Most contractors and industries use grinding machines to smooth surfaces. These machines are fitted with abrasive wheels, which are used for sanding, cutting, sharpening, and polishing various materials. And these days there are various different grinding machines available on the market, with consumers always on the lookout for the ideal machine.
This article will highlight the market demand for grinding machines, and then highlight the most popular models available. It will also point out what to consider when selecting a grinding machine, to ensure businesses can confidently source the best models available today.
Table of Contents
The market projection for grinding machines
Factors to consider when buying a grinding machine
Types of grinding machines
The market projection for grinding machines
The global market for grinding machines was valued at US $4.72 billion in 2018 and is estimated to grow at a compound annual growth rate (CAGR) of 4.6% to reach US $6.73 billion by 2026.
This growth for grinding machines is propelled by several factors such as increased demand for automated grinding machines for jobs with high precision requirements, and increased demand for high-quality surfaces that need grinding machines for finishing.
Also, the enhanced technological development and innovation in grinding machines will likely increase demand as they will cater more to the needs of an industry that requires efficient and effective machinery and solutions.
Factors to consider when buying a grinding machine
Different people have unique preferences when choosing the right grinding machine. This depends on the intended purpose of the machine. That said, the factors below will help one choose the right model with confidence.
The material or surface to be ground
The first factor to consider before buying a grinding machine is the type of material or surface to be ground. For instance, machines with aluminum oxide grain wheels are suitable for grinding ferrous metals, while silicon carbide grains are used on non-ferrous metals and non-metals.
However, machines with ceramic and super abrasive grains are used in specific circumstances where silicon carbide and aluminum oxide are ineffective.
Tough and durable grains are suitable for easy-to-grind surfaces to prevent the material from breaking down. On the other hand, hard-to-grind materials need friable or finer grit wheels.
Grinding pressure
If the projects require high pressure, ceramic and super abrasive grinding grains are the ideal choices. This is because higher pressure levels need tough grains to avoid premature breakdown.
Conversely, light-pressure operations require mild, friable grains because tough grains will only dull. Mild grains can properly fracture under light pressure and self-sharpen before they start burning the surface being ground.
Size and weight
Since larger projects need a grinding machine to run for a long time, they require bigger grinders with larger wheels. Bigger grinders also handle tougher jobs faster than smaller grinders.
However, if the project involves cutting and polishing metal, smaller grinders will suit the bill because they spin faster.
Motor power
Different grinders come with varied wattage, voltage, and amp ratings. Most people prefer grinding machines with wattage ranging from 500 to 250 watts and power ranging from 110 to 230 AC.
A grinder with higher motor power and amp ratings is suitable for tougher and bigger projects. However, if the project involves only household tasks, a grinder with a lower rating is sufficient to handle the job.
The required form and finish accuracy
When choosing a grinding machine, it is essential to establish whether the project requires a fine finish or rapid stock removal. One should also know if the surfaces being ground will be flat or simple.
Finer grits are ideal for low-Ra finishes since they allow more contact points between the wheel and the surface needed for precision finishes. For instance, grinders with fine-grit abrasive wheels are often used if the surface of the final product should have a roughness average (Ra) between 0.01 and 0.05. A smoother surface finish needs polishing or finer wheel grit.
On the other hand, harder and rougher grits are best suited to producing surfaces with higher Ra finish. For instance, a surface Ra finish of 6.3 can be produced through milling, drilling, disc grinds, and hard-grade surface grinds.
Safety and comfort
The safety of the grinders is something the buyer should consider. No one wants to get injured at the workstation! Since grinders are rotating sharp machines, they have a high risk of causing severe injuries.
Therefore, look for grinders with protective features such as eye shields to prevent flying debris from damaging your eyes.
The machine should also be comfortable to hold otherwise this can affect not only the safety of the worker but also how well they do the job. So, ensure that the size and the weight allow for longer and safer holds without the operator getting tired.
Handle
Grinders with adjustable side handles are versatile and easy to use regardless of whether one is left or right-handed. Additionally, one can look for grinders with anti-vibration handles, making the machine comfortable to use for longer.
Wheel Speed
It is important to consider a powerful machine with high wheel speed to quickly get the job done to perfection. Big grinding machines have discs that do between 5,000 and 10,000 revolutions per minute.
High wheel speed means performing numerous grindings, cutting, and sanding jobs. Nevertheless, they can also increase the risk of injury if not properly handled.
