With the wide range of plastic extruders available today, selecting the best can be a challenge. This article will walk you through what you need to consider when selecting plastic extruders to help buyers find the best models available on the market. It’ll also cover the different types of plastic extruders available so that buyers can rest assured that they’re getting the right solution for their needs.
Table of Contents
The growth of plastic extruders market
Tips to consider when selecting a plastic extruder
Different types of plastic extruders
Target market for plastic extruders
Wrapping up
The growth of plastic extruders market
The global plastic extrusion machine market is expected to reach a value of US $7.903 billion by 2027, registering a moderate compound annual growth rate (CAGR) of over 4.5% from 2020 to 2027. The increasing worldwide demand for plastic extruders is being propelled by a rise in awareness about energy saving machines and rapid industrial automation. This demand is being met by an increasing supply of high-performance extrusion machines, with China dominating the supply market. To meet the needs of specific applications, the market players are manufacturing plastic extruders of various types, sizes, applications, and design complexities.
Tips to consider when selecting a plastic extruder
The application of the extrusion machine determines its design, and is therefore the first step for determining extruder specifications. Below is a detailed description of what you need to consider when selecting the extruder and its components.
Material
Material selection is an essential consideration to ensure that your extrusion machine works successfully. To determine the best material, consider the following:
- Durability – How much stress and weight the product can undertake is vital. If it’ll be used to hold something heavy, or exposed to a sudden impact or friction, then a part that can withstand such forces should be considered. Likewise, should the part be expected to undergo stretching, compressing, or any other type of stress, you should opt for a machine with good fatigue resistance. A few of these include: rigid PVC extrusions, cellular PVC extrusions, and polypylene.
- Temperature – If the plastic extruder is to be used with something extremely hot, you should consider its thermal properties. It’s crucial to take into account the highest temperature your product will be subjected to as repeated exposure to heat can cause distortion in shape and durability. Safety measures should also be considered, for instance, if the material needs to be flame resistant then specific materials and additives should be used or avoided during the process.
- Requirements – Depending on the industry you intend to use your plastic product for, you should ensure that it is safe for these intended applications.
- Environment – If you intend to use your plastic extrusion product underwater or in contact with liquids, then you should select a water / liquid resistant product. Similarly, materials used with chemicals need to be non-corrosive. Lastly, materials intended to be kept outside for a long time need to be insulated and electrical resistance needed where necessary.
- Appearance – The finish of your material is another vital area that you should consider for your design. With respect to the specific color or opacity you desire for your product, there are plastics that can better produce the desired effects.
Once you’ve determined the suitable material properties for the part, it’s time to search the resin. It’s important to note that not all resins are fit for the extrusion process. As such, consult your supplier for recommendations based on your design and part requirements. Generally, to reduce the overall failure of the plastic extruder, it’s best to consider the design and other vital part’s requirements. You can start by considering:
Tolerance, which depending on your extrusion length
Thermoplastics contract and expand whenever subjected to temperature changes. Cutting plastic profiles to their exact lengths incur higher processing requirements and attract unnecessary handling costs. The extrusions must, therefore, have a little length tolerance incorporated into the overall length.
Wall thickness
The flow of the material determines the extrusion process. Varying thickness of the walls’ design can make the flow of plastic material difficult resulting in a distorted profile. For a balanced profile, the walls must be uniformly thick.
Hollows
A good profile design should have a limited detail in hollow sections. However, if a hollow is required, the following precautionary tips can help reduce the potential risks:
- Avoid a hollow within a hollow as it will force the intended design out of shape before the thermoplastic solidifies.
- Shun away from hollow sections with internal legs. If a leg is necessary, it should not exceed the thickness of the wall.
Corner radius
While all extrusion profile corners should have a radius, sharp corners can lead to stress concentration and eventually warp and break. For a uniform wall, the inner and outer radii should be an offset of one another. The sharp-edged outer corner is 1/64 inch, thus the recommended inner radius should be the least of 1/64 inch to reduce the possibility of a breakage, especially in rigid materials.
