Metalworking factories specialize in fabricating all kinds of metals. Several operations will always be performed on any metal workpiece, such as milling, lathing, and cutting. This guide focuses on understanding the machines suitable for those operations, how to choose them, and their application in a metalworking factory. Therefore, this guide is essential to any business that seeks to start a metalworking factory.
Table of Contents
Metalworking factory: market size and trends
Lathe machine
Metal cutting machine
Milling machine
Drilling machine
CNC machining center
Metalworking factory: market size and trends
The metal working factory market size is projected to reach $103.43 billion by 2027. Emerging trends in the industry include an inclination toward programmed production techniques, which helps manufacture dependable fabrication amenities by removing dangerous processes such as welding. The increased demand from other industries, such as the automotive industry, means that fabrication will experience immense growth in the coming years. Adoption of advanced technologies in metal fabrication is also expected to take center stage to enhance productivity and minimize wastage of resources.
Lathe machine
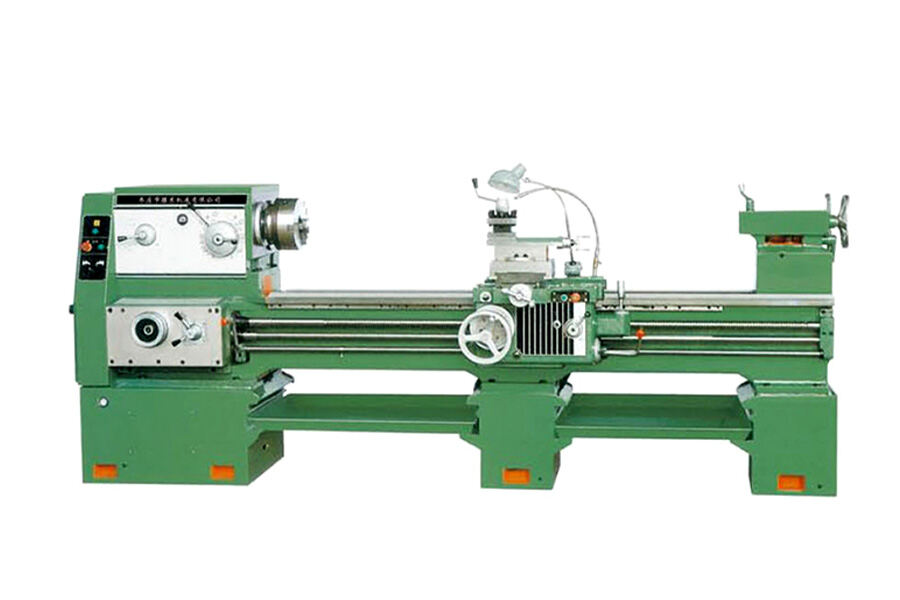
Application in a metalworking factory
The lathe machine is standard in metalworking workshops. It features a rotating center on which a metal workpiece is clamped. The lathe machine is helpful in shaping, drilling, chipping, knurling, turning, sanding, cutting, and deforming the metal workpiece to form the desired shape.
How to choose
Type
There are several types of lathe machines from which businesses can choose. They include speed lathe, bench lathe, engine lathe, automatic lathe, and CNC lathe machine.
Size and weight
Lathe machines are heavy, with their weight ranging from 700 to 1600 kg. Mini lathes weigh 15 kg, while hobby lathes will weigh around 50 kg. The size of a lathe is determined by the distance between the two centers, with most lathes falling between 36 to 48 inches. Smaller lathes will have 15 inches between their centers.
Cost
Lathe machines are not cheap due to the amount of work they accomplish. Even the most straightforward lathe machine will cost upwards of $5000, while more advanced lathes such as CNC lathe machines will cost up to $40,000. This guides businesses on which lathe machine to purchase based on their budget.
Geometric complexity
The traditional lathe machine is simple to use. It clamps the workpiece on the center and, using the tool, machines the workpiece. More advanced lathes such as the CNC lathe feature digital displays. Processes such as clamping and machining are all automated, increasing their complexity.
Accuracy required
The accuracy of machining is determined by the skill of the personnel when using a traditional lathe machine. However, a more advanced lathe such as a CNC machine will be accurate regardless of the operator since it’s automated. Therefore, businesses should consider the accuracy required when acquiring a lathe machine.
