As the manufacturing sector expands, hot rolling mills are needed in different factories to roll hot metals for different purposes.
Hot metal rolling is a process in which a metal is heated beyond recrystallization temperature to deform plastically. The deformation allows the metal to be shaped in desired shapes and dimensions.
There are various hot rolling mills utilized in different industries. This guide will help businesses select the right hot rolling mills for their customers’ needs.
Table of Contents
Hot rolling mill market overview
Types of hot rolling mills
How to select a hot rolling mill
Conclusion
Hot rolling mill market overview
The global rolling mill market is forecasted to grow at a compound annual growth rate (CAGR) of 3.7% in the next seven years.
Rolling mill market growth is driven by the increasing demand for steel products in the energy, automotive, and construction sectors.
The rolling mill market is segmented into the process, machine type, end-use, and application. In end use, the market is classified into general manufacturing, defense, energy, construction, automotive, and transportation.
North America is the largest hot rolling mill market due to the high concentration of steel manufacturing plants. India and China are also experiencing increased demand for metal rolling mills.
Types of hot rolling mills
Two-high rolling mills
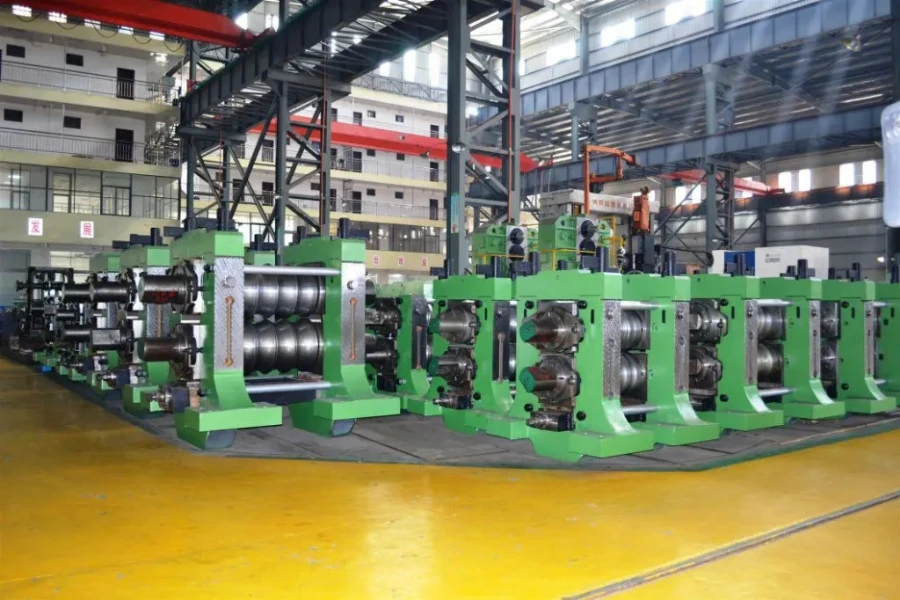
This is the simplest type of hot rolling mill. It consists of two rollers that rotate in opposite directions.
The material to be rolled is fed between the rollers, which apply pressure to deform and shape the material. The direction of the rotation of rolls cannot be readjusted or altered; hence the work has to be fed into rolls from the direction only.
