Rubber products are used widely in industries and homes. From the manufacturing of aircraft and vehicle tires, to footwear, medical devices, and farm tools, the applications are numerous. Rubber-making machines play a central role in ensuring quality output.
The role of rubber product-making machines in industrial processing entails keeping raw rubber pure, cooling, and drying the final products. The demand for rubber product making machines is growing, given the many uses of rubber. Whether for small-scale plants or large enterprises, there are different models in the market for different businesses.
Explore the different rubber processing machine types available today and learn how to choose a suitable one.
Table of Contents
Market performance of rubber-making machines
Types of machines used in the rubber-making industry
How to choose a perfect rubber-making machine
The bottom line
Market performance of rubber-making machines
The rubber global market size estimate is US$ 40.77 billion. Market analysts project the market to hit the US$ 51.21 billion mark by 2027 at a 5.8% compound annual growth rate (CAGR). The high market value and upward trend arises from the wide range of rubber uses.
Rubber is a valuable raw material in the manufacturing and construction industry. Its resistance to abrasion, heat damage, and corrosive substances makes it popular in many industries. For example, it is useful in the automobile industry for tire manufacture, the fashion industry for footwear, and the medical industry for various medical devices.
The high demand has led to a corresponding need for rubber-making machines as manufacturers strive to meet the market demand. As more industries such as construction, packaging, and engineering embrace rubber, the global market for rubber-making machines is set to continue trending upwards.
Types of machines used in the rubber-making industry
Rubber undergoes different stages during manufacturing, such as mixing, moulding, and curing. Different machines are designed to process raw rubber to market-ready products. Here are the common types of rubber processing machines. ,
Compounding
Compounding is the first step in rubber processing. It involves mixing raw rubber with other chemicals to harden it and improve its quality. Rubber rolling mills or mixers help blend rubber with different additives to attain the desired appearance and composition.
When choosing compounding machines, choose automatic models to minimise labor costs and improve efficiency. In addition, the machine should have low noise and polished surfaces to avoid corrosion from chemicals and heat damage.
Extrusion
Extrusion machines help in moulding rubber to specific shaped products. An extrusion machine has two main parts, the die and sharing screw. The machine exerts a force on the rubber material and pushes it through the die, where it attains a new shape.
It’s advisable to select a machine with a touch screen control and automatic cooling system as these features improve efficiency and avoid wastage from vulcanization.
Vulcanization
Rubber vulcanization machines blend rubber with hardening materials like sulfur to improve its physical strength. A vulcanization machine subjects the rubber sulfur mixture to high temperature and pressure to vulcanize.
When choosing a vulcanizer, go for PLC and HMI control models and an automatic hydraulic system. The PLC ensures uniform heat distribution, while the automated hydraulic system improves efficiency. Modern designs have IR sensors to detect motion and monitor the internal temperature.
Calendering
Calendering helps in adjusting rubber thickness to the desired dimensions. Choose a rubber processing machine with adjustable rollers to obtain sheets with different thicknesses.
Also, check out the steel rolls coating. Chrome-coated rolls are more durable and produce aesthetically appealing sheets.
Latex processing
An efficient rubber processing machine should generate dry rubber in less than two seconds. Therefore, choose machines with a high speed and low power consumption.
The machine should also air dry and vulcanize rubber using steam. Check out the mould type and choose machine models made from porcelain or aluminum to avoid staining the rubber.
How to choose a perfect rubber-making machine
The following features are helpful when selecting a rubber-making machine.
Thermal solutions
Rubber has low thermal conductivity, but high temperatures can tanker with its quality. Choose a machine with advanced thermal spray technology for quality and efficiency.
In addition, the machine should save power, have high durability and be easy to install. Machines with microwave pre-heating systems are more efficient since they distribute heat uniformly.