Attachments
Tapes and adhesives increase labor and material costs. Instead, an extrusion machine must have a well designed mechanical attachment. However, if tapes or adhesives must be used, the attachment or placement area should be a flat surface for proper adhesion and be over ⅛’’ wide. The thickness of the adhesive should be taken into account when ruling out the height of the profile.
Different types of plastic extruders
Single screw extruder
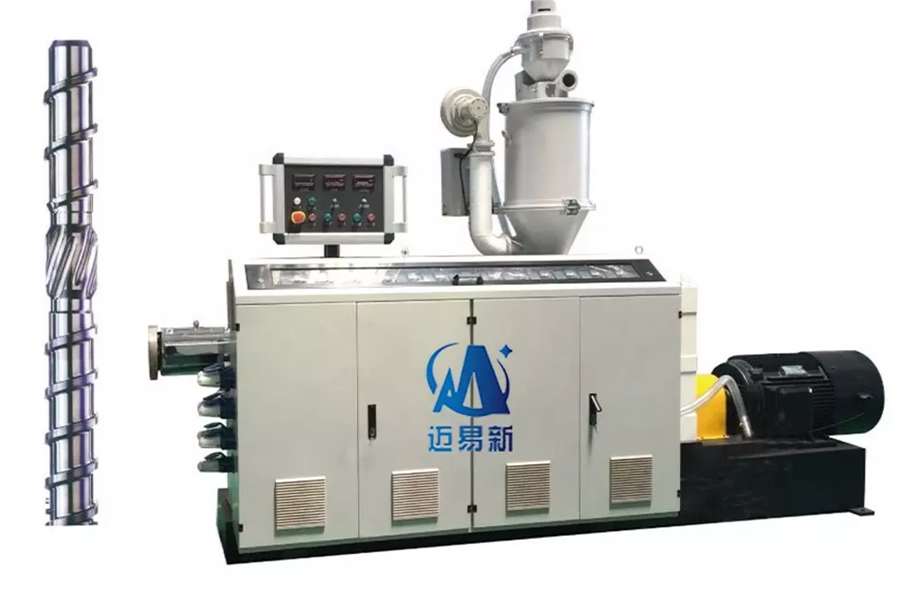
The single-screw extruder is a type of plastic injection pump mostly used as a continuous extruder in the polymer extrusion operation. The primary function of a single screw extruder is to gradually input pressure in the melting of the polymer so that the polymer is extruded through the die.
These extruders are relatively cheap and have low maintenance costs. They are simple and easily provide a continuous output of materials such as HDPE, LDPE, AND PP, which is why they are popular in the plastic product recycling industry. As the design of extrusion screws has improved over the years, single screw extruders with secondary flights for faster melting are also available in the market.
Asia-Pacific is one of the leading markets for the single screw extruders, and the global market growth is expected to grow at a CAGR of 4.4% by 2026..