The general rule is that verified and organic bonds are suitable for 8,500 SFPM (43m/s) surface speed and below, while surface speeds above 8,500 SFPM are preferred for organic bonds only for safety reasons.
A softer performance needs slower wheel speeds because the abrasive particles on the wheel generate high force that breaks down the bonds and grains quickly.
Productivity
The performance of its abrasive wheels determines the grinding machine’s productivity. Some hard-acting wheels last longer but may not remove a lot of material, while the soft-acting wheels may not last long but cut faster.
It is good to strike a balance by selecting a grinding machine with an excellent cut rate and longer wheel life.
Grinding machines have different productivity ranges depending on wheel size, speed, and material. The productivity of a grinder determines how much surface the machine can grind per minute, often indicated in the specification.
For instance, the cylindrical grinding machine and surface grinding machine’s productivity range from 0.1-4m/min, while the belt grinder’s productivity range depends on the size of the belt and the machine type.
Types of grinding machines
The following is a selection of the most popular grinding machines available on the market today:
Bench grinding machines
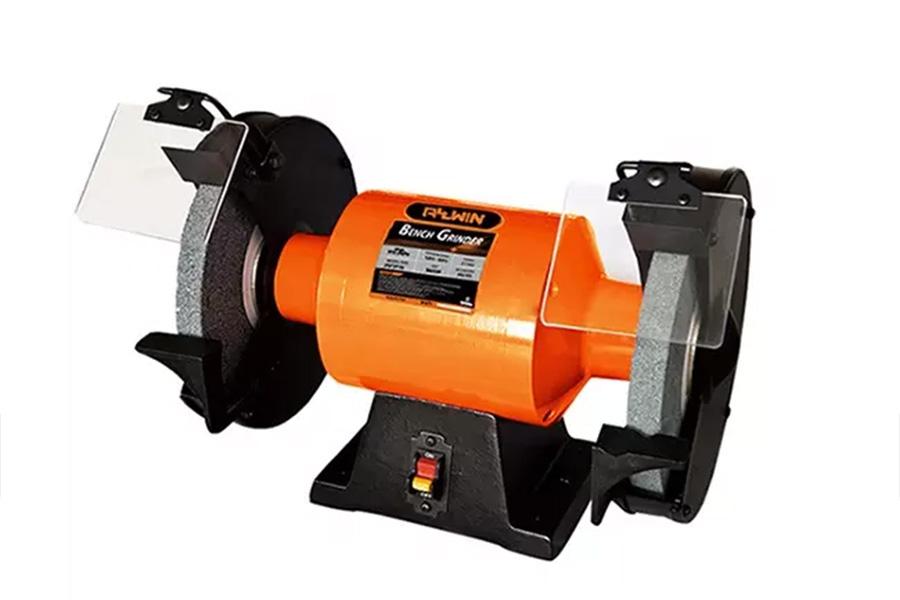
Bench grinding machines are often fixed on a table or workbench and are typically used in workshops for grinding small workpieces. They are fitted with handles for rotating the pulley or big-size gears.
Bench grinding machines come with one or two wheels and can also be powered. They are also used for sharpening drill bits and lathe machine cutting tools.
Pros
- Low risk of injuries since it is stationary
- High productivity
- Easy to operate
Cons
- It is stationary and cannot grind certain surfaces.
Portable grinder
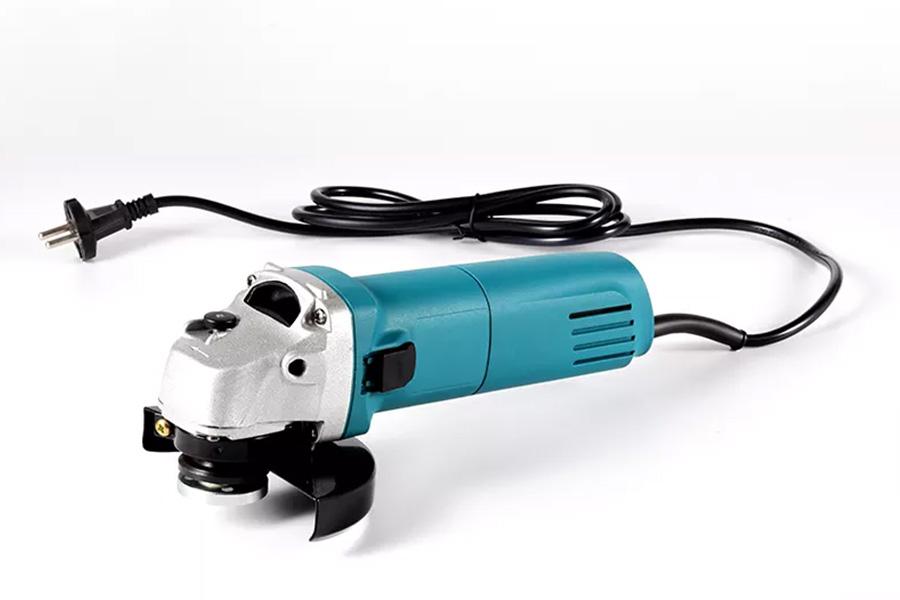
Unlike the bench grinding machine, portable grinders are not stationed at one point; they can be carried from one place to another. And since they are portable, the operator can use them at any position or on different grinding sides. Contractors also use them when cutting tiles or smoothing small workspaces.
