Pharmaceutical granulators convert powder mixtures into free-flowing granules used in solid dosage production. These granulators come with plenty of advantages, such as sample cost reduction. Plenty of samples can be collected from a single batch of ingredients by using granulators.
For those in the market for pharmaceutical granulators, there are many models available, making it hard to source the ideal one.
This guide will walk buyers through the different types of pharmaceutical granulators available, and it will offer key tips to help them source the perfect model. The article will also discuss the market share, size, and demand for pharmaceutical granulators.
Table of Contents
Market share for pharmaceutical granulators
Types of pharmaceutical granulators
How to choose the perfect pharmaceutical granulator
Summary
Market share for pharmaceutical granulators
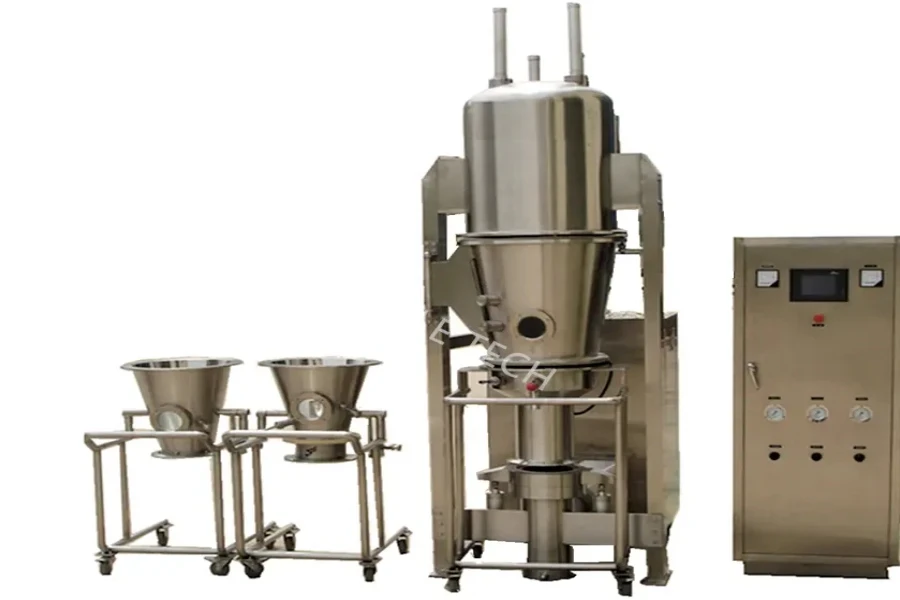
The pharmaceutical granulators market is segmented based on types, mechanisms, applications, and regions. There has been a growth in clinical trials, augmented by the rising healthcare research and development. An investment of about USD 83 billion in research and development in 2021 has resulted in various drug trials, which have driven the growth in demand for pharmaceutical granulators.
Mordor Intelligence reported a continuous annual growth rate estimate of 5.5% during the 2022-2027 forecast period. Having gone through a tough phase during the COVID-19 pandemic, most pharmaceutical players focus on creating new drug molecules or leads to treat the disease. As a result, the need for pharmaceutical granulation equipment has risen to meet the demand for new drugs.
Generally, the pharmaceutical sector is anticipated to hold a significant market share during the forecast period. This is due to advancements in technology and science. For instance, there was a development of 7,000 new drugs, which cost around USD 2.6 million. Regionally, North America is set to dominate the market due to increasing initiatives and investments by public and private entities. This market has several key players, including Alexanderwerk, Syntegon Technology GmbH, and GEA Group.
Types of pharmaceutical granulators
1. Wet granulators
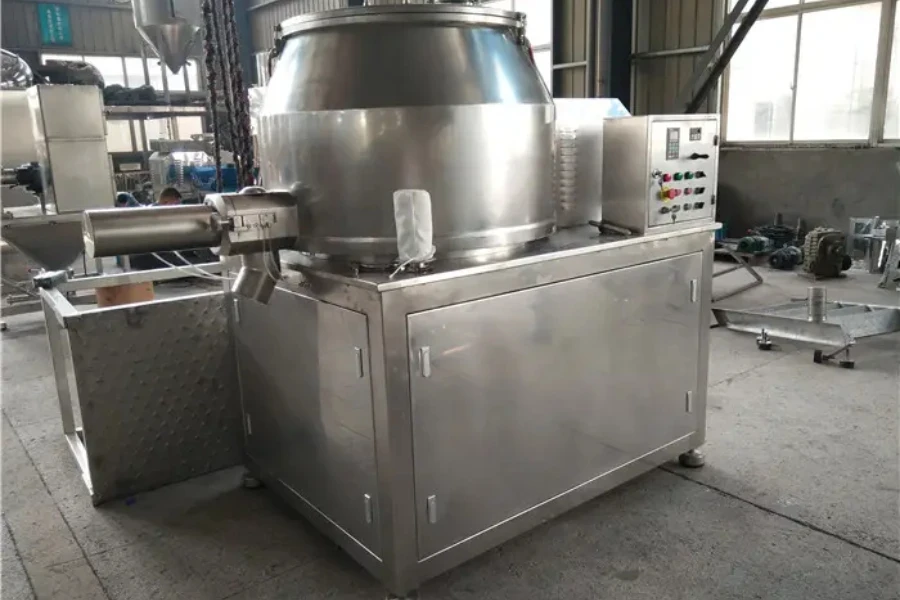
Wet granulation equipment is used in the chemical and pharmaceutical industries to change powdered substances into granules. The machines mix powder over a liquid binding agent, which gives a wet mass. This wet mass is forced via a sieve or screen to make the desired size of granules.
