With climate change becoming an urgent reality, businesses have shifted how they approach everyday technologies, including those used in refrigeration and cooling. As a result, CO2 refrigeration systems have emerged as efficient and sustainable alternatives to traditional refrigeration, which use synthetic refrigerants like hydrofluorocarbons (HFCs) that are potent greenhouse gasses with high global warming potential (GWP) values and energy consumption.
On the other hand, CO2 is a natural refrigerant characterized by low environmental impact, a wide range of working temperatures, and energy efficiency. This has led to increased adoption of CO2 refrigeration systems for commercial and industrial use. For example, nearly 25% of food stores in Europe, which is about 65,000 stores, use CO2 refrigeration technology. This represents a significant increase from the 30,000 stores that used transcritical CO2 refrigeration systems in 2019 worldwide.
This blog therefore provides key insights into CO2 refrigeration equipment for retailers, and explores how it may be the most promising cooling system in the industry.
Table of Contents
What is a CO2 refrigeration system?
Global market for CO2 refrigeration equipment
Applications of CO2 refrigeration systems
Technologies supporting CO2 refrigerant adoption
Benefits of CO2 refrigeration
Conclusion
What is a CO2 refrigeration system?
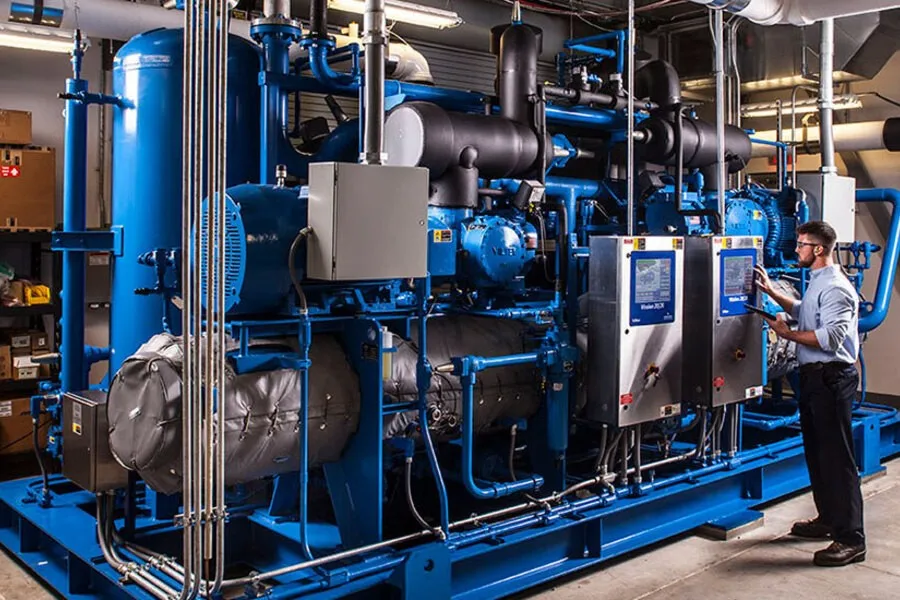
A CO2 refrigeration system is an eco-friendly equipment that uses carbon dioxide (CO2) in the cooling process instead of the synthetic refrigerants like HFCs used in traditional refrigeration units. CO2, or R-744, is a natural refrigerant found in the atmosphere with a GWP of 1 and zero ozone depletion potential (ODP). It is also non-toxic, non-flammable, odorless, colorless, and tasteless. The CO2 refrigeration system comprises various components, including the compressor, condenser, expansion valves, and evaporator.
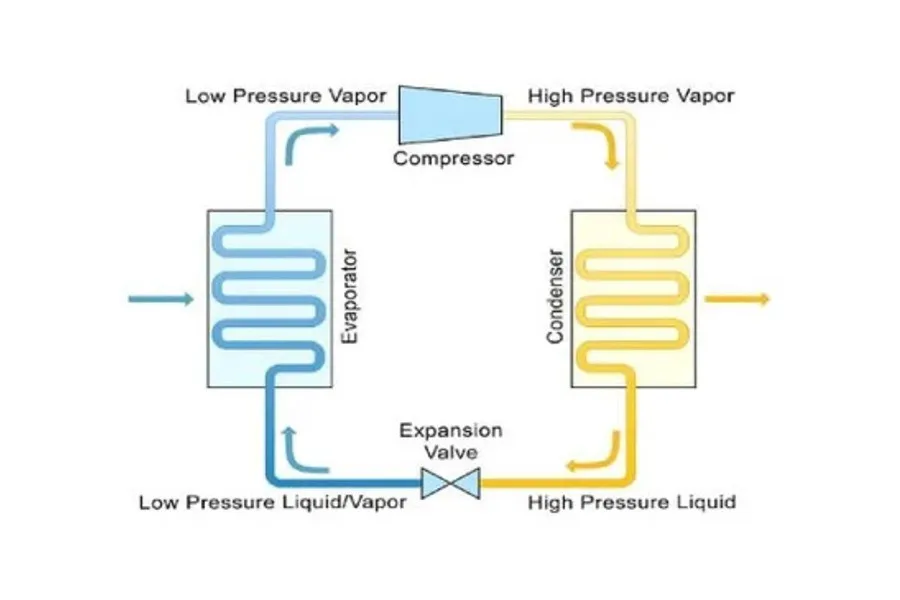
The compressor is a fundamental component used to increase the pressure and temperature of the working gas, which fuels the refrigeration cycle. The high-temperature, high-pressure gas from the compressor is transformed into a liquid state in the condenser. In this component, the system absorbs and sheds the compressed gas, signifying its ability to maintain a cool environment. The refrigerant leaves the condenser as high-pressure, low-temperature liquid and is transferred into the expansion valve.
