Hay balers are a vital part of many farms for their ability to ensure that hay can be efficiently handled, transported, and stored.
However, shopping for new hay balers or upgrading to one that matches one’s business expectations can be a challenge, and the many options in the market don’t make the choice easier.
This article will highlight the essential factors to consider when selecting a baler, as well as the types of hay balers, in order to help business owners find the perfect machine for their needs.
Table of Contents
Market overview for hay balers
Types of hay balers
Factors to consider when choosing a hay baler
The bottom line
FAQs about hay balers
Market overview for hay balers
Data from Impactful insights shows that the global hay baler market size is expected to grow at a compound annual growth rate (CAGR) of 8.5%, signifying an increase from US$ 4.3 billion in 2022 to US$ 7 billion in 2028.
Key drivers for the growth of baler market include:
- Increase in the global meat consumption that fuels livestock farming.
- Ease of financing, government subsidies, and rising income levels which makes baler machines affordable.
- The growing need for efficient and time-saving agricultural practices.
- The adoption of modern farming techniques, such as precision farming and smart agriculture.
Types of hay balers
There’s no one-size-fits-all solution when it comes to hay balers. Different farms have different needs, hence the need to understand the various types of balers. machines.
Mini round balers
Mini-round balers are compact haying machines for small-scale operations or limited storage spaces.
They are the smaller versions of traditional round balers. With a narrower pickup width, they produce smaller bales, typically weighing around 50-150 pounds. Farmers with smaller fields find them ideal.
Pros
- They can navigate tight spaces, making them ideal for small or irregularly shaped fields.
- The smaller bales by mini round balers are easier to handle, stack, and store.
- They have a lower upfront cost, thus accessible for farmers with limited budgets.
- They are versatile, handling various forage, including hay, straw, and silage.
Cons
- Lower production capacity, thus taking more time and effort to bale a significant quantity of hay.
- Since they are small, mini-round balers require more manual labor for loading and unloading bales.
Large square balers
Large square balers produce rectangular bales of hay. They compress the harvested forage material into dense, uniform shapes and secure them with twine or wire.
They are ideal for high-volume hay production in commercial farming operations.
They also have a pickup system that collects the forage and feeds it into the baler chamber, where hay is then compacted and discharged as a finished bale.
Pros
- Unlike the mini-round bale, large square balers have high production capacity for medium to large-scale operations.
- The rectangular shape of square bales allows for more efficient stacking and transportation, thus reducing handling costs.
- They have automated features, such as knotting or tying systems, that reduce manual labor.
Cons
- They require powerful tractors to tow and operate them.
- Higher upfront costs due to their advanced features and production capacities
- Increased maintenance for optimal performance.
Small square balers
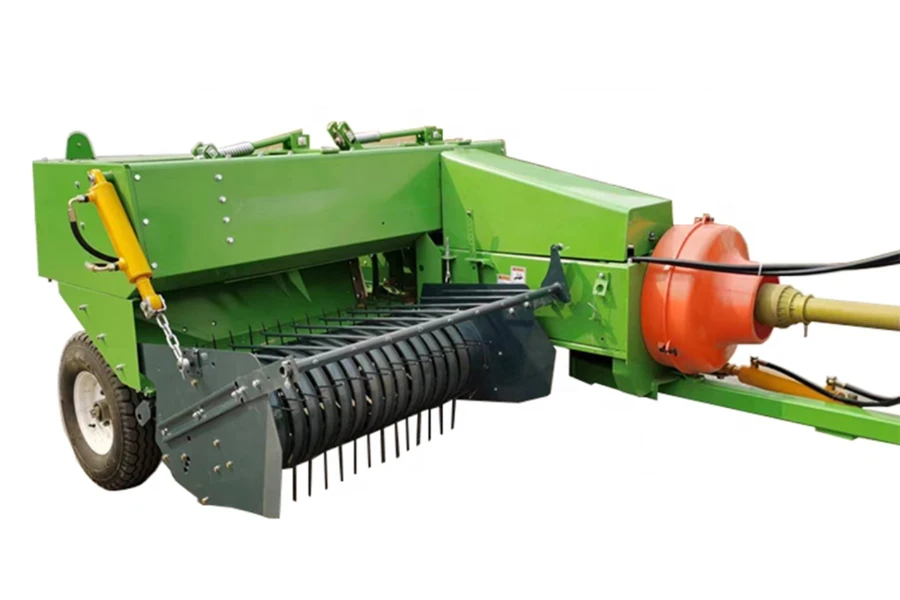
Small square balers offer a sweet spot solution between mini-round and large square balers.