Two types of wet granulators are available: fluid-bed and high-shear granulators. Fluid-bed granulation machines use a stream of air to fluidize the wet mass to make granules. In contrast, the high-shear granulators use a high-speed chopper or impeller to mix and granulate the wet mass. These machines are also used in food and agricultural industries to create uniform granules from powders, crystals, and other cohesive substances.
2. Dry granulators
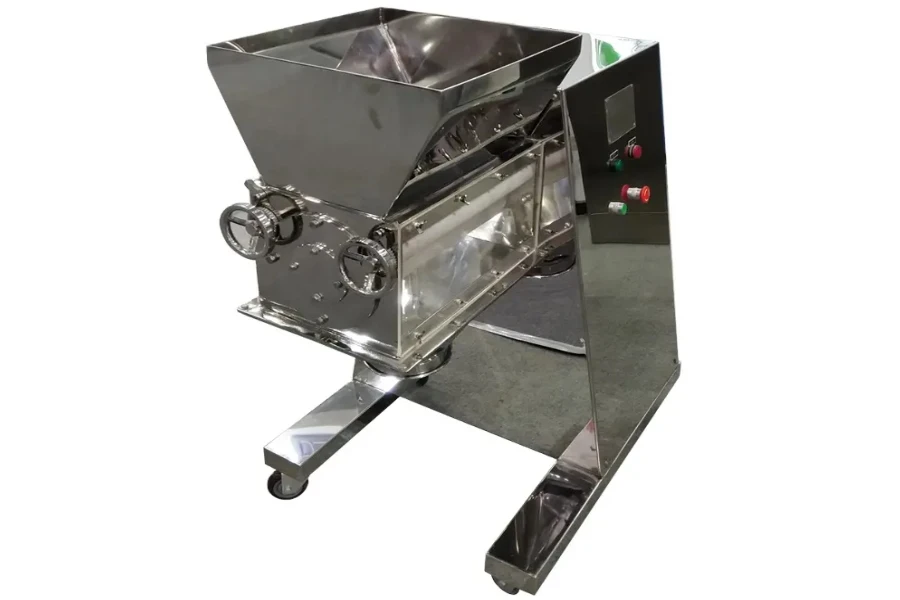
Dry granulators are machines that convert powder particles into denser, larger granules without applying liquid binders. They are also called dry or roller compactors, as they compress the powder between rollers, which compact and press the powder into a solid sheet. Granules are created as the compacted sheet is broken down into smaller particles by passing through a crushing or milling device.
The two main types of dry granulators include single-roller and double-roller compactors. Single-roller dry granulators use a single roller, which revolves against a flat surface, whilst the double-roller compactors contain two rollers that revolve against each other. They are widely applied in the food, pharmaceutical, and chemical industries.
