In the fast-paced landscape, screening machines are in high demand, gaining widespread popularity across industries for their exceptional benefits. These machines play a pivotal role by efficiently sifting, sorting, and separating materials, improving productivity, saving costs, and offering top-notch product quality. Their versatility makes them indispensable in a range of sectors, from mining to pharmaceuticals.
However, the overwhelming number of manufacturers flooding the market with different models has made finding the perfect screening machine challenging. This guide will highlight the key types of screening machines available on the market today. It will also offer vital tips for selecting the best machines.
Table of Contents
Market share of screening equipment
Types of screening machines
Tips to consider when buying screening machines
Final thoughts
Market share of screening equipment
The demand for screening machines has significantly increased due to their multifaceted advantages and efficiency gains across industries. According to Fact.MR, the global market share of screening machines has already reached a valuation of US$ 6.78 billion, and the figure is anticipated to grow at a compound annual growth rate (CAGR) of 5.6% until the end of 2032. This means the market is expected to have a valuation of around US$ 11.69 billion in 2032.
Screening machines have become essential in achieving quick and precise material separation, reducing waste, improving product quality, and achieving more streamlined processes.
Notably, regions like North America, Europe, and Asia have shown significant demand for screening machines. Industries such as mining, construction, pharmaceuticals, agriculture, and recycling in these regions have embraced these cutting-edge technologies to enhance operations and stay competitive in the global market.
Types of screening machines
1. Vibrating screens
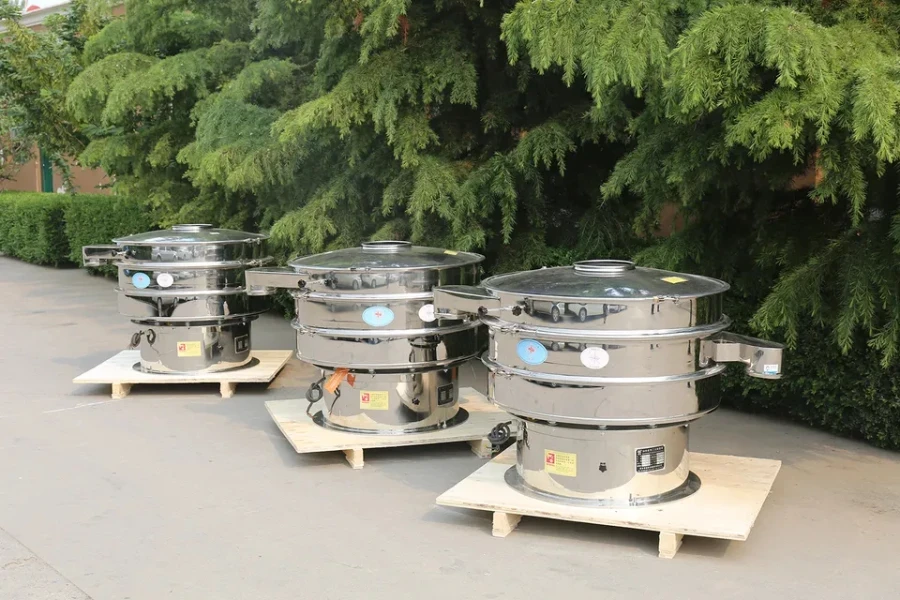
Vibrating screens are incredibly versatile screening machines that rely on vibration to separate and categorize materials according to size. They come equipped with multiple layers of screens, each featuring different mesh sizes to ensure accurate and meticulous material sorting. Due to their adaptability, these screens are widely utilized across diverse industries, ranging from mining and construction to agriculture.
