3D printing is one of the most revolutionary technologies of the 21st century, and it is steadily transforming how things are created, designed, and built. There is therefore no surprise that the 3D printing industry is one of the most important industries for manufacturing retailers to watch.
However, many buyers may struggle to stay up-to-date on the various innovations in 3D printing technology. This article will discuss seven of the key technologies to know, and provide vital tips for choosing the right printing process.
Table of Contents
What is 3D printing?
3D printing industry overview
7 types of 3D printing technologies
How to select the right 3D printing process
Conclusion
What is 3D printing?
3D printing is part of a process known as additive manufacturing, where an object is created by adding a material layer by layer. While this process is used in large manufacturing to create automobile parts or jeet engine components, it can also be used at home or for business use using small-scale 3D printers.
The first step in 3D printing involves creating a blueprint of the object to be printed. Once a user has a 3D design, they send it to a printer which receives the data, pulls the material through a tube, melts it, and deposits it to a plate where it cools instantly. The 3D object is created through layering, as the printer will add one layer of the material at a time until a fully formed structure emerges.
3D printing industry overview
The 3D printing market has been experiencing steady growth. In 2023, the global market reached a valuation of US$ 20.67 billion – a figure expected to rise to US$ 91.8 billion by 2032. Market analysts expect this growth to occur at a compound annual growth rate (CAGR) of 18.92%.
The eruption of digital technology is influencing the rise of the 3D printing industry, which is ideal for modern manufacturing. Many countries have already adopted 3D printing, with the United States emerging as the top spender with regard to buying 3D printers in 2023, accounting for more than 34% of the market share. As the demand for 3D printing technology keeps growing, businesses that source the right 3D printing tools are poised to benefit from the vast market.
7 types of 3D printing technologies
There are several types of 3D printing technologies practically used around the world. Understanding these types can help retailers make informed decisions when stocking products and enhance production selection based on demand. They include the following:
1. Stereolithography (SLA)

Stereolithography, or SLA, is a 3D printing process that uses a laser to cure liquid resin into hardened plastic. Upside-down or inverted stereo is the most common SLA system.
Depending on the machine, resin is poured into the tank by the user or dispensed automatically from a cartridge.
At the beginning of the print, a built platform is lowered onto the resin, leaving only a thin layer of liquid between the building area and the bottom of the tank.
A clear glass at the bottom of the resin tank allows galvanometers to steer the UV laser, sketching a cross-section of the 3D model and selectively hardening the material. The print is constructed in successive layers, each with a thickness of less than 100 microns.
Once a layer is finished, the platform is lowered again, and the component is peeled from the tank’s bottom to allow fresh resin to flow underneath.
Originally developed in the 80s, SLA was confined to large industrial machines until recently. Today, desktop lithography offers affordable, high-resolution 3D printing that fits conveniently in a user’s workspace.
SLA allows for using a wide range of materials with diverse physical properties. Whether an engineer, product designer, sculptor, jeweler, or dentist, there is a material for their application.
2. Digital light processing (DLP)
In digital light processing or DLP, the actual process of curing and manufacturing the 3D object is the same as SLA 3D printing, except for one deviation. Stereolithography uses a laser to project the 3D replica of the object on the tank’s surface, creating a layer on top of another.
In the case of digital light processing, the laser is replaced by an arc lamp or source of light. The light gets projected in the form of the desired shape on the surface of the liquid polymer, and the particular liquid polymer gets hardened easily, making it less time-consuming than the laser to form a shape. The result is a faster 3D printing process than SLA.
Digital light processing uses various materials like nylon, ABS, and thermoplastics. Therefore, it is versatile. It also manufactures different shapes using its bottom-up printing at high resolution.
