Plastic packaging material is one of the important applications of masterbatches. This type of packaging material is characterized by being lightweight yet having good mechanical properties, suitable barrier and permeability, good chemical resistance, good moldability, low processing costs, and good secondary processing and decorative qualities. It has become the most widely used and broadly applied among metal, ceramic, paper, plastic, and fiber packaging materials.
Masterbatches offer solutions to enhance the applicability of plastic packaging materials
Packaging serves to protect goods, facilitate their use, and provide product information to consumers. During the molding process of plastic packaging materials, the addition of plastic masterbatches not only imparts the required color to the packaging materials but also enhances the processability and fastness of the plastic products (such as light resistance, heat resistance, migration resistance, etc.), and can also provide other functionalities (such as flame retardancy, antibacterial, antistatic, barrier properties), thereby offering a comprehensive solution to improve the usability of plastic packaging materials.
Depending on the composition of the additives used, masterbatches in plastic packaging materials can be divided into two types: color masterbatches (the main component is coloring agents), and functional masterbatches (e.g. anti-ageing additives, anti-static agents, flame retardants, fillers, etc.).
1. Color masterbatch
Color masterbatches are currently the most widely used method for coloring plastics. Different colorants give plastic products various color characteristics, such as chroma, coloring strength, coverage, transparency, and color fastness (for example, resistance to sun exposure, weather, solvents, migration, and heat).
For plastic packaging, the purpose of coloring is not only to meet the general color marking requirements but also to capture the consumer’s attention, thereby increasing product sales. Plastic color masterbatches can provide the required colors based on customer demands.
In addition to traditional non-color series like white, black, and gray, and common colors like red, orange, yellow, green, blue, cyan, purple, and brown, various special color effects such as pearlescent, metallic, multi-angle color change, thermochromic, photochromic, whitening, glow-in-the-dark, fluorescent, marble pattern, wood grain, glitter or speckle effects are available, giving packaging products unique visual effects and enhancing product appeal.
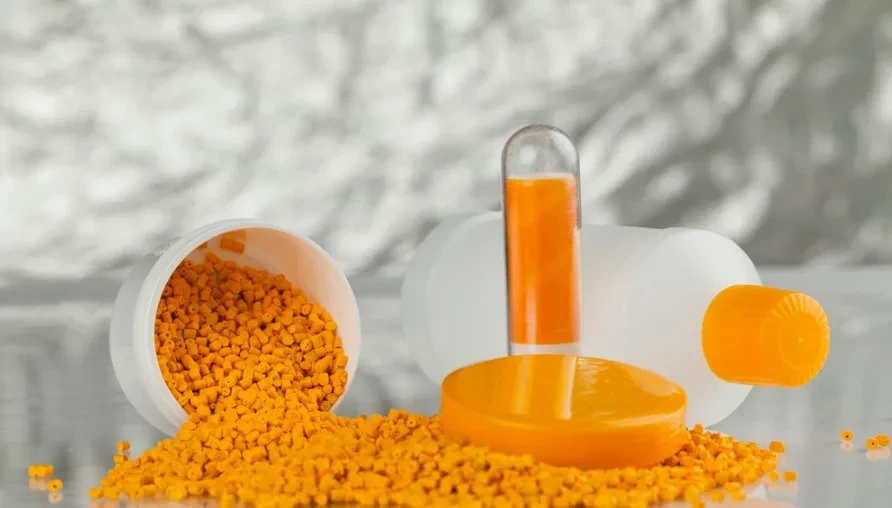
2. Functional masterbatch
Functional masterbatches contain functional additives other than colorants. The specific functions depend entirely on the effective components contained. These functions can be broadly divided into three categories:
Improving plastic molding processability
This includes processing aid masterbatches that reduce die buildup and eliminate melt fracture; cooling masterbatches that lower molding processing temperatures; drying masterbatches that absorb moisture in raw materials; slippery masterbatches that facilitate the demolding of injection-molded parts; anti-slip masterbatches that prevent film from slipping during winding; anti-blocking masterbatches that prevent film layers from sticking during unwinding; and purging masterbatches that save on materials during color changes. Using these types of functional masterbatches not only facilitates the molding process but also improves product quality, increases production efficiency, and reduces energy consumption.
