Flexographic printing is one of the most used print technologies all over the world. The reason for this method in the label printing industry is the range of benefits it comes with such as productivity, quality, and flexibility. Before buying flexographic printers, it is worth noting there are different models available in the market and they have different capabilities.
In this article, we will focus on how to select suitable flexographic printers and how flexographic printers work. We will also talk about the market share, demand, size, and expected growth rate of the flexographic printing market.
Table of Contents
Overview of the flexographic printing market
How flexographic printing works
How to select suitable flexographic printers
Conclusion
Overview of the flexographic printing market
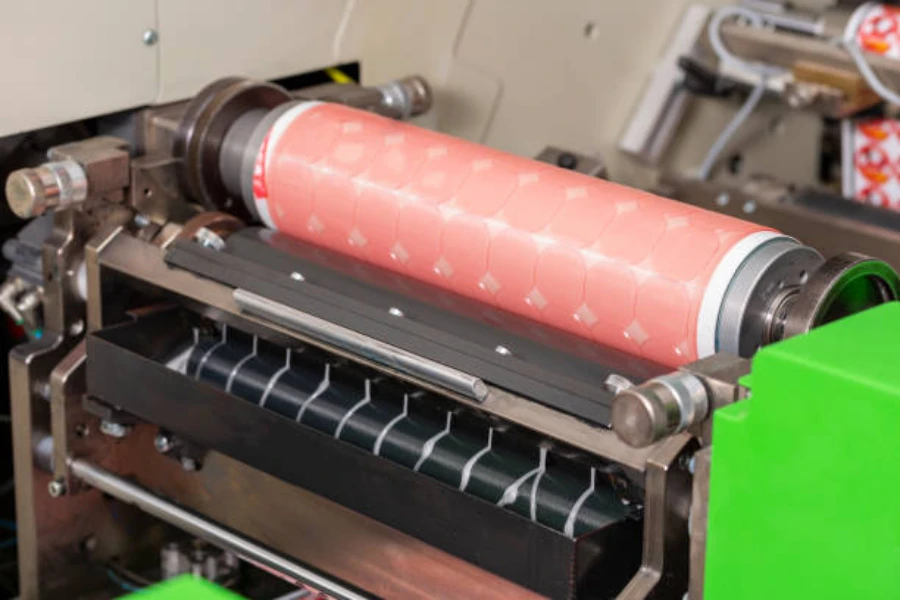
Generally, the global print market is changing steadily due to the shifts in retailer, client, and consumer demands. The flexographic print technology has been mainly driven by lower run lengths and increased demand for more variations. This growth is aimed at improving efficiency in the international digitized market.
In 2020, the flexographic market was estimated to be US $107.42 billion. It was further anticipated to expand at a compound annual growth rate (CAGR) of 2.44% to reach US $124.61 billion by 2026. This growth was ascribed to increased applications of flexographic printing due to the ability to print on non-porous substrates.
The dominant segment in the overall market share was the packaging industry. This industry included food packaging, packaging for drugs, boxes used in storage and shipping companies, and labels on the packages.
Regionally, the United Kingdom registered the largest market share at 39%. It was majorly contributed by the print media and packaging industries. Other regions with major markets for flexographic printers included North America, Asia-Pacific, Latin America, the Middle East, and Africa.
How flexographic printing works
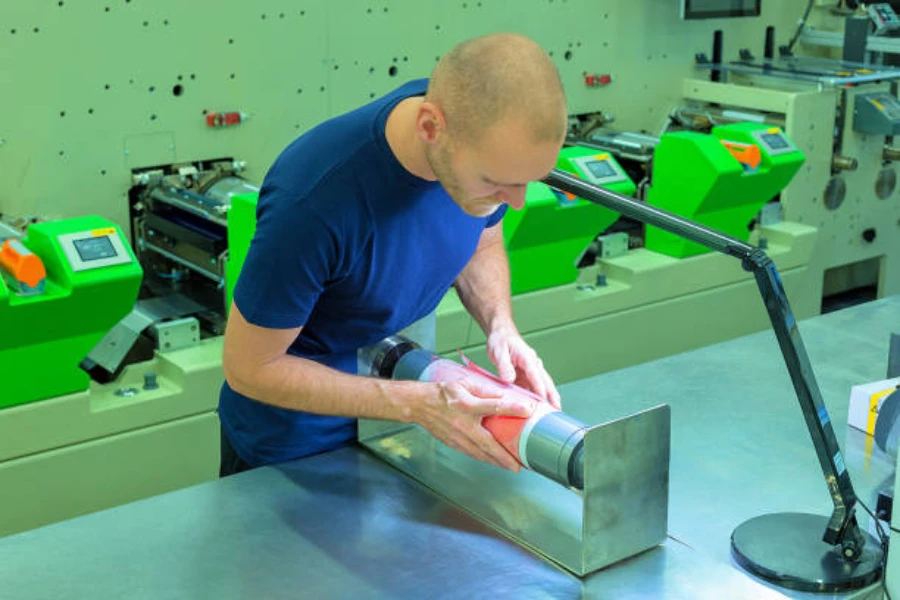
There are various types of flexographic printers. The machines share a conventional printing process. In this case, if several buyers acquire different flexographic machines, they will be able to operate them without difficulties. Below are the key parts of the printing process:
The process begins with platemaking where the printing plate contains the text and images to be printed in negative that appear as a mirror image. There are separate plates for each color mounted correctly and used in the print run to ensure images are accurately transferred to the substrate. The three methods used in this step include metallic plate etching, digital etching, and photo etching.