3. Fused deposition modeling (FDM)
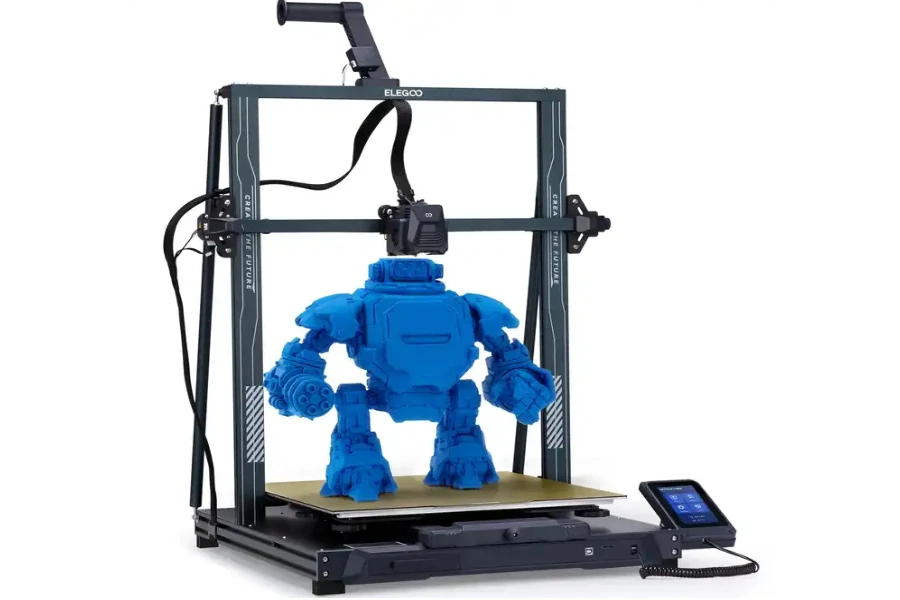
This layer additive 3D printing process uses production-grade thermoplastic materials to produce both prototype and end-use parts.
The technology is known to produce feature details accurately and has an excellent strength-to-weight ratio. It is ideal for concept models, functional prototypes, manufacturing aids, and low-volume end-use parts.
The FDM process begins by “slicing” 3D CAD data into layers. The data is then transferred into a machine that constructs the part layer by layer on a build platform.
Thin thread-like spools of thermoplastics and support material are used to create each part cross-section. Like a hot melt glue gun, uncoiled material is slowly extruded through dual-heated nozzles. With precision, the nozzles lay down both the support and 3D printing material upon the preceding layers.
The extrusion nozzle continues to move in a horizontal X-Y plane while the build platform moves down, building the part layer by layer. The user removes the finished part from the build platform and cleans off its support material.
RAW FDM parts have visible layer lines. Multiple finishing options like hand sanding, assembly, or cosmetic paint can be applied to create smooth, even surfaced pieces.
While FDM parts are constructed with thermoplastics like ABS, polycarbonate, and ultem, they are both functional and durable.
4. Selective laser sintering (SLS)
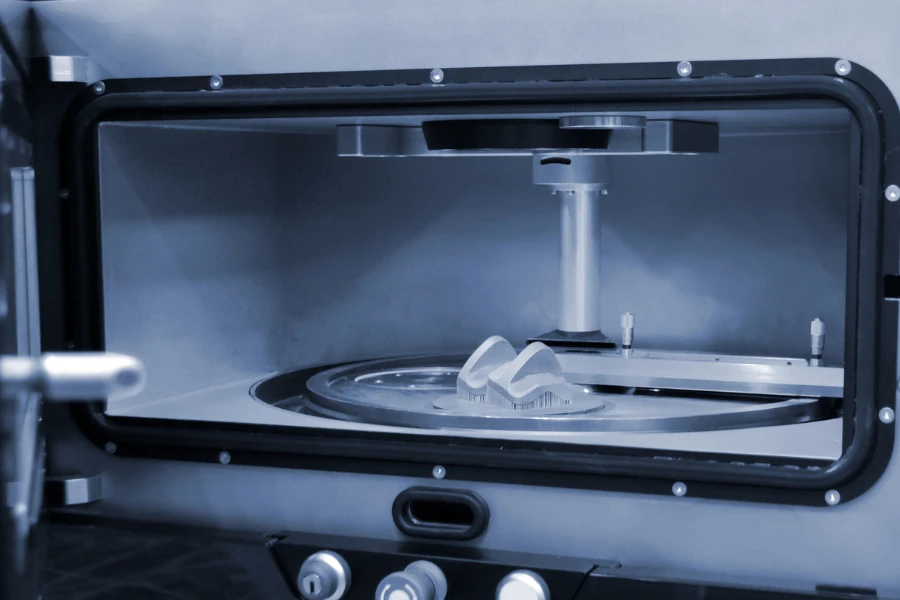
SLS printing is a laser powder-based printing that uses powder as a raw material instead of filament or resin. The printing process begins by lowering a powder reservoir and filling it with thermoplastic powder, typically nylon.
The particles that make up the powder are round, with a diameter of less than 100 microns and a smooth texture. This allows the powder to be spread in a thin, dense layer, which is important for the success of an SLS print.
Before starting the print, the powder is heated just below its melting temperature through heating coils and, in some cases, infrared lamps. The powder is kept at this temperature throughout the print to make it easier for the laser to melt the powder because a small amount of energy will be required. It also prevents the printed part from warping due to temperature gradients.