Improving the physicochemical properties of plastics
This includes antioxidant masterbatches that improve thermal aging resistance and prevent yellowing of parts; anti-aging masterbatches that improve the weatherability of finished parts; nucleating or clarifying masterbatches that increase the rigidity or transparency of molded parts; toughening masterbatches that enhance the mechanical properties of molded parts; slippery masterbatches that reduce the surface friction coefficient of molded parts; opening masterbatches that reduce the torque required to open bottle caps; thermally conductive masterbatches that improve the thermal conductivity of plastic parts; electrically conductive masterbatches, and filler masterbatches that improve the mechanical properties of plastics and reduce costs.
Adding application functions to products
This includes antistatic masterbatches that reduce the surface resistance of molded parts; flame retardant masterbatches that enhance the fire resistance of materials; antibacterial masterbatches that increase resistance to microbial invasion; barrier masterbatches that improve the barrier properties of plastic packaging against gases (such as oxygen, carbon dioxide, water vapor); biodegradable masterbatches that reduce plastic pollution; deodorizing masterbatches that remove odors; flavoring masterbatches that add scent to plastics; anti-fogging masterbatches that reduce fogging on the inner surface of food packaging films; rust-preventive masterbatches that prevent rusting of electronic components; laser-marking masterbatches that provide laser marking effects; matte or sanding masterbatches for matte or sanding effects, and foaming masterbatches that provide lightweight, thermal insulation, sound insulation, and shock absorption functions.
Generally, masterbatches serve a single function, such as color masterbatches providing only color, or antistatic masterbatches providing only antistatic functionality. Sometimes, based on the end-use requirements of the product, dual or multifunctional masterbatches may be needed, such as those that both color the plastic packaging material and improve application performance like anti-aging, thereby combining colorants and anti-aging agents in a single masterbatch, known as multifunctional masterbatches.
Factors to consider in masterbatch formulation
When formulating a masterbatch, manufacturers need to consider various factors, including:
- The requirements of the end application
- The shape of the end product
- The type and specifications of the resin used for molding
- The molding method and processing conditions
- The addition ratio of the masterbatch
- Regulatory compliance requirements for the product
- Control requirements and inspection methods for critical performance characteristics
- Acceptable price and anticipated usage volume
For instance, in designing a formula for a blue masterbatch intended for beverage bottle caps, it is crucial to understand:
- The type of beverage (carbonated, juice, tea, water)
- The material (PP, HDPE)
- The type of cap (single-piece, two-piece, 38mm, 28mm)
- The molding method (injection molding, compression molding)
- The highest processing temperature
- The masterbatch addition ratio
- The method of color determination (visual, instrumental measurement)
- If measured instrumentally, the measurement conditions (sample form, sample thickness, light source, color space selection, color difference range)
- The need for secondary processing (printing, assembly)
- Compliance with regulations (Chinese standards for food contact materials, European standards, US FDA regulations), etc.
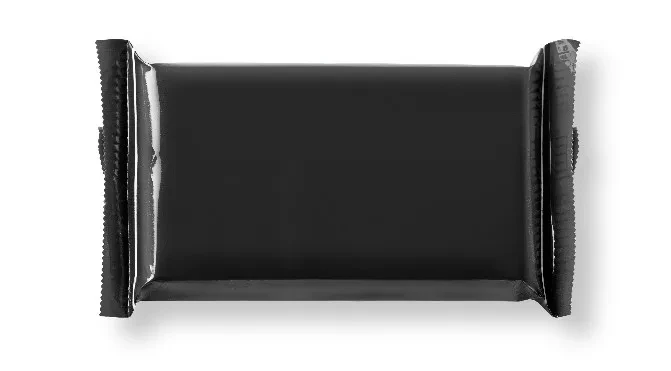
Achieving a single color can involve various color matching schemes, but different colorants come with different properties and costs. Even within the same type of colorant, products from different manufacturers can differ in performance and price. However, even if the colors from several schemes are very similar, it doesn’t guarantee that other properties like heat resistance, dispersibility, migration resistance, and dimensional stability will also be similar, affecting their suitability for use. This can lead to significant cost differences in the masterbatch.