Three-high rolling mills
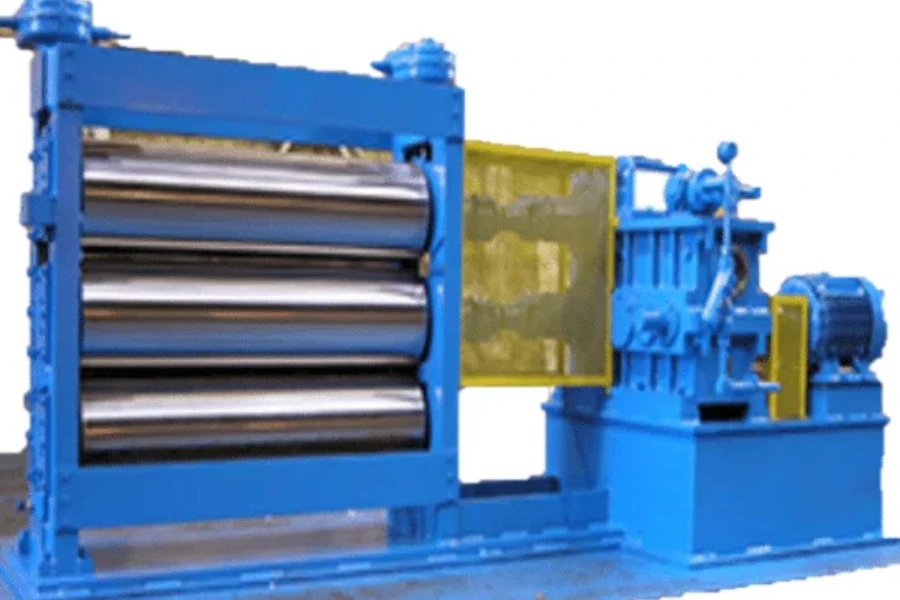
A three-high rolling mill has three rollers, with one roller located above the other two.
The material is fed between the top roller and the two lower rollers, which apply pressure to shape and deform the material.
The main advantage of the three high roller mills is that work material can be fed in one direction between the first and second rolls.
Four-high rolling mills
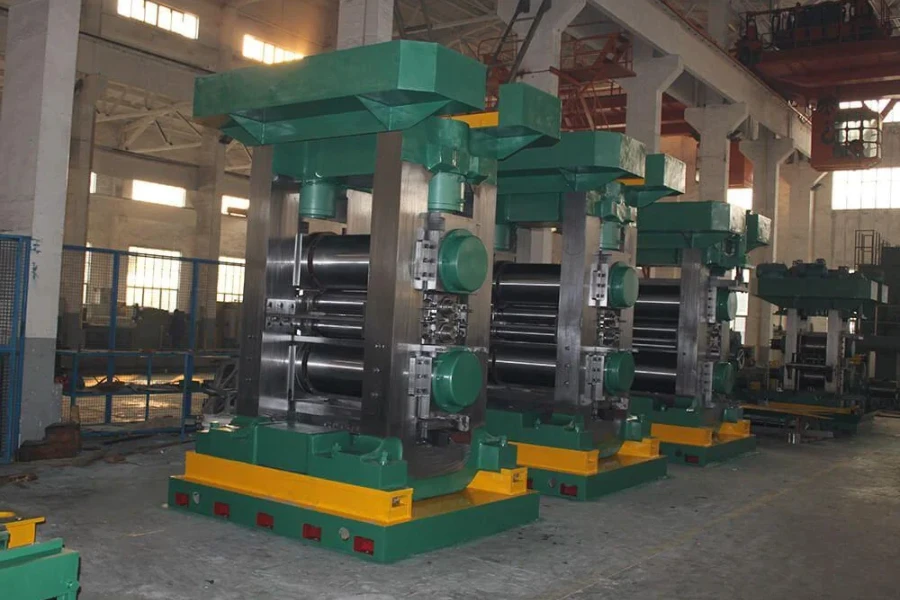
Four-high rolling mills are a type of rolling mill that uses four rolls to reduce the thickness of a metal strip or sheet.
The rolls in a four-high rolling mill are arranged in a two-over-two pattern, with each pair operating in opposite directions.
The top and bottom rolls in a four-high rolling mill are larger than the two intermediate rolls positioned between them. The larger size of the top and bottom rolls allows greater pressure to be applied to the workpiece, resulting in a more significant reduction in thickness.