A powder spreader such as a blade or roller creates a thin uniform layer on the build platform; then, a laser selectively heats regions of the build area to melt the powder in a defined geometry. This part is repeated, with each piece getting taller after each layer.
It should be clear that if there are faults or artifacts in the powder, these flaws will translate directly to the part, resulting in poor mechanical properties or possible print failure. That is why smooth, uniform layers are important.
When all goes well, the unentered powder entirely encases the printed part. This means that support material is unnecessary for SLS printing; any geometry can be printed. The only restriction is there needs to be enough space to remove the loose powder after the print.
5. Selective laser melting (SLM)
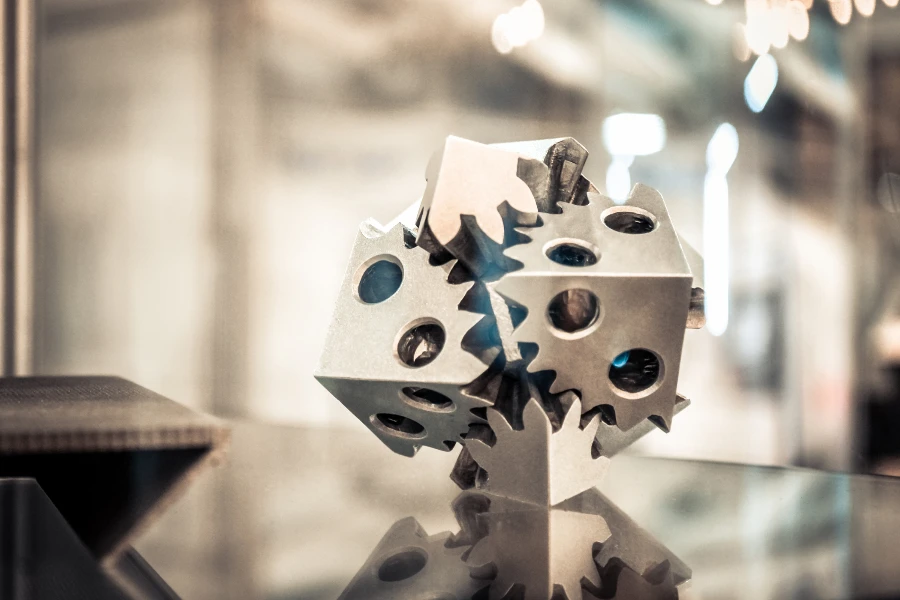
The selective laser melting process uses metallic powdered materials to build up an object layer by layer. It is used to create objects using various metals, which usually have a high density. This 3D printing technology uses a laser to melt metal powder, which cools and solidifies it.
Each laser cycle produces a new slice of the object being created, and then the work platform gets lowered by exactly the thickness of one side as a scraper redistributes the powder. The melted metal solidifies, and the process is repeated.
The laser fuses together the old and new layers until the prototype is completed. Each component is welded to the work platform with a detached support after the component is removed.
The finished object is removed from the unused recyclable powder and freed of excess powder, resulting in very rugged precision manufactured products.
Selective laser melting proves its worth when complex components need to be produced quickly. It also enables the production of complex products with integrated functional elements such as conformed cooling.
6. Electronic beam melting (EBM)
Electronic beam melting is a metal additive manufacturing process with the starting point being a bed of powder metal fused layer by layer to build the solid metal part using an electron beam.
Compared to more common laser powder bed fusion techniques like SLS and SLM, it is a high-energy process, hence using the electron beam.
Electronic beam melting typically occurs inside a machine under a vacuum at high temperatures. A user starts by spreading a layer of metal powder across the build area and preheating all that powder. Then, the electron beam fuses it by melting the places needed to build up the object.
The process is repeated to eventually end up with a semi-solid block or cake of powder containing the preheated granular materials. The next step requires depowering the block and then continuing with the workflow.
One of the benefits of EBM is that the higher energy source makes it possible to use larger-diameter metal powder, which is also easier to work with. It also doesn’t have any respiratory risk when working with fine powder. Therefore, with EBM, working with the powder and being around it without special safety equipment is possible.
Another advantage of electronic beam melting is it takes place at higher temperatures than laser powder bed fusion. This translates to better management over thermal stresses, less warping and distortion, and better dimensional accuracy.
Electronic beam melting is commonly used to make medical implants, although it has also been used in aerospace and automotive engineering.
7. Laminated object manufacturing (LOM)
The other 3D printing technology is laminated object manufacturing. Laminated object manufacturing, or LOM, is a rapid prototyping process in which coated paper, plastic, or metal laminated layers are successfully glued together and cut to shape with a cutting tool or laser cutter.
