In the niche of cup production, more and more businesses are opting for cup forming machines due to their efficiency and ability to deliver consistent quality. These machines have transformed manufacturing by automating production, cutting costs, and guaranteeing cups with uniform shapes and sizes. However, finding the ideal cup forming machine can be overwhelming. With a wide array of options to choose from, buyers need to consider various factors carefully.
This article will delve into the different types of cup forming machines and shed light on the key factors buyers must consider when selecting the perfect machine.
Table of Contents
Overview of the market for cup forming machines
Types of cup forming machines
Key factors to consider when selecting cup forming machines
The bottom line
Overview of the market for cup forming machines
The market for cup forming machines is witnessing a significant surge in demand. This is because businesses are realizing the immense benefits these machines offer in streamlining cup production. With their ability to enhance efficiency, cut costs, and maintain consistent quality, cup forming machines have become highly sought-after. There is also a growing focus on sustainability, driving the increased demand for eco-friendly cups.
Emerging regions like Asia-Pacific, North America, and Europe have witnessed significant demand due to the expanding food and beverage industries and the rising consumer preference for disposable cups. This combination of sustainability and market expansion has fueled the growing popularity of cup forming machines in these regions.
Types of cup forming machines
1. Injection molding machines
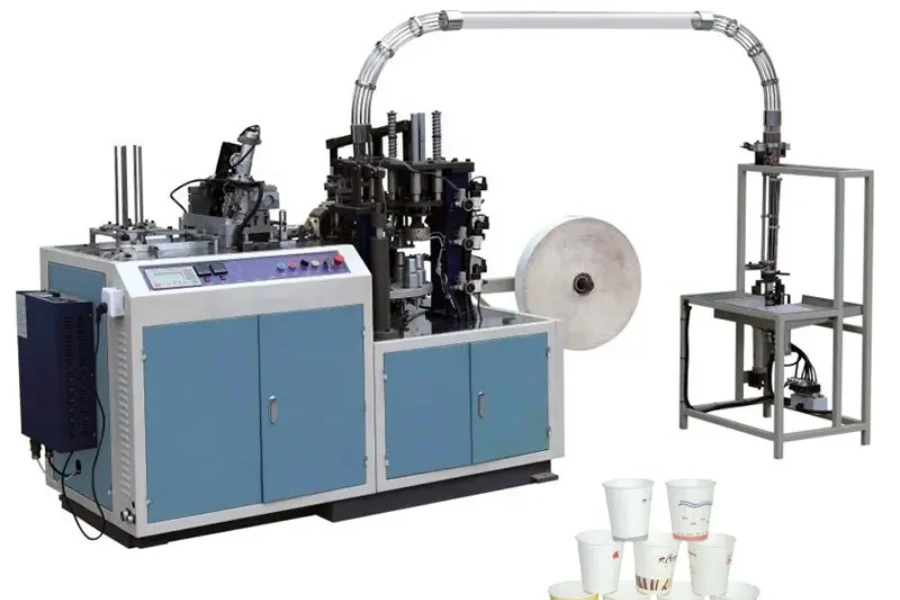
Injection molding machines inject molten plastic material into a specifically designed mold cavity. Once the plastic material cools and solidifies, it adopts the shape of the cup. Injection molding machines provide notable advantages such as remarkable production efficiency, meticulous control over cup dimensions, and the capability to produce cups with intricate designs or features. Their versatility makes them an excellent choice for businesses aiming to produce high-quality plastic cups with precision and efficiency.
