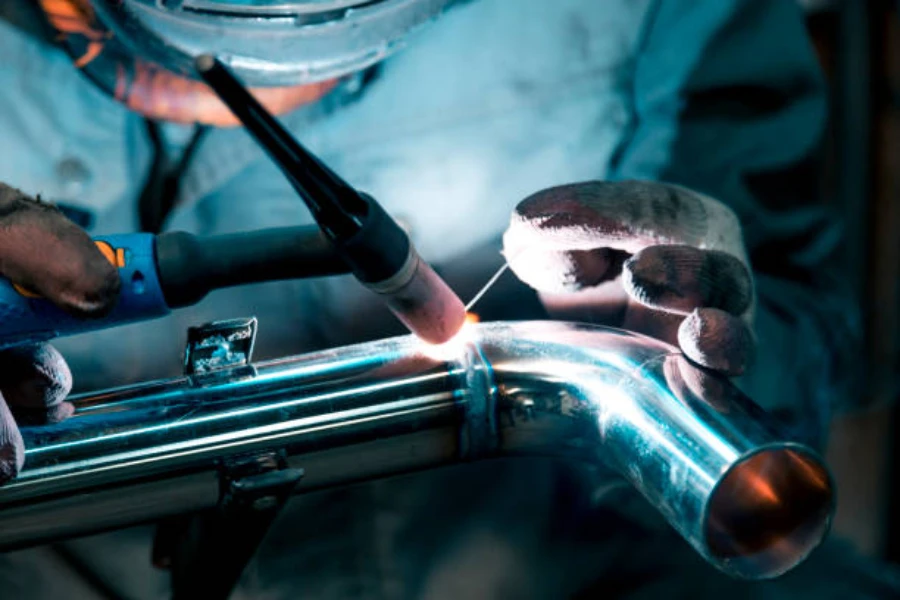
The MIG welding process is easier to learn as opposed to TIG welding. This is because TIG welding involves the use of two hands, where one moves the welding torch and the other feeds the filler rod into the weld pool. In addition, there is a foot pedal used to control the amperage. All these movements need to be synchronized to achieve the desired weld and thus might be difficult to master.
TIG is a more advanced welding process as the joined metals have to be cleaned and prepared well for the process. By contrast, MIG welding is easier to master. There is no foot pedal to control and the filler material is automatically fed into the welding gun, which requires only one hand to create the weld.
6. Electrode
The electrode used in either MIG or TIG differs. The MIG welding process uses a continuously fed consumable wire electrode when joining two pieces of metal. TIG, on the other hand, uses a non-consumable tungsten electrode together with a separate filler metal. As a result, buyers will use one hand to perform MIG welding as opposed to TIG, welding where they need to have one hand on the torch and the other on the filler material.
7. Power source
In MIG welding, a direct current (DC) source is used to create stability in the electric arc. The power also gives enough penetration of the metals. In contrast, TIG welding offers versatility as it can draw power from both alternating current (AC) and direct current (DC) power sources. However, the selection of the power depends on the metals to weld, the amount of spatter in the weld pool, and the desired electric arc.
8. Weld aesthetics
TIG welds exhibit better aesthetic qualities compared to MIG welds. TIG welds have little or no spatter that only requires light polishing to complete and remove discoloration. For instance, TIG welded coins are rendered the most aesthetically pleasing weld and can be used to make unpainted welds look better.
In contrast, MIG welds are less desirable in appearance. It requires experienced welders to create good-looking MIG weld beads. MIG welds are fine for applications where appearance is not considered that important. Additionally, aesthetics are not needed where the welds are to be coated to cover the appearance of the joint.
Conclusion
Clearly, both MIG and TIG can be deemed better than the other as both welding processes have advantages and disadvantages based on the circumstance of application. MIG is generally easier to learn and faster while TIG is deemed to produce higher-quality welds. Nevertheless, both cases might have exceptions and a buyer’s choice depends on the tasks being handled. Buyers should have the projects in mind and consider several factors like cost, type of material, equipment, and post-processing needs to make informed welding choices. To find quality equipment for welding, visit Alibaba.com.