Plastic welding is an art that requires skill and precision to produce a quality result. Heating techniques must be chosen correctly, and the temperatures and pressures must be just right for the appropriate level of plastics to be formed.
A major factor impacting the quality of the plastic weld is the precise timing needed to ensure both surfaces are soft enough at once. Furthermore, proper cooling must also occur after all materials are assembled.
With so many details needing attention, it is no wonder why plastic welding has only become widespread in recent decades. It takes considerable knowledge of thermoplastics and experience and finesse to create strong and long-lasting bonds.
This article will give an overview of the market for plastic welding machines, and then give essential suggestions that will allow one to ensure they are choosing the right machine, and method, for the job.
Table of Contents
What is the global market size of plastic welding machines?
Different types of plastic welders
Test the plastic material to determine welding methods
How to ensure you weld plastic safely?
Final thoughts
What is the global market size of plastic welding machines?
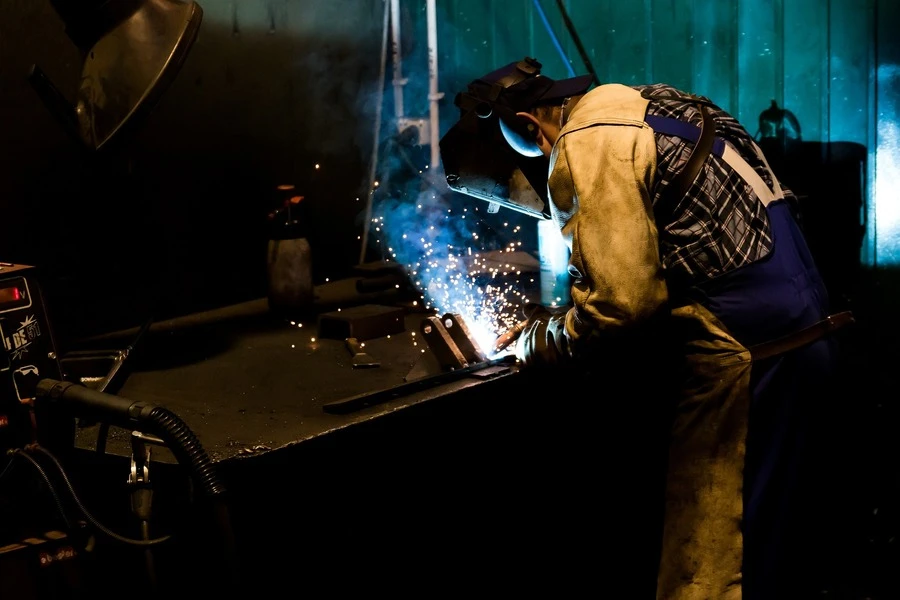
As the importance of welding continues to rise worldwide, the industry has seen incredible growth in recent years. The global welding market is projected to surge from US$ 20.99 billion in 2021 to US$ 28.66 billion by 2028 (Fortune Business Insights). This equals a 4.6% compound annual growth rate (CAGR), reflecting the unprecedented demand for this essential technology.
The growing application scope within welding, enabled by enhanced tools and added automation, is driving this incredible transformation process. It includes innovations like 3D printing systems and robotics-as-a-service being adopted more frequently. If the forecasted projections are achieved, we can expect significant advances in this field as companies strive to capitalize on these emerging trends.
Companies in the industry are responding to this largely positive movement by deploying various tactics such as launching new products, expanding into markets across multiple regions, and strategic agreements to stay firmly planted in their current positions in the market.
Different types of plastic welders
Joining thermoplastic materials doesn’t have to be a challenge. Plastic welding, completed by specialized tools like plastic welders, is the best way to attach the plastic pieces together. This will ensure optimal durability and strength. Before selecting which type of welder is right, it’s important to know all available options, as different plastics require different joining methods.
Depending on the material being joined, various types of welders are available. These include hand-held stick models, airless variants, extrusion kinds, and even injection options. For starters, it’s important to understand what needs to be done and the materials involved.