2. Thermoforming machines
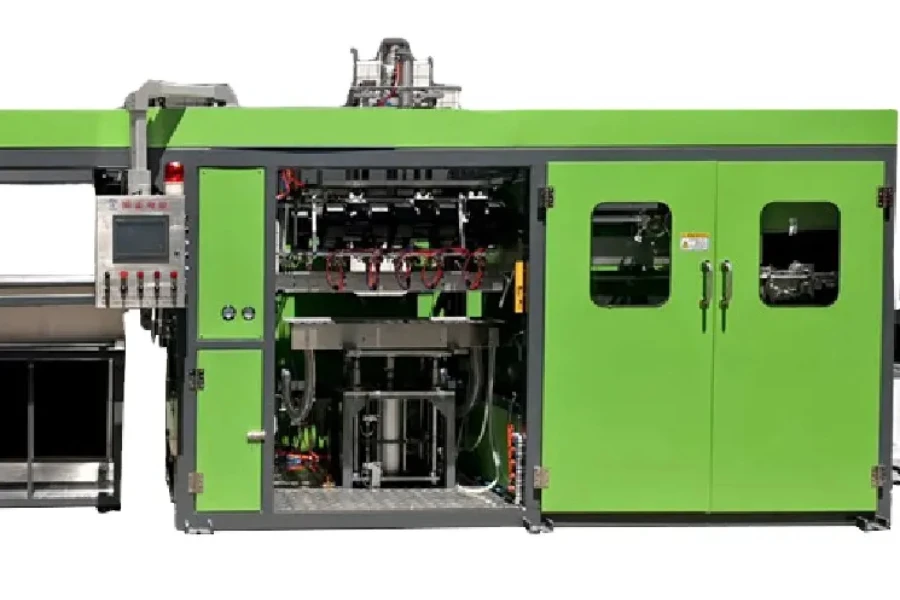
Thermoforming machines are incredibly adaptable and extensively employed in manufacturing various cup types, ranging from plastic and paper to foam cups. These machines use heat to soften a thermoplastic sheet pressed against a mold to achieve the desired cup shape.
Thermoforming machines provide flexibility regarding cup design, enabling rapid production cycles and facilitating the production of cups with diverse thicknesses. Their versatility makes them a preferred choice for businesses seeking to produce cups with customized designs and varying material properties efficiently.
3. Blow molding machines
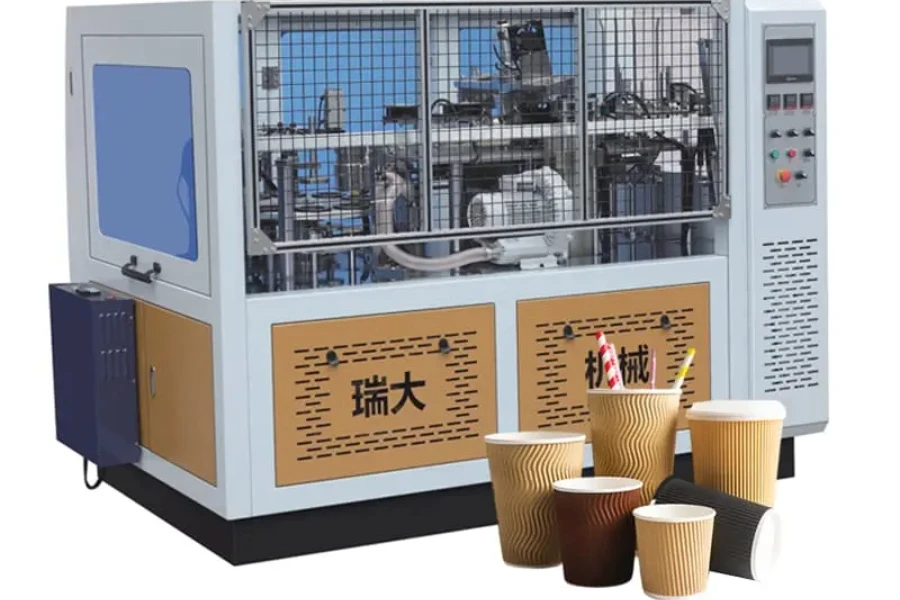
Blow molding machines are extensively employed in producing plastic cups, especially those with distinctive hollow and tapered shapes. They operate by employing a parison, essentially a hollow molten plastic tube. The parison is secured and then expanded by injecting compressed air, causing it to conform to the shape of the cup mold.
Blow molding cup forming machines are renowned for their rapid production speed, cost-effectiveness, and proficiency in manufacturing lightweight cups. They are famous for businesses aiming to achieve efficient cup production with unique shapes and reduced material weight.
