With the world fully integrating into “green” living, the demand for plastic recycling equipment is increasing across many industries working with the material for various applications. Instead of disposing of these products, defective plastic materials can be shredded, melted, and repurposed for other end products.
There are many types of plastic recycling equipment that can be used to repurpose plastics and make them reusable for other products. From pelletizing extrusion lines and pelletizers to shredders and granulators, these machines can break down larger plastic pieces into smaller particles, which can be melted and then molded into a new product.
This guide will highlight the market for plastic recycling machinery, and then it will give a rundown of the top six pieces of equipment that buyers should know.
Table of Contents
The market for plastic recycling equipment
The musk-know plastic recycling equipment
What are the most common recycled plastics?
The benefits of using plastic recycling equipment
Conclusion
The market for plastic recycling equipment
The global plastic recycling machine market size is predicted to expand at a compound annual growth rate (CAGR) of 5.4% between 2022 and 2023. In addition, the plastic recycling machine market size is estimated to reach a valuation of US$ 481.2 million by 2031. Plastic recycling machines use advanced technology to recover scrap plastic materials and process it into useful products.
Modern plastic recycling machines can typically process any type of plastic material. And players in the market are focusing on manufacturing high-quality plastic recycling machinery to protect the environment from harmful effects caused by plastic waste.
These machines offer sustainability and efficiency. The recycled products are used in electrical and electronic components, clothing, furniture, automotive parts, containers, bottles, and the construction industry, generating profitable income for market contributors.
The must-know 6 plastic recycling equipment
Plastic granule machines
Granule machines are used for recycling polypropylene, polyethylene, and other types of polymers. It works with the aid of extruders to recycle and reclaim waste plastic so that it can be suitable for producing raw materials.
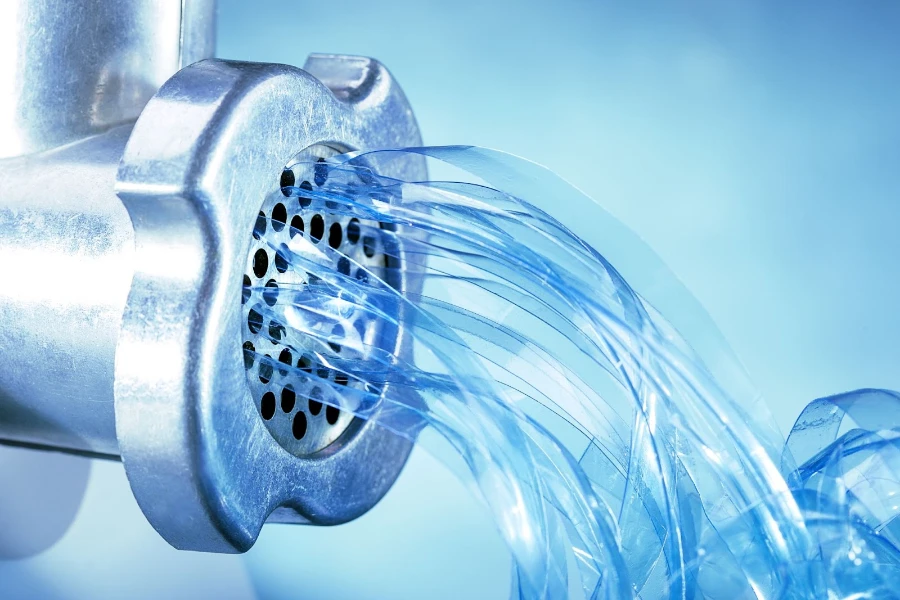
In the first stage, it uses its agglomerator or crushing machine to reduce used plastics’ size and material uniformity. After preprocessing the polymer, the product is then fed into the granulator to produce granule raw material.
Thanks to the special ceramic heaters, heat remains in the machine and initial warm-up time is minimized, and energy saving is constantly ensured. And the PLC control system can be used to control all the heat zones, cutters, and hourly capacity. The PLC also prevents errors caused by the operator.
Granule extruders come in different sizes of screen changers. For one, the nitrogen hydraulic unit changes the filter screen within less than a second. There’s also the granule die that has a pressure sensor. When the filter is filled up, the sensor will gauge the pressure and change it automatically.
Agglomeration machines
Agglomeration machines can physically transform loose plastic material into chips that can be used to feed the hopper of an extruder. The machines offer a cost-efficient process of recycling thin-walled polymers.