2. Trommel screens
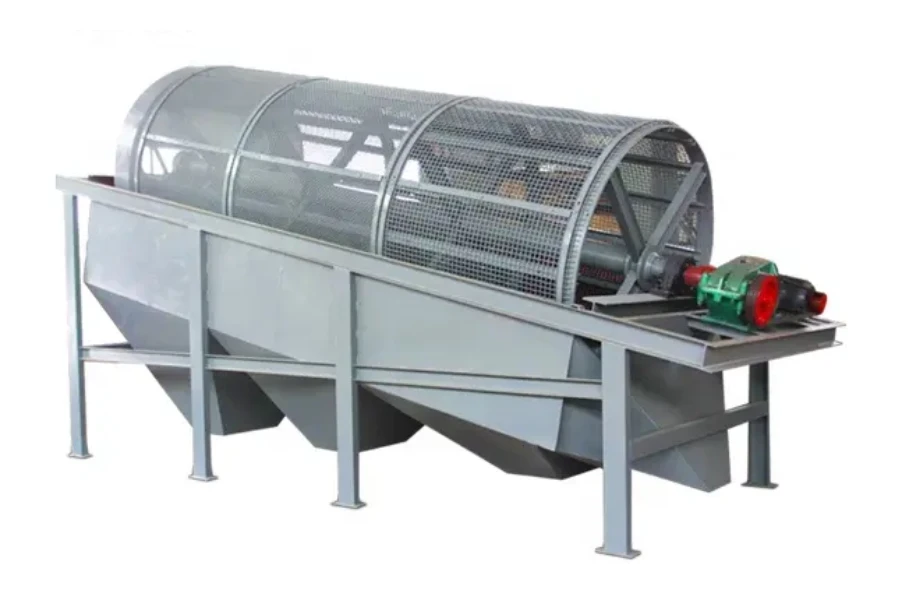
Trommel screens are specialized cylindrical machines that function like drums, expertly separating materials based on size. As the drum rotates, smaller particles effortlessly pass through the screen while the larger ones are held back. These screens find widespread application in diverse fields such as waste management, composting, and mining operations, proving their efficiency and versatility in handling various materials.
3. Rotary screens
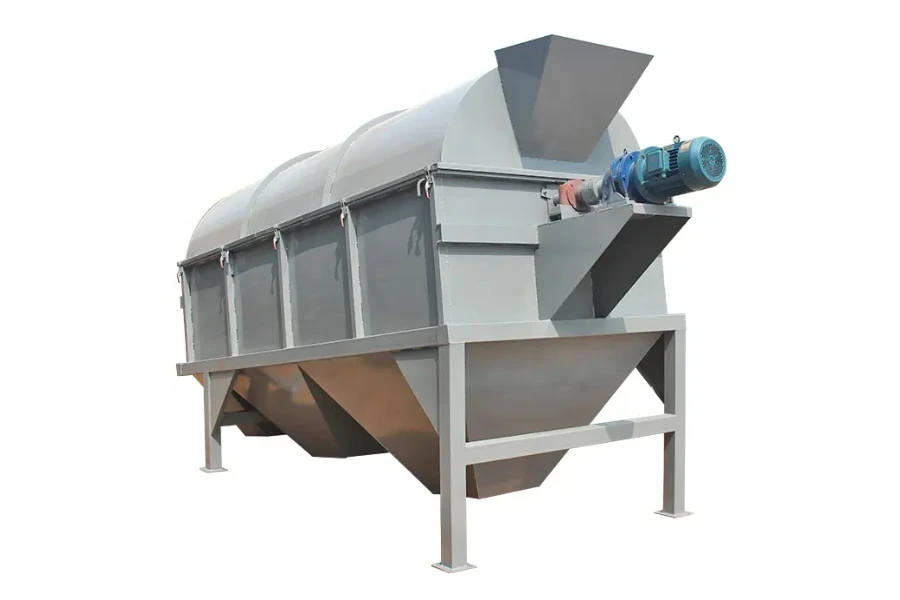
Rotary screens, also called drum screens, work on a principle similar to trommel screens but with a more compact design. They feature a rotating drum equipped with perforated plates or mesh that effectively separates materials according to size. These versatile screens find frequent usage in various industries, including wastewater treatment, paper pulp processing, and textile manufacturing, owing to their efficient material separation capabilities.
4. Disc screens
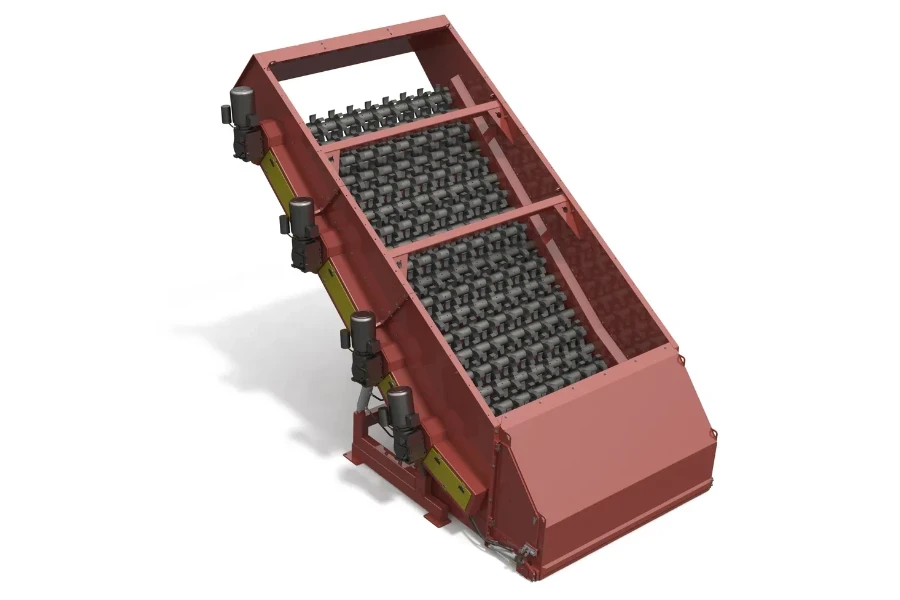
Disc screens employ rotating discs strategically spaced apart to separate material. As materials move across the discs, smaller particles slip through the gaps effortlessly while larger ones continue their course. These screens are extensively utilized in recycling facilities, effectively sorting diverse recyclable materials and enhancing the overall efficiency of the recycling process.