Identify the plastic
The first step is to understand the plastic type. Every blend has its identifying number printed somewhere on the material itself.
Alternatively, there is an option for analysis from a testing lab. Burning small amounts to detect distinctive odors is one way to determine what kind it is. However, taking cautionary safety measures like protective goggles and gloves is vital.
Plastic welder type 1 – hot air welders
A hand-held hot air welder, or “stick welder,” is a popular choice for portable plastic welding. These tools use heat to soften the material while simultaneously melting and fusing rod materials to create strong bonds between pieces of melted plastic.
It is important to maintain consistent downward pressure on the piece being welded, even distance from the heating source, and working speed when applicable. When shopping around for these types of welders, look for features such as adjustable air compressors that control the work environment.
Other essential features include a fine-tunable multi-element heating pad which can help ensure precise temperatures throughout long bouts of usage.
Plastic welder type 2 – airless plastic welder
An airless plastic welder is an innovative tool that uses a heating element to melt plastic instead of relying on outside airflow. It’s perfect for precision joint welding, as the final weld should penetrate 75% of base materials. Afterward, allow it at least 30 minutes to cool down to ensure optimal performance.
Plastic welder type 3 – extrusion welder
Extrusion welding is perfect for bigger jobs that require a larger welded bead. But remember that these are floor-standing machines of considerable weight and size. If the workspace is limited, this welder may not be suitable. The machine’s heft ensures enough pressure during welding to get those large projects done right.
Plastic welder type 4 – injection welder
Injection welders are the perfect choice for those who need to be mobile and want a reliable, high-quality bond. These devices have adjustable aluminum tips that control welding sizes to get an ideal finish every time.
Test the plastic material to determine welding methods
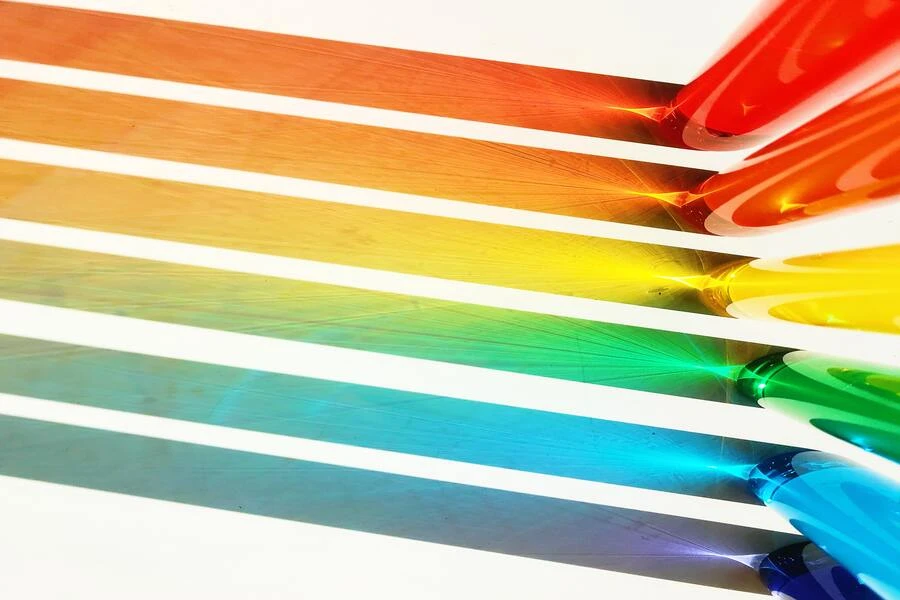
Identifying the right plastic for a project can be tricky. Luckily, it’s much simpler than some people think. Using just four tests and either a testing lab or at-home tools, anyone with an eye for detail should have no trouble distinguishing between materials.
Knowing what type of material to use is key. After all, choosing the wrong welding rod could significantly weaken weld quality in one fell swoop.
Scratch test
When working with plastics and figuring out what type of material it is, giving the surface a scratch test might be helpful. If a fingernail leaves a mark, the plastic must belong in one of those softer categories like PE or PP – ruling out materials such as ABS and PVC, which tend to have higher hardness levels.