3. Melt granulators
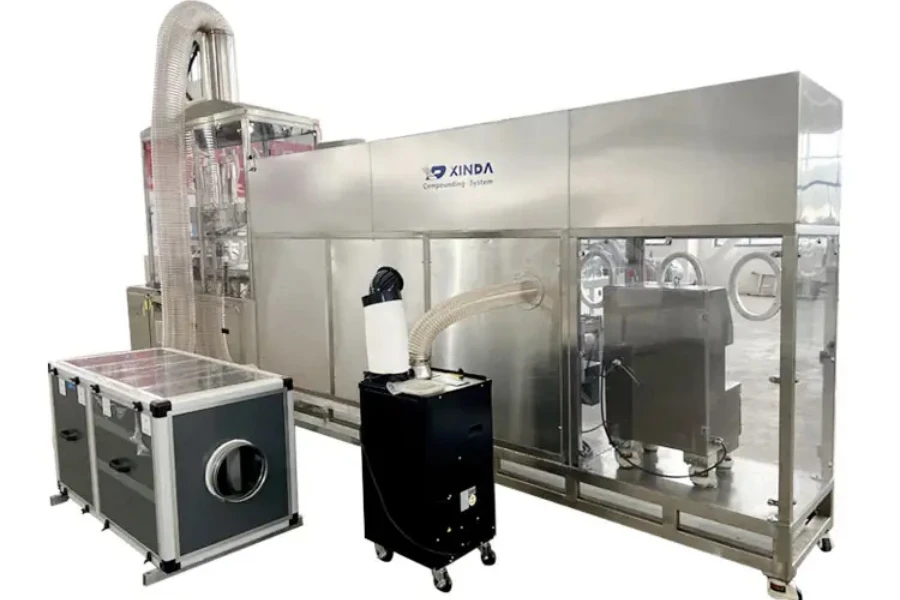
Melt granulators are machines used to create granules by melting and solidifying substances. They achieve this via a die to make strands or pellets, which are cooled and solidified to create granules. The machines generally have a rotor or heated screw that melts the material while mixing. A screen or die shapes the resulting material into pellets or strands. The cooling system solidifies the strands into granules.
Some melt granulators have additional components like vacuum systems or granule sizing units. These machines are commonly used in the plastic industry to convert polymers into granules. Additionally, they are applied in the chemical and pharmaceutical industries to produce granules from thermo-sensitive substances.
How to choose the perfect pharmaceutical granulator
1. Materials to be used
The characteristics of the material to be processed are important when selecting pharmaceutical granulation equipment. This boils down to the shape, size, density of the material, and the required particle size distribution and throughput. Oscillating granulators are suited for brittle materials like granules and crystals. High-shear granulation equipment is used on difficult-to-mix materials like sticky or cohesive powders. On the other hand, the fluidized bed granulators are suitable for heat-sensitive or pro-agglomeration materials. Generally, the granulator should effectively process the material to give quality and consistency to the finished product.
2. Production capacity
Considering the production capacity of pharmaceutical granulators, there are factors that buyers should keep in mind. They include the amount of material to be processed, desired particle size distribution, and the needed throughput. The laboratory-scale granulators are designed for small-scale production or research and development purposes. They have a low throughput and produce from a few grams to up to several kilograms per hour of material. Pilot-scale granulators are relatively small but are used in large-scale production for clinical trials and commercial production. Production-scale granulators handle high-volume materials in large-scale commercial production.
3. Cost
Under cost, buyers should look at the needed throughput and the type of material being granulated. Generally, the equipment ownership cost includes energy consumption, accessories, and maintenance costs. Low-priced granulators seem cost-effective but may become more expensive due to high operational costs and short lifespan. Buyers should evaluate the totality of ownership costs over the estimated service life of granulation equipment. On average, pharmaceutical granulators’ cost falls between USD 5,000 and USD 100,000.
4. Space available
Buyers should consider the granulator layout and physical footprint in relation to the available space. The design and size of the granulation equipment show whether it fits in the available space and space for maintenance and operators’ access. Oscillating granulators have a small footprint; thus, they are suitable for limited space. In contrast, fluid-bed and high-shear granulators are large and need more space. Notably, the type of discharge mechanism affects the needed space. For instance, whether the granulator discharges into a bin or via a separate discharge chute. Buyers can liaise with the manufacturers to acquire machines with specifications that fit in the available space.
5. Quality
The selection of pharmaceutical granulators based on quality takes into account the setup and primary design of the machine. Additionally, factors like construction materials and workmanship quality should be considered. This ensures the equipment meets the quality standards and regulations of the pharmaceutical industry. The machines should be easy to clean and maintain to reduce contamination risks. Also, the workmanship quality shows the equipment’s ability to meet the needed specifications and tolerances.
6. Durability
The durability of granulation machines depends on the construction materials, design, and workmanship quality. This determines whether the granulators are built for longevity and can withstand rigorous pharmaceutical industry operations. Usually, stainless steel is used in the construction of pharmaceutical granulators as they can easily resist corrosion and possess the ability to withstand repeatable sterilization and cleaning. Also, the design should be suited for various granulation processes, which include the particle size to be achieved, distribution, and the features of the starting substances. All these features should guarantee that the equipment is built to last and meets the quality regulatory standards.
Summary
Buyers should carefully evaluate the available options of granulation equipment to identify the ones that meet their specific production needs. The above guide highlights the most important factors to be taken into account. Additionally, they should consider the ease of use and regulatory compliance. Ultimately, the appropriate granulator should offer consistent performance, high-quality products, and efficient operation. To find the desired quality of pharmaceutical granulation equipment, visit Alibaba.com.