Like their larger partners, they produce rectangular bales but smaller ones. They have a pickup system that collects and feeds the forage into the chamber and compresses it into dense bales.
They are suitable for medium-sized farms or small bale operations.
Pros
- They balance large square balers’ higher production capacities and mini round balers’ lower capacity.
- They are more maneuverable and easily navigate smaller fields or tight spaces.
- The rectangular shape of the bales allows for efficient stacking and transportation.
- Small square baler series allow for easy bale-density control since you can adjust the tension applied to the bale chamber.
Cons
- Small square balers may require more manual labor for loading and unloading bales than larger ones.
- They require regular maintenance for optimal performance.
- They have limited bale dimensions, which may be unsuitable for specific markets.
Factors to consider when choosing a hay baler
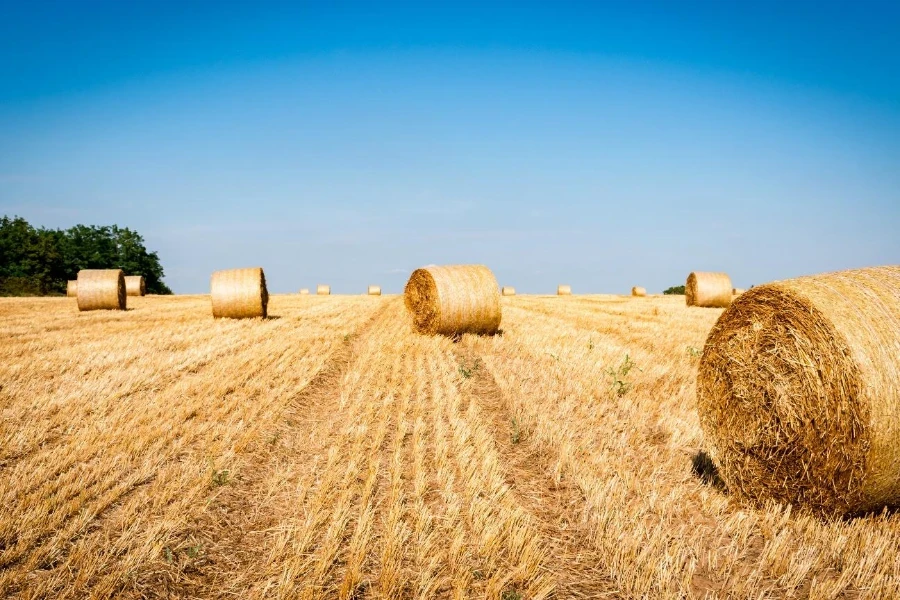
The following key factors will help you make an informed decision when choosing the right baler equipment for a range of needs:
Farm size and hay production volume
It is important to ensure the baler has the capacity and capabilities to handle your farm’s specific requirements. To do so one can evaluate the following:
- The annual hay production volume in acres or tonnage.
- The number of bales a farmer needs to produce to meet their forage needs.
- The time frame you want to complete the baling process.
- Whether the baler can handle different types of forage (e.g., hay, straw, or silage).
For example, suppose your farm has a high hay production volume and a tight timeline. In that case, you will require a higher capacity baler like the hydraulic compactor machine to handle the workload.
John Douglas of Wray House Farm prefers a large square baler to meet the farm’s needs. He has about 1,200 acres to farm and over 2,000 cattle to feed annually. Besides its production volume, John says he settled for the bailer because it’s easy to set up and service.
On the other hand, if your business runs a small-scale farm with limited hay production, a mini round baler or small hay baler machine will be sufficient.
Field conditions and terrain
Different balers perform differently in certain types of terrain or field conditions. Therefore, it’s crucial to select a hay baler that can handle the specific challenges of your land.
Consider the following:
- Whether your farm has flat, hilly, or uneven terrain.