The expansion valve reduces the liquid CO2’s pressure, consequently decreasing its temperature. In addition, the pressure drop causes some of the CO2 to boil rapidly, turning it into a blend of vapor and liquid. The refrigerant then enters the evaporator as a low-temperature, low-pressure CO2 liquid-vapor mixture. It cools the air in the surroundings by absorbing the heat, thereby evaporating and transforming back into low-pressure gas and completing the cycle.
Global market for CO2 refrigeration equipment
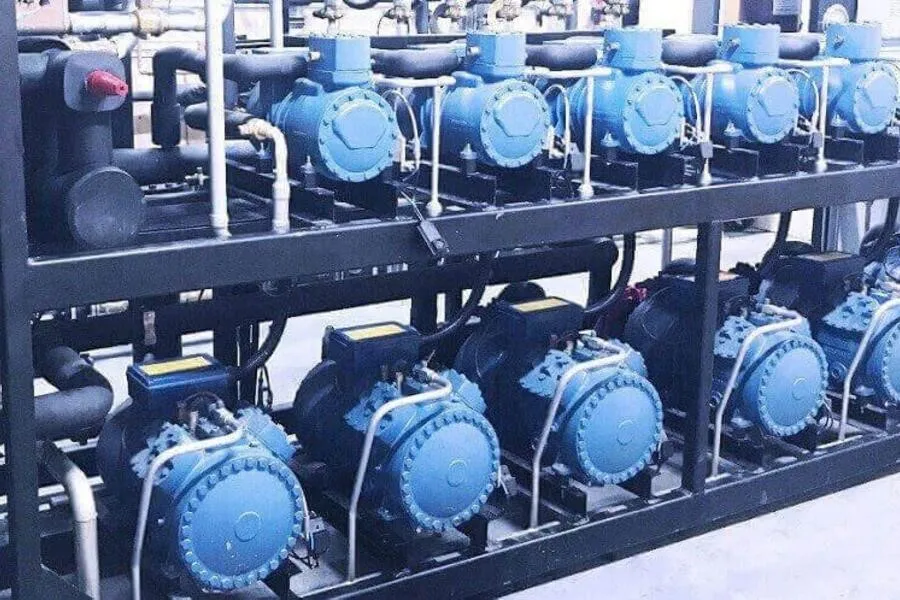
More companies across the world are switching to CO2 refrigeration systems, leading to increased popularity and demand. In 2023, the transcritical CO2 market size was estimated at US$ 48.52 billion. It is projected to reach US$ 140.93 billion by 2030, growing at a compound annual growth rate (CAGR) of 16.5%.
Europe, North America, and Japan make up the largest market for CO2 refrigeration equipment. As the leading market, Europe has approximately 68,500 stores that use CO2 refrigeration systems, of which 60000 have centralized rack systems (stores) and 8500 have CO2 condensing units (industrial sites). Japan has approximately 8385 stores and 400 industrial sites equipped with transcritical CO2 systems. North America has 2930 stores and 498 industrial sites using CO2 refrigeration technology.
Various factors are driving the growing demand for CO2 refrigeration units, including:
- Strict government regulations limiting the use of HFC refrigerants and implementing schedules aimed at phasing down the production and consumption of HFC refrigerants. For example, the American Innovation and Manufacturing Act of 2020 (AIM Act) seeks to reduce HFC to 60% of baseline levels by 2024.
- Ongoing global shift toward environmentally sustainable technologies as companies seek to reduce their carbon footprint.
- Technological advancements in transcritical CO2 equipment, which have led to improved system efficiency, better controls, and improved safety features.