The printing process has the printing plate loaded into the printing press on the plate cylinders. When the run begins, ink is transferred from the ink tank to a ceramic roller or an anilox through a fountain or metering roller.
The anilox is cleared of excess ink using a scraping tool to avoid patchiness or ink flooding. This results in a positive print image from the negative print plate. Afterward, the ink has to dry as quickly as possible when the printed image has been transferred to the substrate. The drying process is effected by fan-powered infrared dryers, or LED or ultraviolet curing based on the ink type used.
How to select suitable flexographic printers
1. Cost
Flexographic machines are quite complex and large in size, usually ranging from 18 to 30 inches. When acquiring this printing machine, buyers should pay for its quality. Limited features on a machine mean it is of low quality and could be less costly. However, these kinds of purchases may end up being more costly in the long run due to functionality problems, voided guarantees, and additional repair and replacement costs.
Another factor to be taken into account is the precise mounting of print cylinders. Any slight inefficiencies in the printing process and defective features will adversely affect the quality of print runs. This could lead to increased wastage, inaccurate printouts, and reduced quality, hence reduced return on investment. Also, more color options, wider print labels, and using advanced print drive systems make the flexo machine more expensive.
2. Quality
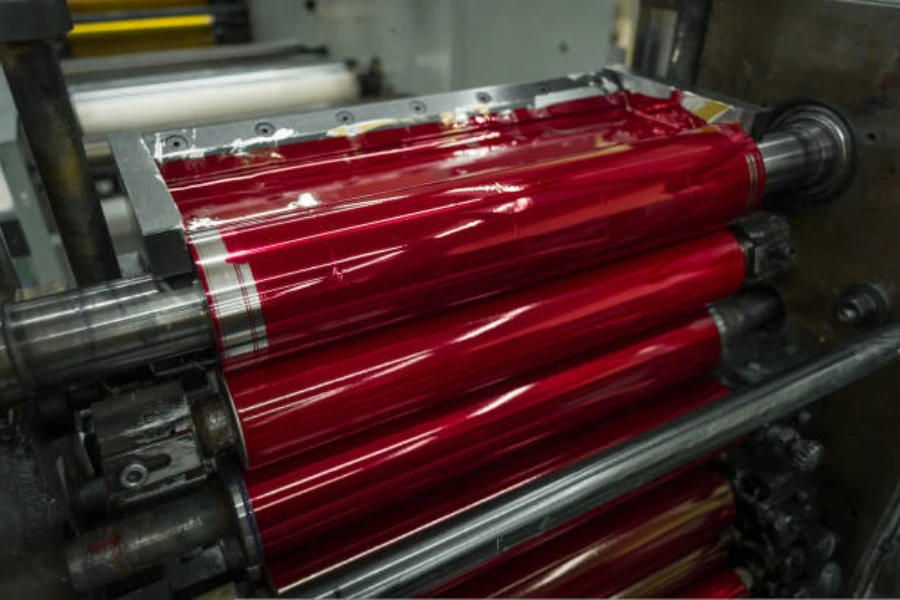
This is one of the most important factors when getting a piece of machinery. It begins with researching and purchasing a quality flexo printer from a well-known and reliable manufacturer. This goes from guaranteeing high performance by their equipment to dynamic and resourceful after-sales services that enhance buyer satisfaction.
Quality can also be shown by the surplus features on the machine like rapid printing, advanced automation, and efficient drive systems. The features add value to production and directly improve the efficiency of the workflow.
3. Operation
Buyers need to thoroughly study and understand the production process. This will be helpful in the event of deciding the kind of flexo machine to be acquired. The current staff should be trained on how to use the machine. This will minimize the room for errors and downtime. Flexographic printers are generally large in size; thus buyers should put into consideration the size of the facility to house the machine they intend to buy.