4. Paper cup forming machines
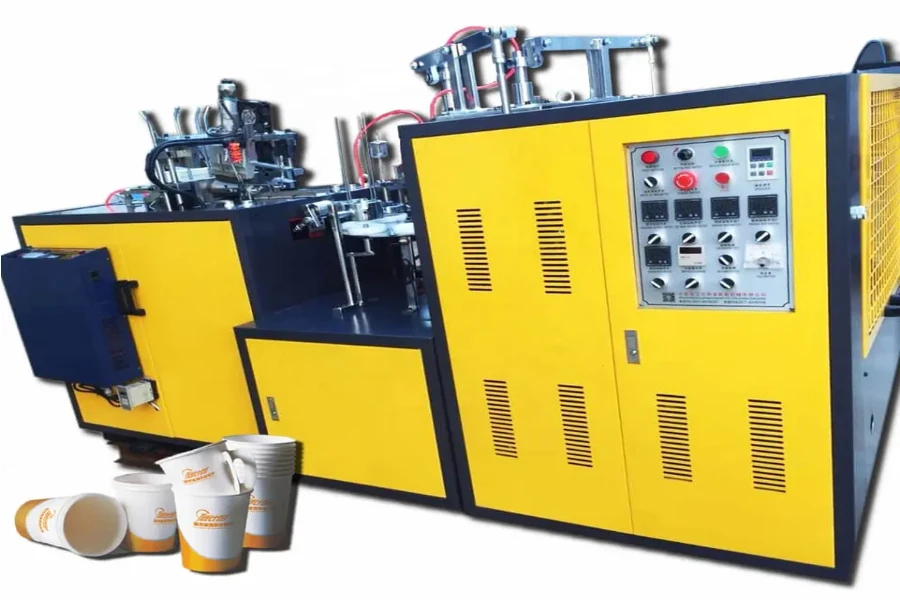
Paper cup forming machines are used for the production of disposable paper cups. These specialized machines primarily involve cutting paperboard into cup blanks, which subsequently undergo a coating process to enhance durability and resistance to leaks. A thin layer of plastic is often applied to the cups for added protection. Paper cup forming machines are in high demand within the food and beverage industry, primarily because paper cups are eco-friendly and easily recyclable.
5. Foam cup forming machines
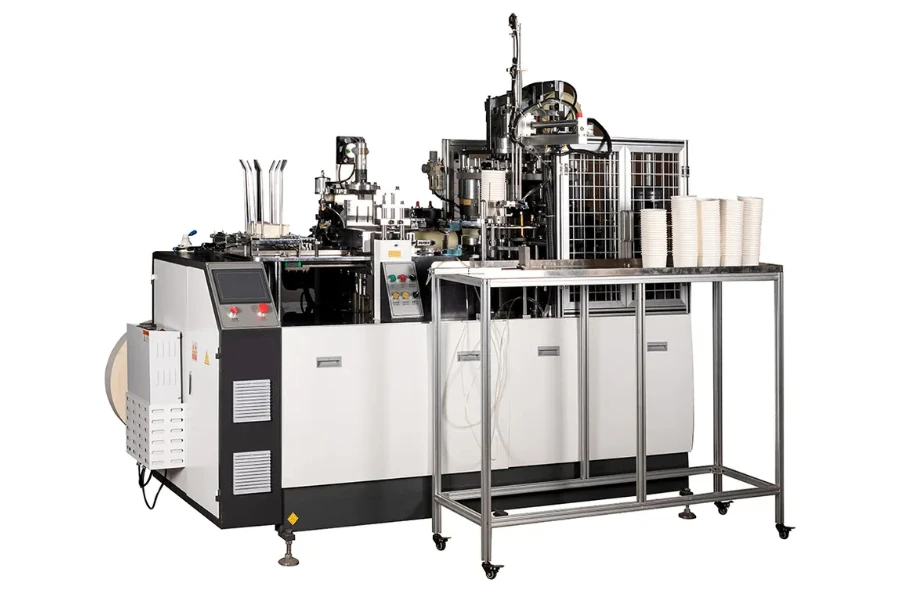
Foam cup forming machines are purpose-built for manufacturing foam cups, which are highly regarded for their exceptional insulation capabilities. These machines employ expanded polystyrene (EPS) or similar foam materials subjected to heating, expansion, and molding to achieve the desired cup shape. The advantages of foam cup forming machines are manifold. They facilitate efficient production, resulting in lightweight cups with excellent thermal insulation.
