Packaging machines run for long hours and risk premature breakdowns. However, such breakdowns can be avoided with regular maintenance of the packaging machines. That way, the machines can have a longer lifespan.
Therefore, this guide will provide tips for maintaining packaging machines to ensure an easy time working with the machines.
Table of Contents
Six amazing ways to maintain packaging machines
Final takeaway
Six amazing ways to maintain packaging machines
Clean the machines
Making sure that packaging machines are clean is the first crucial thing to do as a maintenance measure. Like cars and houses, frequent cleaning of machines is equally crucial for their longevity. After all, the packaging machine collects dust from the packaged products and the surrounding.
Dust may accumulate in the crucial parts of the machine, such as the electrical and mechanical elements—leading to an unpredicted failure. No doubt, ordering and replacing new parts can be cost-effective. Plus, it could cost the operators a ton of valuable time.
Thus, cleaning all packaging machines thoroughly, inside and outside, using the right cleaning products, will remove clogged dust in key areas of the machine. Machine operators should therefore learn how to clean the packaging equipment correctly.
When cleaning the packaging machines, the operators should have protective gear like hand gloves, eyeglasses, and masks. The specks of dust and chemicals in the products harm health.
Lubricate moving parts correctly
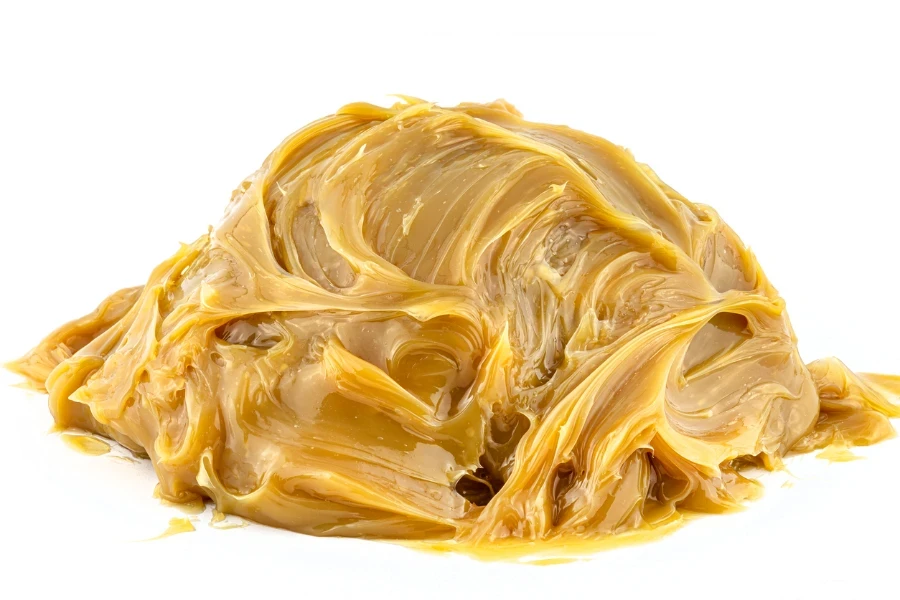
Packaging machine comprises various moving parts that require oiling. So, the operators must ensure that the moving gears, belts, and pulleys have the right lubricants. They can find details of what lubricants to use in the manual.
Remember that the manufacturer’s warranty does not cover problems arising from friction; therefore, lubricating packaging machines avoid such issues.
Inspect the machines
Inspecting the machines on a regular basis is an essential tip for ensuring a prolonged lifespan. The packaging machine will perform as effectively and accurately as a brand-new one when operators carry out routine inspections to identify glitches. The best inspection time is hours before normal operations begin in the plant.
