Table of Contents
– Introduction
– Myth #1: One size fits all – AMRs are suitable for every picking style
– Myth #2: Your WMS is the best tool for managing human-robot workflows
– Myth #3: AMR software can perfectly optimize human and robot coordination
– Myth #4: Robots alone can minimize worker travel
– Myth #5: Existing systems are sufficient for orchestrating human-robot work
– Conclusion
Introduction
As the robotics and automation trend continues to grow in warehouses, with the market expected to reach USD 23.09 billion by 2027 according to a recent study, it’s crucial for businesses to understand how to effectively integrate robots and human workers. However, there are several common misconceptions about coordinating and optimizing tasks between humans and robots in the warehouse.
Myth #1: One size fits all – AMRs are suitable for every picking style
One common misconception is that autonomous mobile robots (AMRs) can handle all picking styles equally well. However, the reality is that different AMRs specialize in different workflows. Some of these workflows include robots-to-goods, goods-to-person, follow-the-robot, transit robots, and full pallet moves.
To get the best blend of robotics in your distribution center, you may need different AMRs from various providers to satisfy every process. This can lead to integration complexities, as each AMR system may have its own unique requirements and interfaces.
The key to overcoming this challenge is utilizing an integration partner, such as smart software and mobile technologies, to orchestrate and optimize these processes. This software-based approach can help you get the most out of robots and reduce time and effort for human co-workers, often without requiring new automation systems or changes to warehouse layouts or storage systems.
Myth #2: Your WMS is the best tool for managing human-robot workflows
Another common belief is that your existing Warehouse Management System (WMS) is the best tool for managing workflows that involve both humans and robots. However, most WMS solutions follow basic logic and location sequence pick paths when allocating work, without considering batch and path optimization in the context of human-robot collaboration.
To truly optimize decision-making and task execution in a system involving humans and robots, it’s essential to implement an additional layer that synchronizes all three components under one controlling entity. WMS solutions often lack this capability, as they typically follow a fixed location sequence using a snake pick path around the facility, which is not always optimal.
Even if a WMS has some optimized paths, they are often hardcoded and inflexible. To achieve a truly dynamic approach, a solution that allows for intuitive real-time adjustments is required. This additional layer of optimization can help ensure that humans and robots are working together efficiently, minimizing wasted time and effort.
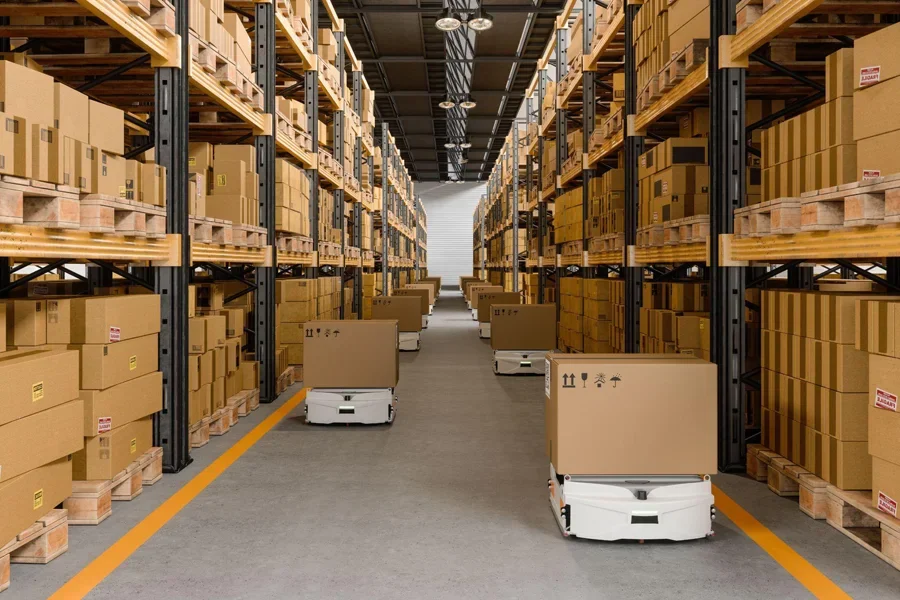
Myth #3: AMR software can perfectly optimize human and robot coordination
Many people believe that the software provided by AMR vendors is capable of perfectly optimizing the coordination between humans and robots. However, it’s important to understand that AMRs are designed to optimize robot performance, not necessarily human performance.