Metal cutting machine
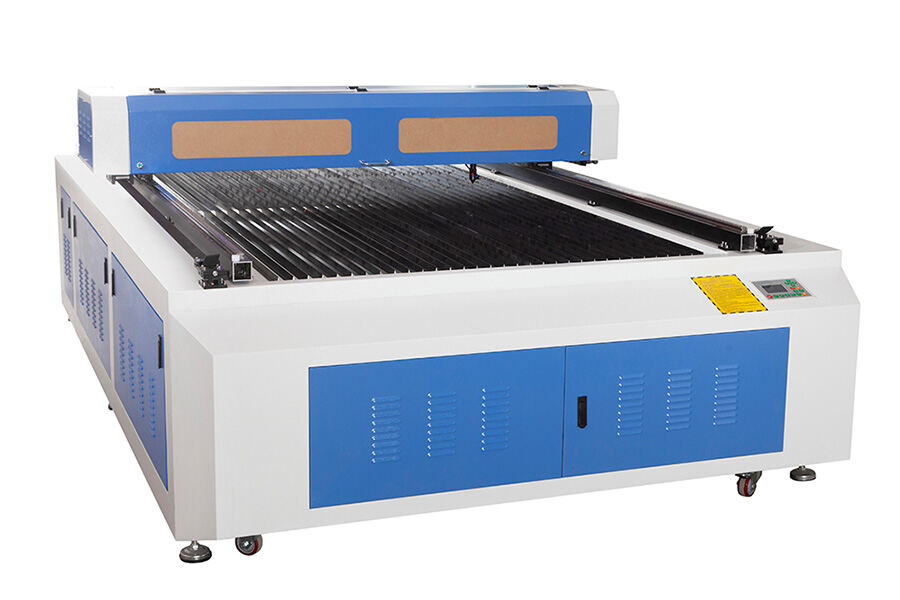
Application in a metalworking factory
Metal cutting machines have a wedge-shaped cutting tool. Depending on the number of cutting points, they can be classified as single, double, and multi-point. Their primary purposes are to cut metal, remove unwanted parts from metal pieces, and fabricate metal parts.
How to choose
Type of cutting technology
Cutting technologies to choose from are laser cutting, oxyacetylene cutting, and plasma cutting.
Capacity and power
Metal cutting machines provide various amounts of power. Some give 1kW, 2kW, 4kW, etc. Depending on the needs of a business, they should select a machine that suits their power needs.
Worksite
Metal cutting machines used in the workshop don’t need special arrangements for electricity as opposed to on-site machines, which may use other sources of energy besides electricity, such as gas.
Size of metal cutting tool
This is a hardened metal tool used to cut, shape, and remove material from a workpiece.
Milling machine

Application in a metalworking factory
A milling machine works by rotating a multi-toothed cutter fed into the workpiece. In a metalworking factory, it’s helpful in machining flat surfaces. It’s also used in drilling, boring, and cutting gears.
How to choose
Type
Bench milling machines are mounted on a bench. As such, they can be bolted to work on any surface. The table does not move vertically. Instead, the headstock is adjusted vertically. On the other hand, the knee mill allows the table to move vertically before milling.
Number of axes and orientation
There are milling machines with 3 and 4 axes of operation. 3-axes machines utilise the X,Y and Z dimensions. In 4-axes machines, the 4th axis is the rotation of one of the 3 axes. 4-axes and 5-axes machines are always CNC machines.
Type of milling machine, CNC, traditional.
Traditional milling machines use handwheels that are marked incrementally by millimeters. They can perform any operation but are limited by the skill of the operator and the time of the process.
Spindle speed
It refers to the speed of the milling machine and affects the tool size, cut depths, and feed rate.
Lubrication/cooling system
Newer milling machines incorporate a lubrication/cooling system. However, older versions of milling machines don’t have cooling systems and need to be cooled externally.
Drilling machine
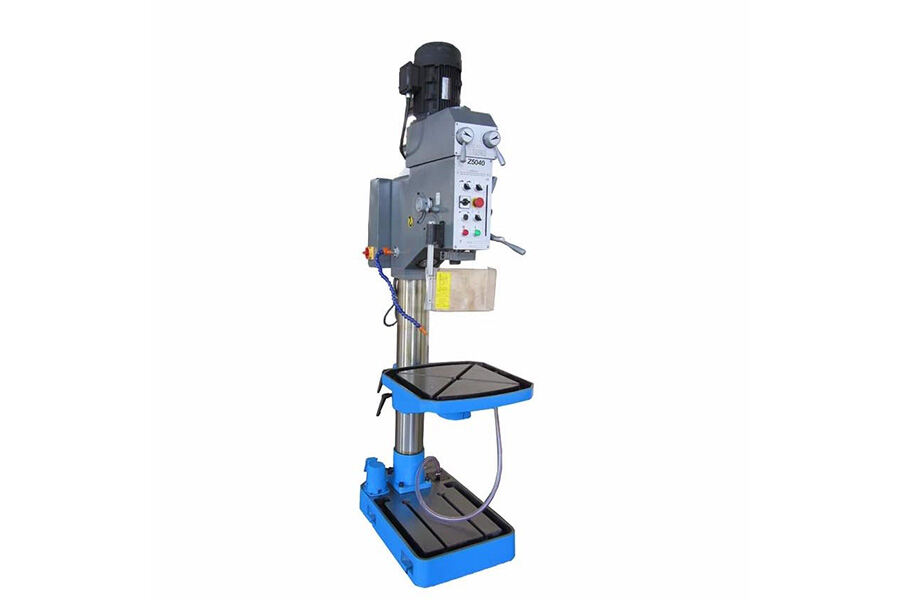
Application in a metalworking factory
Drilling machines are used to bore holes through materials such as metal, wood, and even concrete walls. They come in 2 modes, cordless drilling machines that don’t have an electric cord and cord drilling machines connected to a power supply source.