Agglomerators have two rotating blades at the bottom to create heat and friction. The process causes plastic materials to reach a softening point. In this stage, the operator will have to add some water to create some kind of shock.
After water evaporates, the material comes out from the operated discharge door as chips. Additionally, agglomerators can operate as material driers and densifiers.
Plastic crushing machines granulators
Crushing machines are crucial equipment for recycling. They grind waste plastics such as PVC, ABS, PE, PP, PET, rubber, PS, and PC waste materials. Depending on the customer’s request, plastic crushers produce between 300 to 1500 mm rotor sizes that have a capacity between 100 kg/hr to 2000 kg/hr.
Furthermore, the machine has a plastic granulator with fixed and rotary blades positioned to create scissor movement. It has a maximum capacity to prevent dust, heat, and sound pollution. Crushers are also produced with heavy-duty tough MIG welding methods and heavy-duty bearings to absorb the vibrations and shocks caused by the crushing.
Cutter compactor plastic recycling pelletizing system
This compacting and pelletizing system is another recycling plastic equipment to work with. It combines the function of compacting, crushing, pelletizing, and plasticization into one single step. The system is an efficient and reliable solution for plastic filaments, raffias, woven bags, and foaming materials.
Conical granule machines
Conical granule extruders are a piece of equipment used for recycling polyethylene film and related materials. Its screw shape design has made it possible to recycle plastics directly, even without preprocessing such as agglomeration or crushing.
In addition, the machine can recycle loose materials, such as shopping bag clippings, and transform them into pellets by using its conical granule extruders. Likewise, it melts plastic materials by extrusion and filtering using a melt filter. So it’s a very simple and effective way of recycling bulk plastic material, specificly manufacturer’s waste.
Plastic micronizer machine
This machine can convert plastic resins, such as flakes or pellets, into powder form. The plastic resin must be in powder form to produce final products. For example, the rotational molding process must contain micron-level powder resin to manufacture products like drums, containers, and water tanks.
Plastic micronizing machines are created to start this process. The machine converts plastic resin using circular rotating and statuary blades to process it. The high-speed rotating blade has a statuary counter blade that grinds plastic resin into a fine powder, perfect for plastic recycling.
What are the most common recycled plastics?
Virtually all plastics are recyclable. It is essential to recycle these plastics to create a healthy environment. However, here are the common types of plastic that can be recycled.
Polyvinyl chloride (PVC)
Polyvinyl chloride is a thermoplastic used for producing pipes, wires, bottles, and clings films. This type of plastic is renewable.
Polyethylene terephthalate (PET)
Polyethylene terephthalate is another commonly used thermoplastic. It is thin and perfect for low-pressure manufacturing products. Materials like clothing fibers and soft drink bottles are recyclable products made from PET.
High-density polyethylene (HDPE)
High-density polyethylene is also a thermoplastic. However, it is softer and more flexible compared to PET and PVC. Examples of products made from HDPE are gallons and pipes, which are commonly recyclable.
Low-density polyethylene (LDPE)
Low-density polyethylene is the direct opposite of HDPE. It is generally used to manufacture plastic bags. However, this plastic material isn’t easily recyclable. So, instead of recycling, it can be cleaned and reused for other purposes.
The benefits of using plastic recycling equipment
Many may wonder if using plastic recycling equipment is worth it when these plastics can be easily reused for other purposes. But overall plastic recycling equipment is valuable for its economic, health, and environmental benefits. The advantages of using plastic recycling equipment are described below.
- It requires less energy to produce plastics and helps conserve natural resources.
- It relieves the demand on fossil fuel consumption. For example, a ton of recycled plastic saves about 7,200 kilowatt-hours of electricity – about the same amount of energy to run a household for seven months.
- It goes a long way in conserving the environment.
- It promotes sustainability.
- It makes it cheaper for companies to use recycled plastics.
Conclusion
With technological advancements in plastic recycling, the idea of waste management is gradually gaining ground. Today, it has become easy to recycle plastic, even at an industrial level. As a result of this, companies are finally embracing the idea of a green environment due to the ease of recycling plastic with technology.
Furthermore, if businesses around the world integrate plastic recycling and reuse strategies in their waste management approach, it’ll be a big step towards protecting and preserving our precious environment. Implementing the use of efficient plastic recycling equipment will make this a whole lot more accomplishable.