There are two common processes involving AMRs: follow-the-robot/cobot styles and zone picking. In cobot picking, a human follows the robot, often based on tasks allocated by the WMS. Zone picking keeps humans in a fixed zone, reducing human travel but requiring pickers to be allocated to the correct zones and ready for AMRs. Both approaches can be quite static and may not fully optimize human travel.
True optimization involves three key aspects: work prioritization, batch optimization, and finding the most efficient pick path. A best-case scenario system should consider these priorities on a just-in-time basis, increasing pick density and creating better batches. As new orders enter the system, they should be automatically slotted and prioritized appropriately. Warehouse leads and supervisors should have full control over changing priority for their orders, ensuring the system operates on-demand and always provides optimally prioritized work when a user requests it.
Myth #4: Robots alone can minimize worker travel
Another common misconception is that robots themselves can minimize worker travel in the warehouse. While zone picking can reduce human travel by keeping workers in a specific area, cobot picking is unlikely to achieve the same result.
In cobot picking, the human worker travels around the warehouse with the robot, following the same path. Although an optimized robot path can lead to a more efficient route for the human, the concept still involves the human and robot being tied together, which may not always be the most efficient approach.
Zone-based picking, on the other hand, can reduce human travel, but it’s a very rigid system. In this scenario, humans are assigned to specific zones and must be present when a robot arrives to pick and load items. If a worker needs to take a break or is not replaced, the entire solution can start to fall apart. Additionally, balancing the workforce in a zone-based system can be challenging, as picking demands may vary significantly from one day to another, leading to underutilized or overworked staff in certain zones.
To truly minimize worker travel, it’s essential to harmonize the travel of both robots and humans. This approach allows workers to dynamically travel to the most optimized pick location and meet the AMR there, reducing travel while maintaining flexibility. By incorporating a layer of orchestration that minimizes worker time at the pick face, businesses can create a more efficient and adaptable system that optimizes both human and robot performance.
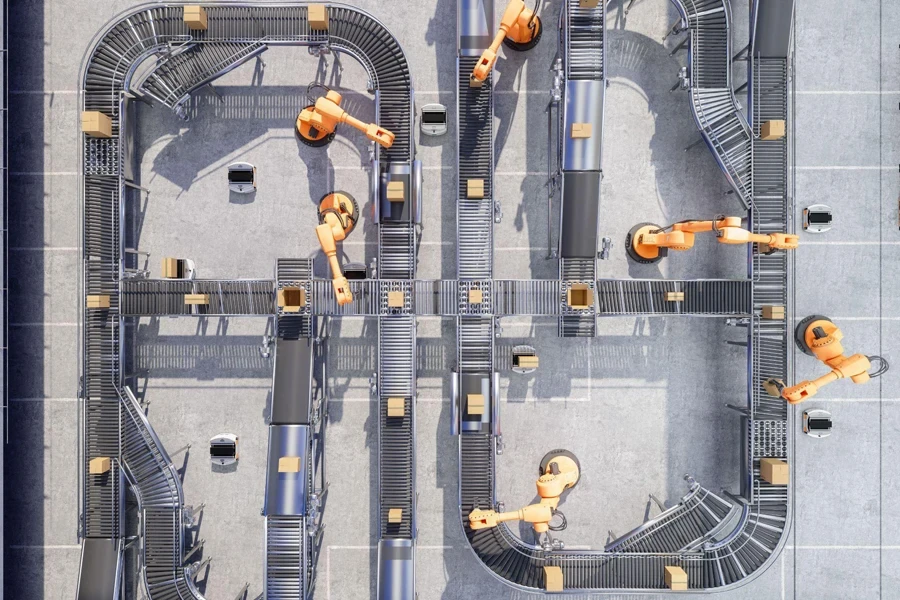
Myth #5: Existing systems are sufficient for orchestrating human-robot work
Finally, there is a common belief that existing systems, such as WMS and AMR software, are sufficient for orchestrating the work of humans and robots in the warehouse. However, these systems often lack true orchestration capabilities, focusing more on the next easiest pick where a robot is already present in the same aisle.
To achieve genuine optimization, it’s crucial to incorporate system software and artificial intelligence (AI) that provide the necessary intelligence. The primary focus of optimization should be minimizing the human pick path, which is often overlooked by AMR and WMS systems.
True orchestration and optimization do not follow a rigid zone-based picking approach. Instead, they employ a hybrid model where the system dynamically makes decisions at various points to reduce human travel. This flexibility and dynamic decision-making set true orchestration and optimization apart from traditional systems.