Reliability
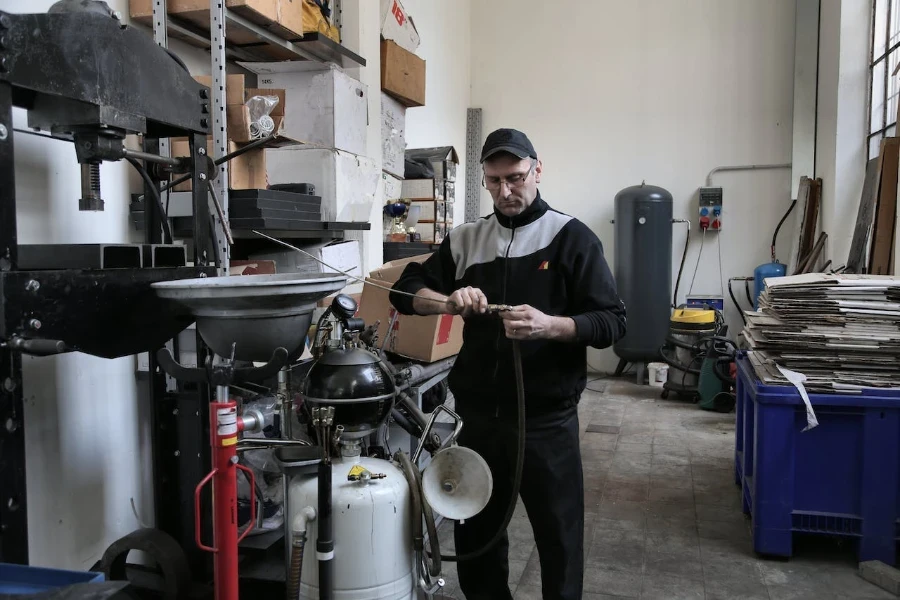
A reliable processing machine should have low maintenance costs, automated control, and adjustable speed. Delivering rubber without failure requires near to 100% reliability.
Examine the reliability rate of a processing machine by analyzing its subsystems and components, power requirements, and operation. Also, the maintenance rate for a reliable rubber machine is low.
Ease of installation
Installation affects a machine’s output. Therefore, pick an easy-to-install rubber processor to avoid failure while operating.
Besides this, choosing a machine that requires minimal human power to install saves time and money. It should require low cost and time, whether installing it for the first time or after repair.
Flexibility
Choose a machine model able to produce rubber sheets with varying thicknesses and sizes. It is easy to shift operations in a flexible processing machine, and in rubber making, the product is easy to modify.
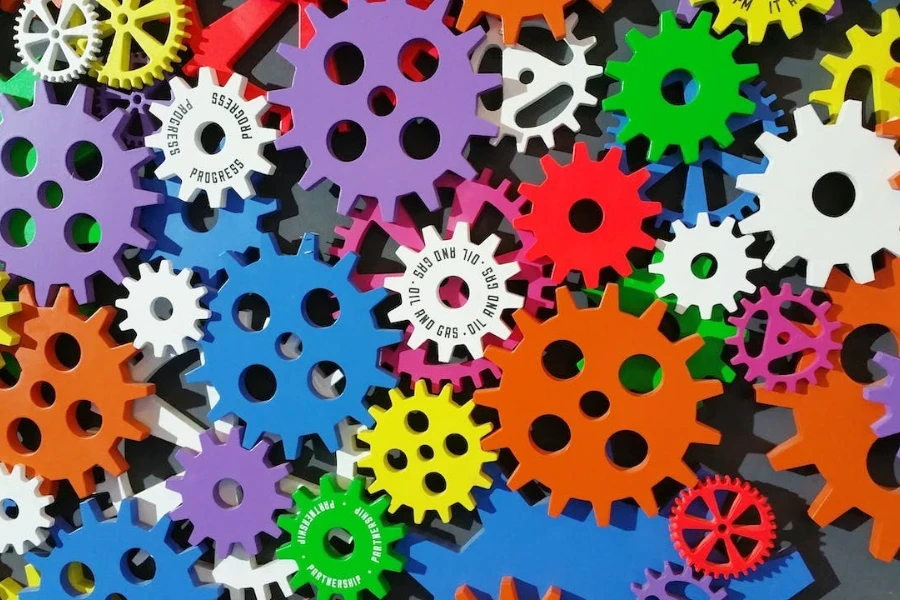
Advanced control
When choosing a rubber processing machine, go for models that can gauge different properties before and after curing. It should also analyze the rubber quality and notify of any need for adjustment.
Note that a machine with advanced control should detect any compounding problem in all processing stages.
Capacity and size of final products
Rubber is used widely in homes, medical, auto, and footwear industries. When choosing a rubber-making machine, consider the size of the final products. For example, rubber sheets for making vehicle tires are thick and large while those used in medical devices are smaller.
Therefore, choose a machine that meets the target output of products and their size.
The bottom line
Different businesses have varying needs when it comes to rubber processing machines. Some require large output, while others only require low quantities. Therefore, stock different machine models with the required features to meet customer needs.