Each layer of the building process contains the cross-sections of one of many parts. Before the processing begins, an image from a CAD-derived STL file is fed to the printer. A LOM system software calculates and controls the slicing functions, while the lamination and object orientation occur manually.
In the building process, the system creates a cross-section of the 3D model, measuring the exact height of the model, and slices the horizontal plane accordingly. The software then images cross-hatches and the model’s perimeter.
A larger beam cuts the thickness of one layer of a material at a time, and after the perimeter is burned, the model’s boundary gets freed from the remaining sheet.
The platform with the stack of previously formed layers descends, and a new section of material advances.
The platform ascends, and a heated roller laminates the material to the stack with a single reciprocal motion, bonding it to the previous layer. Then, a vertical encoder measures the height of the pile and relays the new height to slice. This sequence continues until all the layers are built.
Processing the material follows after the materials are fully formulated, which involves separating the laminated part from the LOM block. After separating, the object can be sanded, polished, or painted as desired.
How to select the right 3D printing process
Businesses can be able to choose the right 3D printing method only if they consider some key factors. Here are three key elements to prioritize before investing in a specific technology.
1. The manufacturing or the process capability
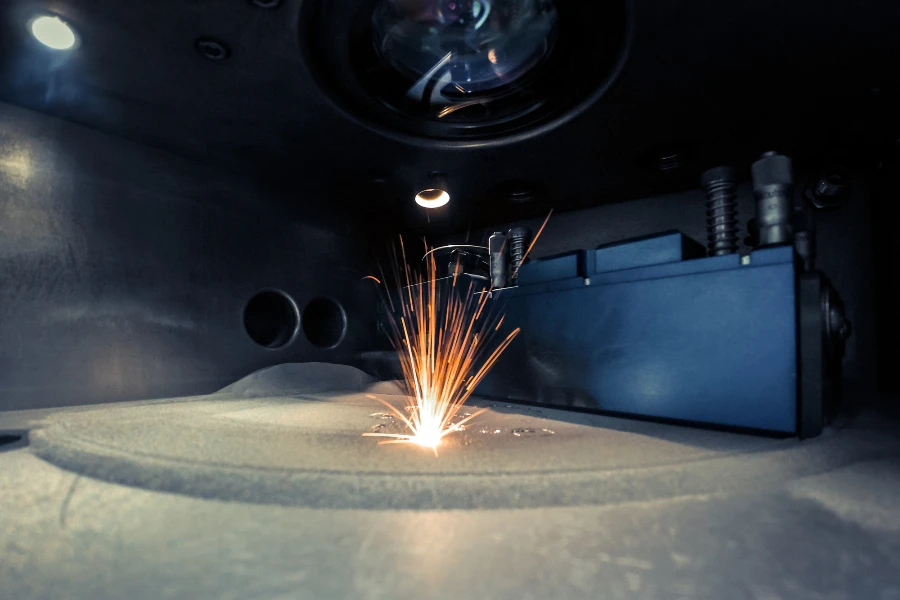
First, when selecting a 3D printing technology, it comes down to the practicality of the procedure to make the product. The physical characteristics of the manufactured object can help users narrow down the printing methodology. These include the finished product’s desired thickness, accuracy, size, or support structure.
For instance, the minimum wall thickness in SLA printing is 0.6mm, while digital light processing can accommodate up to 0.2mm. The result of the printed object is the least accurate with fused deposition, while SLA is the most accurate and has the highest resolution.
While SLS or SLA is excellent for most 3D printing needs, more complex designs that require expert handling can be achieved through FDM, EBM, or LOM printing.
