The machine tool industry is ever-changing to facilitate the prudent production of standardized tools. From milling and molding to drilling and nibbling metal, these changes are affecting investment decisions by buyers. This is due to the sector’s great focus on increasing efficiency and decreasing downtime during operations.
This article walks you through the new trends and their benefits, which are a prerequisite for the sound selling of power-driven metal working machinery.
Table of Contents
The global market growth for machine tools
3 emerging trends shaping the present and future
Final word
The global market growth for machine tools
Machine tools have proved to be an unmixed blessing in the manufacturing processes of equipment. The industry’s global market size is currently valued at US$ 81.5 billion. It is expected to hit US$ 127.7 billion by 2030, growing at a CAGR rate of 5.7% during the forecast period. The key drivers of this growth include technological advancements in machine tools, such as robotic and multi-axis arms, as well as increasing demand for metal-forming tools.
In addition, the increasing demand for higher efficiency and precision in complex machining products, reduced lead time, and affordable industrial operating costs is likely to contribute to the market growth in bulk processing industries such as pharmaceuticals, paper, and textile.
3 emerging trends shaping the present and future
CNC software advancements
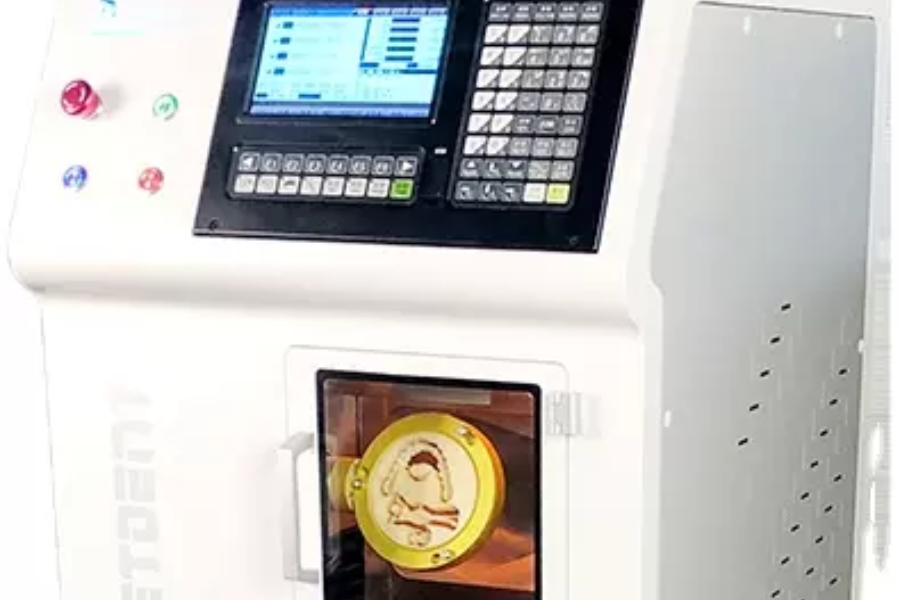
Modern industries demand more complex and precise machine tools for high-quality standards and protocols. The most common CNC software is the CAD/CAM integration. CAD, or computer-aided design, helps in creating 2D and 3D seamless design processes. Most designers use this software because of its speed and accuracy.
On the other hand, CAM, or computer-aided manufacturing, improves precision during manufacturing processes such as cutting, drilling, or milling by following the instructions on the codes. The CAM/CDM software package has greatly advanced over the years to become more efficient, accurate, and innovative workflows in metalworking tools.
Common CAD/CAM software integrations are:
Fusion 360
Fusion 360 is among the most renowned free CNC software for professional product and design manufacturing. It has both 3D CAD/CAM functionalities. Its computer-aided manufacturing software is ideal for milling and laser techniques.
Fusion 360 can connect your design to manufacturing techniques such as turning, turn-milling, probing and part inspection, 2.5-axis milling, 3-axis milling, and 4- and 5-axis simultaneous milling.
Still, you can use this software integration for data management and decision-making to strike a balance between performance and costs. With its prediction feature, you can predict the cost of manufacturing your design based on the production needs.
This software is applied by professionals across various fields, from electronic and mechanical engineers to industrial engineers and machinists.
EnRoute
Enjoying both CAD/CAM functionalities, EnRoute is an easy-to-use CNC software for textured paneling, cutting, creative designing, and metal and aluminum machining, among other manufacturing processes.
Its designs are ideal for use on knife-cutters, waterjets, plasma cutters, CNC router software, and lasers. EnRoute has realistic simulations that you can use to spot errors that might interfere with your design manufacturing. You can also use it to test different models for your manufacturing processes.
In addition, this software features precision editing tools that you can apply to enhance your shapes when drawing freehand.
Process automation
Process automation is the use of technological resources to optimize and standardize an industry’s operations. For a company to achieve sustainability, it’s crucial to get rid of bottlenecks while saving costs, enhancing efficiency and productivity, and increasing customer satisfaction and retention.
In order to achieve such bespoke, holistic benefits, there has been exponential growth in the world of automation. A case in point is the emergence of robotic process automation (RPA), which is steadily gaining a lot of steam. Most companies are looking to replace the repetitive and time-consuming nature of human resources. Further, the repetition of tasks hugely results in costly errors.
RPA’s ability to streamline processing by copying how humans perform is too promising to ignore. As RPA enters the next phase of its evolution, beware of the following three trends.
Intelligent automation (IA)
It combines RPA software with artificial intelligence (AI) and machine learning (ML) to automate the process of quality control. Incorporating AI and ML further solves common industry challenges like pattern identification and data analytics.
Center of Excellence (CoE)
Like in other industries over the globe, the adoption of RPA CoE in the machine tool industry will automate all the industrial functions using a single bot.
