In the food processing sector, the bean peeler machine has quietly transformed how beans are prepared. It’s gained recognition from chefs, restaurant owners, and food manufacturers for its impressive ability to quickly remove the outer skin of beans, which makes the preparation of a range of dishes vastly more efficient.
Like any investment, there are essential factors to consider before diving into the world of bean peelers, and in this guide, we will take a closer look at the different types of bean peelers, and explore the crucial considerations to ensure you make the right purchase! So read on for a must-know guide to purchasing bean peelers.
Table of Contents
Overview of bean peeler machines
Types of bean peeler machines
Things to consider when buying bean peeler machines
Conclusion
Overview of bean peeler machines
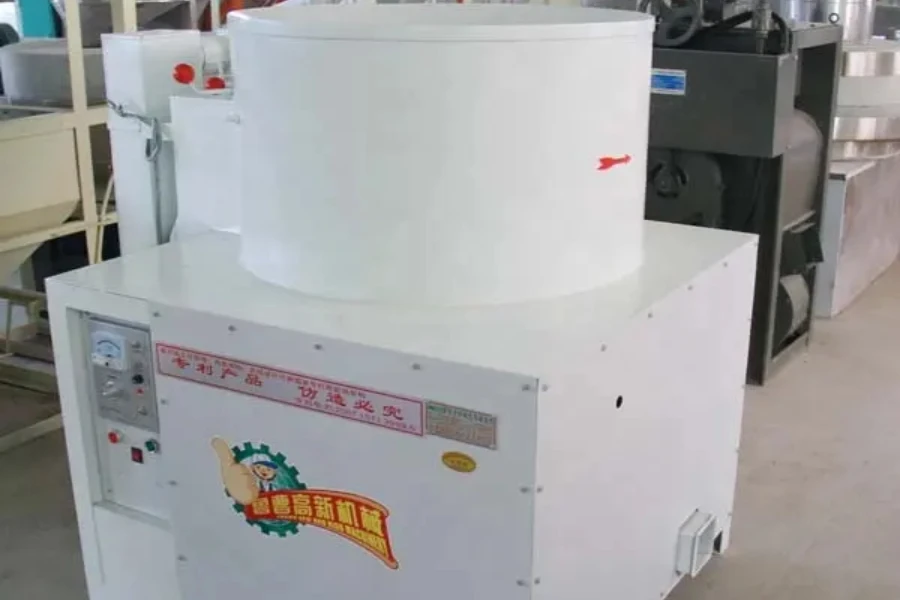
Bean peeling machines are specifically designed to streamline the peeling process, offering time and effort savings in commercial food processing operations. These machines utilize mechanical or abrasive methods, employing rotating drums, discs, or rollers to create friction and separate the outer skin from the bean kernel. Some machines may even incorporate air or water to assist in the peeling process. With their versatility, bean peeling machines can handle various beans, including black beans, chickpeas, lentils, soybeans, and more.
The advantages of using bean peeling machines are manifold. They significantly reduce the need for manual labor, boost productivity, and ensure consistent and uniform peeling outcomes. By removing the outer skin, beans become more convenient to cook, digest, and incorporate into various recipes. Moreover, using peeling machines enhances the overall quality of the final product, elevating its visual appeal and market value.
Types of bean peeler machines
1. Roller peeler machines
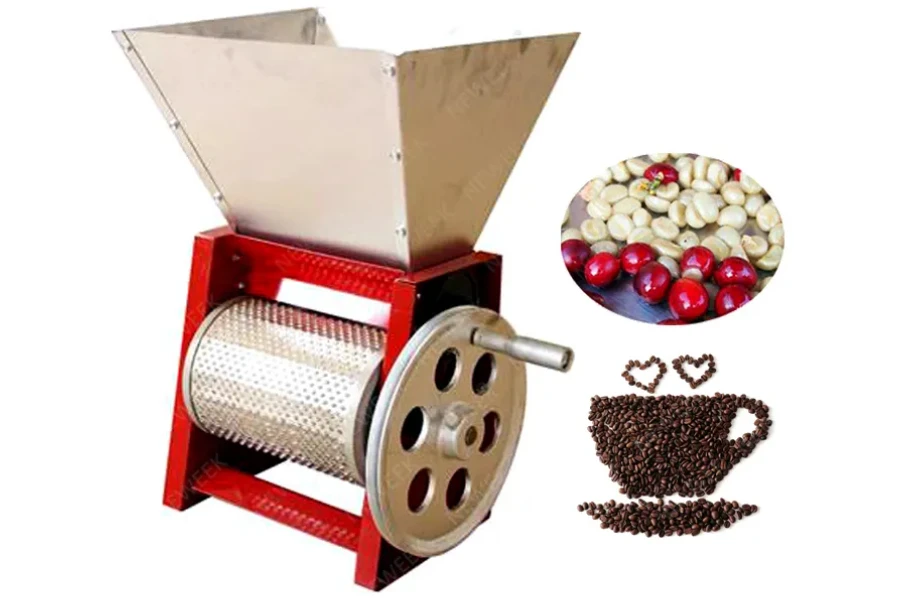
Roller peeler machines use rotating rollers to remove the outer skin from beans efficiently. The beans are fed into the machine, and as they pass through the rollers, the friction between them causes the skin to separate from the kernel. These machines are particularly suitable for larger beans and are known for their reliability and effectiveness. They offer a continuous operation, ensuring consistent peeling results.