Cluster rolling mills
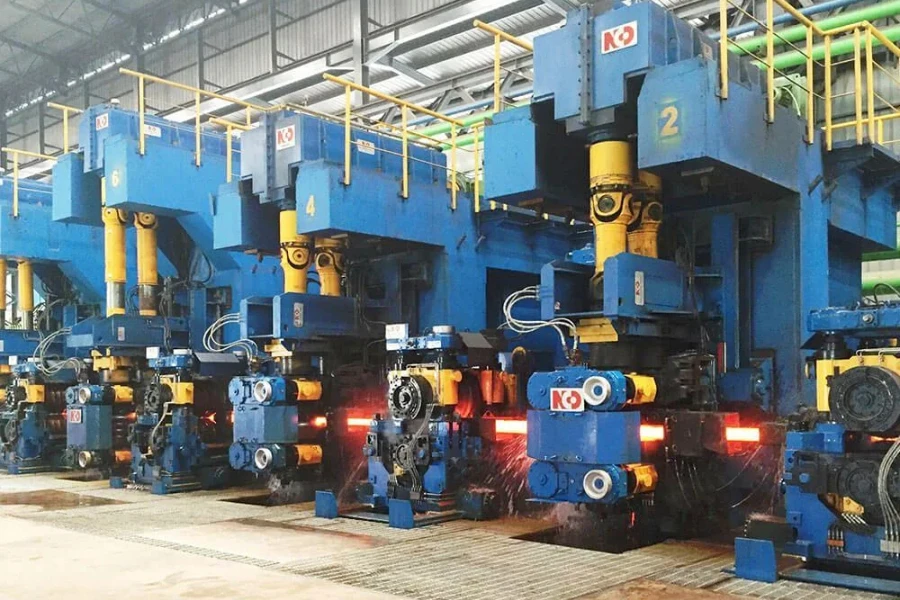
Cluster rolling mills have several pairs of rolls arranged in a cluster, each pair of rolls operating in tandem.
The rolls in a cluster rolling mill are arranged in a specific pattern, typically in a diamond shape or a cluster of four or more rolls. The workpiece passes through the center of the cluster and is subjected to multiple reductions in thickness as it passes through each set of rolls.
This design allows for greater flexibility and a more comprehensive range of product sizes. Cluster rolling mills produce high-quality, high-precision products like automotive parts, bearings, and aerospace components.
Tandem rolling mills
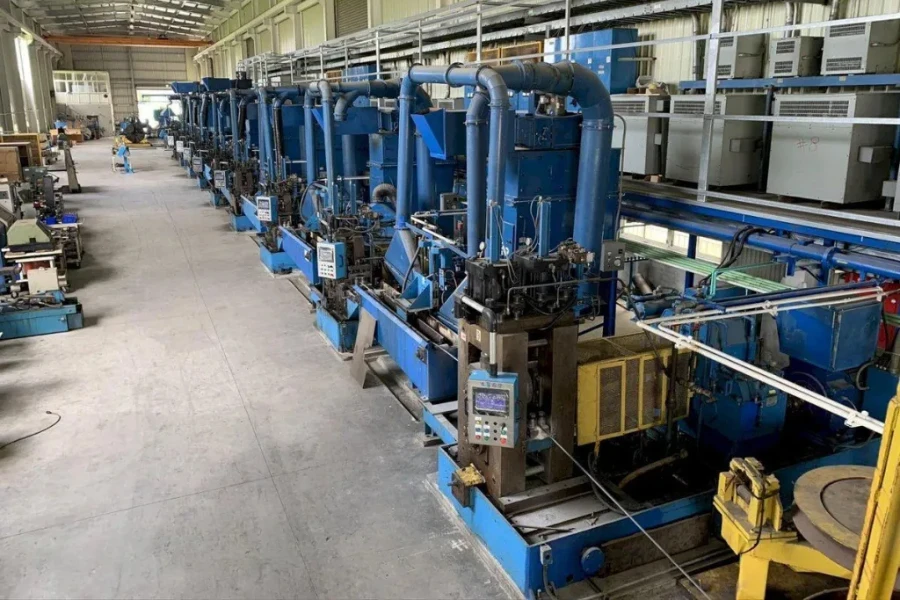
Several stands of rolling mills are arranged in a series in a tandem rolling mill, each performing a specific function.
The material passes through each stand in turn, with each stand contributing to the final shape and size of the product.
Tandem rolling mills can achieve a higher reduction in thickness than single-stand mills and can also be used to produce a wider range of products.