- Whether the field has obstacles such as rocks, ditches, or rough surfaces.
- The soil moisture levels and the potential impact on baling operations.
For instance, if you have hilly fields with numerous obstacles, a mini-round baler with excellent maneuverability, adjustable pickup height, and ground clearance would be ideal.
And for farms with wet field conditions, a baler with superior moisture management features, like bale chamber sealing or integrated hay moisture sensors, can help maintain bale integrity.
Bale size and density requirements
Bale size and density are important because they impact storage, transportation, and feeding efficiency. These factors are precious for a farmer selling hay to end users.
Here are what determines your bale size and density needs:
- Specific end-users’ (livestock feeders or hay buyers) requirements.
- Your storage capacity and farm limitations.
- Ease of bale handling and transportation.
You’ll need mini round or small square balers if you have limited storage space or the market demands smaller bales. However, large hay balers would suit your business if the market requires denser bales.
For instance, the vertical hydraulic Holland Square Baler has a hydraulic bale density control system. This feature allows farmers to adjust bale density according to the desired weight and crop variations.
Budget and cost factors
Cost-effectiveness and budget considerations are vital in any purchase decision, and hay balers are no exception. As a farmer and a business owner, it’s essential to evaluate the baler’s upfront cost, operational expenses, and long-term value.
It is therefore important to compare the prices of different baler models, and to evaluate whether purchasing a new or used baler would be more cost-effective.
Other costs to consider include:
- Attachments
- Maintenance equipment
- Spare parts.
- Operational expenses
Besides costs, it’s crucial also to consider the baler’s long-term value, including its durability, expected lifespan, and reliability.
For instance, while a new hay baler may have a higher initial cost, it has a higher long-term value. It comes with warranty coverage and potentially lower maintenance requirements.
On the other hand, purchasing a used baler at a lower price may require more frequent maintenance and higher repair costs.
The bottom line
It’s no secret that choosing the right hay baler equipment for your farm or business can be challenging. The options are extensive, and one can make a less than ideal choice if one isn’t careful.
With this in mind, one should remember to:
- Choose a baler that aligns with your needs and goals.
- Assess your farm’s size, production volume, field conditions, bale requirements, and budget.
- Read customer reviews and conduct in-depth research on your preferred bailer.
This way, you’ll choose a hay baler that fits your farm or business goals, and ensure an efficient and cost effective solution to your baling needs.
FAQs about hay balers
What do you look for when buying a used baler?
When buying a used baler, inspect its overall condition, such as:
- The body
- Mechanical components
- Maintenance history
- Signs of wear, rust, or damage
- Previous usage
- Check if all the necessary parts are available and functioning correctly.
What equipment is needed for baling hay?
Haying equipment includes:
- A hay baler (round baler or square baler)
- A tractor to power the baler
- Appropriate attachments for the baler (twine or wire for securing the bales)
- A hay rake for gathering the hay
- A hay tedder for drying the hay
- A bale accumulator for efficient bale handling.
What is the difference between a square hay baler and a round baler?
A square hay baler creates rectangular-shaped bales, while a round baler forms cylindrical-shaped bales.
Square balers are ideal for higher bale density and efficient stacking, transportation, and storage. In contrast, round balers are famous for their simplicity, ease of use, and versatility.
What are some advantages of a large round baler over a conventional square baler?
- Large round balers are more efficient for high-volume hay production due to their faster baling speed.
- They are easier to handle and transport, especially in large-scale operations.
- They can handle wetter forage more effectively than square balers.
- And since they have fewer moving parts, they require less maintenance.
What makes a good hay bale?
- A good hay bale should have a consistent density for uniformity and stability.
- It should be tightly packed to prevent spoilage and maintain nutritional value.
- It should have consistent shape and dimensions for efficient stacking and transportation.
- A good hay bale should be free from mold, excessive dust, and contaminants to ensure high-quality feed for livestock.
What is the difference between vertical and horizontal balers?
Vertical and horizontal balers have different baler chamber orientations during the baling process.
Vertical balers compress materials from top to bottom, resulting in vertical bales. They are often used for recyclable materials like cardboard or plastics.
In contrast, horizontal balers compress materials horizontally, producing larger bales suitable for heavy-duty materials like metals or paper.