6. Rotary cup forming machines
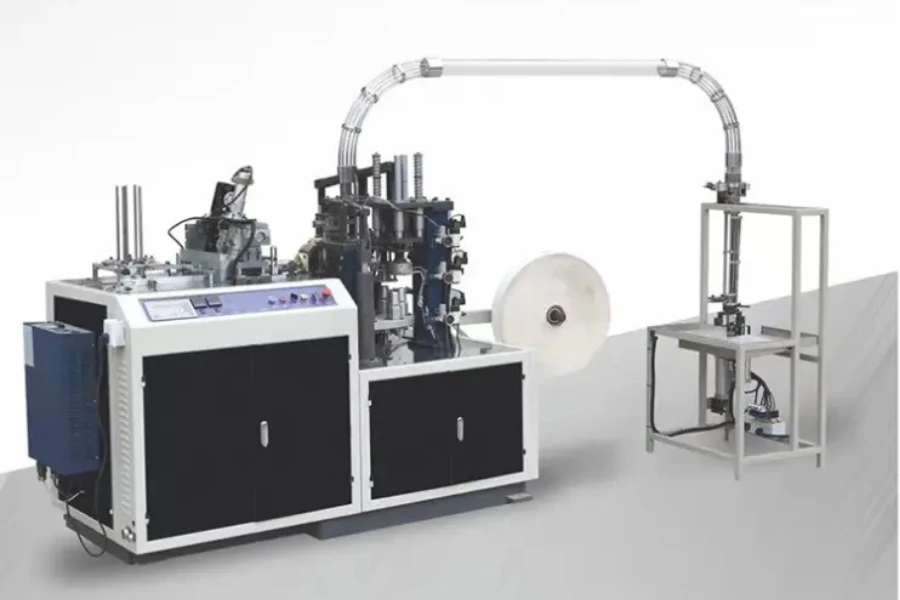
Rotary cup forming machines are exceptionally efficient for large-scale cup production. These machines employ a rotating carousel mechanism that guides cup molds through multiple stages of the forming process. One of the key advantages of rotary cup forming machines is their high-speed production capability, allowing for swift manufacturing of cups.
These machines offer precise control over cup dimensions, ensuring consistent quality. Furthermore, rotary cup forming machines excel in producing cups with intricate shapes or multilayer structures, providing businesses with the flexibility to meet diverse customer demands and innovative design requirements.
Key factors to consider when selecting cup forming machines
1. Cost
Striking a balance between affordability and the desired features and functionalities of the cup forming machine is crucial. On average, cup forming machines can range from US$ 10,000 to US$ 100,000, depending on machine type, production capacity, and additional features. Careful consideration of the cost ensures that businesses make a prudent investment that aligns with their budget and needs.
2. Capacity
You should evaluate cup production requirements and choose a cup forming machine that can efficiently meet volume needs. If necessary, factors such as cycle time, output rate, and the machine’s ability to scale production should be considered. Cup forming machines can have production capacities ranging from 1,000 to 10,000 cups per hour, depending on the machine type and specifications.
3. Size
When purchasing a cup forming machine, consider its physical size and dimensions to ensure it fits well within the production facility. Cup forming machines can have dimensions ranging from 2 to 5 meters in length, 1 to 2.5 meters in width, and 1.5 to 3 meters in height. Evaluating these measurements in relation to available space, businesses can ensure seamless integration, efficient workflow, and compliance with safety regulations.
4. Durability
Prioritizing durability is vital when buying cup forming machines for long-term efficiency. Assessing the construction quality and materials helps select a machine that can withstand continuous production demands. A durable machine minimizes downtime and repairs, with an average lifespan of 10 to 20 years. Regular maintenance and adherence to guidelines extend its longevity.
5. Compatibility
Compatibility considerations should include the machine’s capacity to handle various cup sizes, its versatility in forming different cup shapes, and its capability to work with different materials like plastic, paper, or foam. Choose a machine that can accommodate the desired cup designs and features required for the target market.
6. Cup shape
Consider the machine’s capacity to form various cup shapes (cylindrical, conical, or square) and its capability to work with different materials like plastic, paper, or foam. Only choose a cup forming machine that can accommodate the desired cup designs and features required for the target market.
7. Applicable material
Different cup forming machines are designed to work with specific materials, such as plastic, paper, foam, or eco-friendly alternatives. Evaluate whether the machine can handle the required material thickness and properties to achieve the desired cup quality. Ensuring compatibility between the machine and the intended cup material reduces costs and increases production.
The bottom line
If you are looking to buy cup forming machines, consider factors such as cost, capacity, size, durability, material compatibility, and cup shape versatility. Carefully evaluating these factors can help you buy machines that meet your business needs. Explore a wide range of cup forming machines on Alibaba.com.