Tips to consider when buying screening machines
1. Cost
Take a close look at the initial investment required and consider the average price range for the specific type of screening machine you’re interested in. The average cost range for different types of screening machines can vary significantly depending on factors such as brand, model, capacity, and features. Vibrating screens typically range from US$ 10,000 to US$ 80,000, trommel screens from US$ 30,000 to US$ 200,000, rotary screens from US$ 15,000 to US$ 100,000, and disc screens from US$ 20,000 to US$ 150,000.
2. Capacity
Look for the average throughput per hour or day for the specific type of screening machine you’re interested in. The capacity of screening machines can vary significantly based on their type and size. Vibrating screens typically have an average capacity range of 50 to 800 tons per hour, trommel screens range from 100 to 1,500 tons per hour, rotary screens range from 50 to 500 tons per hour, and disc screens range from 20 to 300 tons per hour.
Selecting a screening machine with a capacity that matches or surpasses the anticipated materials volume is vital. This ensures smooth and uninterrupted operations, preventing bottlenecks and maximizing productivity in line with production needs.
3. Efficiency
Check the screening accuracy, ranging from 80% to 95%, indicating how effectively the machine separates materials of different sizes. Also, consider the percentage of fines removed, which typically falls within the range of 70% to 90%. Lastly, look at the overall yield, varying from 60% to 95%. Higher efficiency means the machine can achieve more accurate material separation, increasing productivity and reducing material waste in operations.
4. Durability
Focus on the construction materials used for the screening machine and thoroughly research the manufacturer’s reputation. Investing in a durable machine can result in longer service life, with some machines lasting anywhere from 10 to 20 years with proper maintenance. Prioritizing durability minimizes disruptions to operations, reduces the frequency of replacements, and ensures smoother and more reliable screening processes over the years.
5. Compatibility
Thoroughly examine the machine’s dimensions, connections, and adaptability to integrate into the production line seamlessly. Check if the machine aligns with the current infrastructure to avoid potential delays and costly modifications. Additionally, consider the compatibility of the machine’s output with downstream equipment. A compatible screening machine can streamline operations, facilitate a smoother material flow, and optimize production.
6. Noise level
You need to check the average decibel rating of each screening machine and how it may affect the working environment. Vibrating screens produce noise levels between 70 to 85 decibels, trommel screens generate around 80 to 95 decibels, rotary screens typically range from 75 to 90 decibels, and disc screens produce noise levels of approximately 70 to 85 decibels.
To maintain a comfortable and safe workplace, consider opting for models equipped with noise-reduction features, which can help mitigate the impact of operational noise on employees and ensure a conducive working environment.
7. Speed
Look for the average screening rate or throughput to determine how quickly each machine can handle materials. On average, vibrating screens can achieve screening rates of 100 to 500 tons per hour, trommel screens can process materials at rates ranging from 50 to 800 tons per hour, rotary screens typically have throughput capacities between 50 to 1,000 tons per hour, and disc screens can process materials at rates of 50 to 300 tons per hour. Opting for a faster machine can significantly enhance productivity and reduce processing time.
Final thoughts
The demand for screening machines continues to soar as businesses recognize their efficiency gains and cost-effectiveness. However, finding a suitable screening machine amidst numerous options can be challenging. To make an informed decision, consider crucial factors such as cost, capacity, efficiency, durability, compatibility, noise level, and speed.
For a wide range of high-quality screening machines, visit Alibaba.com and discover the perfect solution to enhance your operations.