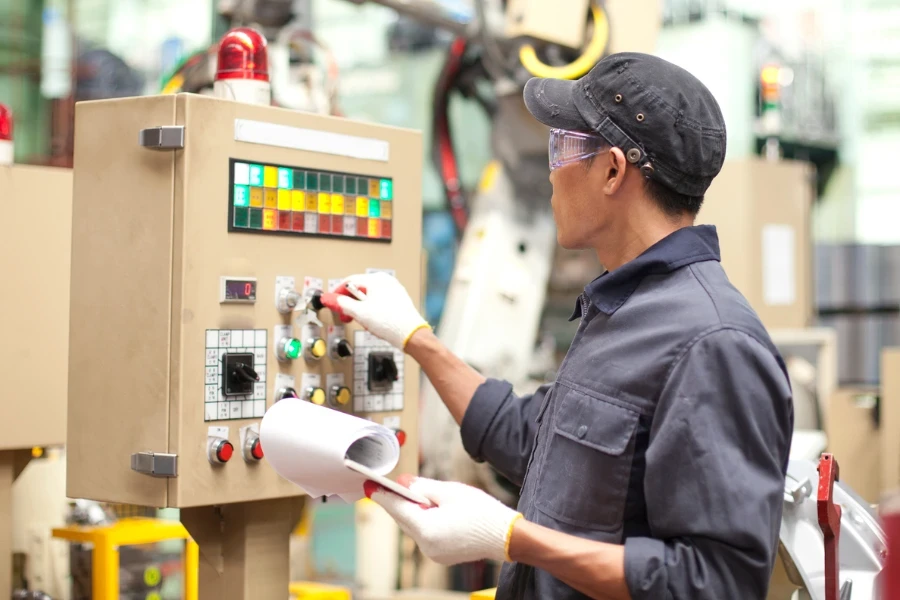
While inspecting, operators can have an inspection sheet with a checkbox of all the machines and parts running in the packaging line while identifying the issues.
Beyond manual inspections, computerized inspections can be more helpful. A program with diagnostic features can be installed to provide alerts if issues are detected in the packaging machine. Of course, a mixture of the two preventive routine maintenance procedures ensures less downtime in the machine.
If there’s an issue, an expert can correct it before it persists and damage the entire packaging machinery.
Early identification of the problem saves time and repair costs. Compared to finding out an anomaly late as the machines are running, the repair bill can be high and time-consuming, which is a financial setback for business.
Change parts regularly
Wear and tear is a normal occurrence in packaging machines used often. To maximize the performance output of the machines, users must be familiar with the parts that require regular replacement.
Qualified service technicians should only perform the parts change. Otherwise, things can go wrong that may even cause more damage to the whole system—if an untrained personnel handles replacement of parts.
The parts of the packaging machines classify as follows:
- High-wear parts have a short lifespan.
- Medium-wear parts – have a longer life. They may or may not ever break down.
- Low-wear parts – these are parts that should never fail.
When changing these parts, some may collide with others needing an upgrade. So, it is crucial to communicate with the equipment provider to recommend the number of times to change what part. Overall, this ensures longevity in the packaging process for the business.
Plan for machine upgrades and discontinuance
Over time, machines wear out requiring constant replacement and with the advent of technology, new features arise, making the packaging process simple and less time-consuming.
When packaging machines become worn out and old, finding the parts becomes challenging because the manufacturers have discontinued the components for the older version. In such cases, upgrading the machine will the best bet.
However, upgrading the machine is expensive, so buying a new one can be the better alternative. Nevertheless, it’s key to weigh the available options before upgrading.
Better still, seek advice from experts or manufacturers of packaging machines to get the right information to pick the best choice.
Partner with the OEM manufacturer
A faulty packaging machine results in lost production and income. So, vetting the legitimacy of the packaging machine manufacturer before acquiring a packaging machine is essential. Find out if they offer after-sales services and original spare parts.
Buying a packaging machine from a trustworthy manufacturer offering remote customer support, like troubleshooting problems without visiting the location, is a significant investment. Most times, such visits are expensive and can waste valuable time when the diagnosis can be done offsite.
Crucial details operators should have from a dependable packaging machine provider are the company’s president’s or managing directors’ contact details. If these details are available at any time when there is an issue, the consumer can contact them.
Final takeaway
A simple procedure like ensuring the machines are clean and well-lubricated prevents unnecessary breakdowns that can lead to hefty repair bills. So, always use the recommended cleaning supplies as advised by the manufacturer.
For more information about the latest packaging machine models, visit Alibaba.com.