Roller peeler machines are adjustable to accommodate various bean sizes, preserving the integrity of the beans while minimizing kernel damage. They are widely used in food processing operations, providing efficient bean preparation and contributing to enhanced productivity.
2. Abrasive peeler machine
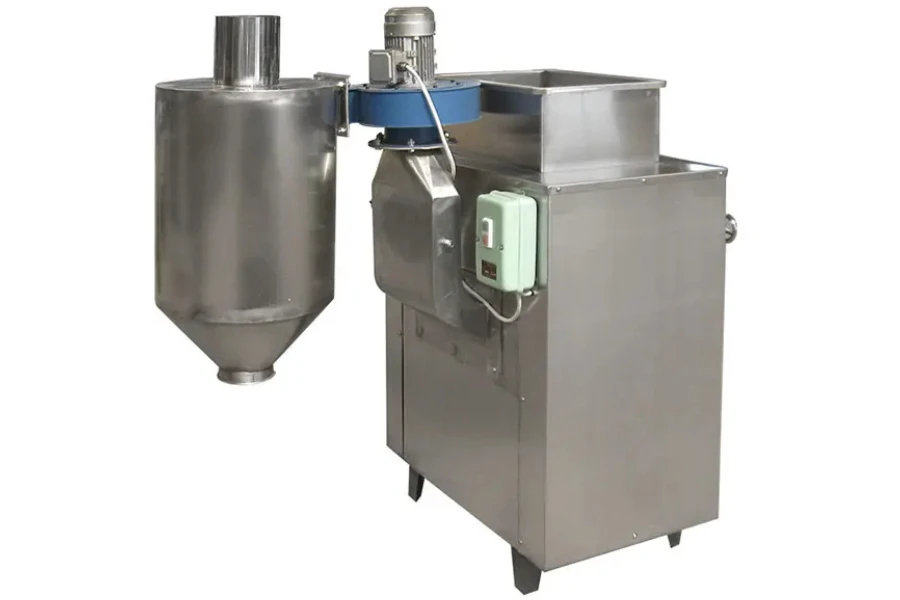
Abrasive peeler machines employ the power of abrasion to strip off the outer skin from beans. These machines have a drum or disc coated with abrasive materials like emery or sandpaper. As the beans enter the machine, they come into contact with the abrasive surface, causing the skin to be rubbed away.
With their versatility, abrasive peeler machines can effectively handle beans of various sizes. Their abrasive action ensures thorough and efficient peeling, making them a valuable tool in bean processing operations.
3. Air-assisted peeler machine
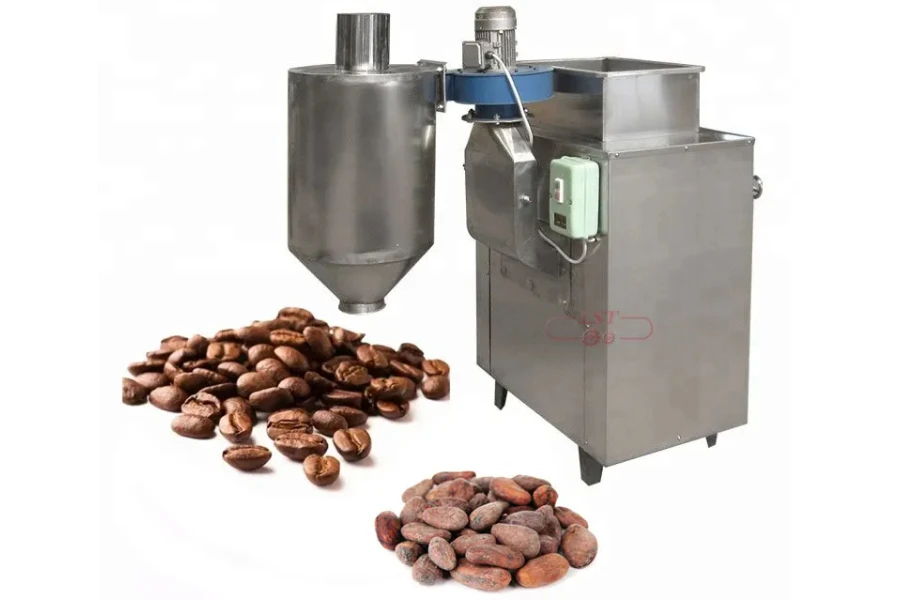
Air-assisted peeler machines employ a combination of mechanical action and air to achieve bean peeling. Equipped with an air blower, these machines generate a controlled airflow that effectively separates the outer skin from the beans. The gentle air current blows away the skin particles as the beans pass through the machine.