A Steckel mill
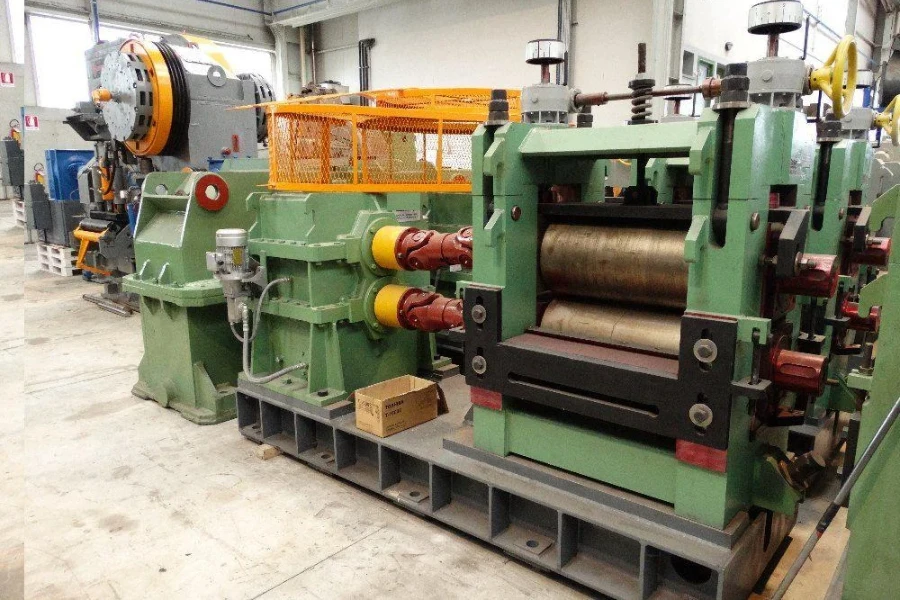
A Steckel mill is a rolling mill used to produce high-quality hot-rolled steel coils. It is named after its inventor, Edward Steckel, who patented the design in 1923.
The Steckel mill combines a reversible rolling mill and a continuous caster. In a traditional rolling mill, a steel slab is rolled repeatedly to reduce its thickness and shape it into a coil or sheet. However, in a Steckel mill, the steel is cast directly into a hot strip, then rolled through a series of rolling stands to achieve the desired thickness and shape.
One of the primary advantages of a Steckel mill is its ability to produce high-quality, low-cost steel products with a wide range of thicknesses and widths.
How to select a hot rolling mill
Selecting a hot rolling mill requires careful consideration of several factors, including the type and size of the material to be rolled, the desired product specifications, and the production volume.
Here are some key factors to consider when selecting a hot rolling mill:
Material type and size
Consider the characteristics of the material to be rolled, such as its composition, thickness, and width. Some mills may be better suited for specific materials or product sizes than others.
Product specifications
Determine the desired specifications for the final product, such as thickness, width, surface finish, and mechanical properties. Choose a mill that can meet these specifications with high accuracy and consistency.
Production volume
Consider the required production volume, as some mills are better suited for high-volume production than others. Additionally, consider the efficiency and throughput of the mill, as well as its maintenance and downtime requirements.
Every customer’s production needs differ, and the selected hot rolling mills’ production capacity should match these needs.
Cost and budget
Determine the budget for the mill, and compare the cost of different options to find the best value for the investment. The average price of a hot rolling mill starts from US$ 60,000.
It is a considerable investment, but the returns are likely to be worth the price. It is therefore important to select a hot rolling mill that meets your customer’s expected budget.
Technical expertise and support
Finally, it is important to consider the technical expertise and support level of the mill manufacturer or supplier. Look for a supplier with a strong track record of quality and reliability and one that can provide training, technical support, and spare parts as needed.
After-sales support is crucial to ensuring your customer has access to the required technical expertise to ensure business continuity.
Conclusion
Hot rolling mills are essential in many industries due to the increased use of steel in manufacturing, construction, oil industry, and defense. The industry forecast looks bright and the demand will continue to increase as regions across the globe continue to expand their manufacturing and industrialization.
Businesses in the machinery sector should consider stocking and marketing hot rolling mills to capitalize on the increased demand. Visit Alibaba.com for listings of high quality hot rolling mills.