Also, concerning operation, the equipment should be able to promote the planned production process so that the buyers will not need to regulate work around it. Various types of flexographic equipment are dried by high-pressured air, ultraviolet curing, or infrared systems. Others use LEDs to feed the ink to the substrate. Notably, the machines that use LEDs require lower energy to run as compared to those that use fan-powered systems.
4. Functionality
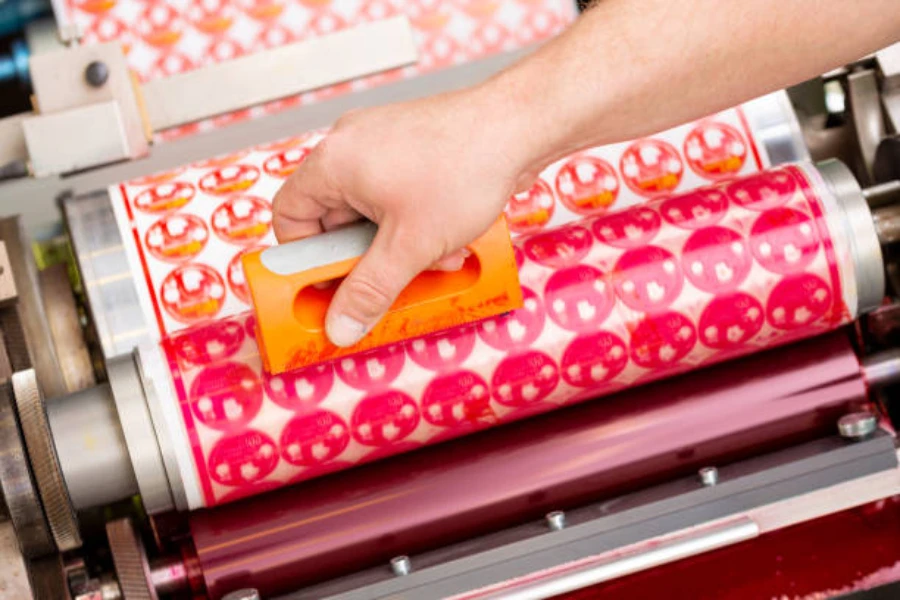
Flexo printing equipment comes with supplementary specialties meant to improve functionality. Several factors could be taken into account depending on production requirements. For instance, a machine with an extra drying system, a conveyor system, a web cleaner, and an automated inking system.
The specialties should be able to handle the current and future printing tasks. This will eliminate the need to acquire another machine or need for additional features in a few years of use; thus saving money and time. Modern printing has rather sophisticated and high levels of automation, and this has cut back on manpower requirements and made production lines more efficient.
5. Productivity
The combination of a flexographic machine and other external equipment improves its functionality and performance. For instance, elastomer sleeves increase productivity by reducing waste and fixing time. They are a simple printing solution that is sustainable, long-lasting, and adjustable compared to other materials.
Buyers should also consider adding pre-print solutions to aid in reducing wastage and lead time. On average, a modern flexo printer can print at a 400m-per-minute rate. As a result, they are extremely cost-effective and efficient compared to other printing methods like lithographic presses.
6. Applicability
Flexographic printing is a form of rotary printing where ink is applied to surfaces by use of flexible rubber or printing plates. It has been widely used as an economical and quick way of making simple designs and applying color to various packaging materials like plastic and paper containers.
Buyers should check out printers that have special effects and can achieve brilliant colors. The printers should be used with fluid or solid inks available. It is worth noting that flexographic printers can also be used in newspaper printing presses. This is because they offer ease of ink distribution and simplicity.
7. Operating size
The flexographic printing method is a typical example of convex printing done on plastic, paper, and cardboard. Buyers should consider the dot per inch (dpi) of a printer, which is the measure of the printed image quality on the material. The minimum dpi for a standard flexographic printer is 3% file dot. A plate cannot hold an image element smaller than 3%.
This technique also requires low-viscosity printing inks with a pascal second range lower than 0.05 to 0.5. UV flexographic inks have a higher viscosity of about 0.1–0.25 Pa.s. On average the flow time of flexographic printing ink equals 18–35 seconds through an outlet diameter of approximately 4 mm.
Conclusion
Acquiring a flexographic printing machine is like purchasing any other industrial machinery. Buyers will need a proper balance of functionality, safety, and other features while striving to remain within their budget.
A flexographic printer is a major investment. It requires the buyers to understand its compatibility with other flexo printing devices and overall performance.
The above guide outlines the vital factors that should be considered on the buyers’ paths in seeking to purchase the most suitable flexographic printer for their press operations. To find efficient flexo printing equipment, visit Alibaba.com.