Advantages
- Less shear
- High throughput
- Better at extruding common materials compared to twin screw extruders
- Far much cheaper than other extruders
- Can be used in operations for wide range of varying material types
Disadvantages
- Limited feeding performance
- Unsuitable processes due to difficulties when mixing materials such as paste or powder
Twin screw extruder
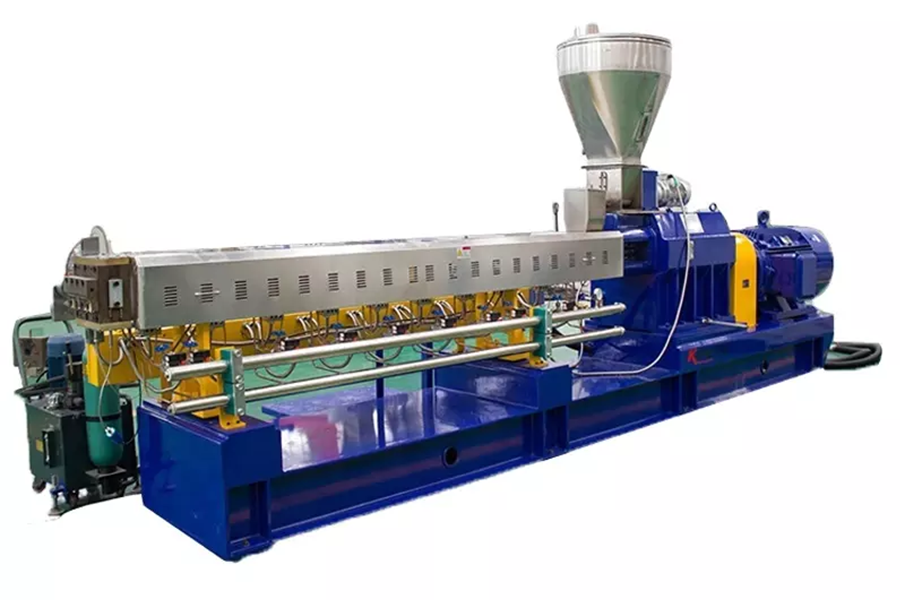
Twin screw extruders have two parallel intermeshing, co-rotating screws installed on the shafts to ensure effective transporting, compressing, mixing, cooking, shearing, and heating. Twin screw extruders are popular, with an estimated US market value of US $253.5 million and global growth value at a (CAGR) of 6.30% by 2026.
Advantages
- Good self-cleaning during the screws mutual friction
- Convenient to observe the wear of the threaded element for timely and effective replacement
- Lower production costs
- Improved labor efficiency of the maintenance and production interruptions during use
- High torque, high speed, and low energy consumptions
- High yield and high quality compared to the single-screw extruders
Disadvantages
- High discharge rate
- Severe wearing out of the barrel and screw edge in the meshing zone
- Expensive screw and barrel of the conical twin-screw extruder
- Less heat produced in the barrel
Blown film machine
Blown film machines produce specialized polymer films that are widely used in packaging, such as shopping bags, barrier films, stretch, and shrink wrapping. Air pressure is used to expand the film and afterwards cooled to solidify the polymer. This extruder has multilayer film structures made through film coextrusion combining two or more molten polymer layers. The transition from using standard polymers to biodegradable polymers plus the steadily expanding pharmaceutical industry has increased the overall demand of blown film. The projected global film extrusion machinery market is valued at US $ 2,563.7 million and is expected to grow at a CAGR of 4.8% until 2031.
Advantages
- Better balance of mechanical properties
- Require lower melting temperatures than other extruders
- Stretches film to varying degrees in longitudinal and transverse directions
- Full thickness control
- Higher flexibility, thus higher productivity
Disadvantages
- Less effective in cooling
- Complex and error-prone method of controlling film thickness
- Can easily trap air between the layers of the film
Target market for plastic extruders
Extruded plastics are commonly used across all industries and the demand is projected to grow at a CAGR of 4.5% from 2020 to 2027. This growth is as a result of increasing demand for efficient and reliable parts that are more eco-friendly and reusable. The buying potential for the plastic extrusion machines is expected to grow across the global markets by 6.9% over the forecast period.
A rise in demand for plastic extruders in the building and construction industry is expected to boost the growth of the Asia Pacific market, which currently holds 40.2% market share, with a projected highest CAGR of 5.4%. The growth of the automotive industry in Europe will increase the current 19.80% market share. Further, the busy lifestyle of consumers worldwide has heightened the consumption of frozen foods, leading to a rise in demand for plastic extrusion machines. Northern America, Europe, and Latin America, the Middle East, and Africa (LAMEA) are potential key players in the market.
Wrapping up
The expanding plastic market globally has created many opportunities for the suppliers of the plastic extruders. This article gave an insight of the types of extrusion molding machines available and the essential factors to consider during the sourcing decision making process. For more information on plastic extruders, and to look into the available models in the market today, check out the Alibaba.com marketplace.