2. Characteristics or functionality of the end parts
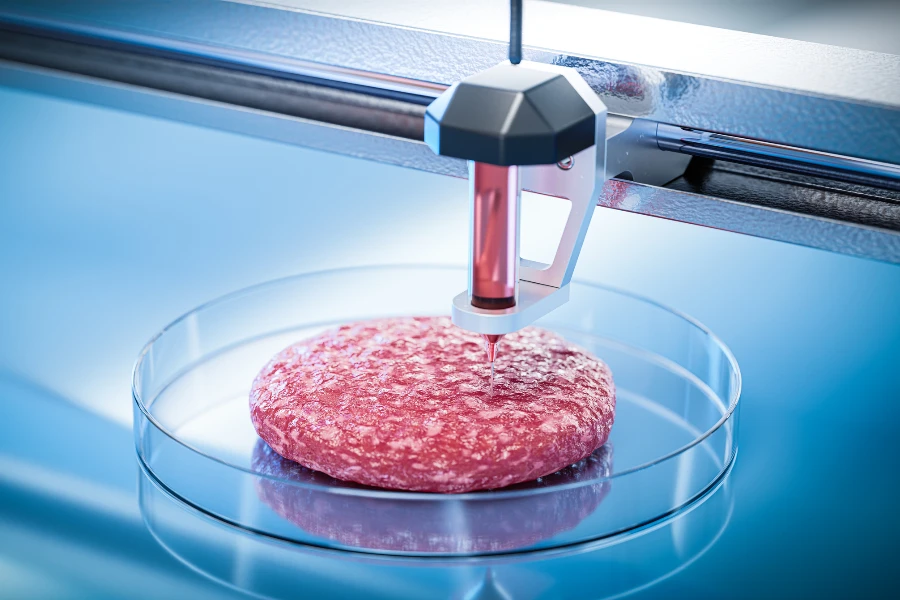
Another way to pick an ideal 3D printing process is by considering the final product’s functionality. This entails looking at the non-susceptibility to environmental conditions, flexibility, rigidity, and other physical aspects such as chemical and heat resistance, ecological safety, and if it’s even edible.
Exposure to moisture or sunlight can affect the quality of products; hence, heat and moisture resistance is not assured with resin-based processes such as SLA or DLP. Therefore, users may consider powder infusion-based methods like EBM, SLM, or LOM printing technologies. In addition, items printed using these technologies have the strongest chemical properties.
This means that SLA and DLP will suit the printing of materials that won’t be exposed to harsh external elements, while electronic beam melting selective laser sintering methods work best for printing industrial-grade materials.
3. Material and the finishes
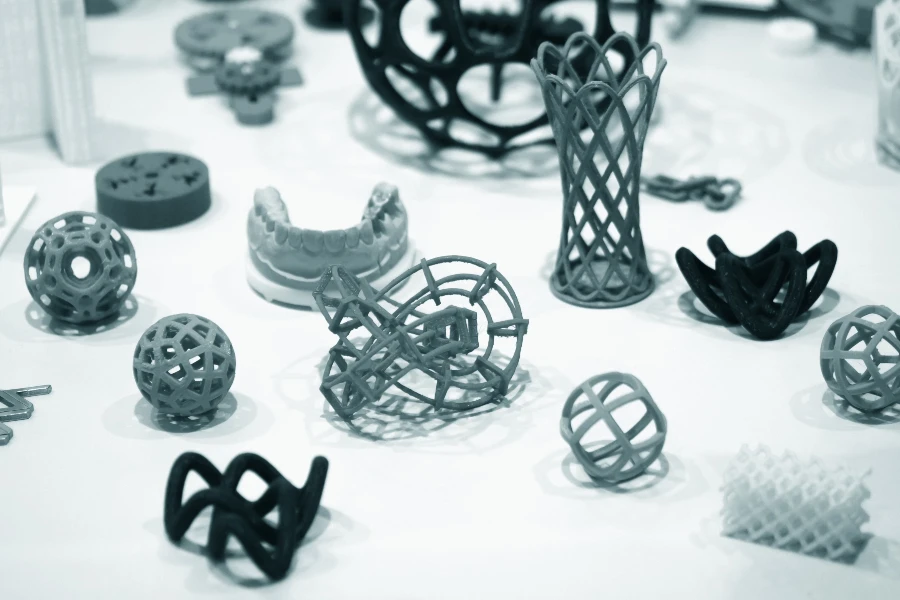
Finally, businesses must emphasize the type of material they will use to produce the object and the finish they expect from the print. The most common materials used for 3D printing include filament, powder, and resin, where these materials are further classified into polymers or plastics, metals, ceramics, and composites.
Plastics are also categorized into thermoplastics and thermosets. SLS and FDM are best suited for thermoplastics, while the best printing technology for thermosets is stereolithography and Digital Light Processing (DLP).
Metal materials have the strongest qualities and suit aerospace, automotive, and medical applications. The type of material also matters when making strong parts such as door hinges or other metallic parts for light applications. SLM, LOM, and EBM processes offer printing solutions for such needs.
Meanwhile, these different printing technologies also have different finishes. For example, those looking for a plated or glossy finish can choose SLA and FDM techniques. SLA and DLP will execute a clear finish. A dyed or matte finish is possible when using selective laser sintering.
Conclusion
Ultimately, there are different 3D printing technologies, and picking the right one comes from the user’s needs. Other factors, such as the material and the practicality, will also determine the type of technology to use. Users ready to embark on a successful 3D printing journey can explore a range of reliable 3D printers on Alibaba.com.