Applications of CO2 refrigeration systems
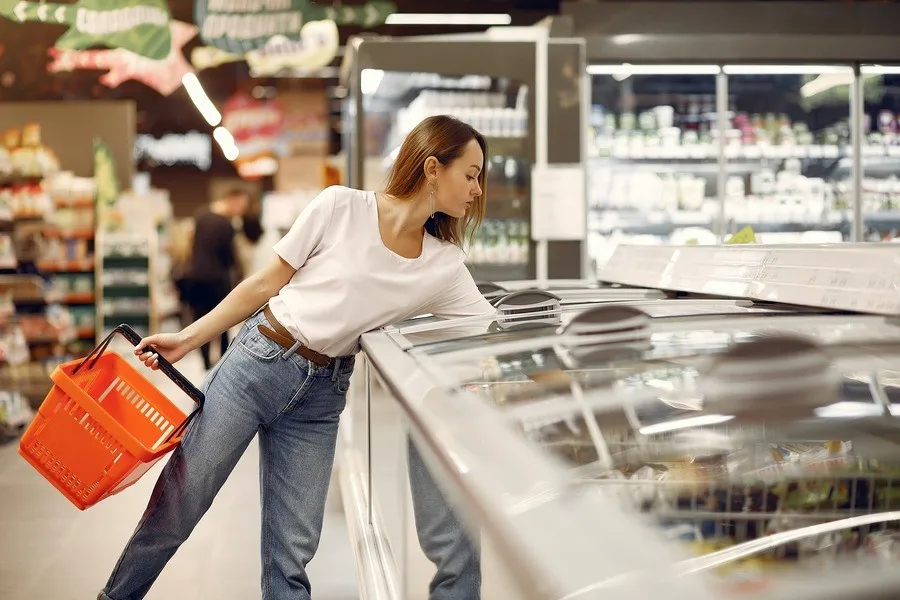
CO2 refrigeration systems are used in various industries and settings, including:
- Industrial settings such as food processing, pharmaceuticals, and manufacturing, for cooling processes and equipment
- Commercial refrigeration, including supermarkets, convenience stores, restaurants, and other food retail establishments
- Cold storage and warehousing, where temperature control is critical for maintaining the quality and safety of stored products
- Refrigerated transportation systems in trucks and trailers for safe transport of temperature-sensitive goods
- In heating, ventilation, and air conditioning (HVAC) systems to reduce their environmental impacts
Technologies supporting CO2 refrigerant adoption
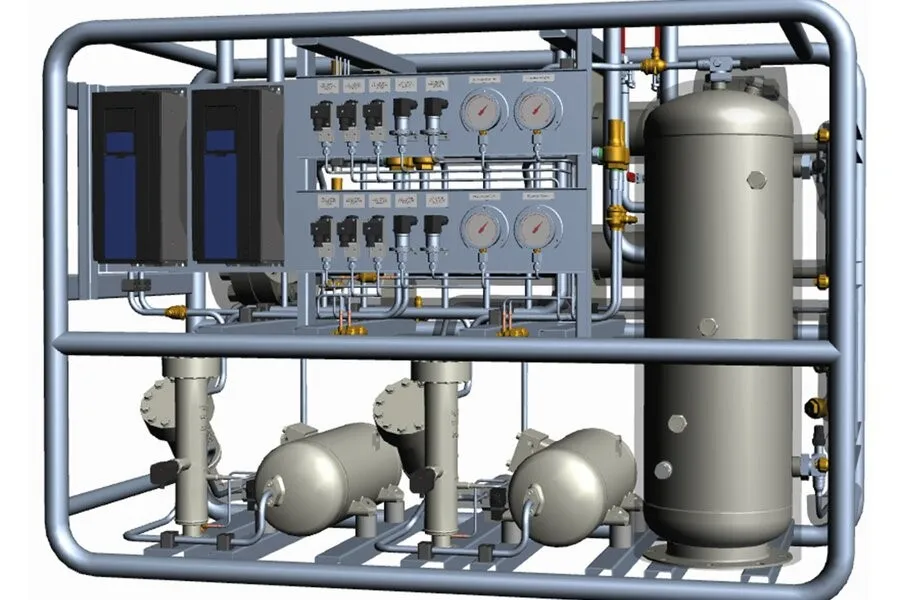
The technologies used in CO2 refrigeration units are continuously evolving, enabling manufacturers to create more efficient and cost-effective equipment. These may include:
Subcritical and transcritical CO2 systems
CO2 refrigeration systems can operate in subcritical or transcritical cycles. Subcritical systems operate below the critical point of CO2 (31.1 ℃ and 7.37 MPa, for temperature and pressure, respectively), while transcritical systems operate above this point. The choice between subcritical and transcritical cycles depends on the specific application and environmental conditions. For example, transcritical cycles are ideal in retail contexts where natural refrigerants are used in booster systems.