High-quality plastic masterbatches typically exhibit several characteristics:
- Good compatibility with the molding resin
- Good dispersion of functional components
- Good moldability and processing properties
- Non-toxicity and environmental friendliness, meeting the regulatory requirements of relevant industries
- High dilution ratio (i.e., low addition level required)
- Good batch-to-batch quality stability
- High cost-performance ratio
Generally speaking, a masterbatch that provides only one functional enhancement to plastics is called a single-function masterbatch. For example, a color masterbatch provides only color, and an antimicrobial masterbatch provides only antimicrobial functionality. Sometimes, based on the end-use requirements of the product, a dual-function or multi-function masterbatch may be needed. For instance, if a plastic packaging material needs to be colored and also have improved application performance such as anti-aging, colorants and anti-aging agents can be compounded together in one masterbatch, creating a multi-function masterbatch.
16 common functional masterbatches
1. Smooth masterbatch
Adjustable slip and anti-adhesion properties, good anti-adhesion properties and increased slip without affecting strength and dimensional stability at high temperatures.
2. Open masterbatch
Enhances the slipperiness of the film surface and has certain anti-static properties, prevents film-to-film bonding, and increases the openness of the tube film.
3. Anti-aging masterbatch
Extends the life cycle of the film by absorbing and truncating those UV rays that cause film aging. The main constituent substances are: light stabilisation, UV absorbers, and heat aging protectors.
4. Anti-corrosion masterbatch
Prevents rusting and chalking of plastic parts in the contact area of metal inserts.
5. Water-absorbing masterbatch (moisture-proof, defoaming masterbatch)
Eliminate the problems caused by moisture such as bubbles, clouds, cracks, spots, etc., and have no adverse effect on the physical and mechanical properties of the products.
6. Degradation Masterbatch
Widely used in PE, PP and other major raw materials, so that its products (such as agricultural film, bags, cups, plates, discs, etc.) degrade on their own after use, without any pollution to the natural environment.
7. Flavour masterbatch
The fragrance retention time can be up to 10 to 12 months, and can be applied to toys, daily necessities, stationery products, automobile interior accessories and packaging of beauty and cosmetics.
8. Transparent Masterbatch
Improve the transparency of products.
9. Foam Masterbatch
Elimination of shrink marks and dents (shrinkage) on the surface of manufactured parts, foam weight reduction, and reduction of raw material costs at the same time.
10. Cooling masterbatch
It is mainly used for PP and can probably cool down 30 to 50°C.
11. Filled masterbatch
In addition to calcium carbonate, there are talc, wollastonite, graphite, kaolin, mica and other inorganic mineral materials used as fillers in plastic products, which can be widely used in PE, PP, PS, ABS and other plastic products.
12. Antistatic masterbatch
It is obtained by high-speed mixing of carrier and antistatic system, extrusion moulding, and then granulation, which is used to reduce the surface resistance of the material, and prevent the adverse effects of static electricity to various industrial sectors and human beings.
13. Antimicrobial masterbatch
With a certain amount of antibacterial masterbatch and the corresponding resin particles mixed, according to the plastic, fibre processing and moulding methods, can be produced with antibacterial effect on the surface (bactericidal and bacteriostatic effect) of the plastic parts, products and antibacterial fibre.
14 Enhancement Masterbatch
Enhancing the strength of target materials, its modified materials can be widely used in construction, machinery, electronics, electrical appliances, automobiles, transport, daily necessities, agriculture and other manufacturing industries.
15. Brightening masterbatch
Also called bright masterbatch, the purpose is to improve the brightness of the products; its main brightening agent has ethylidene bis stearamide, general masterbatch dosage of 20% to 30%, the products are 0.2% to 0.3%, too much will affect the printing effect of the products.
16. Flame retardant masterbatch
Mainly used in flame retardant modification occasions, composed of flame retardant + resin + additives.
Disclaimer: The information set forth above is provided by Shanghai Qishen Plastic Industry independently of Alibaba.com. Alibaba.com makes no representation and warranties as to the quality and reliability of the seller and products.