RPA as a Service (RPAaaS)
This model will eliminate the need for installing or licensing by outsourcing automation tasks to managed service providers (MSP).
Integration of 3D printing/additive manufacturing
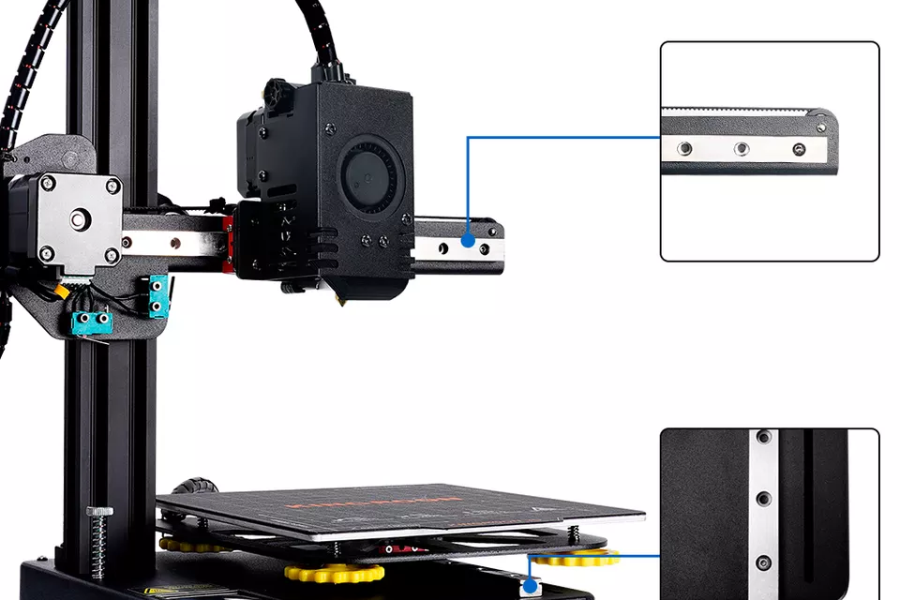
Still a buzzword in the 21st century, 3D printing, alias additive manufacturing, has become a part of the engineering sector as it has come down in cost and up in ease of use. 3D printers are used to create complex three-dimensional models and designs from a digital file by adding material layer by layer.
Various industries are embracing the 3D printing process because it has shorter lead times, high-quality prototypes, lower manufacturing risks, and ensures environmental sustainability. Industries like healthcare, construction, aerospace, defense, and automotive, among others, are key players in the adoption of additive manufacturing.
Examples of additive manufacturing include:
Material extrusion
Material extrusion using fused deposition modeling 3D printers works by melting plastic filament, mostly thermoplastic polymers, and depositing it in a bed to form layers. FDM has been used widely in the automobile industry to test models, lightweight tools, and final functional parts.
Other applications include;
– Chromating ABS parts
– Manufacturing short series of pieces
– Manufacturing parts at lower costs
Selective Laser Sintering (SLS)
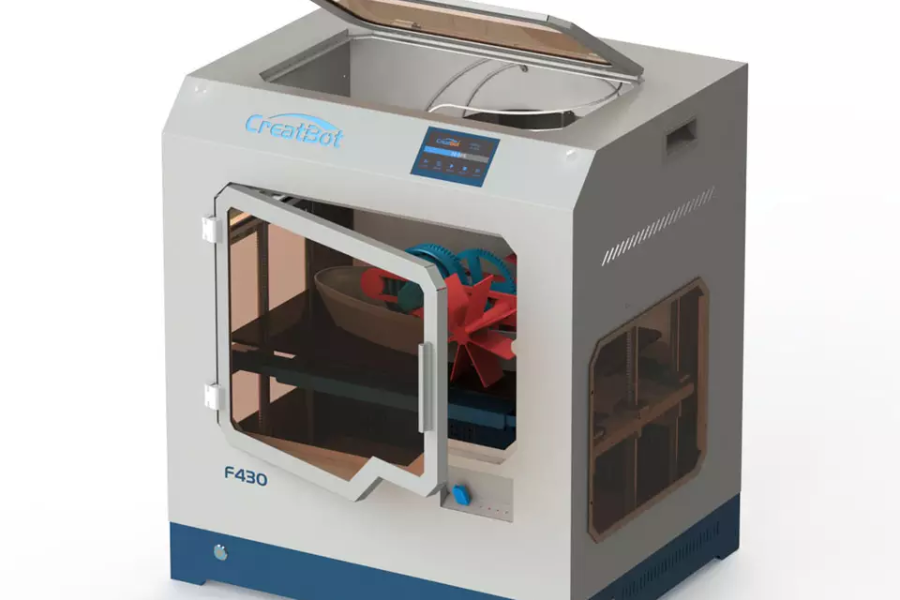
SLS uses a high-power laser to selectively fuse small particles of powder into different layers on the heated surface of a powder bed. This rapid manufacturing model is used in:
– Aerospace hardware
– Medical and healthcare
– Military hardware
– Homeland security
It is also great for:
– Automotive design
– Wind-tunnel test models
– Low-volume production and mass customization solutions
– Tooling and casting patterns
– Short-run end-use components
– Part consolidation exercises
3D printers have technologically advanced to enable mass production. Equally, there have been similar improvements in software, quality management, and design thinking.
Final word
In 2022 and beyond, it is vital to understand various profitable industrial trends to help you develop a sound business strategy in response.
Granted, the growth of the machine tool equipment industry will continue to cement itself as an essential milestone for improved efficiency. In this article, it is evident that automation will become easier by being guided by AI and ML.Industrial operators can control their equipment using advanced computer interfaces easily, eliminating the potential for human bias. Follow this guide to learn about the key machines used in metalworking that can give you an edge over your competitors.