Safety features
Safety in a refrigeration system is important. CO2 refrigeration units incorporate various safety features, such as pressure relief devices, leak detection systems, and emergency shutdown mechanisms, to ensure safe operation.
Advanced control systems
CO2 transcritical booster systems integrate advanced control systems that help manage system volatilities and CO2’s high pressures. These control systems are used to monitor and optimize CO2 refrigeration system performance. For instance, they ensure precise temperature control, energy efficiency, and adaptability to varying operating conditions.
Energy recovery systems
In traditional refrigeration systems, the heat generated during the cooling cycle was often discarded. This made heat recovery a major concern among businesses and consumers. Therefore, energy recovery systems in CO2 refrigeration address this challenge by providing solutions for capturing and reusing waste heat generated during the refrigeration process. This technology improves the system’s overall energy efficiency, cost-effectiveness, and sustainability.
Benefits of CO2 refrigeration
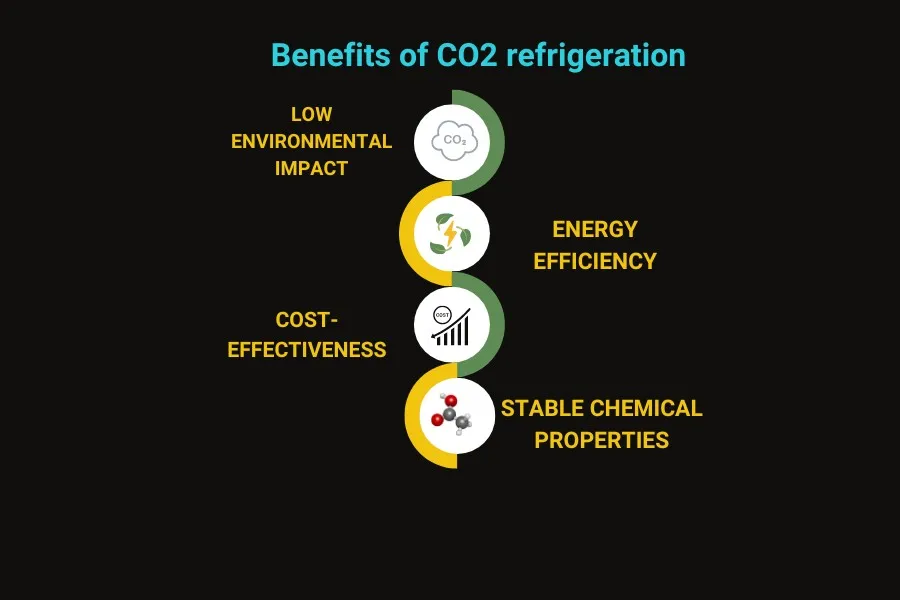
C02 refrigeration systems are transforming the cooling industry, gradually replacing traditional refrigeration equipment. They offer various benefits, including:
Energy efficiency
CO2 has higher thermodynamic performance, which leads to lower energy consumption. In addition, CO2 has a higher discharge temperature (approximately 100 -120°C) than traditional refrigerants, which improves its heat recovery capabilities, index of compression, and heat rejection.
Cost-effectiveness
CO2 refrigeration equipment has relatively lower maintenance and operating costs. For instance, energy efficiency ultimately reduces costs. Besides, the increased research and development (R&D) has led to increased production volumes and integration of advanced innovations, which has brought system costs to parity with those of traditional HFC refrigeration systems.
Stable chemical properties
CO2 refrigerant has stable chemical properties that ensure reliability and safety during operations, such as non-toxicity and non-flammability. Its inert nature helps ensure that it does not react with other substances in the refrigeration system.
Low environmental impact
CO2, as a natural refrigerant, has a GWP of 1 and ODP of 0, which is far less than that of synthetic refrigerants such as CFCs and HCFCs. For example, R-134 and R-404A have GWPs of 1400 and 3260, respectively. These GWP values make CO2 a more environmentally sustainable option. In addition, most of the CO2 used for refrigeration is an industrial by-product released from factories. Therefore, its use as a refrigerant can be regarded as recycling, reducing environmental impact.
Conclusion
CO2 refrigeration units are becoming alternative cooling systems, replacing traditional cooling equipment. From supermarkets to restaurants and manufacturing plants, CO2 refrigeration systems are gradually becoming the preferred cooling mechanism.
This creates an opportunity for businesses to not only champion environmental sustainability but also cater to the increasing demand for eco-friendly solutions in the market. Providing cooling machinery known for its low environmental impact and compliance with stringent environmental regulations enables these companies to position themselves as leaders in responsible practices.
Other than the environmental benefits, CO2 refrigeration systems provide high efficiency and cost savings, which benefits both the businesses and target customers.