Sound test
By listening to the distinct sound of a dropped plastic sample, one can identify and distinguish different types of plastics. Experienced professionals can even differentiate between members within each family by taking note of subtle differences in their tones. Drop the material from roughly 5-10 inches (or 10–25 cm) onto an even surface to properly hear these nuances.
Floating test
A simple and easy way to identify any plastic is by comparing its specific weight with that of water. To start, fill up a glass of clear room temperature water and cut small samples from the desired material. Now add it into the mix. If it floats, it is either Polyethylene or Polypropylene, as all other plastics will sink.
Burning test
It’s likely the most accurate DIY method available, requiring minimal effort for maximum accuracy. Simply find an area with fresh air ventilation and scratch off a small sample over a heat-resistant surface (not your hand). Use a lighter or flame to ignite it, but avoid matches, as these produce sulfur odors that can interfere with results.
As helpful reference points, keep samples from materials whose origin is known – sometimes even stamped on their exterior. This will help to ensure that there is something reliable to compare against unknown plastics when assessing reaction behaviors and smells produced by combustion.
Discovering and identifying plastic material is possible with these four specialized tests mentioned above. With this information, the project is already one step closer to completion.
How to ensure you weld plastic safely?
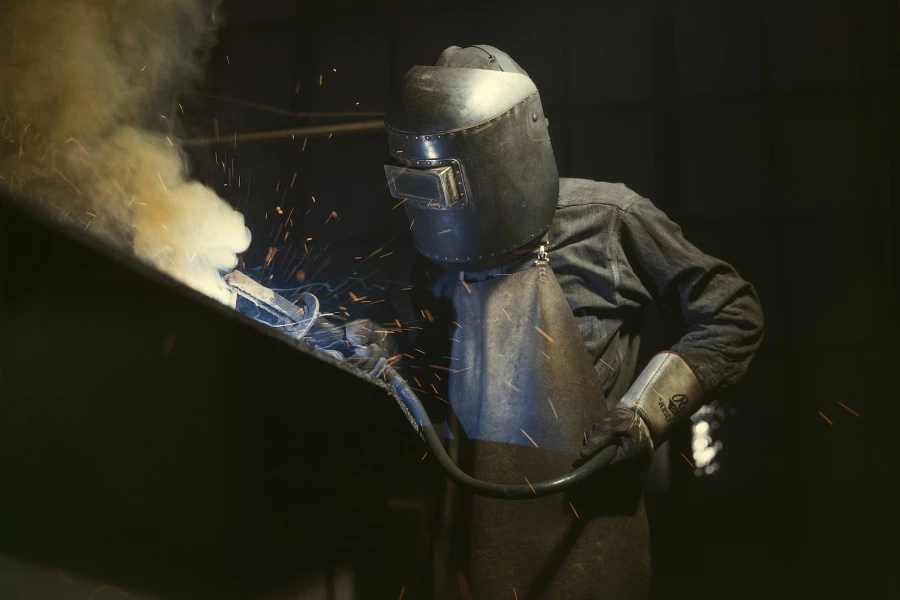
One must observe the following precautions to ensure they complete their projects safely:
- When setting up, always turn on the airflow before igniting the heating element and keep it running until after turning off the power. This prevents the burning out of critical parts.
- Be careful when handling metal components; wait for them to cool down and only use pliers for changing tips or removing welding nozzles from guns.
- Turn off the electricity but not the airflow. This helps increase cooling time so that elements last longer.
- Never put a welder in a vise to change parts, and keep it away from children at all times! Beyond this, always practice safe welding habits.
Final thoughts
As tech advances rapidly, the machinery and suppliers offering such services will only grow in number. Therefore, wholesalers and retailers should stay up-to-date with market needs and upgrades to cater to their customers.
Marketplaces like Alibaba.com provide vast information about current trends in various industries. So don’t hesitate to use these resources and stock your store or workplace with the necessary tools.