How to choose a drilling machine
Power
The drill’s power is an essential feature because it determines the amount of work the drill can manage. Whether the machine can drill through hard surfaces such as concrete will depend on the power. Materials such as wood will require around 450 watts. Hard surfaces such as concrete and metals require 1500 watts and above.
Diameter
Drills can drill holes of different diameters depending on the user’s needs. The drill diameter can vary by changing the drill bit. Bit sizes range from 104 to 12.70mm. Drill bit size 104 has a diameter of 0.0031” while size 12.70mm has a diameter of 0.5”.
Voltage
Voltage is necessary for cordless drills because they use batteries and don’t have an extension to a source of electricity. The battery ranges from 12V to 20V. In addition to this, using rechargeable lithium-ion batteries is advisable because the charging time is less than 60 minutes.
CNC machining center
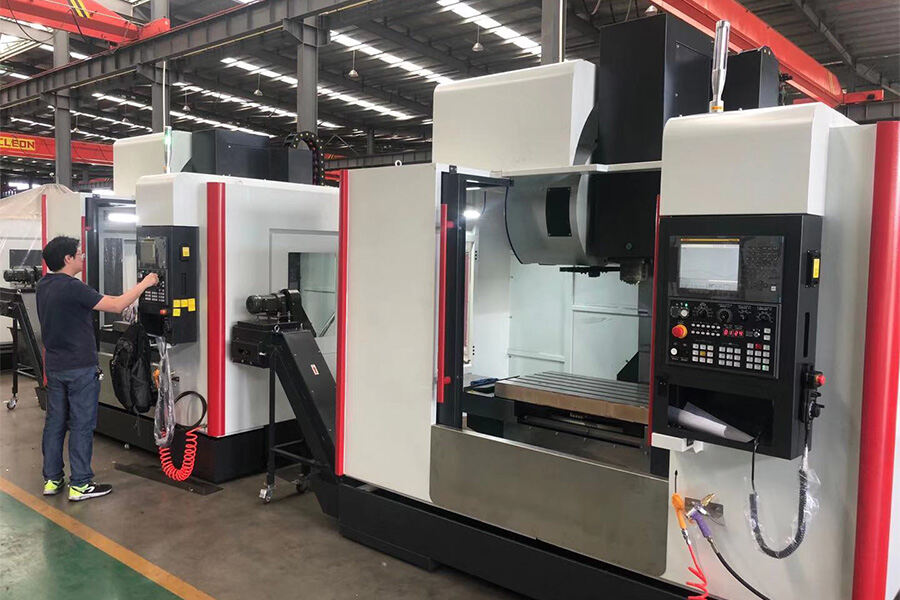
Application in a metalworking factory
The CNC machining center is a high technology machine used to develop prototypes of parts and products in the factory. It can provide drilling, milling, and lathe functions with high quality and high surface finish properties.
How to choose a CNC machining center
Experience of operator
Businesses should consider whether they have personnel with the necessary experience operating the machine. The CNC machining center is a fairly complex machine that will need experts to give good quality end products.
Materials to be machined
CNC machines can work on many materials such as aluminum, copper, hardened and mild steel, titanium, and Inconel. The type of material to be machined will determine the spindle, center, and design to be used, and the accuracy that can be achieved. The physical properties of the materials will also determine tool factors such as the maximum spindle speed and torque.
Cost
CNC machining centers are costly due to their advanced technology, and they imply fixed and variable costs. Fixed costs include initial capital investment and the machine’s depreciation, while variable costs are labor costs, maintenance, servicing, and materials used. A professional CNC router will cost up to $100,000, while a 5-axis machine will range between $200,000 and $500,000.
Space available
Due to their large size, businesses will need to consider the space available to place the CNC machining center.
Conclusion
Knowing how to choose equipment could determine the success or failure of a metalworking factory. This guide aimed at helping factories choose metalworking machines based on several factors such as size, cost, power, etc. Readers may now be better informed to buy suitable metalworking machines, whether they be lathe machines, metal cutting machines, milling machines, drilling machines, or CNC machining centers.