This method proves particularly beneficial for delicate beans that may be sensitive to the friction generated by other peeling techniques. Air-assisted peeler machines provide a gentle and efficient peeling process, ensuring the preservation of bean quality while effectively removing the outer skin.
Things to consider when buying bean peeler machines
1. Applicable materials
Applicable materials like the types of beans, sizes, conditions, quality, and the presence of debris should be considered. The bean peeling machine should be designed to handle specific beans, accommodating their size range and effectively peeling them.
Additionally, it should be adaptable to different bean conditions and offer mechanisms to sort out low-quality beans and debris. Consider the machine’s adjustability, durability, and ease of maintenance to ensure long-term reliability and optimal performance in peeling various beans.
2. Production rate
The production rate refers to the number of beans the machine can peel in a specific timeframe, such as per hour or batch. This assessment helps determine if the machine can handle the desired output and prevent potential delays in the processing line. Different machines have varying production rates, with average rates ranging from 100-500 kg of beans per hour, depending on the specific model and design.
3. Price
Assess potential benefits such as labor savings, increased productivity, and maintenance costs. Striking a balance between affordability and the machine’s value in efficiency and performance is key. The average price of bean peeler machines can vary depending on capacity, features, and brand. On average, you can expect prices ranging from US$ 1,000 to US$ 5,000 for smaller to mid-sized bean peeler machines, while larger or more advanced models can cost upwards of US$ 10,000.
4. Size
Evaluate the bean peeler machine’s length, width, and height to determine if it can be accommodated without disrupting workflow or causing congestion. Selecting an appropriately sized machine is crucial for optimizing operational efficiency and maintaining a seamless processing flow.
The average size range of bean peeler machines can vary, but they typically fall within dimensions of 2-4 feet in length, 1-2 feet in width, and 3-6 feet in height. Carefully measuring the available space and comparing it with the machine’s size specifications will help you choose a machine that fits well within your facility.
5. Capacity
It is important to assess the capacity of the bean peeler machine in relation to the amount of beans it can hold and process at a time. Opting for a machine with a suitable capacity is essential for maximizing efficiency and reducing the need for frequent reloading or processing cycles.
The average capacity range of bean peeler machines can vary, but they typically have capacities ranging from 50-200 kilograms (110-440 pounds) of beans per batch.
6. Durability
Seek out bean peeler machines constructed from sturdy materials capable of enduring the demands of continuous operation in a processing environment. Investing in a durable machine guarantees longevity and minimizes the risk of downtime or expensive repairs. Bean peeler machines have a lifespan of 5-10 years, although this can vary depending on usage, maintenance, and specific machine quality.
7. Noise
You need to choose bean peeler machines that operate at a noise level that aligns with your requirements. Opting for a quieter machine can create a more pleasant working atmosphere, reduce noise pollution, and enhance overall workplace satisfaction. The average noise range of bean peeler machines can vary, but they typically operate at noise levels between 70-80 decibels. However, it is advisable to refer to the specific machine’s specifications or consult with suppliers to obtain accurate noise level information.
8. Compatibility
Different bean peeler machines are designed for particular bean varieties, sizes, or moisture levels. Confirm that your chosen machine can efficiently peel the desired beans to achieve optimal results. Consult with suppliers or review product specifications to ensure compatibility with the beans planned to be processed. Doing so can avoid potential issues and guarantee that the machine will effectively meet the peeling requirements, ensuring high-quality results and maximizing operational efficiency.
9. Key components
Choosing machines constructed with stainless materials for durability, hygiene, and corrosion resistance is essential. The control unit plays a crucial role in optimizing the peeling process by offering precise adjustment of parameters. A well-designed conveyor system ensures efficient material flow and gentle handling of beans.
The peeling mechanism should be adjustable to accommodate various bean sizes and deliver effective peeling results. Additionally, consider other key components such as debris separation mechanisms, ease of cleaning and maintenance, and safety features.
Conclusion
To make an informed decision when purchasing bean peeler machines, you must consider factors such as production rate, price, size, capacity, durability, noise level, and compatibility. Evaluating these aspects ensures that the chosen machine meets the processing needs, budget, space limitations, and desired bean types. This leads to streamlined peeling processes, increased productivity, and consistent, high-quality results. If you are ready to find the perfect bean peeler machine for your business, explore a wide range of options on Alibaba.com.