Pros
- The operator can use them at any angle or position
- They are versatile, which means they can be used for various jobs
- They consume less power
Cons
- High risk of injury if not properly handled.
Cylindrical grinding machine
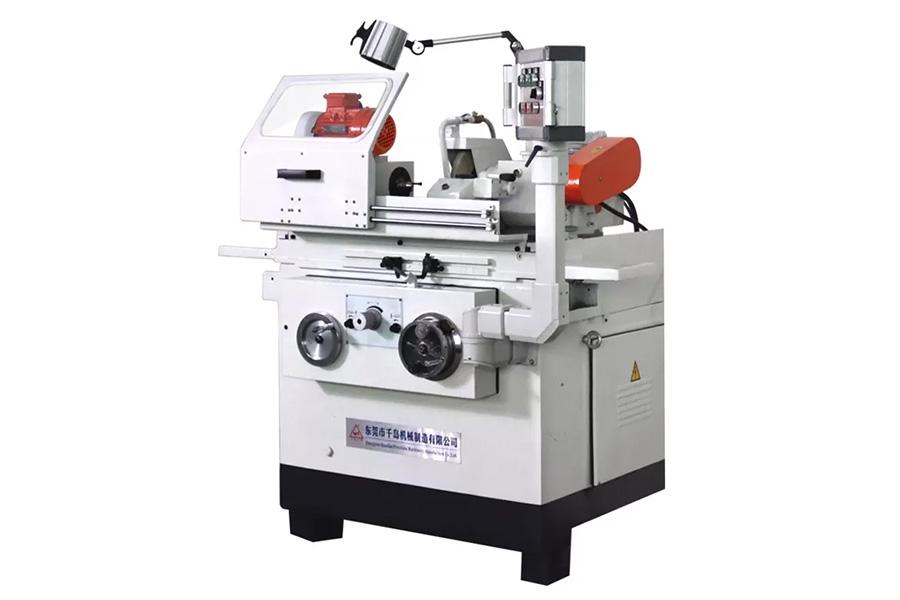
Cylindrical grinders are used when shaping the outside surface of a cylinder. These grinders are suitable for jobs requiring different shapes to rotate through the central axis.
Their operations are similar to lathe turning ones. They are often used to replace the lathe when the surface is hard or when the operation requires a superior finish or extreme accuracy.
Cylindrical grinders differ in sizes one can choose from depending on the scale of work at hand. For instance, CNC cylindrical grinder has a wheel size of 600* 75*305 mm and a maximum grinding diameter of 320mm, while the Timeaway cylindrical grinder has a wheel size of 400*50*203 mm and a maximum grinding diameter of 800mm.
Besides workload, the wheel and table size for the cylindrical grinder one chooses also depends on the operation space.
Pros
- It can run all day long without breaks
- High productivity range of 0.1-4m/min.