For example, in an AMR-supported picking workflow, a worker can avoid unnecessary walking by picking items to a tote on an AMR, directing the AMR to a conveyor system to unload, and then triggering another robot to move into place for the worker to continue picking. Interfaces with the robots and workers can be directed by voice, similar to conventional voice picking systems, with workers confirming their work using voice, scan, RFID, or robot-mounted screens or lights.
Conclusion
In conclusion, integrating robots and human workers in the warehouse is a complex process that requires a deep understanding of the various challenges and misconceptions surrounding the topic. By debunking these five common myths, businesses can better understand the importance of effective orchestration and optimization in achieving the full benefits of human-robot collaboration.
To successfully integrate robots and humans in the warehouse, companies must address labor challenges by incorporating robots into multiple workflows, dynamically allocating workers and robots to maximize productivity, and improving ergonomics and safety. By utilizing smart software, AI, and a flexible, hybrid approach to orchestration, businesses can unlock the true potential of human-robot collaboration and stay ahead in an increasingly automated world.
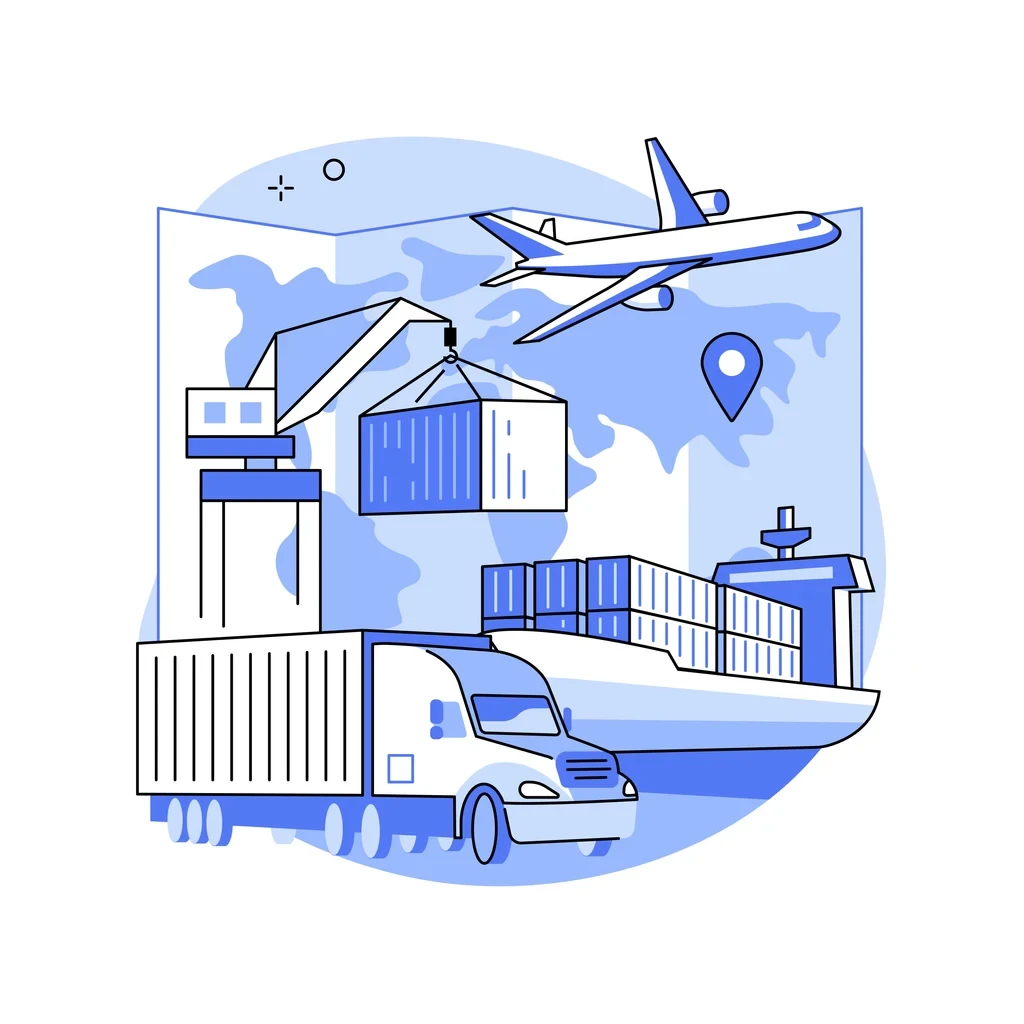
Looking for a logistics solution with competitive pricing, full visibility, and readily accessible customer support? Check out the Alibaba.com Logistics Marketplace today.