- Enhanced roundness accuracy ranging between 0.000025mm to 0.0005mm
Cons
- It is complex and time-consuming
Surface grinding machine
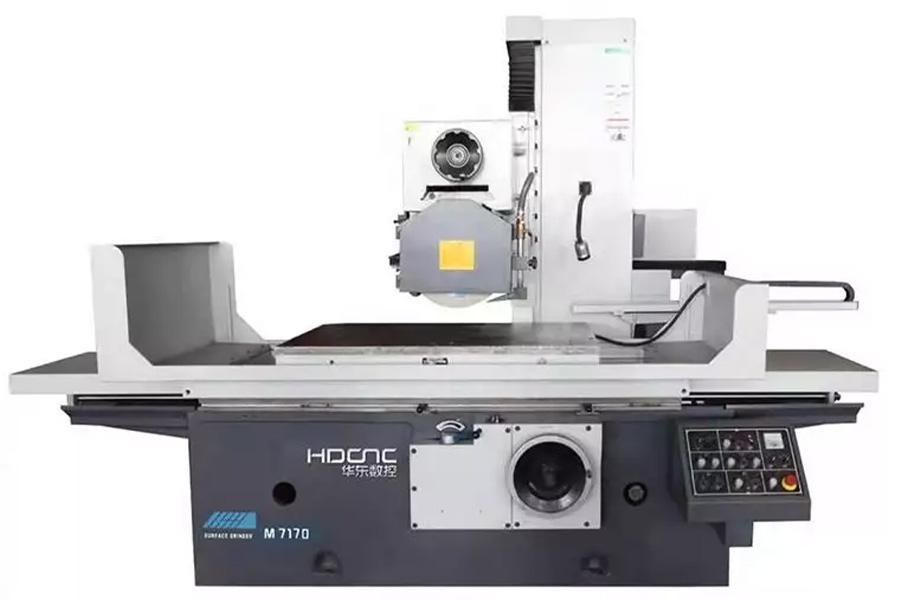
The surface grinder consists of an abrasive wheel, a rotary table, and a workpiece holding the device. They can work on flat, irregular, and angular surfaces.
The grinding wheel rotates on a spindle while the workpiece is mounted on a rotary table. The mounted workpiece is held in position by the chuck while the wheel and the table are rotated to create a smooth finish.
Pros
- High productivity ranging from 0.1-4m/min
- It does not require a skilled operator
- It produces smooth surfaces on metallic and non-metallic materials
Cons
- It does not allow reverse grinding
- The grinding wheel degrades faster and needs much spindle power.
Belt grinding machine
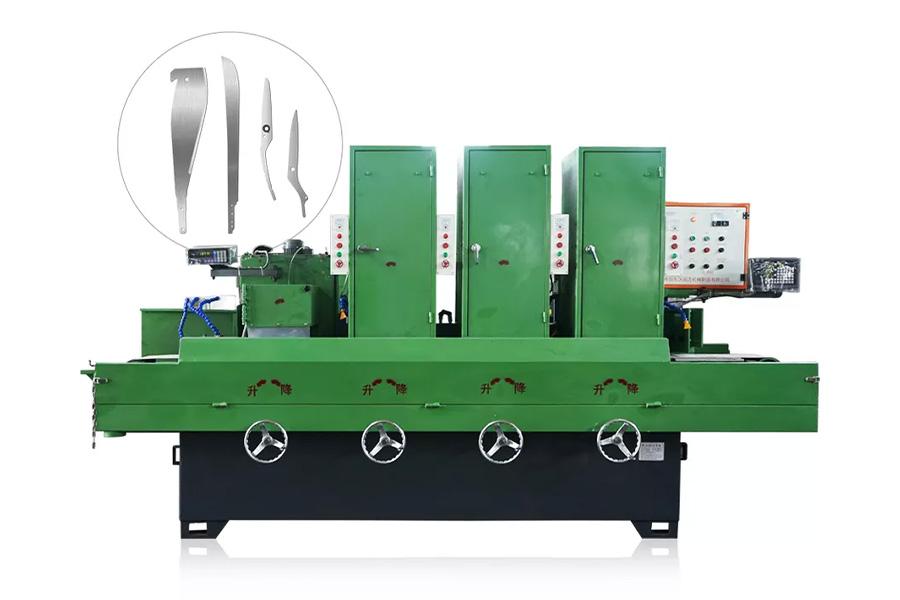
The belt grinding machine has an abrasive belt attached to its motor to help grind the workpiece or material. They are often used to grind metallic surfaces; therefore, they are mostly utilized by fabrication and metal working industries, adjacent metal fields, and blacksmithing industries.
Pros
- Easy to use
- Optimal productivity range from 100-500m/min depending on the belt size and machine type.
- They are diverse
- Easy to replace dull belts
- High accuracy of 0.1μm or less and surface roughness below 0.025 μm, especially with low belt speed.
Cons
- It does not have a protective cover to protect your eyes and clothes from emitted sparks.
The bottom line
Grinding machines have abrasive wheels that are used for grinding metals, surfaces, plastics, and other materials. They are essential for a number of industries, but with many types of grinding machines available on the market, consumers will be on the lookout for the machine that best suits their needs. This article has therefore highlighted the key factors that businesses should consider when sourcing grinding machines, so that they can boost their appeal to customers with a well-stocked inventory.